知恵と工夫で自働化だって安くできる!!
1年間で生産性 20%UP
結果
モデル仕上工程での腰曲げ回数と腰曲げ回数時間、全体で50%低減。
重量物の軽減(男・女):約1人当り/日:1000kg(1トン)⇒約1人当り/日:500kg
50%低減。
ベトナムのA社では、設備稼働率(チョコ停、ドカ停。設備故障)が悪く生産計画に対し生産量の20%~40%減が続いており、弊社のコンサルタントがTPM活動を行っていた。
そんな中、お金をかけずに、ラインを自働化したいとのこと、カラクリ改善の依頼を受けた。
<改善前の状況>
セル生産の為、各工程間にかなりの人員が配置され、ムダな動きが目立っていた。
ベトナムでは、安全衛生に関する意識はほとんどなく、重量物も1トンを超える中、頻繁に腰曲げ作業をやっていた。
(空運搬、空歩行、手待ち、取り置き、手伸び、腰曲げ、カン・コツがわかっていない)

- 業界詳細
- 電子機器製造
- 国
- ベトナム
- 企業規模
- 従業員 2000名
- 課題
- 自働化
- 目的
- 収益改善
- 業界
- 電機・電子
スケジュール
2回/月:1年間各工程間にカラクリ改善チームを編成、現状調査・作業の分析・カラクリ改善案出し
問題点
2)自動化をするにはお金がかかってしまう。安く出来ないか。
改善事例
(1)各工程間にカラクリ改善実施後、ムダな動きを無くし、重量物を持つ作業を軽減化した。
(2)製品をとるときに、遠回りしている。レイアウトを変更し、移動距離を短くする。
まとめ
日本と違いベトナムの改善チームは、各工程から兼任で30名集まります。ベトナムではレイティング70%~80%の動きで仕事を行っているため、人員に余裕があるからです。
また、チームワークの統制がとれており、宿題を前向きに行い、必ず実施しているなどやる気もあります。理由としては、成果を出せばすぐに出世して給料が上がり生活が楽になるからです。その為、ハングリー精神が強いのです。
日本の場合はレイティング100%に近い動きで仕事をしている為、現場作業者は余裕が有りません。
