「トヨタらしさ」、TPS、ボトムアップ
その情報は一般的にも入手可能です。
では、トヨタがいまでも明らかに他とは違うのはなぜでしょう?
トヨタ自動車が「トヨタで働く人々が共有すべき価値観や手法」についての記述を初めて提示したのは 2001年のことです。
「トヨタウェイ2001」は、公式に明文化された企業理念であり、いまだに有効性を保っています。それから20年弱を経た今、「トヨタらしさ」についての新しい発言が見られます。
トヨタ自動車のトップマネージャーの最近の発言からは、TPSは現在トヨタに固有の「トヨタらしさ」の中枢であり、他の「普通の企業」との差異をなす特徴であると見なされていることがわかります。
友山茂樹執行役員のインタビューでは、次のような発言がありました。
豊田章男CEOもまた色々な場において、TPSは「トヨタらしさ」の中核をなす要素であると強調しています。そこでTPSは生産システムをはるかに超えたものとされています。友山執行役員は以下のように話します。
「一番怖いのは、我々自身がトヨタ独自の共通の価値観を失いつつあるということだ。企業は人である。人が普通になるとトヨタは普通の会社になる。そうすると、トヨタ特有の競争力は失われ、その先にトヨタの明るい未来は無い」
このような背景から、TPSが生産システムから基本的な管理原則にまで引き上げられていることは理にかなっているように考えられます。
TPSは、製造から経営までの全体的なマネジメントシステム
「100年に一度という激動の時代を生き残るためには、TPSを生産分野はもちろん、事技系や販売流通分野にも徹底し、開発から、生産、販売、アフターサービスに至るまで一貫してビジネスの戦闘能力を上げていかなければならない」
海外では、TPSを全体的な「リーンマネジメントシステム」として理解するという見方が長らく普及していますが、そうすると、トヨタはそこに近づいていると言えます。
今年はMITの研究報告「The Machine that Changed the World」の出版から30周年です。その著者は「リーン生産」という語を作り出して、トヨタのもとで見い出したことを描写しました。
それ以来TPSは世界中で邁進し、工業生産に革命をもたらし、自動車業界やその他の分野で多くの企業がTPSを模範として生産システムを改革してきました。トヨタは多くの出版物の中で、可能な限りあらゆる側面から検討されてきました。トヨタが世界で最もよく解説されてきた企業であることに疑いはなく、そこからの情報は一般的にも入手可能です。
鍵となるのは、トップダウンとボトムアップのバランス
では、トヨタがいまでも明らかに他とは違うのはなぜでしょう?
実践においても文献においても見落されている「トヨタらしさ」の一面があります。
これは本質的な違いであり、トップダウン組織の企業(つまり大部分の企業)が自然の理として手を焼いていることでもあります。
– TPSの実践に成功しているトヨタや他の日本企業の成功は、少なからずボトムアップ・アプローチに基づいています。-
多くの人々は、日本企業と言えばヒエラルキーとトップダウンと固くなに考えているため、これは驚きかもしれません。ただし、リーンな企業は、従業員を「訓練」、「錬成」し、改善活動を行う自由を与えます。
QCサークルは、日本人の耳には特に進歩的には聞こえないかもしれませんが、実際は改善トレーニングとして、そして従業員の参加と育成の手段として日本のリーン企業で進歩的に使用されています。
これは「エンパワーメント/権限付与」と言い表すこともでき、たいへん時流に沿ったものです。
これに対してほとんどの欧米企業では、改善では主に節約成果に焦点があわせられており、改善活動は継続的ではなく、いささか特別なもので、「ワークショップ」に参加する従業員は少数のみです。日本的な意味でのQCサークルはほとんど存在しません。
しかし時の経過とともに、QCサークルの活動を通して、従業員全員が改善の方法論、改善の考え方、それに対応する行動パターンに関して技能を習得してきています。
これにより現場力と結びついた改善能力が組織内に生まれます。
継続的に活動を実行すると、結局は大きな目標であるQ、C、Dに反映され、最高レベル(オペレーショナルエクセレンス)にまでつながります。
トヨタなどの成功を収めたリーン企業では、ボトムアップ・アプローチが、改善とTPSが機能することに大きく貢献しています。ただ実際に鍵となるのは、トップダウンとボトムアップのバランスです。
これに対し、TPSを導入した欧米企業がトップダウンに傾きすぎて、ボトムアップ・アプローチをなおざりにすることがよくあります。
さらに言えることは、オペレーショナルエクセレンスはソフト要因なしでは達成できません。ここではマネージャーや管理監督者が決定的な役割を果たします。日本のリーン企業では、「左脳」だけでなく「右脳」によっても機能するリーダーシップスタイルが実践されています。
これが何を意味するのかについては、次の記事で詳しくご説明したいと思います。
引用:トヨタ自動車HP、トヨタイムズ、The Machine That Changed the World」(1991年)の広告文より
▼組織を強くする無料セミナーはこちら
このコラムを書いたTPS改善コンサルタント
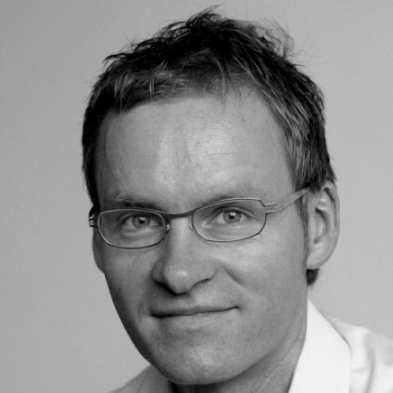
Dr.ロマン・ディツアー (Dr. Roman Ditzer)
コンサルタント ドイツ・ハンブルク在住
ドイツの大学で経済学と日本学を専攻後、交換留学生として来日し一橋大学で学ばれ、その後上智大学、琉球大学等では研究員として活躍された。
モノづくりに強い日本企業を頻繁に訪れその背景にある要素を継続して追求し、コンサルタントとして、リーン・マネージメント、KAIZEN、リーダーシップ、 “学習する組織”といった分野で活躍されている。
日本語が達者で、日本的モノづくりや経営について、ヨーロッパの観点で文章にされる。一方で京浜精密工業社のアドバイザーとして欧州連絡事務所の責任者も兼務されている。
「KAIZENのバランス・マトリクス モノづくりに強い日本企業は何が違うのか?」も是非ご覧ください。