コロナ禍の中、リモートワークの拡大が進んでいるが、組織(企業全体)として果たして「品・量・コスト」を満足した効率の良い経営または管理が出来ているだろうか。
コロナ禍以前にも多くの中小企業の経営者のみなさんが悩みを抱えていた課題と同様に思えてきた。
マネージメントの世界にトヨタ生産方式の考え方を参考にして支援した企業が数社ある。
今回はその概要を紹介する。
皆さんは、「必要な情報」が「欲しい時」に「欲しいデータ量」で得ることができてますか?
コロナ禍前から、「コミュニケーション不足」
企業の課題をお聞きしていくと、多くの場合「コミュニケーション不足」という課題に突き当たる。組織内・組織間の連携のことである。言い換えれば「うちの社員は『報連相』が出来ていない」ということもひとつのコミュニケーション不足の話である。一つの課内、部内でも影響は大きいが、会社全体のコミュニケーション不足は多くのロスを生み、利益だけでなく安全、信用などにも関わる多くの損失に繋がる実態をよく見てきた。
これはコロナ禍以前の話であるから、コロナ禍のリモートワークの世界ではもっと切実な課題になっているのではないだろうか。
目次
1. 「プル型」がマネージメントを変える
トヨタ生産方式の考え方のひとつは、「プル型の方式」である(カンバンで代表されるように後工程引き(プル)で生産が行われる)。この考え方を生産現場だけでなく、マネージメントの世界に応用することで大きな成果に繋げることができる。「プル型マネージメント」を考えていくと、上記の「報連相」の課題が見えてくる。そして管理監督者が自分自身で実践することで、より実践的なトヨタ生産方式を行う事ができると考える。
2. 「プル型マネージメント」の考え方
経営者・管理者のみなさんの中で「なんでこんな報告をするんだ!」「報告が遅い!」と言ったことはないだろうか?あるいは月曜日の朝、自分の席に着いてパソコンを開くと、メールが100通も200通も来ていることがないだろうか。
「プル型」を考えて欲しい。報告・連絡の後工程は経営者・管理者のみなさんである。こう考えると、「必要な情報」が「欲しい時」に「欲しいデータ量」が入ることである。
トヨタ自動車の製造現場では長年の積み上げで、このデータが現場サイドに常にある状態になっている。いわゆる「見える化」である。つまり経営者や管理者は欲しい情報が常に製造現場だけでなく事務・技術部門の作業エリアにある状態にすれば良い。みなさんの熟練技術・技能のみならず多くの経験から自分自身で項目を設定すれば良いわけである。企業の永続的発展を考えた項目を検討する事前準備の段階が大切である。
3. プル型マネージメントの利点
「過去は変えられるだろう?」みなさんが得る報告は結果が多いのではないだろうか。
過去は変えられないから負の結果の場合、出てからでは損失は大きい。
反対に「未来は変えられるだろうか?」
当然事前に分かれば未来を変えることは可能である。プル型のマネージメントの利点は、仕事(工程)の途中が分かる情報を経緯で追うことで、途中での変更や修復を可能にすることである。
「品質は工程で造り込む」と言う言葉を聞いたことがあると思うが、工程途中であれば微小の問題は工程内で造り込めるし、不良が出たとしても部品や半完成品を作り直すことができる。
廃棄費用も無駄な時間も大幅に圧縮できる。
ロジックで考えればこういう表現ができると考える。
先手必勝のマネージメントの世界を創ることができる。
プル型の報告・連絡ができるようになれば、上司の意図が部下にも把握できることで「相談」活動も活性化するはずである。
「プル型のマネージメント」は部下の背中を押すこと(プッシュ)ではなく、引き寄せること(プル)である。
4. 自身の常識と世間の常識
私が企業を支援する場合注意していることは「トヨタグループの常識、世間の非常識」と思ってみなさんのご意見を聞くことである。もし自分の常識がみなさんの世界で正しいと思ったら、自分のやり方を押し付ける(プッシュ)だけで、みなさんのものにはならないからである。企業を永続的に発展させていくのはみなさんである。その企業にあった手段をみなさんと考え、必要があればみなさんの常識を変えていく(プル)。
