食品工場は通常の10倍速で改善をまわせ!!
結果
改善前10分 → 改善後5分
食品製造の特徴は、
・賞味期限が短い
・材料にばらつきがある
・生産変動が大きい
など、さまざまな要因でとても変化が多い業種ですので、確実に利益に繋げる改善を行うには、スピード感を持った改善活動を行うことがポイントです。
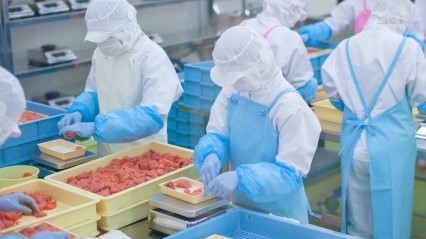
- 業界詳細
- 総菜の製造
- 国
- 日本
- 企業規模
- 従業員 200名
- 課題
- 利益率の改善
- 目的
- 収益改善
- 業界
- 食品
スケジュール
ステップ1 現状調査(現状調査なくして改善はない)ステップ2 安全:ケガをしそうな作業箇所(手作業・設備作業)の洗い出し
ステップ3 作業時間、前段取り時間、段替え時間などの計測
ステップ4 作業改善
切り替え時の歩行削減
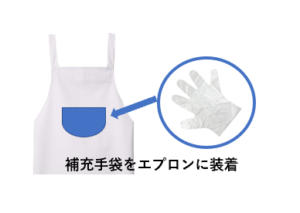
食品製造では、数秒で製品が腐敗するということもあります。
前段取り・段替え0秒に挑戦します。
例えば、製品が変更になる度に取り換えていた手袋。手袋補充置場までの往復はムダです。補充手袋はエプロンにくっつけて歩行をゼロにします。
食品用コンテナ(番重:食品用語)の改善
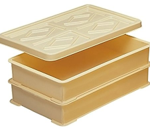
食品用コンテナは積み重ねられるようになっています。よって、そのように積み重ねて利用する食品工場も多いです。
しかし、大抵の場合、人に対しての動作12ムダと、モノに対しての2つの大きなムダがあります。
<2つの大きなムダ>
1)探すムダ
2)取り置きのムダ
今回は、パイプフレームでコンテナを探さず・取り置きなしで一発で取り出せる台車を作成しました。
<段取り替え時間の削減>
改善前10分 → 改善後5分
「カイゼンを10倍速く」のコツ!
0. 「稼働分析」実施
1. 「問題点登録用紙」を現場設置
2. 出て来た問題に対して、「ブレーンストーミング」実施する
3. 「改善ポテンシャル」抽出
4. 「改善テーマ登録用紙」作成
5. 改善実施・評価(改善前・改善後の事例作成)
