(Statistics according to the 2022 Manufacturing White Paper.)
The transfer of skills from skilled technicians is a common challenge for many companies.
Even if skilled technicians are no longer on site, it is essential to continuously maintain and manage SQCD (Safety, Quality, Cost, and Delivery); without this, a company cannot survive.
In the midst of a rapid shortage of talent, these are the three key points to focus on.
- Ways to Replace Skilled Workers.
- Techniques for Transmitting the Expertise of Skilled Workers.
- Management’s Decision-Making Skills.
1. Ways to Replace Skilled Workers.
Addressing the shortage of talent starts primarily with automating or utilizing robotics to reduce labor in manufacturing sites and enhance the efficiency of on-site operations.The most knowledgeable about the site—skilled workers, leaders, and supervisors—are the most appropriate individuals to implement site improvements. TPS (Toyota Production System) improvement training typically takes about 2 to 3 years, but the key is for them to acquire knowledge and expertise in improvement, assess the proportion of actual work, and determine how much of the ancillary work and waste can be eliminated.
Subsequently, after increasing productivity and reducing overtime hours, we can proceed with automation and robotics, further reducing the need for manpower and deploying those who are part of the reduced workforce in new business ventures.
2. Techniques for Transmitting the Expertise of Skilled Workers.
The know-how of experts is divided into explicit knowledge and tacit knowledge.
Explicit knowledge | Information that can be seen or expressed in words, such as work procedures and know-how, which can be documented in manuals. |
Tacit knowledge | Information that is invisible or difficult to verbalize, referring to the experience, intuition, and unconsciously acquired skills that skilled workers have accumulated. |
To ensure effective technical succession, the key lies in how well tacit knowledge can be conveyed.
I recommend using video manuals with work analysis software, as they allow for the visualization of operational know-how, significantly shorten the on-the-job training time for skilled workers, and increase the net work efficiency, thereby streamlining training for new employees.
It is urgent to create video manuals analyzing the techniques and tricks of skilled workers using work analysis software for the succession of their expertise.
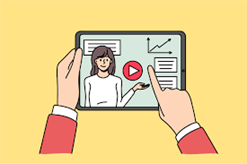
3. Management’s Decision-Making Skills.
The success of technical succession is greatly influenced by the decisions of management.When managers do not visit the site and are not fully aware of the situation on the ground, it is difficult for them to make decisions. Managers who acknowledge the importance of technical succession but admit it is not going well often have a prevailing sense of ‘it’s still okay,’ which hinders the progress of technical succession.
Technical succession is a crucial strategy that influences future technical capabilities, and it requires a unified approach from the entire corporate organization, including management.
Specialist in On-site Improvement
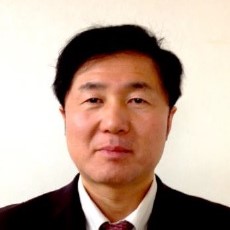
Koichi Kakizawa
Ricoh Retiree, Quality Assurance and Manufacturing Technology Departments
At Ricoh, I established the Ricoh Production System based on the Toyota Production System. Subsequently, I provided practical guidance on the Toyota Production System across various other industries including food, confectionery, and medical sectors. My work involved improving machine productivity, enhancing the capacity of bottleneck machines, reducing the cost of conveyor production, and constructing cell production systems (single-person, patrolling, division of labor, and division methods), trolley-pulled production systems, and fostering a 5S workplace culture, along with practicing quality and facility management.
▼Details on the factory’s DX services can be found here
工場のIot3 reasons why we are chosen REASON
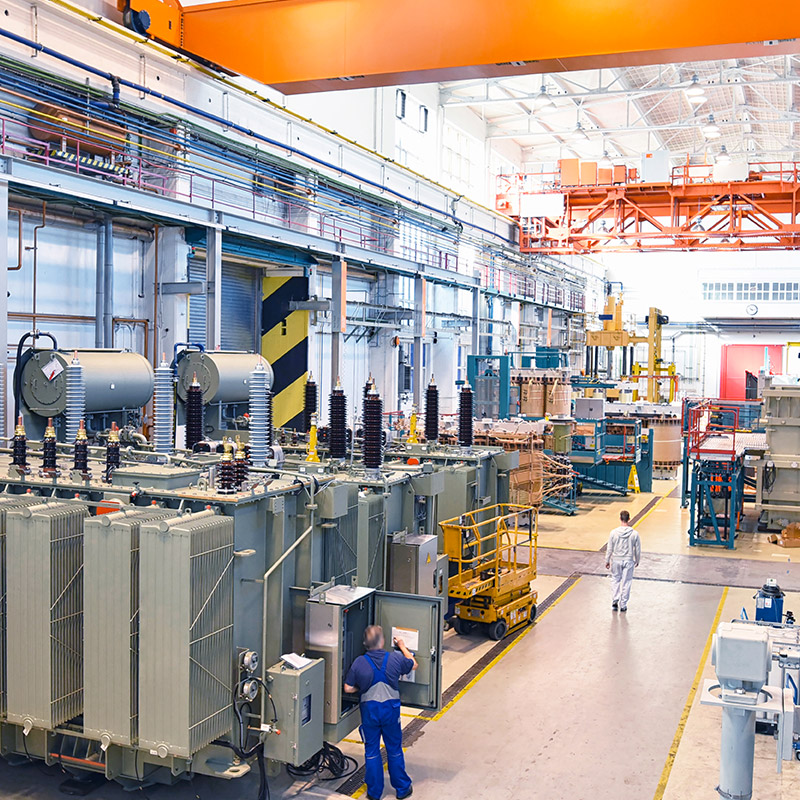
REASON 1
Improvement experience of
more than 1,500 companies in 40 countries
There must be the shop floor issues that cannot be solved by your own company alone. Improvements and reforms for manufacturing industry to survive, regardless of country or industry, need development of your human resources through practical experiences of improvement, and strengthening of your production system base.
