売れた数とつくる数を同期化(同数)して余分なモノはつくらないこと
令和元年12月31日、未知のウイルスによる肺炎が蔓延し始めたと中国政府がWHO(世界保健機関)に届けた。新型コロナウイルスで飛沫や接触によって伝染し、症状が現れるまでに1~2週間、症状の出ない人もいる。保菌の有無が分からないで接触や会話をすれば伝染は避けられず瞬く間に世界に蔓延、海外の国々に比べ感染者の少ない日本でも9万5千人を超え、死者も1,700人を上回り増え続けている。外出時のマスクは常用、密閉・密集・密接を避ける政府が国民に求めた対策で生活様式は変わり、経済活動も自粛要請で人の動きが止まり、働き方にも変化をもたらした。テレワークや在宅勤務が奨励されているが机上でできる仕事が対象だ。
直接モノを扱い人と接する仕事の感染対策は休業が最も有効だが、それでは生活も経済も成り立たない。マスクの着用や間仕切り、こまめに手洗いや消毒をすることしかない。モノづくりや飲食業は経済活動の基盤である。しかし、仕事をすれば感染の危険にさらされる。テレワークや在宅勤務のできる職業がうらやましく思う。
テレワークや在宅勤務は、IT(情報技術)の進化で様々な人やモノの動きを制御する情報をつなげたデジタル化の見える姿と考える。デジタルとはアナログデーターをデジタルデーターに変換することで、人が行う様々なアナログの動きをデーターに置き換えられる規格化によって成される。
システム化しても問題解決に至らず、負の循環のなか、TPSを導入
材質や形状の異なる1万種以上の規格化した機械部品を扱う企業は、70%を自社工場、25%を協力会社で製造、集荷場を備えた倉庫に運び込み受注日から3日後に出荷、5%は特注品で2週間、品物によっては3週間の余裕をお願いしている。
この企業で抱えている問題は、集荷を始めてわかる在庫切れ、異品納入や数の間違い。特注品の寸法不良などである。それらの原因は人の力だけに頼っていることが問題、在庫をパソコンで管理すれば受注段階で品物の有る無しがわかり、欠品も2日の猶予で防ぐこともできる。集荷時のどたばたは避けられ、特注品は出荷日が近づいて慌てることもなくなるとシステム化に投資、7ヶ月後に本格運用に入ったが問題解決には至らなかった。
規定の残り数で仕掛け指示をしているが、同品目が2つ以上重なると現場から優先順位の問い合わせがくる。段取り替えを始めると前加工が済んでいるはずの材料がない。あるいは修正をしなければ使えないなどのごたごたも絶えてはいない。負の循環は業績に影響、右肩下がりの最中にTPS(トヨタ生産方式)を導入した。
製造単価を下げても、利益は増えない理由
倉庫には5段積み、幅90㎝の市販の棚が背中合わせに1m間隔で並べられ、天板にも建屋の天井に届くほど品物が積んである。集荷通路で脚立を使っていれと作業が終わるのを待つ、あるいは空いている通路に移動して出荷指示書を探す。奥の集荷台車を通すために手前の台車はいったん外にでる。
工場では、原材料や加工途中の品物が壁際や機械間の空き地に積み込まれ、一時置きか放置なのか通路にもある。段取り替えをしている人に目を向けると、共用で使っているのであろう3mほど離れている工具棚の間を頻繁に行き来している。段取り時間はベテランで20分そこそこ、不慣れだと人によって異なるが40~50分掛かかるとの説明だ。
1度に仕掛ける数はモノによって異なるが、小さいモノは加工時間も早いのでできるだけ多くしており、約100個である。、「できればもっと多くしたい。」との事。なぜか聞くと、「多くするほど機械の稼働率が良くなる。」との返事である。
出荷は1週間に1~2度、数は5~15個だと言う。仮に毎週20個としても5週間ある。仕掛け数50を提案すると、製造部長は、「とんでもない。段取り替えが増え稼働率が下がって製造単価も悪くなる」と反論した。
製造単価を下げると利益が増える。何十年も前のモノが無い時代の思想である。利益は品物をお金に換えてのたまもの、製造原価が安くても材料や労務費などを先食いして倉庫に積んでいたのでは利益は生まない。
品物を効率よくお金に変えるには、売れた数とつくる数を同期化(同数)して余分なモノはつくらないことだ。
売れた時に売れた品物を売れた数だけつくるには段取りに手間取っていたのでは成り立たない。
段取りに時間がかかるのは何が原因か、どうすれば短くできる。試行錯誤の改善を積み重ねて4年、全ての加工機の段取り時間を1/3に、半日かかっていた大型設備も30分を切るまでになった。そこに至るまでには様々な確執もあって、管理者は部下との葛藤を繰り返しながら やって診る やらせて看る を忍耐強く続けた結果である。
小ロット生産が進むにつれて倉庫の在庫も棚も減った。集荷作業で棚間を移動するには間口のある集荷場に戻っていたが壁際と中間に横断できる通路を設けた。在庫には3定(定位・定品・定量)を定め、品物と品物の間には間仕切りを設けた。先入れ先出しを示す[取り口]の表示や、1ケ月の品物の動きで在庫をコントロール、余分なモノはつくらない。つくらせない仕組みにした。
改善のすべては人がやるべき仕事の規格化で、様々な部署の様々な人が1つの決めごとを守ることで成り立たせている。
事例はおよそ6年の外部指導を受け13年前に区切りをつけたもので、元号が平成から令和になった今も、多くの在庫を抱えながらも生産現場や出荷部署では、今必要なモノがあれもない これもない。調達担当者はどこかにあるはずと探し回っている企業の資材調達の責任者は「システムが古い。更新しなければ改善されない」
システムが古いのが問題ではない。人やモノの動きと制御する機能が同期し、状況の変化に合わせたメンテナンスがされていれば問題はなく、あるとすれば動きが遅いことだ。
▼組織を強くする無料セミナーはこちら
このコラムを書いたTPS改善コンサルタント
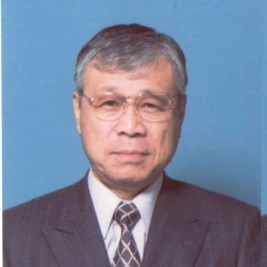