「全体最適」の視点から
工程間を超えて取り組む 社内物流改革
結果
<問題点>
日本の電線産業の世界における地位は中国、米国について3位。一方、国内では大・中・小から零細企業まで400社がひしめいており、過当競争に陥りやすい体質となっており、経営環境が非常にきびしい。
約3000種の製品を手掛けているが「緊急・小口・納入時間指定」など業界特有の物流慣行にさらされている。
いわば「注文がきてからでないと注文の内容が何もわからないので、その日の作業ボリュームがどれくらいあり、いつ作業が終わるのか見当がつかない」という状況。
全社としては「総コストの大幅削減」、物流部門では「モノと情報の整流化」を目指した取り組みを展開した。
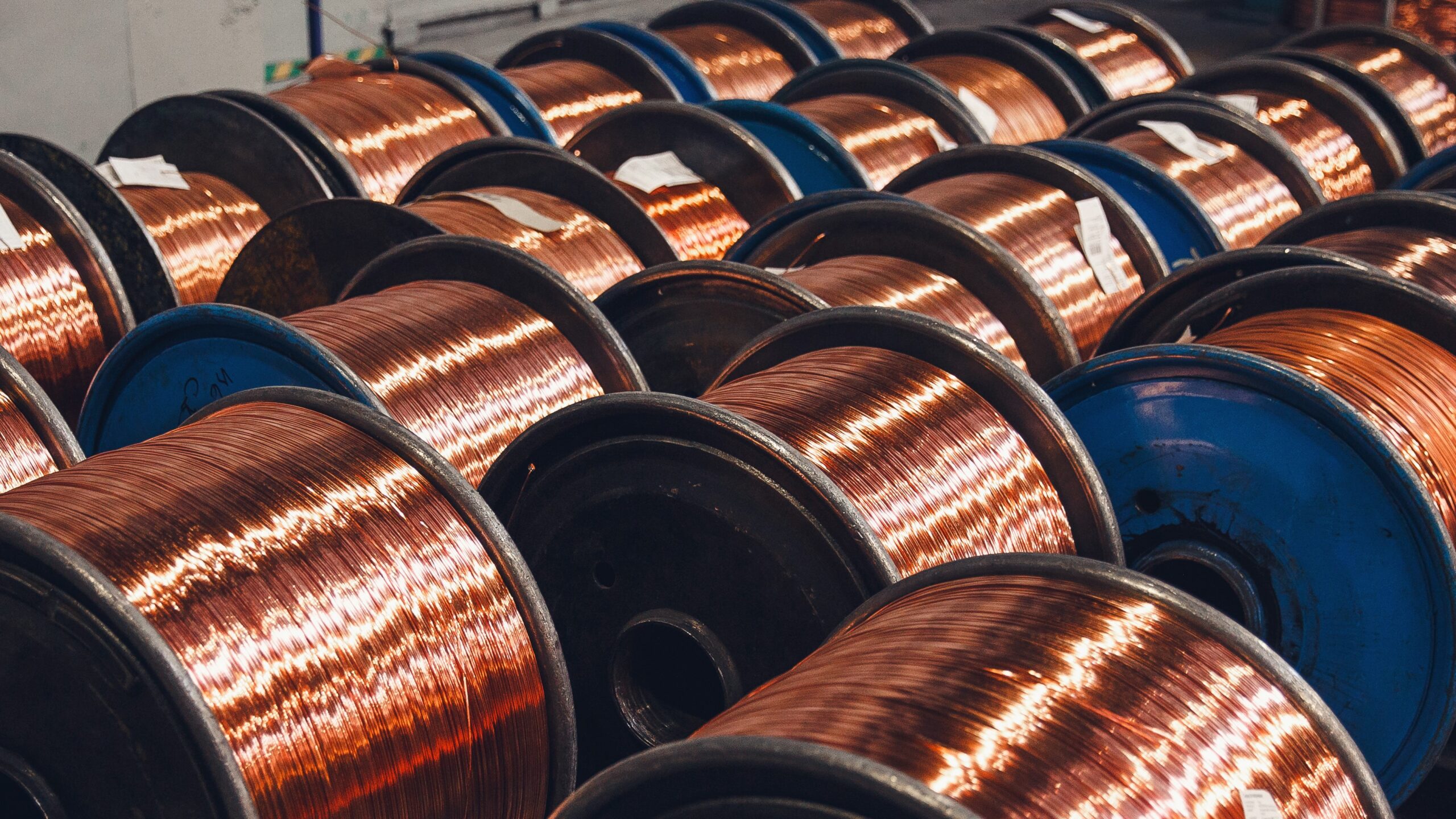
- 業界詳細
- 電線ケーブル及び光ファイバーケーブルの製造
- 国
- 日本
- 企業規模
- 従業員 350名
- 課題
- 管理監督者の育成
- 目的
- 在庫管理
- 業界
- その他
スケジュール
2年間のコンサル指導(2日/月)改善前の状況