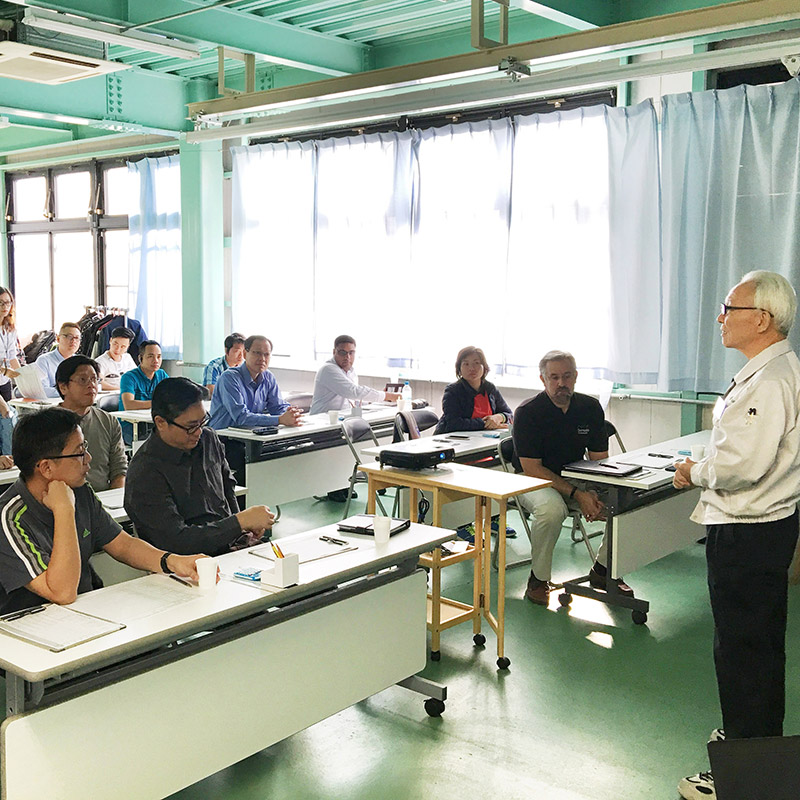
REASON 2
Consulting that shop floor workers
acknowledge our superiority and be pleased
In conventional consulting styles, there was a distance between consultant and the shop floor because it was promoted mainly consultant and management executives. Our consultant can provide a guidance without a distance between consultant and the shop floor through the guidance based on the “seeds of improvement” in a concrete way, instead of “finding fault” like a critic.
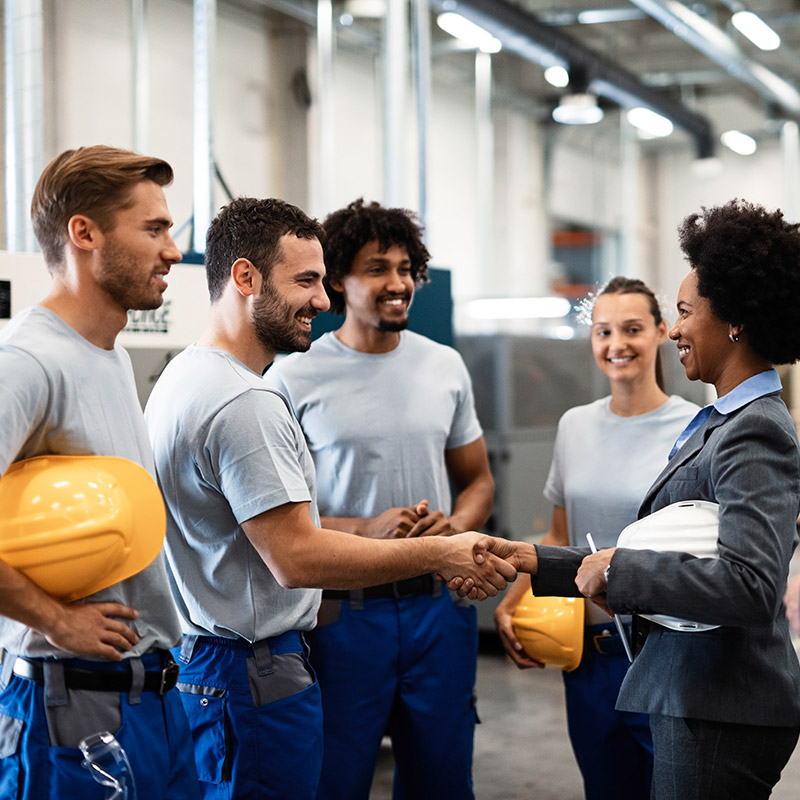
REASON 3
Continuous improvement will continue
even after the end of guidance
While strengthening “human resource development”, we focus on the “overall flow” from design to purchasing, manufacturing, logistics, and production control, and provide guidance that matches the actual situation of your company. Continuous improvement will continue even after the end of guidance through the guidance that is acceptable to the shop floor workers.
Consultants from major companies
with experience in over 40 countries will respond.
Please feel free to contact us.
If you are in a hurry, please call us.
(Japan time)
Except for Saturday, Sunday, holidays, Year-End and New-Year holidays