という言葉があるように、設備停止は製造業にとって多大なる損失をもたらすため、設備停止影響を最小限に抑えるためには、迅速かつ効果的な保全活動が必要です。
また、近年の技術進歩により、予知保全を活用する企業も増えていますが、保全コストの適正化を図るためには、事後保全から学び、効率的/効果的な保全活動を推進することが重要です。
今回は、設備保全の概要を紹介するとともに、設備故障低減のために必要なことは何かに重点を置き説明します。
1.設備保全概論
設備保全は、機械や設備の故障を未然に防ぎ、機能を維持するために必要不可欠な活動です。その目的は突発的な故障を減少させ、設備の寿命を延ばしライフサイクルコスト(LCC)を抑えることにあります。
設備保全には大きく分けて以下の種類があります。
(1)予防保全: 機械の稼働時間や経過時間に基づいて点検や部品交換を行い、トラブルを未然に防ぐ。
・時間基準保全: 定期的に決められたタイミングで点検/保守を行う。
・状態基準保全: 機械の稼働状態を監視し、異常が発生する前にメンテナンスを実施する。
(2)事後保全: 故障が発生した際に修理を行い、再発防止策を講じる。
(3)改良保全: 故障後に再発を防ぐために設備を改造/改善する。
これらの保全活動を実施することで、工場の生産性を向上させるだけでなく、故障による生産停止のリスクを最小限に抑えることが可能となります。
2.設備保全における具体的な手法
日常点検や定期点検は、機械の状態を常に把握し、故障を未然に防ぐために非常に重要です。特に、点検項目の具体的な判断基準や方法を定め、管理者がチェックの履行状況を確認することで、設備の健全な状態を維持することができます。
近年では、「設備保全管理システム」を活用して、点検の最適化や作業負荷の軽減を図る企業も増えてきました。このシステムにより、故障実績やコストを考慮したタイムリーな保全計画の自動化が可能です。
さらに、予兆(予知)保全は、振動センサーや超音波センサーなどを活用して、故障の兆候を早期に検出し、事前に対応する手法です。特に、超音波センサーは振動センサーよりも早期に異常を検知できるため、効果的な故障予防策として注目されています。また、AI診断ツールは、熟練技術者の不足に対応するための技術革新の一環として、近年益々重要になっています。
3.事後保全の対応
事後保全は、機械が故障した後に修理を行い、その後に再発防止策を実施する手法です。機械故障が発生した際には以下のフローで対処することが一般的です。
- 故障停止原因の究明: まず、故障の原因を特定し、過去のトラブルシュート集も活用して状況を整理します。
- 部品交換の可否判断: 予備部品の有無や、他の工場で同型機種が使用されているかどうかを確認し、部品交換が可能かどうかを判断します。
- 関係者との緊急会議: 修理方法や工程再開までの段取りを関係者と迅速に協議します。
- 設備トラブル報告書の作成: 故障の経緯や処置内容を定型書式にまとめ、次のシフトに確実に事象を引継ぎます。
4.故障停止低減に向けて大切なこと
故障停止の低減を図るうえで、まずはKPIの設定時に年度目標を明確にすることが必要です。故障停止時間/件数について前年度のデータを整理し、再発防止策が完了した項目や進行中の項目を区分けしたうえで目標数値を設定します。
さらに、過去3年間の設備故障実績を分析し、コスト対効果を考慮した予防保全計画を作成することが効果的です。
設備故障低減委員会の定期的(毎週が望ましい)な運営も重要です。この委員会では、毎週の定期会議を通じて故障の実績や原因分析、再発防止策の進捗を確認します。製造部門を中心に、施設管理部門、保全部門、品質管理部門、原価管理部門が一体となり、工場全体として故障低減に向けた対策を実行することが重要です。
5.人材育成の重要性
設備保全には人材の育成が欠かせません。特に、技術的な知識に加え、現場での経験を通じて異常を察知する力を養うことが求められます。
異常に気付くためには、設備や機械の「通常」の状態を知り、その状態からの変化を敏感に感じ取る必要があります。また、トラブルシュートやデータ分析、論理的思考力もエンジニアにとって重要なスキルです。気付いた違いについて、技術的仮説を立て速やかに上司に伝える際にはコミュニケーション力も重要となります。
現在、多くの製造業ではエンジニアの不足が課題となっており、特にベテラン社員から若手社員への技術伝承が重要なテーマとなっています。経験を積むことで成長を促し、最終的には「真のエンジニア」として活躍できるような人材育成が、設備保全活動の成否を分ける大きな要因となっています。
特に設備故障低減委員会を牽引できるエンジニアが、現場の問題点改善の取組みを主体的に実施することで、現場の安定稼働が図られるといっても過言ではありません。
このコラムを書いたコンサルタント
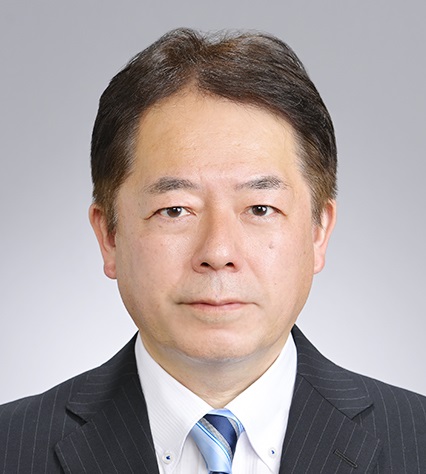
鈴木 智博
現場改善コンサルタント / 日本たばこ産業OB 技術開発部・製造部
新規工程開発/安全管理/品質向上/コスト低減/納期管理/人材育成の経験が豊富。
▼工場診断のお問い合わせはこちら
工場診断のお問い合わせ