工程は、下記3つに分かれている。
- 顧客の注文どおりにケーブルをカットする「切分組」
- 定尺品や切分品を出庫する「倉庫組」
- 荷揃えとトラックへの積込み立ち会いを行う「積込立会組」
現場では以下の問題が順次発生している。
取り組み内容と改善結果
(1)切分作業の動作改善による生産能力改善:ムダと問題点の排除 (2)管理ポストの設置による作業進捗の見える化:「管理ポスト」と名付けた手作りの棚を設置した。 | 一本の切り分けに要する時間のライン平均は、改善前が「20.1分」、改善後が「17.4分」と大きな成果を上げた | |
(1)「倉庫組」版監理ポストの設置 (2)QRコードの導入 | 作業改善とIT化の両面作戦で、作業のムダ・繁閑が把握できたことで効率向上ができ、倉庫組では1名の省人化につながり、誤出荷が皆無となり、「CSと品質の向上」に大きく寄与した。 | |
「トラックの最終出車の理想時間22時厳守」を命題に下記のアクションプランに取りくんだ。 (1)前工程の応援強化:前工程の切分作業の遅延解消 (2)繁閑に応じた機動的人員配置 (3)作業進捗管理システム構築 | 当初目標の「22時全社出車」は未達成なるも出車台数のピークであった時間帯が23時超えから20時~21時と前倒しとなった。また積込工程では2名の省人化が実現。 |
まとめ
各工程別の改善と併せ、「全体最適」の視点から工程間を超えて取り組んだ結果、大きな成果を生み出した。 今後、物流コスト発生の様々な要因を営業部門と共有し、「受注~出荷」の「整流化」を意識した全社的な取り組みを展開する。
TPS公式トレーナー
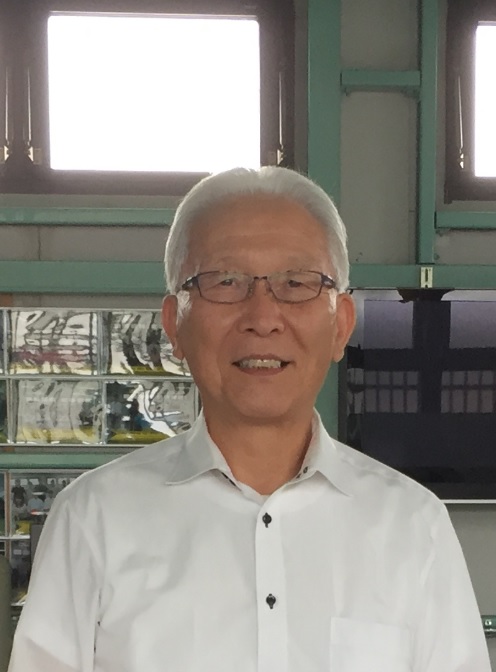
石垣 忠政(いしがき ただまさ)
トヨタ自動車OB 元本社工場工長
本社工場の組立職場を第一線で支えてきた筋金入りの現場職人。妥協を許さない現場への思いは人々を引き付ける。 技能育成グループトレーナーとしても活躍し、トヨタ生産方式など、さまざまな現場教育、指導を実施。
選ばれる3つの理由 REASON
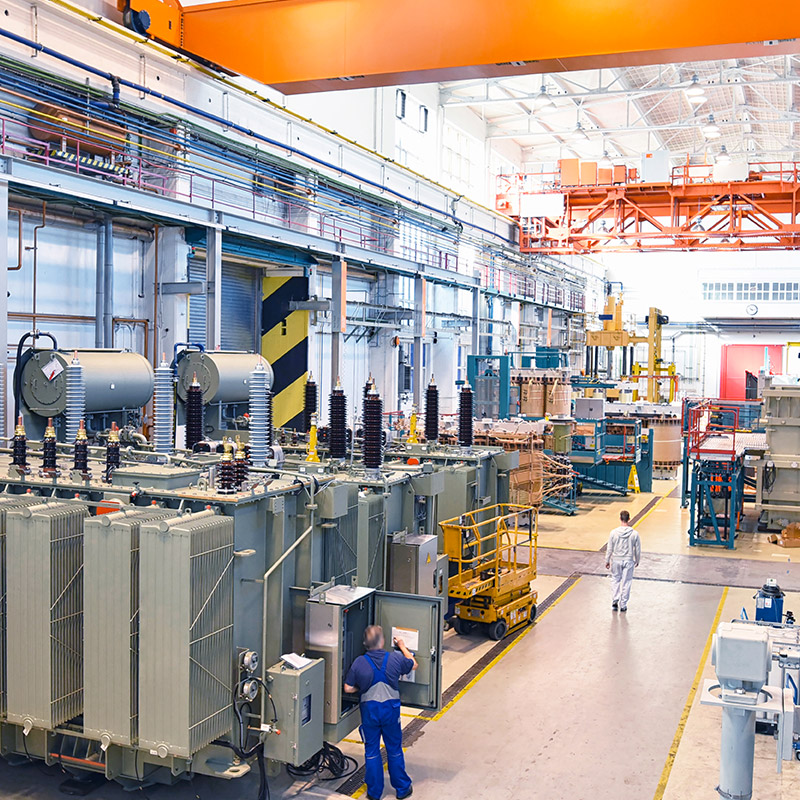
REASON 1
40ヶ国、
