This is a common term in on-site KAIZEN in China.
I shall report the current state of Chinese on-site KAIZEN from the local community under the COVID-19 pandemic.
Table of contents
- Chinese manufacturing industry accelerating changes under the COVID-19 pandemic
- KAIZEN activities in the manufacturing industry in China
- The reason why KAIZEN of small and medium-sized enterprises is slow to improve
- How shall TPS in China proceed
- A message to Japanese companies that are going to expand to China
1. Chinese manufacturing industry accelerating changes under the COVID-19 pandemic
In 2020, the COVID-19 pandemic caused four major changes in Chinese manufacturing industry.
Change 1: IoT introduction accelerated
The city of Wenzhou, which led to the rapid shut down of the city due to the COVID-19 pandemic, has become clear that many of its production sites use many Chinese workers in traditional manner.
The biggest hurts in manufacturing industry were those with the most workers and those with traditional, non-automatic management techniques.
Regardless of large or small and medium-sized enterprises, the production method with many workers in the old-fashioned work-site has proven to be inefficient, inflexible and expensive to operate under special circumstances such as the COVID-19 pandemic. It has shown that digitization and the introduction of IoT make manufacturing faster, more flexible and less costly.
Chinese manufacturing industry is now signaling the arrival of a full-scale IoT implementation.
Change 2: Activity status for cost reduction and productivity improvement
In recent years, the Chinese manufacturing industry is facing a gradual increase in labor costs, environmental measures, and taxes. In order to improve productivity in various situations, an increasing number of companies have stopped investing in not generating profits, such as human resource development.
Rather than establishing a waste-free manufacturing site through the continuous activities by leaders who have well knowledge of waste-free production sites or by consultants of Japan, Germany, and Korea, companies were trying to reduce costs and improve productivity by implementing IoT in the operational aspects such as supply, marketing, and transportation.
However, cost reduction and productivity improvement cannot be solved simply by reducing training and transportation costs. Because the root causes of wastes are not solved, yet.
“At Post-COVID, practicing and establishing waste-free production site makes possible to reduce cost and improve productivity on the whole shall be the mainstream opinion.”
Change 3: Realignment of the industry from a value chain perspective is inevitable
The pandemic has put many of Chinese manufacturing industries at a risk of survival, especially small and medium-sized enterprises. In order to resume operations that have stopped, business restructuring from the value chain perspective continues to increase.
Some powerful manufacturers don’t miss the opportunity to buy at a low price.
Of course, the Chinese government has taken relief measures to deal with the crisis for survival, such as reducing taxes and fees or providing subsidies. However, few small and medium-sized companies can actually receive subsidies.
In short, many small and medium-sized enterprises today are expected to survive by finding sponsors and other strong external entities.
Change 4: The business model with enhanced cash flow is required
In the past times, many owners of manufacturers had known the importance of cash flow, but in the midst of the current pandemic, many manufacturing management felt the importance of cash flow for the first time in the true sense of its importance. Today, most business owners recognize that cash flow is important in superficial operations, but they have never faced a serious crisis like this before.
A group of small and medium-sized manufacturing companies that are not listed often do not have a cash flow strategy for their business. It is often considered that the causes of collapse of such companies could be by a “bad environment” like COVID-19, but that is a mistake; it is because of not having the cash flow strategy.
Many Chinese management of manufacturing, who experienced the crisis management of cash flow after COVID-19, have realized the real importance of cash.
2. KAIZEN activities in the manufacturing industry in China
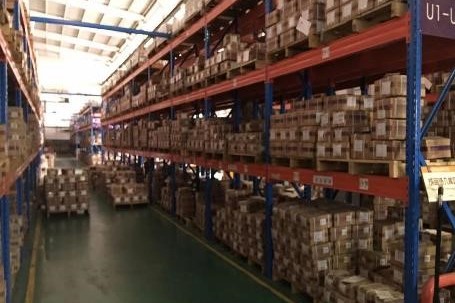
Lean (TPS) in China has been widespread primarily by large companies in automotive, electronics, medical equipment and machinery industries. The results of China FAW Group, Dongfeng, Shanghai Automotive (SAIC), TFTE, Shanghai GM, and SANY Group Company are remarkable.
For example, China Dongfeng carried out the lean product system for a year at its gearbox plant. In terms of production, it doubled its original design capacity, reduced labor capital and production workers by 50 percent, and doubled labor productivity.
On the other hand, a number of small and medium-sized enterprises (with fewer than 1,000 employees) and companies in the Midwest of China are at a low level that they do not yet know about TPS, and the difference between large and small enterprises is significant.
Photo: The production system from the past, which had wastes and used a lot of space and money
3. The reason why KAIZEN of small and medium-sized enterprises is slow to improve
The biggest reason for slow improvement is that the management and leaders do not understand the nature of the TPS. In that situation, they only want to “get results of great improvements in the short term.”
