

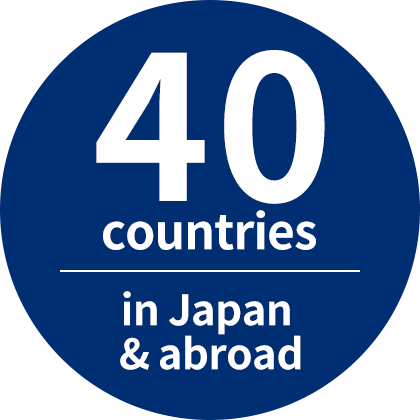
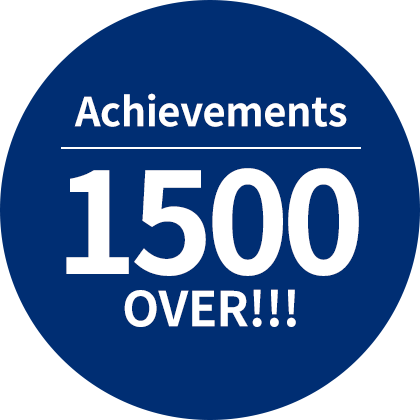
Hirayama Gemba Kaizen Consulting ABOUT US
Based on TPS (Toyota Production System), we will thoroughly eliminate waste and provide guidance support for creating your own production system in order to realize your management strategy.
We analyze the current situation and review the direction of reform. While educating employees, we will provide guidance and support that is suitable for your company’s shop floor, and will realize “improvement of quality, cost competitiveness, and performance” and “human resource development”.
Consultants from major companies
with experience in over 40 countries will respond.
Please feel free to contact us.
If you are in a hurry, please call us.
(Japan time)
Except for Saturday, Sunday, holidays, Year-End and New-Year holidays
GEMBA KAIZEN
Service List
SERVICE
Upcoming
Seminars / Training
SEMINAR/TRAINING
There are no scheduled events scheduled.
Consultants from major companies
with experience in over 40 countries will respond.
Please feel free to contact us.
If you are in a hurry, please call us.
(Japan time)
Except for Saturday, Sunday, holidays, Year-End and New-Year holidays
3 reasons why we are chosen REASON
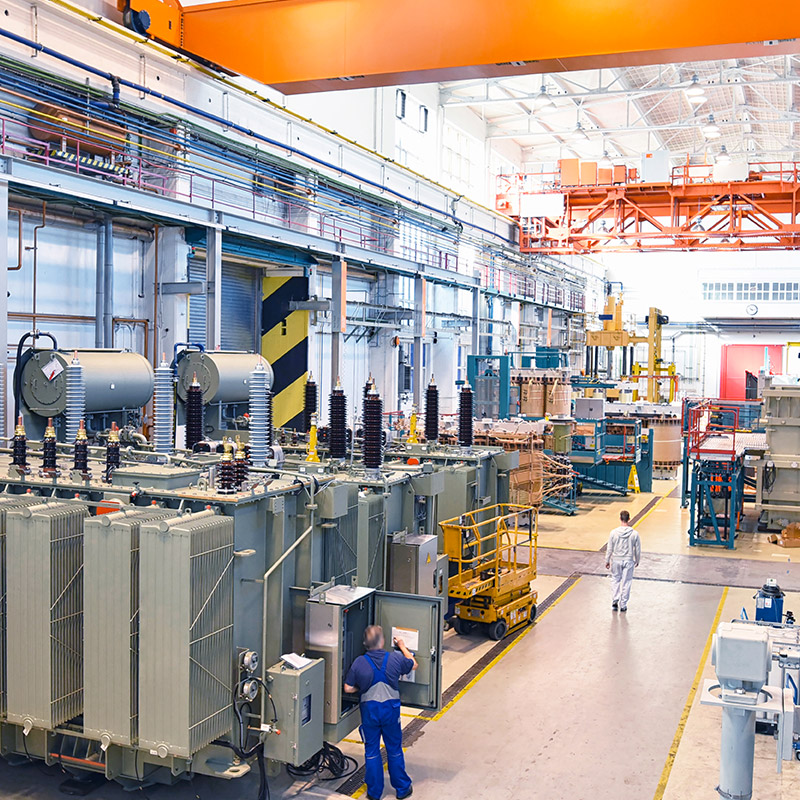
REASON 1
Improvement experience of
more than 1,500 companies in 40 countries
There must be the shop floor issues that cannot be solved by your own company alone. Improvements and reforms for manufacturing industry to survive, regardless of country or industry, need development of your human resources through practical experiences of improvement, and strengthening of your production system base.
