7カ月間徹底したムダとりの実践
小さな工場でもTPSで大きなコストダウン!!
結果
効果金額:年間100万元(約1,700万円)
7カ月間のTPS導入プロジェクトを実施した、中国昆山にある表面処理メーカーの改善成果と事例を抜粋し紹介いたします。
活動期間
2017年3月~10月(7ヶ月間)
活動内容
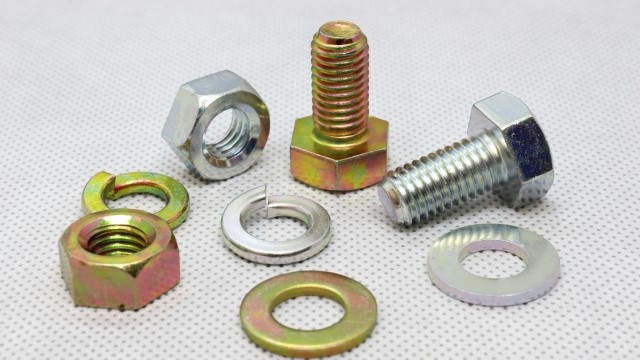
- 業界詳細
- 表面処理
- 国
- 中国
- 企業規模
- 従業員 約160名
- 課題
- 生産性向上
- 目的
- 収益改善
- 業界
- 金属
スケジュール
- 現状調査
- 問題点の洗い出し
- 改善案検討
- 改善実施
- 効果の検証
前半の改善成果
工程 | 改善前 → 改善後 | 改善効果 | コストダウン |
組立 | 7人 → 6人 630分/人 → 400分/人 7*630=4410分 → 6*400=2400分 |
省人1人 230分/人 4410-2400=2010分 |
192960元 |
分解 | 19人 → 13人 72分/人 → 72分/人 19*72=1368分 → 13*72=936分 |
省人6人 1368-936=432分 |
41472元 |
下ろし、全検 | 11人 → 6人 630分/人 → 400分/人 11*630=6930分 → 6*400=2400分 歩留まり:85% |
省人5人 230分/人 6930-2400=4530分 歩留まり:95% |
434880元 1000*1.64*1.5=2460元 2460*24*12=708480元 |
後半の改善成果:工場レイアウト
1. 全検ラインのレイアウト改善
264秒/パレットの運搬ムダを刈り取った。
年間コストダウン:264秒*20パレット/3600秒=1.46時間*20元*22日*12月=7708元
2. 全検の通い箱置き場変更
作業手順を変更し、20パレット/日,600個の通い箱を生産量とする。
年間コストダウン:20パレット*96秒+600箱*9秒=7320秒/3600秒=2.0時間时*20元*22日*12月=10718元
イレクターによる改善事例
改善事例1
改善前 | 改善後 |
![]() |
![]() |
