“ How Proactively Can Local Staff Engage in Improvements? ”
When considering the review of the production system and revenue improvement, temporary improvements, unfortunately, do not yield the expected results. Especially in overseas factories, it is extremely important for productivity enhancement that local staff continue to proactively work on improvements.
In Hirayama’s on-site improvement consulting, various solutions to problems faced by management and the field are learned through theory and practical training. Consultants work together with local staff, who have developed an eye for improvements, to address on-site issues and support the practice and entrenchment of specific improvement activities.
Introduction of On-site Consulting – On-site Improvement Seminar
STEP1 Lecture : The Fundamental Principles of the Toyota Production System
The fundamental principles of the Toyota Production System (TPS) are explained clearly through successful case studies of TPS, emphasizing its importance and benefits. By systematically understanding and learning the basic knowledge and methods of improvement activities on the shop floor, participants will be able to confidently engage in improvement efforts.
STEP2 Workshop : Production Line Improvement and 3M Activities
STEP3 Practice : Developing an Eye for Identifying Waste and Improving It
It serves as an opportunity to realize anew the potential on the shop floor, with management often remarking, ‘If we provide training and methods for upgrading the production site, they can take such initiative
The seminar is not the end but the beginning.
Through these activities, we build a system where local staff can proactively engage in improvements and support sustainable improvements.
For those who are looking to explore the potential for improvement activities at overseas factories, please contact Hirayama Corporation. We provide methods that are tailored to local cultures and environments, help to draw out the strengths of the site, and shape the future of your organization.
The consultant who wrote this column
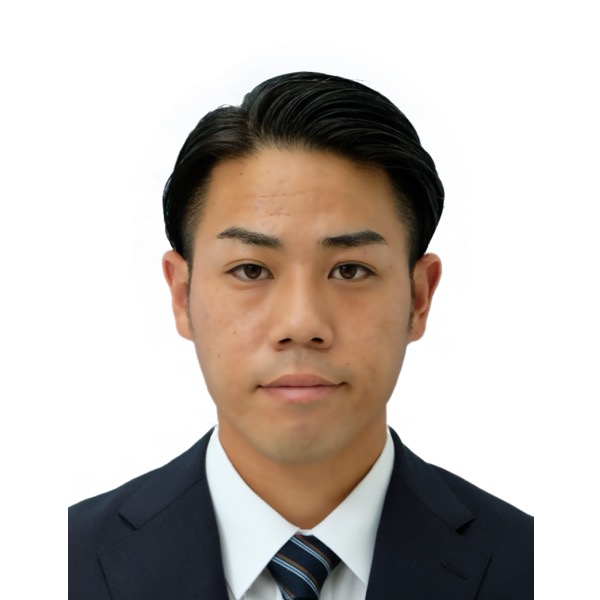
Eiji Hirayama
Hirayama Corporation, Overseas Business Department Supervisor / Former Telecommunications Infrastructure Industry Professional
With extensive experience in the telecommunications infrastructure industry, including project management for base station construction and maintenance, signal transmission operations, software development, and the testing of new equipment and solutions both domestically and internationally.
Currently serving as the Overseas Business Department Supervisor, leveraging past experiences to contribute to the expansion and support of overseas business initiatives.
▼For inquiries about factory assessments, please contact us here.
For inquiries about factory assessment