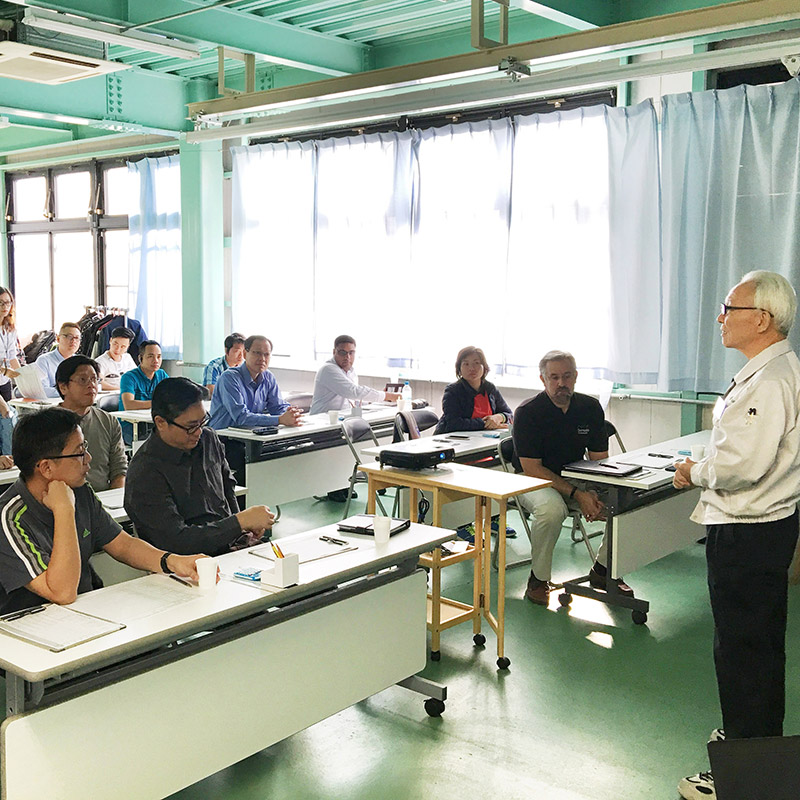
REASON 2
Consulting that shop floor workers
acknowledge our superiority and be pleased
In conventional consulting styles, there was a distance between consultant and the shop floor because it was promoted mainly consultant and management executives. Our consultant can provide a guidance without a distance between consultant and the shop floor through the guidance based on the “seeds of improvement” in a concrete way, instead of “finding fault” like a critic.
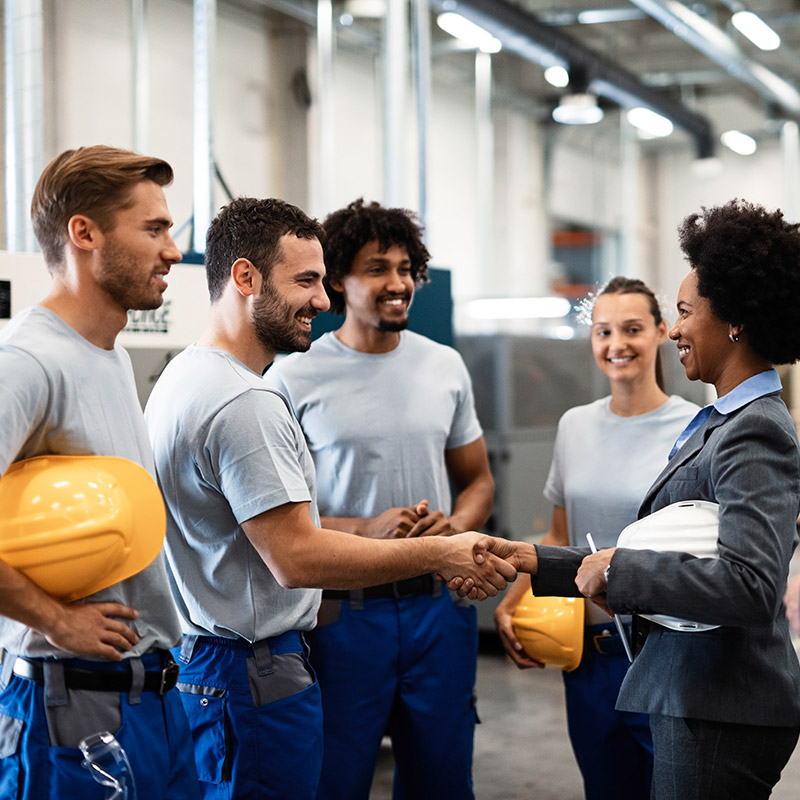
REASON 3
Continuous improvement will continue
even after the end of guidance
While strengthening “human resource development”, we focus on the “overall flow” from design to purchasing, manufacturing, logistics, and production control, and provide guidance that matches the actual situation of your company. Continuous improvement will continue even after the end of guidance through the guidance that is acceptable to the shop floor workers.
