製造業の就業者は2021年度までの20年間で157万人も減少しました。
(「2022年版ものづくり白書」による集計)
熟練技術者の技術伝承は、多くの企業の共通課題です。
熟練技術者が現場からいなくなっても、S・Q・D・Cを維持管理継続し続けなくて企業の存続は有得ません。
急速な人材不足の中、注目するべきポイントはこの3つです。
(「2022年版ものづくり白書」による集計)
熟練技術者の技術伝承は、多くの企業の共通課題です。
熟練技術者が現場からいなくなっても、S・Q・D・Cを維持管理継続し続けなくて企業の存続は有得ません。
急速な人材不足の中、注目するべきポイントはこの3つです。
- 熟練者の代わりを担う方法
- 熟練者のノウハウを伝えていく技術
- 経営者の判断力
1. 熟練者の代わりを担う方法
人材不足の解消は、自働化 or ロボット化の活用によって、製造現場の省人化を図り現場作業の効率化をすすめることがまず第一歩です。現場のことを一番わかっている熟練作業者、リーダー、監督者は現場改善を実行する相応しい人達です。
TPS改善教育は一般的に2~3年ほどかかりますが、彼らが改善の知識・ノウハウを習得し、正味作業の割合を調査し付随作業とムダをどのくらい刈り取れるかが勝負になります。
そのように、生産性向上し残業時間は低減されたあと、自働化・ロボット化、省人化に繋げ新規事業に省人化した方たちを投入します。
2. 熟練者のノウハウを伝えていく技術
熟練者のノウハウは、形式知と暗黙知にわけられます。
形式知 | 目に見える情報や言葉で表現できる情報のことで、作業手順やノウハウなどマニュアル化することが可能 |
暗黙知 | 目に見えない情報や言語化が難しい情報のことで、熟練作業員が蓄えてきた経験やカン、無意識に身に付いているコツなどを指します。 |
技術伝承を着実に行うためには、暗黙知の情報をいかに伝達できるかが鍵をにぎっています。
作業分析ソフトを活用した動画マニュアルは、業務ノウハウの可視化が可能で、新人教育の効率化と熟練者のOJT時間がかなり短縮し正味作業率がupするので活用をお勧めです。
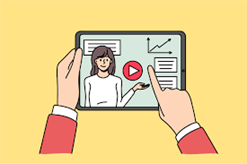
3. 経営者の判断力