While waste-free production requires continuous KAIZEN, the management and leaders are lacking in the philosophy and recognition of TPS, which prevents them from taking the basics such as 5S seriously, and if ia problem rises, KAIZEN activities shall be stopped.
4. How shall TPS in China proceed
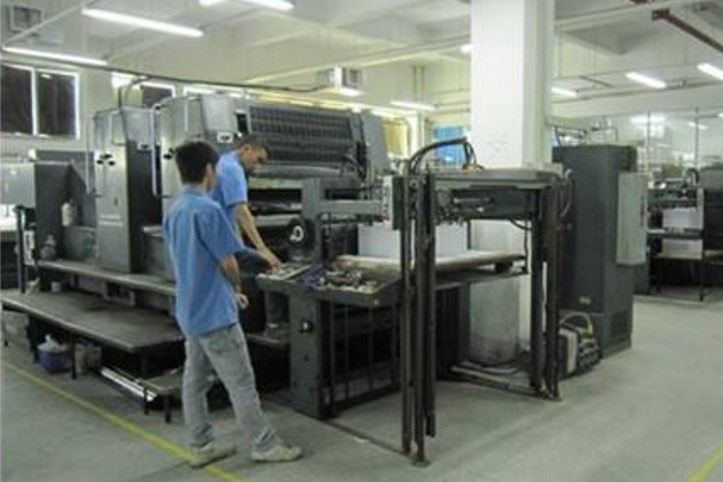
In addition to large enterprises, Japanese-Korean companies, Western companies, Taiwanese companies, and Hong Kong companies have already adopted TPS, and their production systems are well established. Therefore, small and medium-sized enterprises managers and leaders are also aware that the Lean System (TPS) is needed at the manufacturing site, and which is attracting attentions so much.
However, because they have mistaken understanding in regards to TPS, it is essential that we first educate them on TPS. There is still room for the development of the manufacturing industry in China.
5. A message to Japanese companies that are going to expand to China
1. In the future, China will become more aware of the health, safety and quality of life of the Chinese people.
These areas are the strengths of Japanese companies.
Therefore, Japanese companies have a great opportunity to show their strengths.
2. Japanese companies must pay special attention to the development of new infrastructure, which is actively being discussed in China. As the new infrastructure involves many parts, raw materials and production facilities, Japanese companies can still play a very important role. So the business opportunity is huge.
3. The Chinese market has not changed much. China is probably the fastest to recover its economy, and it recovers its economy to the maximum in the world. This is because Japan’s leading companies are looking for a rapid recovery in the Chinese market in order to fill the gap between the U.S. and European markets, and taking actions for that.
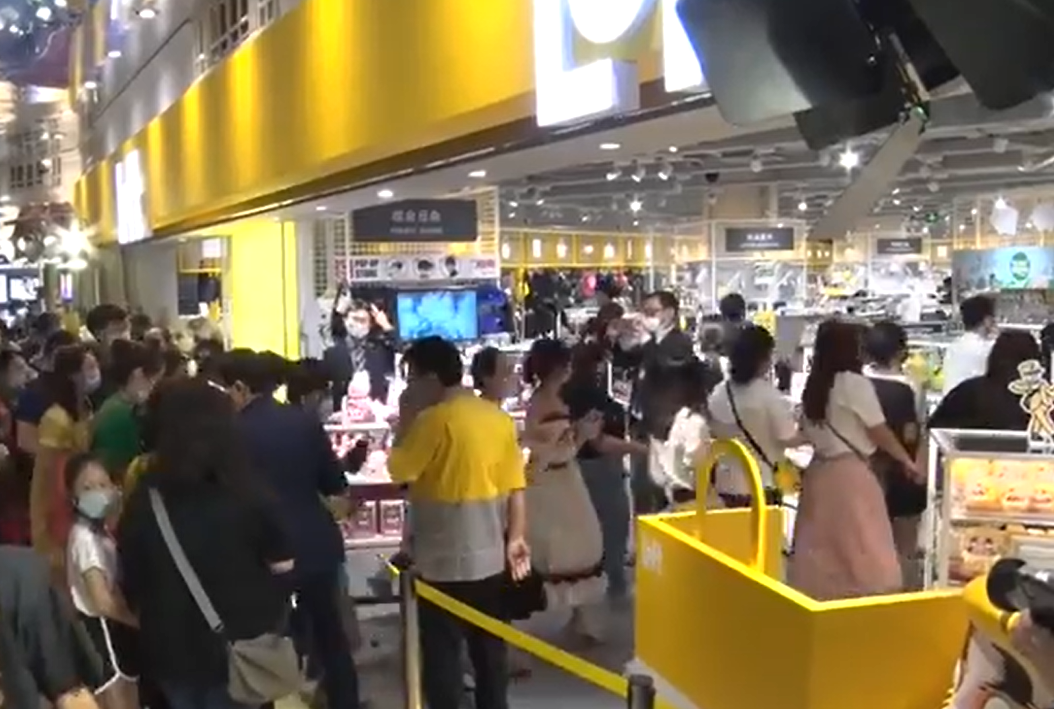
Loft opened its first store for China in Shanghai in July 2020. Loft is a very popular lifestyle collection store with more than 100 stores in Japan, proposing a high quality life. Loft has been receiving high praise from young consumers in China as well. With the store area of approximately 1,046 square meters, the store sells 25,000 to 30,000 items, focusing on the four major categories of stationery, general goods, health goods and daily goods. After the official opening of the store, the sales products shall basically be the same as the Japanese store. (Loft plans to open 6 directory managed stores in Shanghai, Chengdu and other areas within the next three years.)