その他、段取改善には現場だけでは解決しません。
ムダ(人に対してのムダ)ではなく、むだ(システムに対してのむだ)の改善が必要になります。 生産計画の平準化と視える化・現場の5S・3定、それらをトータルで実施する事が必要です。 詳細については、是非弊社にご連絡ください。
食品工場改善のスペシャリスト
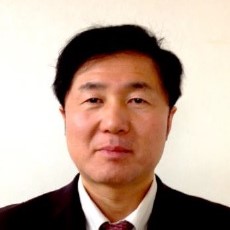
柿沢 高一(かきざわ こういち)
リコーOB 品質保証部・製造技術部
リコーにてトヨタ生産方式をベースにリコー生産方式を立ち上げ。その後、食品・菓子、医療業界など他業種にトヨタ生産方式を実践指導。 マシンの生産性向上、ネックマシンの能力向上、コンベア生産の原価低減、セル生産(1人方式・巡回方式・分業方式・分割方式)の構築、台車引き生産方式の構築、5S職場風土づくり、品質・設備管理を実践する。
選ばれる3つの理由 REASON
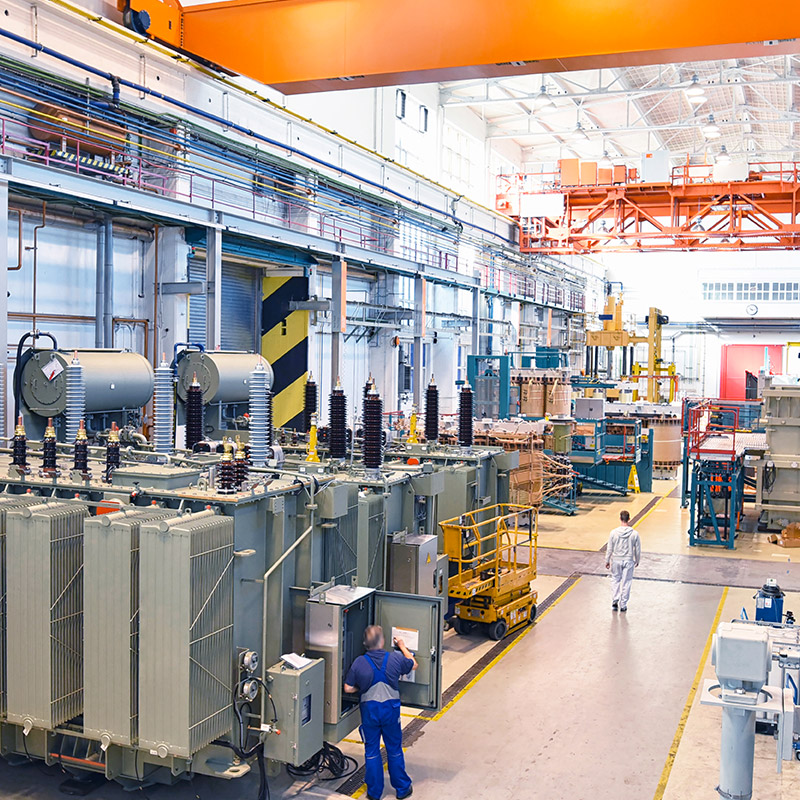
REASON 1
40ヶ国、
1,500社以上の改善実績
自社だけでは解決できない現場の問題は必ずあります。製造業が勝ち残るための改善・改革は、国や業界を問わず、改善の実践体験を通じて、人材を育成し、生産体制基盤を強化することが必要です。
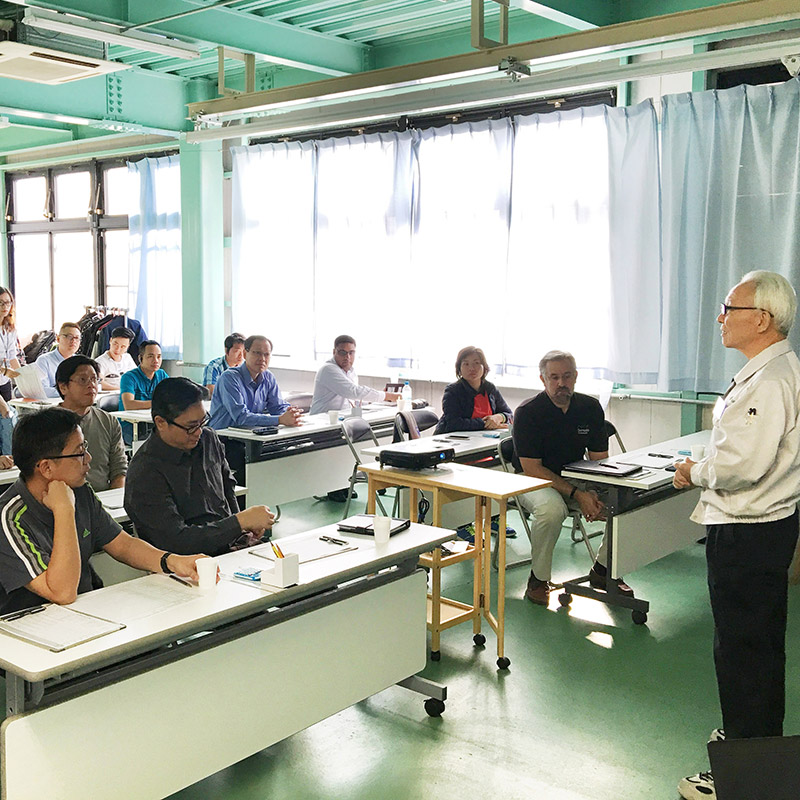
REASON 2
現場が一目置き、
喜ぶコンサルティング
従来のコンサルティングでは、経営層とコンサルタントが中心になってすすめるため、現場とコンサルタントの間に距離がありました。弊社コンサルタントは、評論家的な「あら探し」ではなく「改善の種」を具体的に見出す指導により、現場の人間との隔たりのない指導をすることができます。
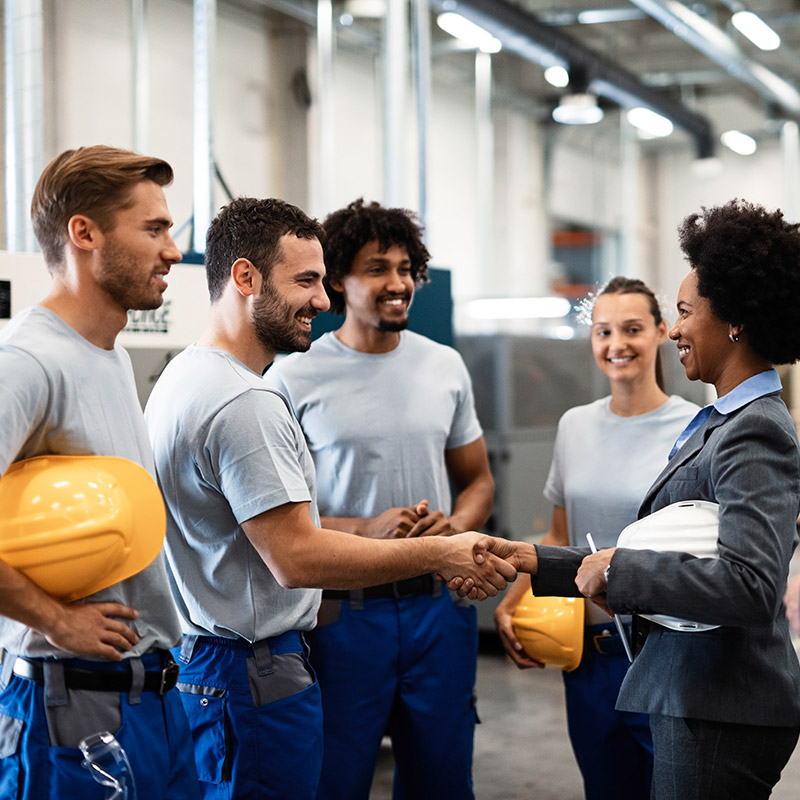
REASON 3
指導終了後も
継続的改善がされる
「人づくり」を強化しながら、設計から調達・製造・物流、そして生産管理と「全体の流れ」を重視し、貴社の現場の実態に合った指導を実施。現場が納得できるコンサルティング指導を行うことで、指導終了後も改善文化が継続されます。