紙はラインの上に置き、作業補助台が8台ある。不良品入れも定位置もなく台の下か横に置かれ、乱雑だった。 | 作業に合わせ、イレクターで補助台を作成し、図のように2名で1台を使用し、全部で4台を設置。紙・箱・不良品入れを定位置に置くことができた。作業のしやすさ、作業の見える化を実現し、作業ルールの統一を図れた。 |
改善事例2
改善前 | 改善後 |
![]() |
![]() |
図のように、中間のイレクターが縦向きに組んだため、箱が非常に不安定。 | 縦向きを横向きにすることにより、箱が安定し、重量も耐えられるようになった。 |
現場改善のスペシャリスト

伊藤 彰洋(いとう あきひろ)
現場改善コンサルタント
業種を問わず、現場改善の文化を企業へ根付かせ、現場の人間と共に改善活動をおこない、品質向上・生産性向上・リードタイム短縮を実現する。 また、生産管理システムを手掛けた経験により、「営業~資材~生産管理~製造~外注」と工場内のあらゆるプロセスにおいて改善活動を実践する。
選ばれる3つの理由 REASON
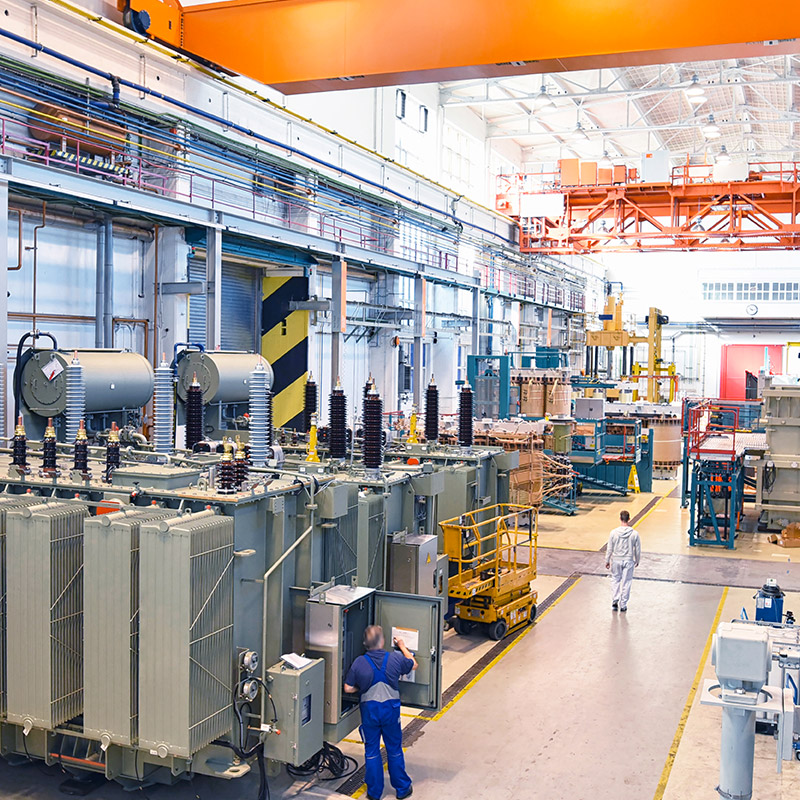
REASON 1
40ヶ国、
1,500社以上の改善実績
自社だけでは解決できない現場の問題は必ずあります。製造業が勝ち残るための改善・改革は、国や業界を問わず、改善の実践体験を通じて、人材を育成し、生産体制基盤を強化することが必要です。
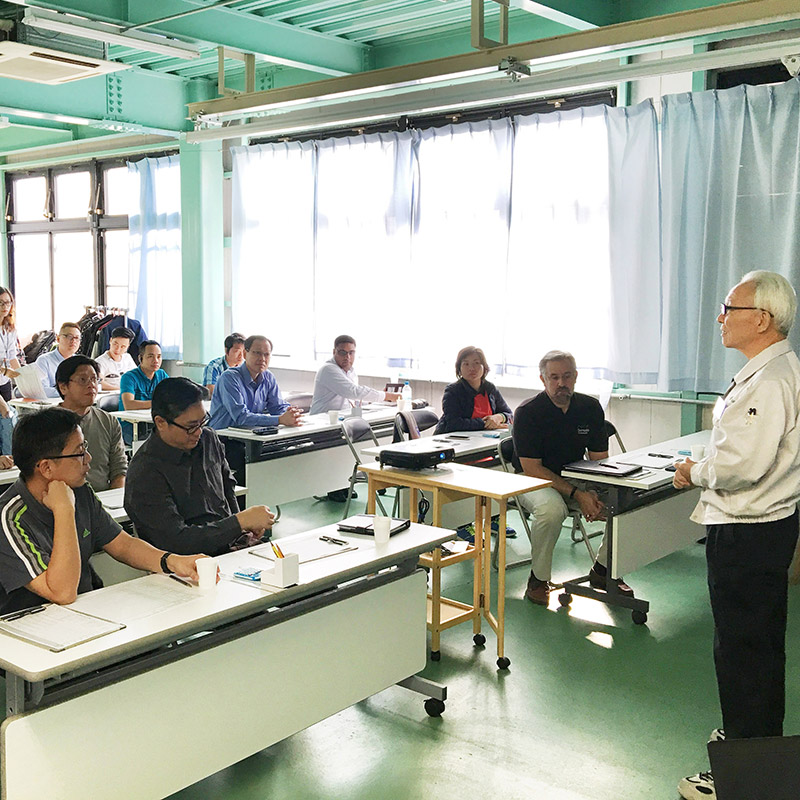
REASON 2
現場が一目置き、
喜ぶコンサルティング
従来のコンサルティングでは、経営層とコンサルタントが中心になってすすめるため、現場とコンサルタントの間に距離がありました。弊社コンサルタントは、評論家的な「あら探し」ではなく「改善の種」を具体的に見出す指導により、現場の人間との隔たりのない指導をすることができます。
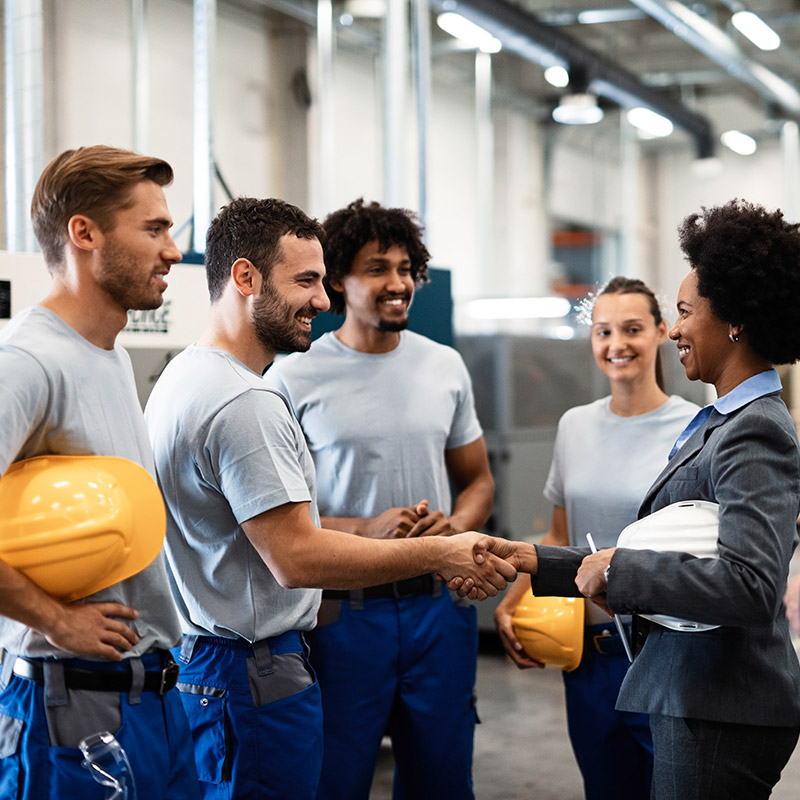
REASON 3
指導終了後も
継続的改善がされる
「人づくり」を強化しながら、設計から調達・製造・物流、そして生産管理と「全体の流れ」を重視し、貴社の現場の実態に合った指導を実施。現場が納得できるコンサルティング指導を行うことで、指導終了後も改善文化が継続されます。