Consultants strong
in Gemba Kaizen
CONSULTANT
The consultants are all experienced personnel who have accumulated many achievements at the shop floor of major manufacturing companies.
There are many consultants who have TPS trainer qualifications, and our practical and accurate consulting is highly evaluated both in Japan and overseas.
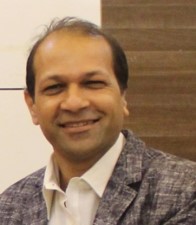
Factories of India Founder & CEO, Gemba Kaizen consultant
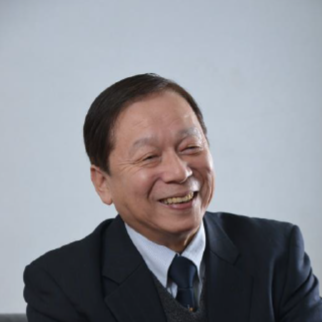
Former Toyota Motor East Japan, Inc.: Technical Supervisor & Advisor, in charge of PS (Production System) and TQM (Total Quality Management) projects.
Former Kanto Auto Works: Executive Managing Director, Deputy Head of Production Technology Division, in charge of overseeing overseas business.
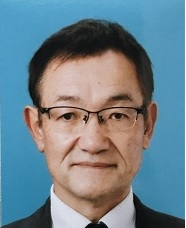
Former Motomachi Plant Section Chief, Toyota Motor Corporation (OB)

