ローカライズが鍵!
平山では世界40ヶ国の実績で、
現場改善をローカライズします。
結果
- 段取り替え時間 50%短縮
- 生産性 30%UP
- リードタイム短縮 30%
海外でリーン生産方式を導入する際に気を付けることは、日本では当たり前に使われているの言葉の意味が違った解釈をされたり、文化の違いで考え方が理解されていない場合が多いので、そこら辺からしっかりと現地語で基礎教育していく事が重要です。
その点、今回のプロジェクトでは現地で活動経験豊富なコンサルタントが、ローカルスタッフと強い信頼関係を構築し基礎教育·意識改善を行いながらリーン生産方式の導入を進めたので、短期間で大きな成果を出すことが出来ました。
※1.リーン生産方式とは、1980年代にアメリカのマサチューセッツ工科大学(MIT)がトヨタ生産方式「TPS(Toyota Production System)」を研究し、体系化・一般化したもの。
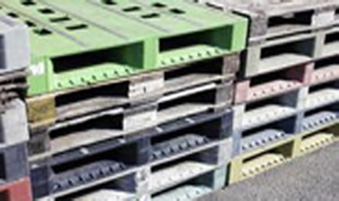
- 業界
- プロスティック部品の加工
- 国
- 東南アジア
- 企業規模
- 従業員 約320名
- 課題
-
過剰な在庫
リードタイムの短縮 - 目的
-
リーン生産方式の導入
コスト削減リードタイム短縮その他 - 業界
- 自動車
スケジュール
- 現状調査
- 改善チームの設立、育成
- 改善工程の決定、改善計画の作成
- 改善活動
- 改善チェック、是正処置
- 標準化、よこてん
「物と情報の流れ線図」による現状調査
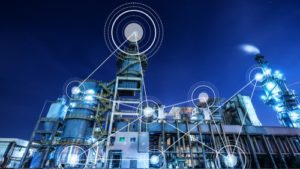
現状調査で分かったことは、過剰な仕掛在庫がモノの流れを阻害しリードタイムを長大化させていた。
過剰な仕掛在庫は、ロット生産・ジョブショップ・段取り時間が長い・生産指示が悪い・工程内不良が多いなど様々な問題がからみあっている事が原因だが、生産現場は仕掛在庫をある程度持っておかないと納品が遅れ売上が減少するという認識であった。
これは正に過剰な仕掛在庫を持って現場の悪さをカバーしている事であり、リーン生産方式とは正反対の考えであった。
まずは「物と情報の流れ線図」を作成し、受注から納入までの流れの中にある仕掛在庫を把握し現状のリードタイムを共有し、仕掛在庫削減とリードタイム短縮を目標とした改善活動を行うことにした。