例えばある鋳物業の場合、「鋳物は生き物だから、不良率は下がらない」と工場長から言われたことがある。このため検査工程を3段階にして検査で不良を発見して廃棄する方式がとられていた。さらに鋳物の不良は内部欠陥もあり、お客様に届いた以降お客様の機械加工で不良が顕在化することも多い。
こうなると不良補填・補償による大きなロスだけでなく、大切なお客様の信用を失いかねない。製造工程を流れで表し、どこに変化点があるか温度・湿度・機械の使用頻度・鋳型の熱・流動状態など定量的なデータを経緯でシンプルに捉えることで真因が分かり大幅にロスコストが低減できた。
対策に要した設備的な投資はかからなかった。
データがあればシンプルに物事が考えられ、今まで「生き物」だと思っていたものが「製品」に変わる例である。
現場の監督者や作業者は日々の対応に追われこういうことまで気が回らないのが実情ではないだろうか。だから手っ取り早く「鋳物は生き物」になってしまう。
5. プル型の安全対策
安全は企業にとって第一に優先されるものである。会社の目標値で唯一「必達 0」なのは安全である。どの企業もKY活動(危険予知)活動を行っていると思う。
しかしながら「0」にならないのが実情である。「予知」「予測」は大切な活動であるが、予測は当たらないこともあり、対策項目の優先度もつけにくい。
KY活動を補完する「YK活動」というものがある。単なるKYの反対ではない。
Yは「やりにくい」、Kは「気遣い」であり、やりにくい作業や気遣い作業を実際に作業する作業者の方に洗い出して頂き、作業者の方と優先順位も決めて対策することで、実態の安全を確保するものである。
作業者に寄り添い引き付けるプル型マネージメントの一例である。
6. お客さまを味方につける/情報の共有化の事例
みなさんがマネージメントに必要な情報の一部をリアルタイムでお客様と共有することで、お客様の信用度や利益に繋がり、競合他社に差別化できた例もある。
数社で行った事例としては製造工程や建築などの個別現場の進捗状況をエクセル化して日々の進捗を量データやグラフで表したものをお客様の品種のみ毎日送信あるいは現場に貼り出して共有する。
このことにより、客先都合の変更があっても即座に対応の検討を実施し対応することで、お客様の信用度もあがり、こちらの問題に対しても融通を効かせて頂けるようになった。情報は多方向でさらに有用になる例である。
この他にも、情報を共有化し効果を生んだ事例は沢山ある。
シンプルに現場の作業者にも分かり易い財務状況をグラフ化すれば、作業者の改善活動が会社に貢献しているか分かり、改善活動が活性化した例もある。
不確実性の高い開発プロジェクトでも会社全体だけでなく協力メーカーの進捗も一元管理し、プロジェクトを構成する組織・協力メーカーと共有することで、遅れの挽回のみならず開発リードタイムが大幅に短縮できた例もある。
こうしたことを推進するためにも、経営者・管理者のみなさんから「報連相」の芽を部下の皆さんに与えるような「プル型のマネージメント」を考えて頂ければと思います。
最後に私が役員時代非常に教えられ、参考になったことがあります。
東北の牡蠣養殖を再生させた畠山重篤さん*1のご講演です。
牡蠣養殖が盛んになるにつれ牡蠣の品質や収穫量が減って来た時に、多くの方が養殖そのものの対策をする中で、畠山さんだけが、海を汚す原因が森林の破壊によるものだと気付き植林を始めおおくの森林対策をおこなったことで海が再生し、養殖も再生したという事例です。同じ海のデータをみて、次にどこの情報をとるべきか、そして何をすべきか。物言わぬ牡蠣や海から情報を得る、正に「プル型」のマネージメントではないだろうか。
ぜひみなさんも一度「プル型」を考えてみて下さい。もしかしたら現場の声が違って聞こえるかもしれません。
*1 「日本<汽水>紀行」畠山重篤著 (文芸春秋社)
▼組織を強くする無料セミナーはこちら
このコラムを書いたTPS改善コンサルタント
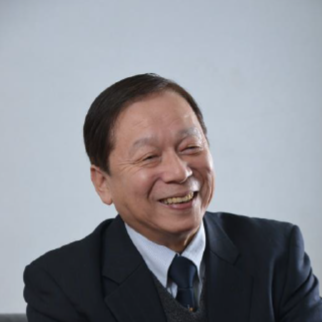
長屋 信俊(ながや のぶとし)
元トヨタ自動車東日本株式会社/技監・顧問、PS事業、TQM事業担当
元関東自動車工業/常務取締役生産技術本部副本部長、海外事業統括
前ゴールドラット・コンサルティング PD
大野耐一元副社長の四天王の中の内川晋氏に直にTPSの本質を教わる。国内外、様々な企業へトヨタ生産方式の導入を手がける。