技術継承の成功には、経営者の判断が大きく関わってきます。経営者が現場に行っておらず、現場の状況を把握しきれていない場合、判断することは難しく、「技術伝承が重要だがうまくいっていない」と答える経営者の心には、「まだ、大丈夫だ」という気持ちが先にたっているため、技術伝承がす進みません。
技術伝承は未来の技術力を左右する重要な施策であり、経営者をはじめとする会社組織全体が一丸となって取り組む姿勢が必要です。
現場改善のスペシャリスト
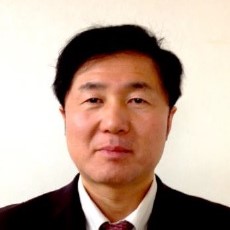
柿沢 高一(かきざわ こういち)
リコーOB 品質保証部・製造技術部
リコーにてトヨタ生産方式をベースにリコー生産方式を立ち上げ。その後、食品・菓子、医療業界など他業種にトヨタ生産方式を実践指導。 マシンの生産性向上、ネックマシンの能力向上、コンベア生産の原価低減、セル生産(1人方式・巡回方式・分業方式・分割方式)の構築、台車引き生産方式の構築、5S職場風土づくり、品質・設備管理を実践する。
▼工場のDX サービス詳細はこちらから
工場のDX選ばれる3つの理由 REASON
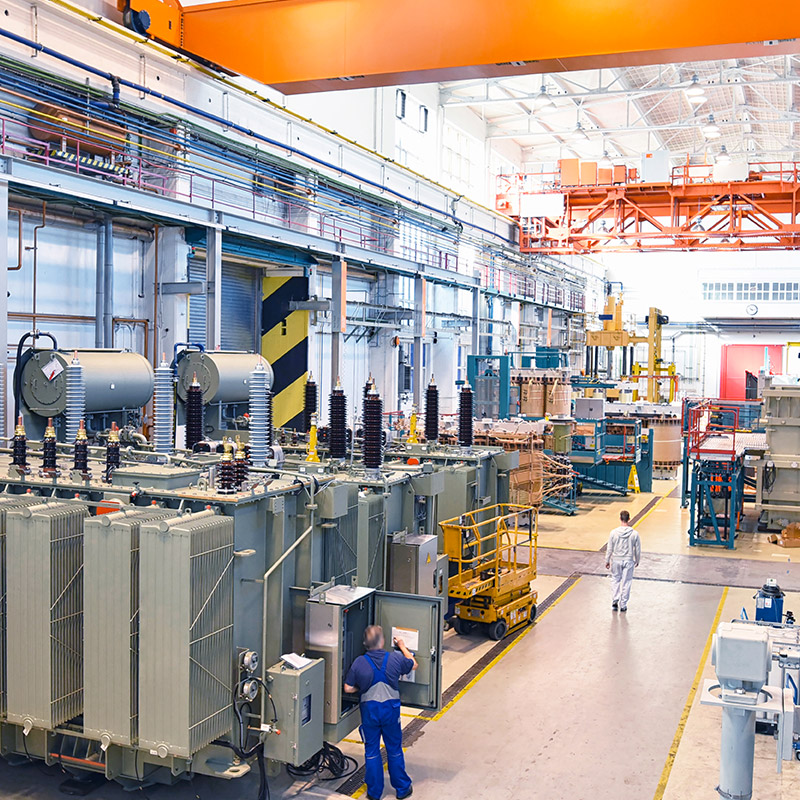
REASON 1
40ヶ国、
1,500社以上の改善実績
自社だけでは解決できない現場の問題は必ずあります。製造業が勝ち残るための改善・改革は、国や業界を問わず、改善の実践体験を通じて、人材を育成し、生産体制基盤を強化することが必要です。
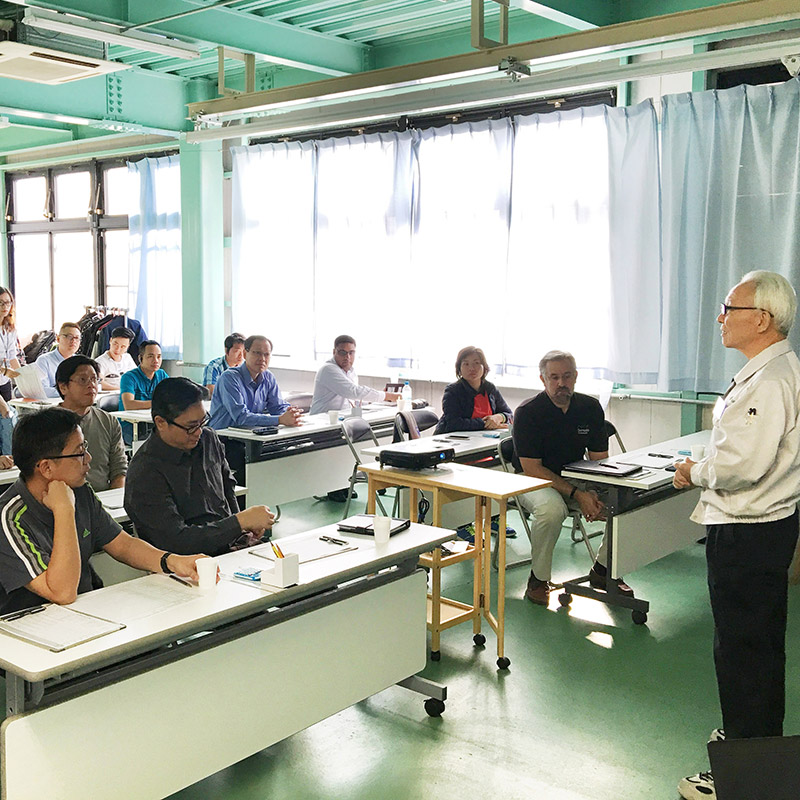
REASON 2
現場が一目置き、
喜ぶコンサルティング
従来のコンサルティングでは、経営層とコンサルタントが中心になってすすめるため、現場とコンサルタントの間に距離がありました。弊社コンサルタントは、評論家的な「あら探し」ではなく「改善の種」を具体的に見出す指導により、現場の人間との隔たりのない指導をすることができます。
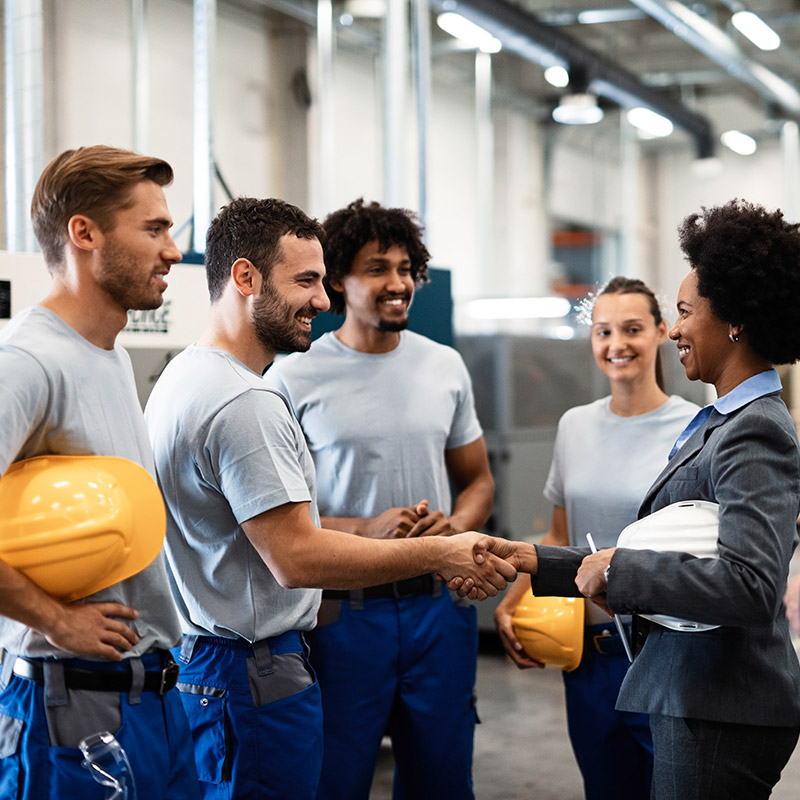
REASON 3
指導終了後も
継続的改善がされる
「人づくり」を強化しながら、設計から調達・製造・物流、そして生産管理と「全体の流れ」を重視し、貴社の現場の実態に合った指導を実施。現場が納得できるコンサルティング指導を行うことで、指導終了後も改善文化が継続されます。