1,500社以上の改善実績
自社だけでは解決できない現場の問題は必ずあります。製造業が勝ち残るための改善・改革は、国や業界を問わず、改善の実践体験を通じて、人材を育成し、生産体制基盤を強化することが必要です。
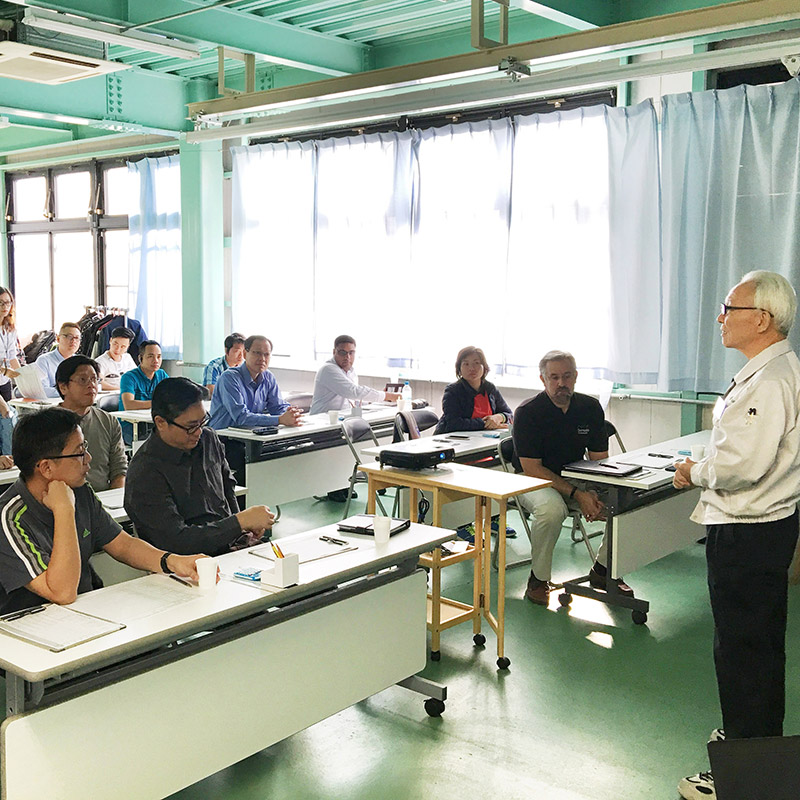
REASON 2
現場が一目置き、
喜ぶコンサルティング
従来のコンサルティングでは、経営層とコンサルタントが中心になってすすめるため、現場とコンサルタントの間に距離がありました。弊社コンサルタントは、評論家的な「あら探し」ではなく「改善の種」を具体的に見出す指導により、現場の人間との隔たりのない指導をすることができます。
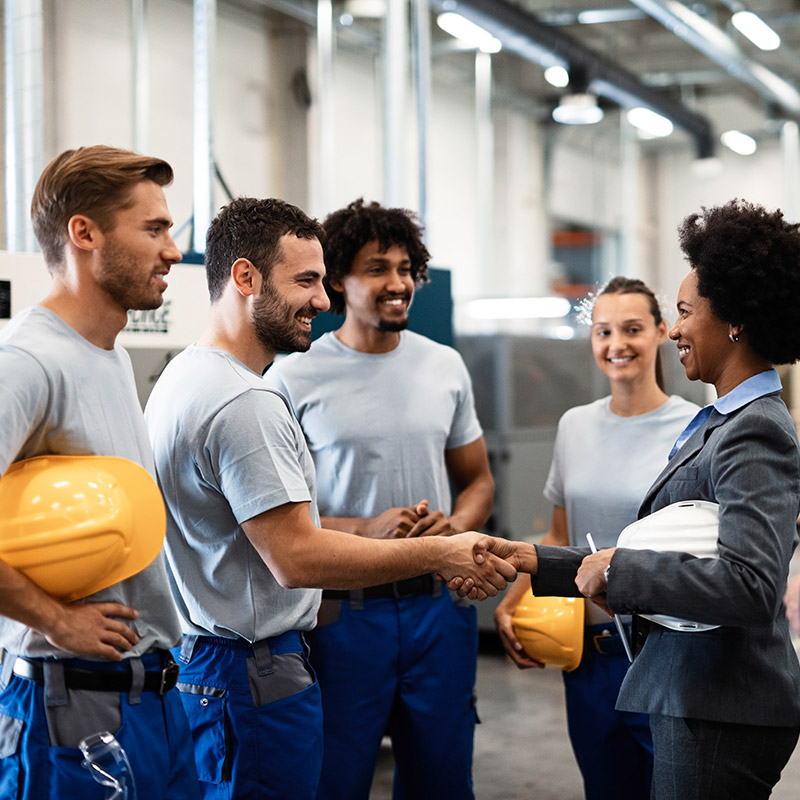
REASON 3
指導終了後も
継続的改善がされる
「人づくり」を強化しながら、設計から調達・製造・物流、そして生産管理と「全体の流れ」を重視し、貴社の現場の実態に合った指導を実施。現場が納得できるコンサルティング指導を行うことで、指導終了後も改善文化が継続されます。