▼Click here for details on overseas manufacturing support services
overseas manufacturing support servicesConsultant who wrote this article
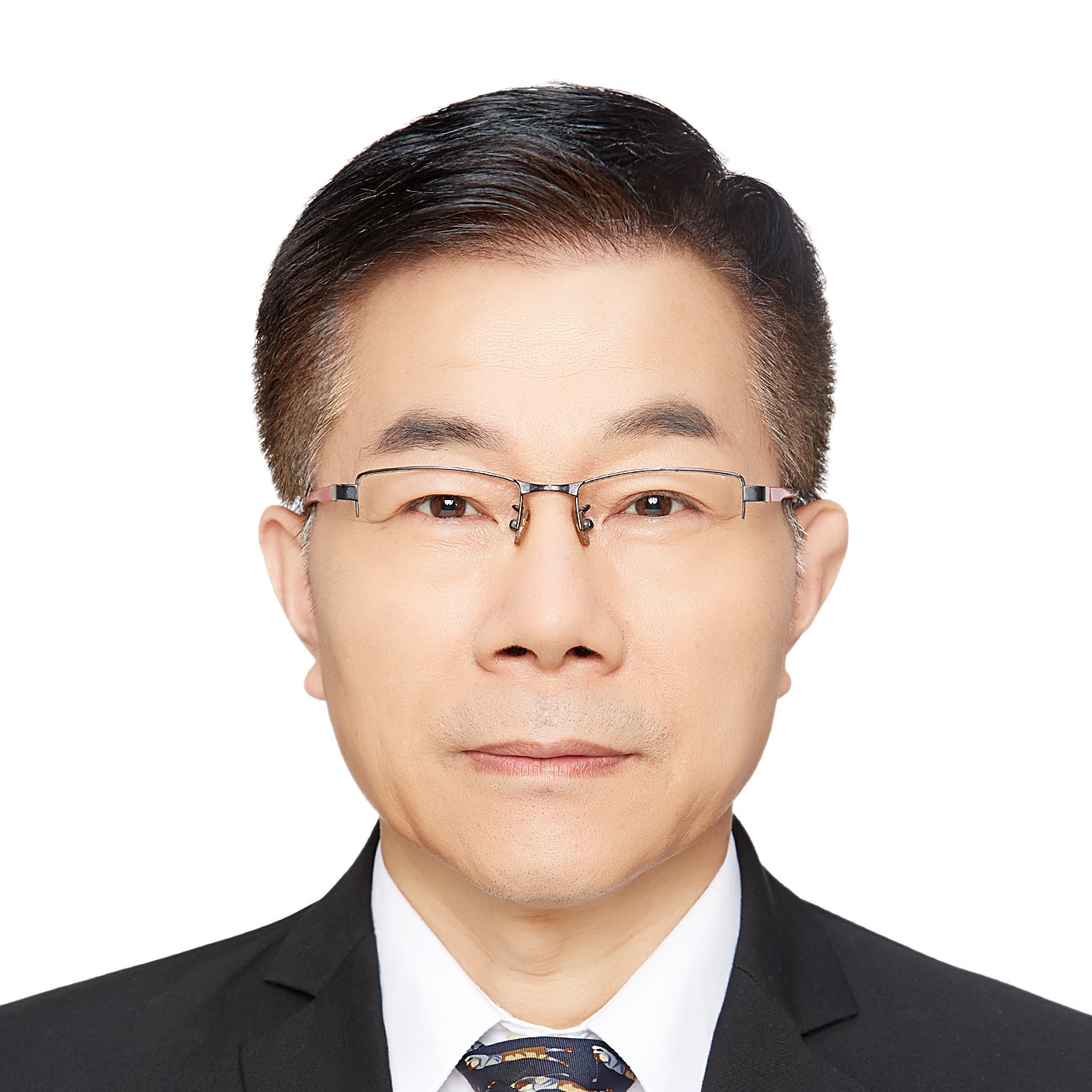
Haku Keizen (白 敬全)
Gemba (Work-site) KAIZEN consultant (China)
Worked for GM and Toyota affiliated companies, and then served as vice president of Toyota affiliated companies for more than 10 years. In addition, there is abundant experiences in work-site guidance for local companies in China, the United States, and Japan. He is a professional consultant of TPS and Lean.