現行商品の売れ行きが悪くなり、多少回復しても、新たな市場では売れ筋商品から外れたり、更には、在庫処分に困り、従業員の整理・解雇など企業の存続や社会的な危機に迫られます。
目次
常日頃からの改善活動を、全員参加の自分達で疾風を吹かせ
「ムダやネック工程を改善しよう!」
これからも、トヨタは「2本の柱を原点に」展開する
1. 疾風に勁草(けいそう)を知る ~後漢書~
強い風が吹き、始めて風にも負けぬ強い草がわかるように、困難や危急に際して、はじめて節操の固いことがわかる。
(例)肌寒い早春に、若草の茎を強くする麦踏み作業。
これまでも「強い疾風に晒され、厳しいダメージを受け」ながらも、人類は進化し続けてきた。
2. トヨタの職場づくり
トヨタの職場づくりは、良いものを、安く、タイミングよく、多くの人に提供する。
そして、安全を第1に作業を標準化し、2本の柱を実践し続けること。
現場の特長は、安全・品質の造り込み標準書を現場の管理・監督者が決めて実践する。だから、日々の体験や改善で「標準書を改定」し、即時に活用している。
【2本の柱】
1) 自働化
異常時は機械を自動停止・あんどん点灯、管理監督者に知らせる。
作業者は「止める・呼ぶ・待つ」:作業者に生産ラインを停止する権限を委譲。
2) JIT(ジャストインタイム)
仕掛品をカンバン枚数管理(カンバンで生産指示;余分な生産を禁止)
仕掛り在庫を最少化:前工程は仕掛カンバンによる補充生産をする。
*標準作業⇒ 生産の流れや作業者の仕事量・働き振りが一目瞭然になる。
*仕掛品の姿(加工、運搬、検査、停滞)に注目し、流れを改善する。
3.課題の共有化
日頃から基本を貫き、苦情など職場の声を吸い上げ・改善する。
(需要は変化する;安全・品質に支障なしだけの標準固定の職場は疾風に倒れる)
先ず、個人の意見や姿を職場の問題・課題として吸い上げ、急所の共有化を行い改善。
仲間との声掛け(お早う、お疲れ)を行い、要望などの困った事を課題に上げ、改善。
このように、共有課題の改善から、更には生産のリードタイム短縮や製品の混流生産などに挑む。
つまり、日頃から、自力で疾風を起こし総力を結集して「社会変動に強い職場づくり」に邁進する。
*TOYOTA WAY:世界で働くトヨタマンが共有すべき価値観や手法を基本理念に制定。
7項目を明文化:2001年~人間性尊重(リスペクト&チームワーク)を軸に展開中。
:個人の創造力とチームワークの強みを最大限に強める風土づくり。
⇒人間性尊重の下、仲間と自主性を高め合い、知恵と努力で活性化職場づくり。
(活動の急所は技術や管理のレベルではなく、先ずは、仲間づくりから)4.改善事例
1)作業者の苦情や疲れた姿を見て、仲間の助け合いの課題として取り組む。 |
作業着が汚れる ⇒ その作業を観察して汚れる工程を探す ⇒ 仲間の知恵と努力で改善 √ 一人の小さな困った事でも、すぐに改善できると、職場が明るく元気になる。 新人配属や職場実習生の仕事を観察し、その困った事を改善すると、盛り上がる。 √ トヨタでは創意工夫制度があり、職場で現金支給される:本人の小遣い銭にもなる。 |
2)生産の流れが悪く「仕掛けカンバン」ゼロ ⇒ 自工程の生産中断。の筈だが?生産継続。 |
~カンバン無視する監督者の方便~ √ すぐに必要になるので、定時までは生産したい。 √ 別途保管し、自工程責任のストップ時に使いたい。 管理監督者の資格なし ⇒ 隠し在庫やカンバンなし生産 ⇒ 課題や問題点を覆い隠す。 企業のあるべき姿はムダ・問題点の顕在化 ⇒ 共有課題とし ⇒ 力強く改善すべき。 <停止時間の活用例> 職場の清掃 = 点検 ⇒ 問題点を発見 ⇒ 改善 |
3)類似品の混流生産:サイズや左右の違いなどを1つの生産ラインで造り込む。 |
自分達の発想で疾風を吹かせ、常に時流に先んずる、若々しい活性化職場づくり‼ |
▼組織を強くする無料セミナーはこちら
このコラムを書いたTPS改善コンサルタント
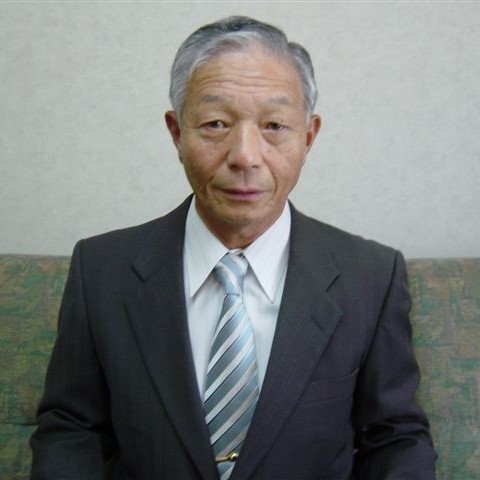
小坂 善治(こさか ぜんじ)
トヨタ自動車OB 現場改善コンサルタント
トヨタに30年間(本社副工場長)在籍、本社・上郷で18年間に亘り、大野耐一工場長~副社長に訓導を受けた。その後、TPS推進の新明工業㈱へ転籍、15年間(副社長・社長)在籍。
「やって見せ、言って聞かせて、させてみせ、褒めてやらねば、人は動かず」をモットーに人が主役の改善を進める。機械加工・組付のエキスパート。