自分たちで“ムダ”を発見できる!!
現場が変わり、会社が変わる!!
結果
(改善前)約1,570分
(改善後)約1,200分
A社では、全社挙げての改善活動を実施する方針を定め、間接部門を含む改善プロジェクトを立ち上げ2年間実施することとなり、
弊社は改善指導の依頼を受けた。
以後、生産部門、品質部門、技術部門、資材部門の各部門で改善への取組みを進め、全ての部門で大きな成果を創出するとともに、メンバー一人ひとりの改善への意識高揚に繋げることができた。
ここでは、生産部門でのムダ排除の取組み事例を紹介する。
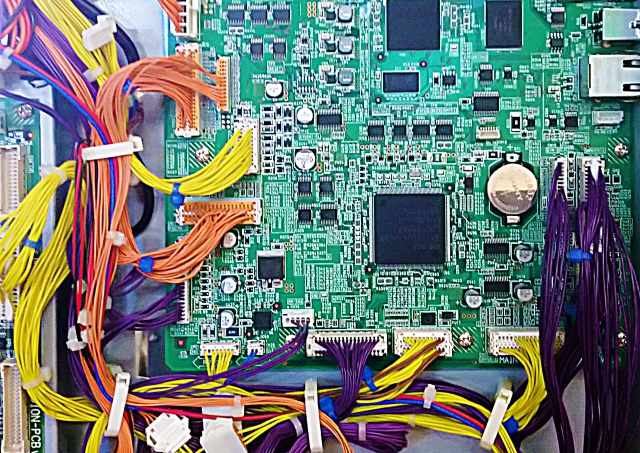
- 業界詳細
- OA機器製造など
- 国
- 日本
- 企業規模
- 従業員 500名以上
- 課題
- 生産性の向上、その他
- 目的
- 収益改善
- 業界
- 電機・電子
スケジュール
- 現場診断
- TPS研修
- キックオフ
- 改善活動
ムダ排除の取組み事例
サイクルタイムの長い現場で、作業者は30秒~1分程度歩いて遠方の部品置場に部品を取りに行くことに何の問題意識も持っていなかった。はじめは、問題意識が欠如していたため、多くの“ムダ”が当たり前に潜んでいる現場であったが、改善指導が進むにつれ、多くの成果を創出することができ、製品の生産時間が2年間で約1,570分→約1,200分に短縮した。(370分短縮:23%低減)
(改善前)比較的小さい部品ユニットの組立は、別場所で一度に大きいバッチ生産をしていたため、作り過ぎのムダがあった。 (改善後)作り溜めを廃止しインライン作業とすることで、部品ユニット組立と総組立てを1:1で対応することにより、ムダを排除することができた。 | |
(改善前)ライン作業者が大物部品を遠方の部品置場に取りに行っていた。 (改善後)ライン内作業とライン外作業を完全分離のうえ、部品配膳に特化した「水すまし」を配置。 各工程にシグナルタワー(行灯)を設置し、「問題発生」「部品切れ」「応援要請」を直ちに周囲に知らせる仕組みを作ることにより、ラインバランス調整による手待ち時間解消を図った。 | |
(改善前)
部品を固定する治具の設置がねじ止め方式 (改善後)クランプ方式に変更することで、作業時間の短縮、作業負荷軽減を図った。 また、薬品ポンプの横にウエスが置いてあったものを薬品ポンプ台と一体化させ、動作軽減とスペース極小化を図った。 |