改善キーマンは間接の方(主任・係長・課長・部長etc)が行なうので、現場の方に改善教育が回りません。
これが日本の中小企業の実態でしょう。これでは、ますます日本の改善力は弱くなってしまう。
その為に我々のような、外部のTPSコンサルの力が必要と考えます。
現場改善のスペシャリスト
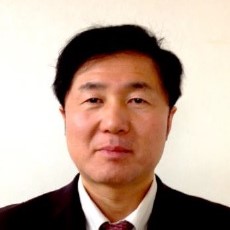
柿沢 高一(かきざわ こういち)
リコーOB 品質保証部・製造技術部
リコーにてトヨタ生産方式をベースにリコー生産方式を立ち上げ。その後、食品・菓子、医療業界など他業種にトヨタ生産方式を実践指導。 マシンの生産性向上、ネックマシンの能力向上、コンベア生産の原価低減、セル生産(1人方式・巡回方式・分業方式・分割方式)の構築、台車引き生産方式の構築、5S職場風土づくり、品質・設備管理を実践する。
選ばれる3つの理由 REASON
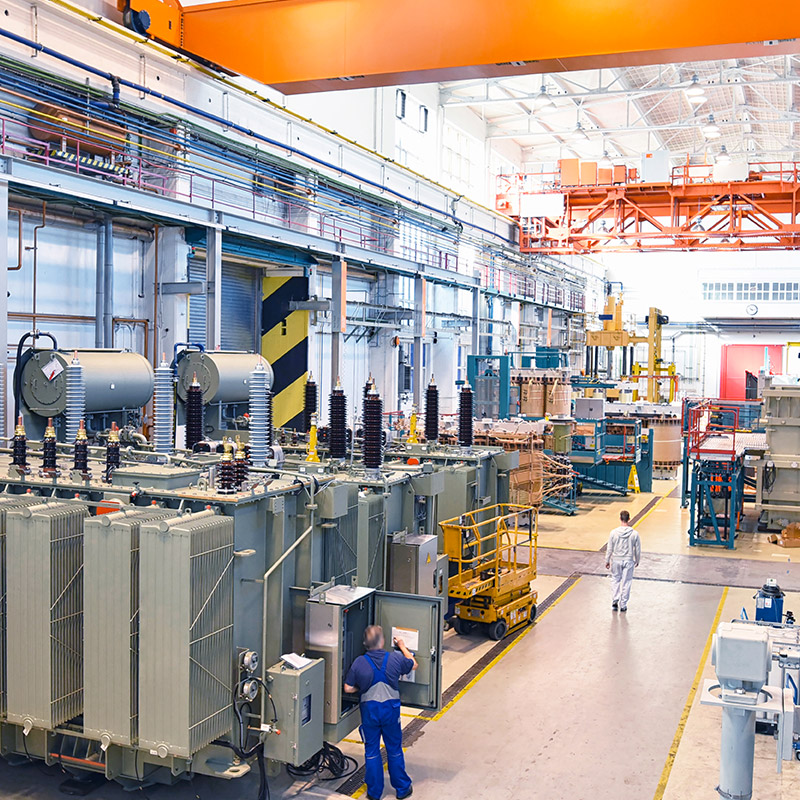
REASON 1
40ヶ国、
1,500社以上の改善実績
自社だけでは解決できない現場の問題は必ずあります。製造業が勝ち残るための改善・改革は、国や業界を問わず、改善の実践体験を通じて、人材を育成し、生産体制基盤を強化することが必要です。
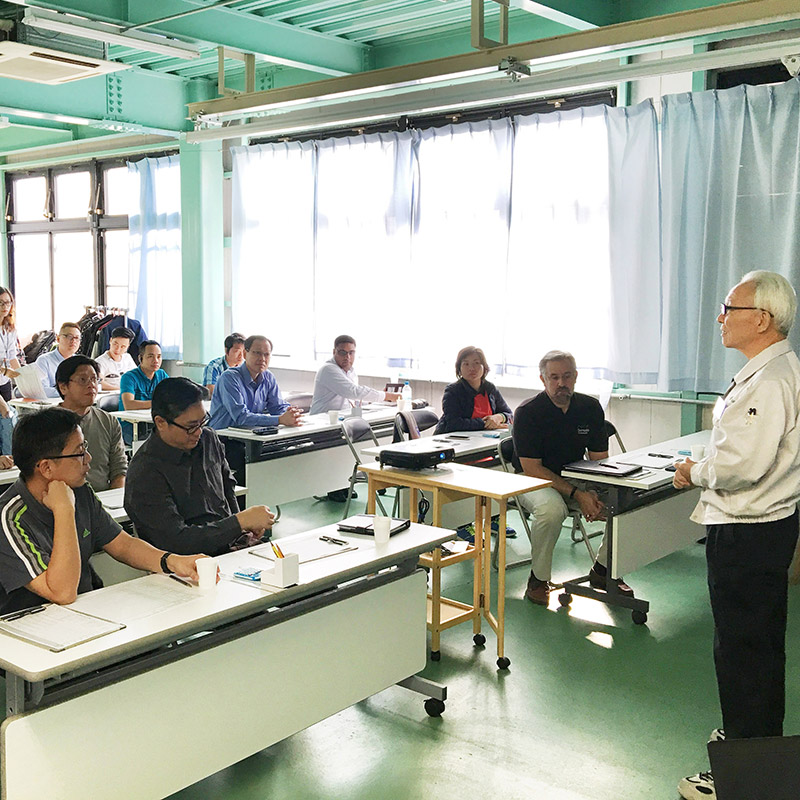
REASON 2
現場が一目置き、
喜ぶコンサルティング
従来のコンサルティングでは、経営層とコンサルタントが中心になってすすめるため、現場とコンサルタントの間に距離がありました。弊社コンサルタントは、評論家的な「あら探し」ではなく「改善の種」を具体的に見出す指導により、現場の人間との隔たりのない指導をすることができます。
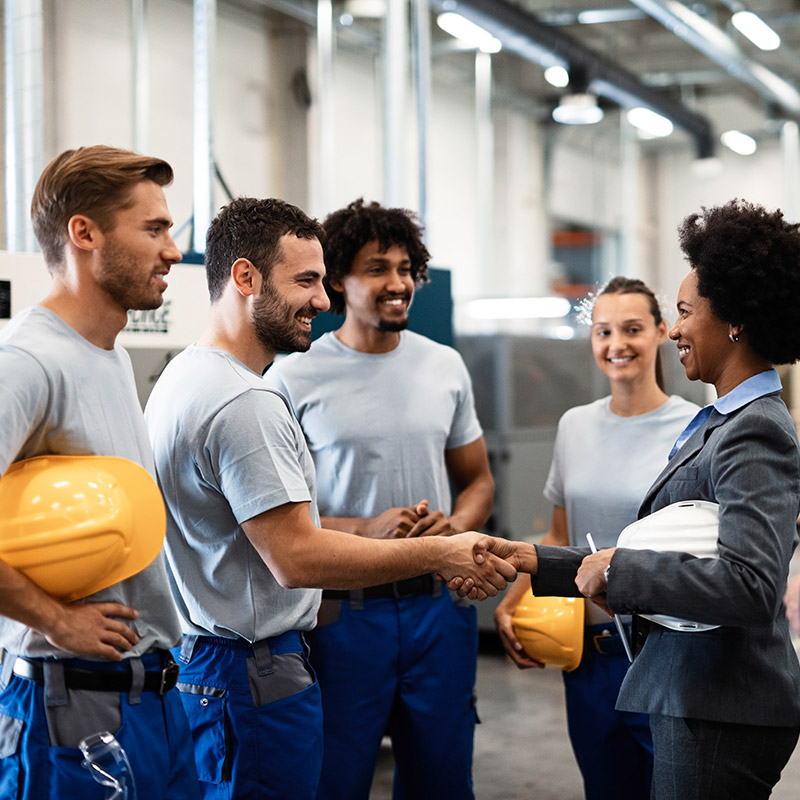
REASON 3
指導終了後も
継続的改善がされる
「人づくり」を強化しながら、設計から調達・製造・物流、そして生産管理と「全体の流れ」を重視し、貴社の現場の実態に合った指導を実施。現場が納得できるコンサルティング指導を行うことで、指導終了後も改善文化が継続されます。