仕掛在庫削減とリードタイム短縮改善
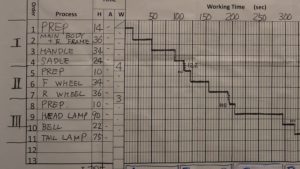
まずは「段取り替え」の作業分析を行なった。そして、段取り替え作業を
・内段取り
・外段取り
・ムダ
の3つに分類し明確化。
ムダの削除、内段取りの外段取り化、オペレーター教育をすすめ、段取り替え時間をなんと50%短縮し小ロット生産することに成功した。 更に、「工程のライン化」、「品質を工程の中でつくり込む」を改善して生産性も30%向上した。
リーン生産方式のスペシャリスト
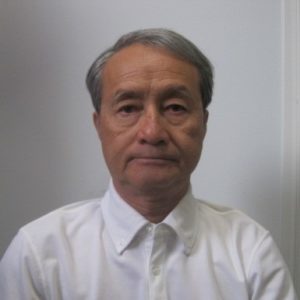
森嶋 敏雄(もりしま としお)
デンソーOB 元デンソーマレーシア工場長、元ブラジル工場長
デンソー イタリア工場の経営コーディネター等、実績豊富。マレーシア・日本両国政府の生産性向上プロジェクト(MAJAICO)のメンバー。海外における経験が豊富。英語での対応可ゆえ通訳は不要。
選ばれる3つの理由 REASON
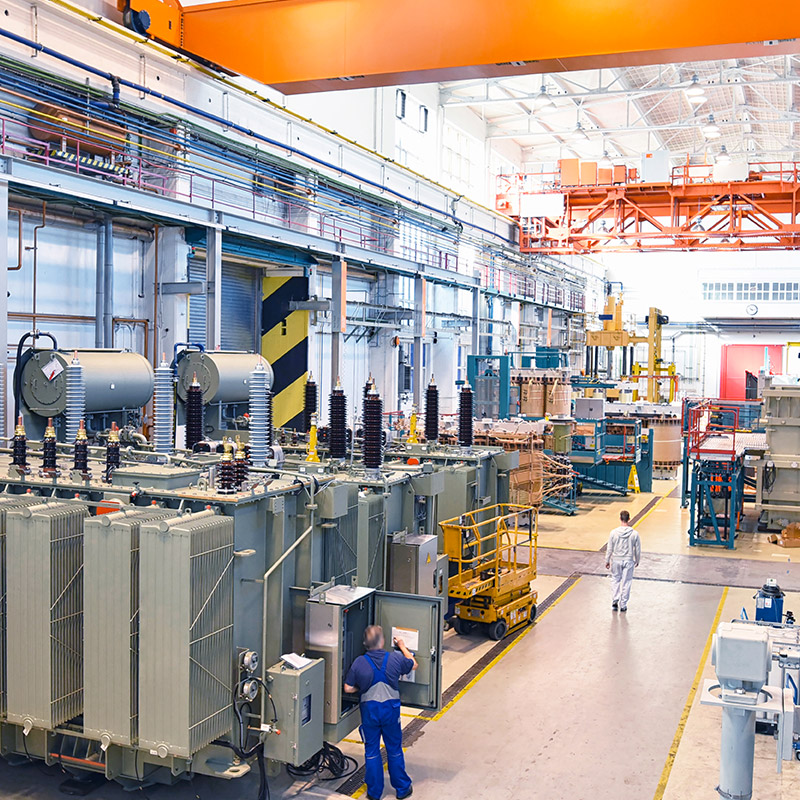
REASON 1
40ヶ国、
1,500社以上の改善実績
自社だけでは解決できない現場の問題は必ずあります。製造業が勝ち残るための改善・改革は、国や業界を問わず、改善の実践体験を通じて、人材を育成し、生産体制基盤を強化することが必要です。
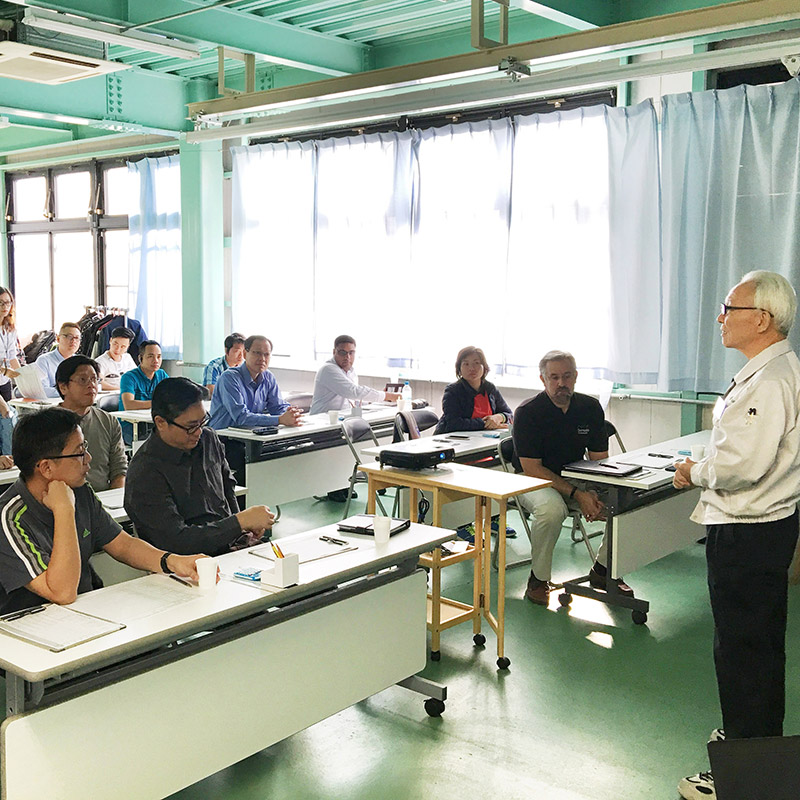
REASON 2
現場が一目置き、
喜ぶコンサルティング
従来のコンサルティングでは、経営層とコンサルタントが中心になってすすめるため、現場とコンサルタントの間に距離がありました。弊社コンサルタントは、評論家的な「あら探し」ではなく「改善の種」を具体的に見出す指導により、現場の人間との隔たりのない指導をすることができます。
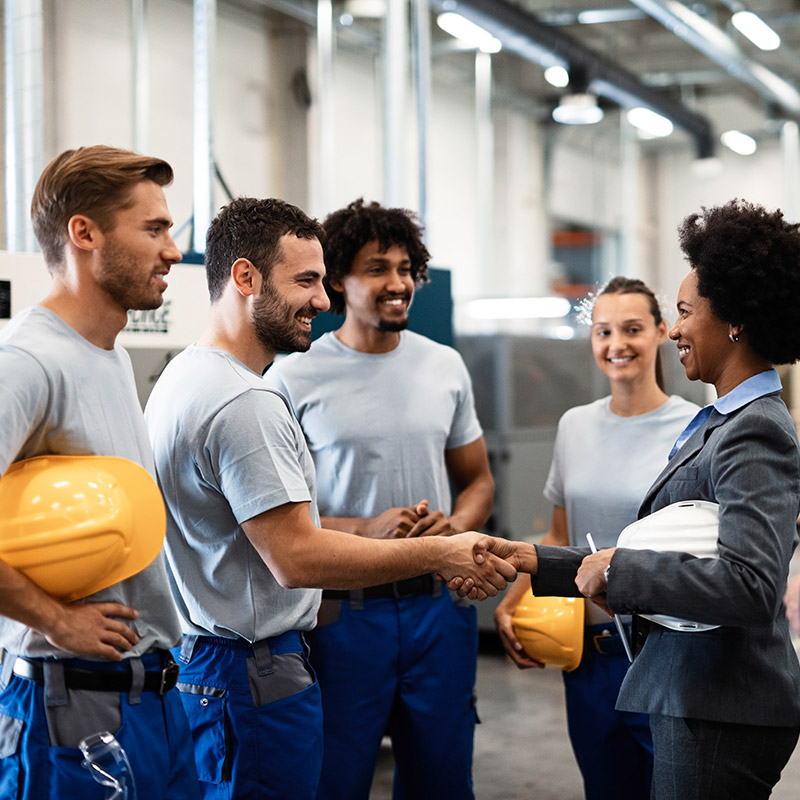
REASON 3
指導終了後も
継続的改善がされる
「人づくり」を強化しながら、設計から調達・製造・物流、そして生産管理と「全体の流れ」を重視し、貴社の現場の実態に合った指導を実施。現場が納得できるコンサルティング指導を行うことで、指導終了後も改善文化が継続されます。