失敗 その1 プロジェクトの見切り発車スタート
市場の要求に応えるために、
「多少、生産性が悪くてもまずは稼働。」
「後から生産性を改善すればなんとなるだろう。」
というプロジェクトは、生産性を熟考せずスタートするため、結局は早期解決ができない状況に陥ります。
思いの他問題点や課題が多く中間管理職は右往左往し、改善を行う人も不足し、経営者の計画通りに進まないのです。
失敗 その2 現場改善のやり方を知らないけどチャレンジ
現場改善のやり方を知らないで、改善活動を行うと失敗します。
それは経験する必要のない、不要な失敗です。
改善活動を始める前に、
- 目標を達成するための方法を知っているかを確認。
- 知っていれば見守り、知らないのであれば、同じ目線で手本を見せる。
- 最終的には手本通りできていることを確認。
失敗 その3 当事者による作業分析
一般的に作業内容は標準などで決められていて、それを守ることで品質や安全、納期が管理されているため、当事者による作業分析は負担が大きく、できない状況が発生します。改善活動を行う前に、当事者による自己分析ができる時間が、どのくらいあるのか見返す必要があります。
分析力と改善経験が豊富にある第三者に作業を分析してもらい、職制やオペレータの合意をもって適正な時間設定に見直す改善活動は、短期間で生産性向上という結果につながるだけではありません。
新しい視点で問題を発見できる目を養い解決した経験は、更なる改善への高いモチベーションを生み出し、他社と差がつく競争力のある現場をつくりあげることができます。
このコラムを書いたコンサルタント
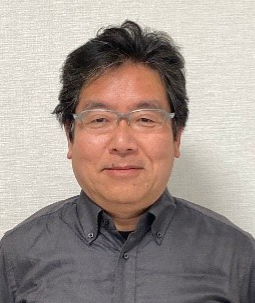
吉田 正幸
現場改善コンサルタント / 日本特殊陶業株式会社 OB
生産設備の電気設計、修理、保全、IEなど幅広い分野にて、トップと現場の間の意思疎通を取りつつ、管理指標の生産性向上を行なう現場改善の経験が豊富。
▼工場診断のお問い合わせはこちら
工場診断のお問い合わせ