Manufacturing Operations Excellence Consultant
Actual introduction effects of
HIRAYAMA CONSULTING BUSINESS
CASE STUDY
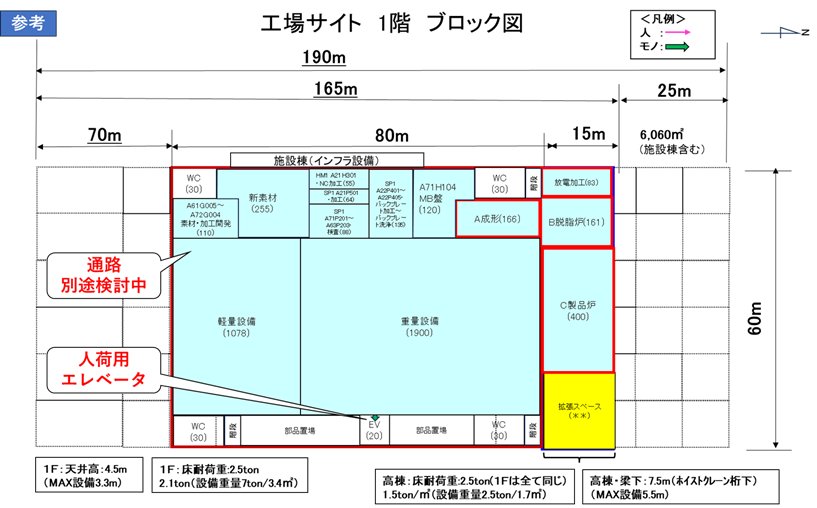
Case Study: Improvement of a New Factory Layout
Establishing a New Plant to Increase Production Capacity by 40%
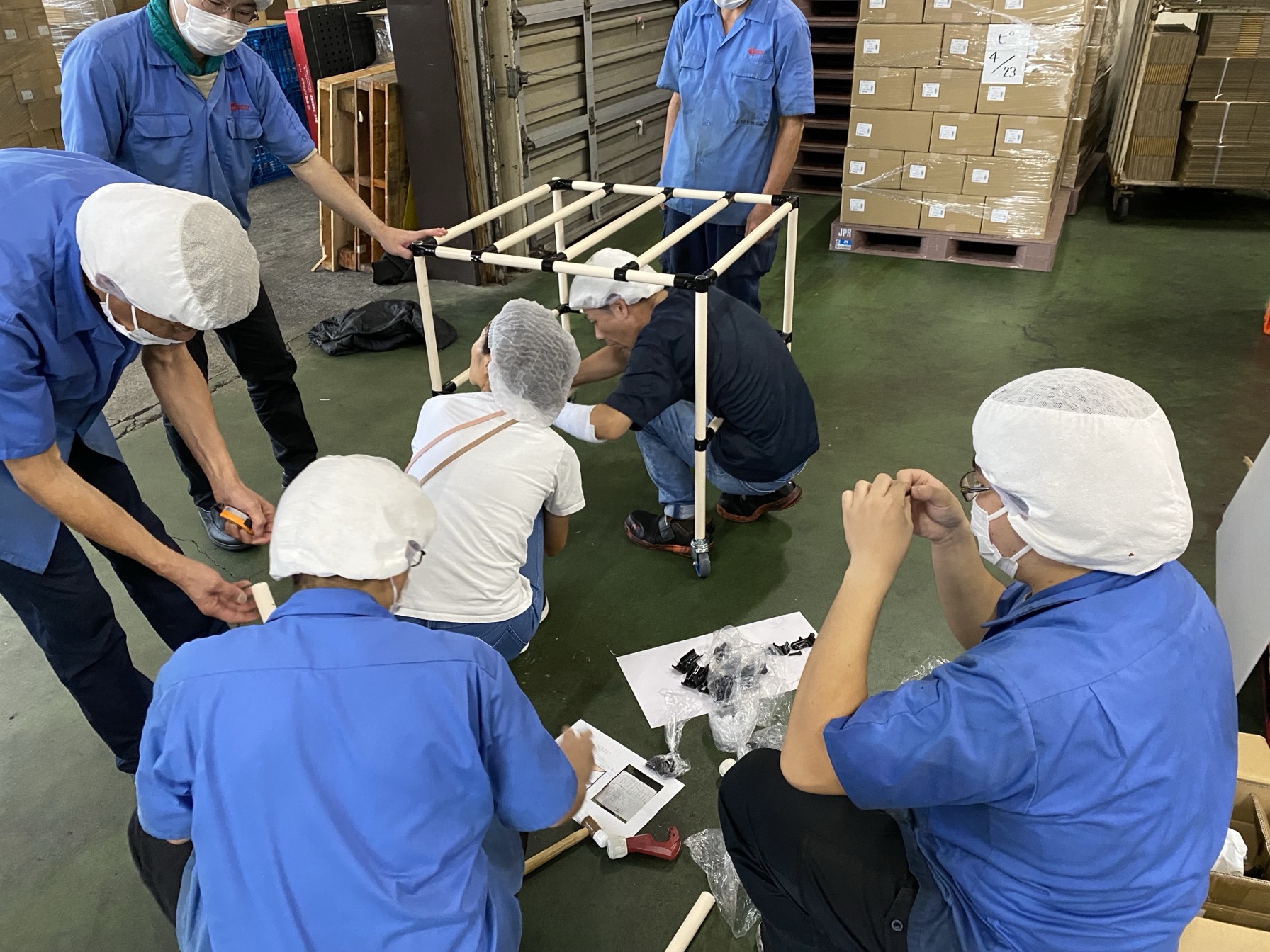
Case Study: Workbench Improvement in a Food Factory
・Bending Work: 3,000 to 5,000 times per day → 0 times・Work Improvement: Reduction of 48 to 120 minutes per day
What's new NEWS
- 2025/06/13
- [Case Study] Eliminating 12 Types of Muda – Workshop Seminar
- 2025/04/23
- 【In Response to Your Inquiry】Embedding TPS and Kaizen Practices
- 2025/01/10
- Training for Enhancing Production Site Capabilities at a Factory in Vietnam
- 2024/12/25
- TPS Dojo / Record-Breaking 1,358 Participants in 2024
- 2024/10/16
- Introduction of the New Training Equipment at the TPS Dojo