考えるような状況に追い込み、困らさせる。
そのやり方は、今の時代、パワハラと言われるかもしれない。
しかし、人の本質は変わらない。
困って、困って、困り抜いた時に本当の知恵がでる。
困って、困って、困り抜いた時に本当の知恵が出る
人の本能、さまざまな知恵
2020年コロナ禍の初冬、日本学術会議会員の任命拒否問題が発覚しておよそ2ヶ月、本筋をはぐらかす答弁はするも、頑として理由は明かさない。国会の内外で批判の声が渦巻くも滑った転んだは国民が忘れるのを待つ そんな姿勢が透けて見える。
米国の大統領選挙では決着の報道に、現職は感染防止策の郵便投票に不正がある。訴訟する と支持者をあおり対立候補の当選を認めない。根拠となる事実も示さない。
これらも知恵、それと性善説を盾にした本性の現れ、知者ほど嘘が上手と聞き入るが、いずれにしろ潔(いさぎよ)さが無い。
イタチの屁と人間の知恵の出どころは同じ、生きるための冒険でキツネなどの大きな動物に襲われ、逃げ場がなくなると猛烈に臭いガスをあびせ敵がひるんだ隙に逃げ出す。
この時のガスの発射は親から教わったものではなく、持って生まれた本能である。
人の知恵も勉強や教育で身につくものではなく、経験や体験の積み重ねが知恵を出す。
安全平穏、リスクは避ける生活に知恵はなく、困って、困って、困り抜いた時に本当の知恵が出る。
TPS(Toyota Production System)の創始者 大野耐一氏の説である。
1973年 コンベア撤去 立ち作業へ
本社工場で指導員を招いてTPS活動がキックオフしたのは、1973年第一次オイルショック(産油国イスラエルとアラブ諸国の間で起きた第四次中東戦争)の翌年である。エネルギー源を石油に頼っている日本は原油価格の高騰で様々な品物の値上がりが庶民の生活を直撃、春闘で景気の冷え込みを押して高額回答した企業の経営基盤を大きく揺るがした。
言われたら直ぐやれ、まごまごするな と部品箱をひっくり返されたなど、吹き荒れる波風の情報は7㎞ 離れた分工場にも入る。
ベルトコンベアーと平行に並べた作業台と作業台の間に女子従業員が椅子に掛け、流れて来るコンベアー上の容器から右手でワークを取り、左手に持ち替え部品を組付けカシメや圧入を終えると再び右手で戻していた。
コンベアーは撤去、立って作業のできる台を連ね、容器を手送りするレールと手前には中・小物部品の置き場、異常を知らせる赤(ライン停止)・黄(呼び出し)のランプも1人に1灯設けられた。
立ち作業は動きやすくなる。右手で容器を送りながら左手で次のワークを取り出すこともできる と両手をくまなく使えとの説は理屈ではわかる。しかし、コンベアーは仕事を進めるペースメーカーでもある。
不慣れと足腰の疲れも重なって生産量は大幅に落ち、段取り替えが更に足を引っ張った。今必要でないモノはつくるな。指摘されていた在庫が底をつくと納入のための残業・休日出勤、各部署から駆り出された男子従業員の夜業でのその日暮らしが改善されるまでに13ヶ月を要した。
生産性だけの改善に没頭、築いた在庫の山
繰り返す改善。必要な人工は、6.4。7 ではつくり過ぎ、6 は能力不足。
改善の手が入れば落雷は避けられない。ベルトコンベアーを嵩上げ、生産低下を予測し立脚座椅子も準備したが作業中に常用することはなく足腰の疲れは言葉として現れ3週間が過ぎた。大きな問題が起きることなく更に2週間、モノが流れてくる間に背伸びや屈伸、足首を回す姿が見られ、意見を聴き新たな作業範囲をやってみる。やらせてみる。その繰り返しで10名が9名になった。
予告なしで訪れた指導員は、ラインを見渡すといきなり「バカ者 なんちゅう(なんという)アホなことをやらせている」
現場は意味が解らず硬直。
「この場に立ってモノと人の動き観ていろ」・・・怒りを抑え生産ラインを眺めていた。
他部署で矢継ぎ早に指摘の声が響く。
“なぜ” 組付けたワークを後工程に手渡す。
“なぜ” 前工程まで手を伸ばしてワークを取る。
あの半完成品は・・?
止め輪圧入治具は、使い込むほどハンドル操作にコツが必要となり定期的にメンテナンスされている。しかし、整備直後であってもハンドルの動きに異変を感じ、圧入状態のチェックが作業遅れの原因である。構造的欠陥に気づき対策を申し込むも色よい返事はない。休日返上で改善治具が完成したのは1.5ケ月後である。
その後も聴いて やってみて改善する。その積み重ねで更に2名を削減。
半年後に訪れた指導員は工程ごとにモノと人の動きの観察を終えると、笑みを浮かべ右手で左肩をポン。
安堵もつかの間、再び「バカ者」 即座に「すみません」
生産性だけの改善に没頭、築いた在庫の山に対する戒めである。
必要なモノだけをつくる。必要な人工を計算すると6.4といった端数が出る。7ではつくり過ぎ、6は能力不足。端数を整数にする1人工追求のスタートとなった。
実のある改善は仕事を楽にする。楽になれば生産性はUpする
「バカ者」「立っていろ」今流で言うなら超のつくパワハラ、当時にその言葉はなく、非を気付かせ反省を促す時や、揶揄する場合にも親や兄弟だけではなく教師や仲間内でも躊躇なく使われていた。
しかし、初対面で使うことはなかった。
“なぜ” 言われなければならなかったのか。指示される前に取り組んだ。生産性も上げた。非難される筋合いはない。おごりが無かったと言えば嘘になる。本心を認めたら改善は止まる。真の改善とは何か を知らしめるためであったすれば納得せざるを得ない。
単に生産性を追い、数値目標を達成するためのだけの改善は、やや-もすると労働強化を招く、改善をするとは、現場の真実や本音をオモテ化することである。具体的問題が明らかになれば改善の道筋はおのずとつく。実のある改善は仕事を楽にする。楽になれば黙っていても生産性はUpする。その根源は人の知恵である。
人は知恵を出す場をつくってやれば限りなく湧いてくる。
これも大野氏の教え、TPSは知恵を出す場づくりでもある。バカをきつい 怖い と受け取るか、知恵出しの機会とするかは本人や企業の体質による。
▼組織を強くする無料セミナーはこちら
このコラムを書いたTPS改善コンサルタント
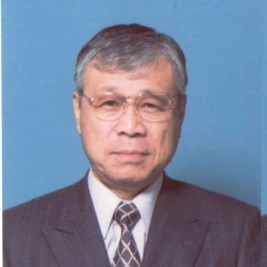