座学ではなく現場での改善実践
生産現場から間接部門の改善活動へもスムーズに展開
結果
月末在庫金額の24%低減
倉庫内物流の44%低減
リードタイム5日短縮
<品質技術部・品質管理課>
部品サプライヤの10社全てで不良が合計45%の減少
2Sと業務の視える化をテーマに、全社的改善活動を社長が主導。
弊社は改善活動スタート時から全面的にサポート。
トヨタ生産方式(TPS/JIT)を基本とし、座学ではなく現場での改善の実践を掲げ、何より改善を継続的に推進できる「人材を育てる」ことを目的とする方針が、S社と改革の方向性が合致。
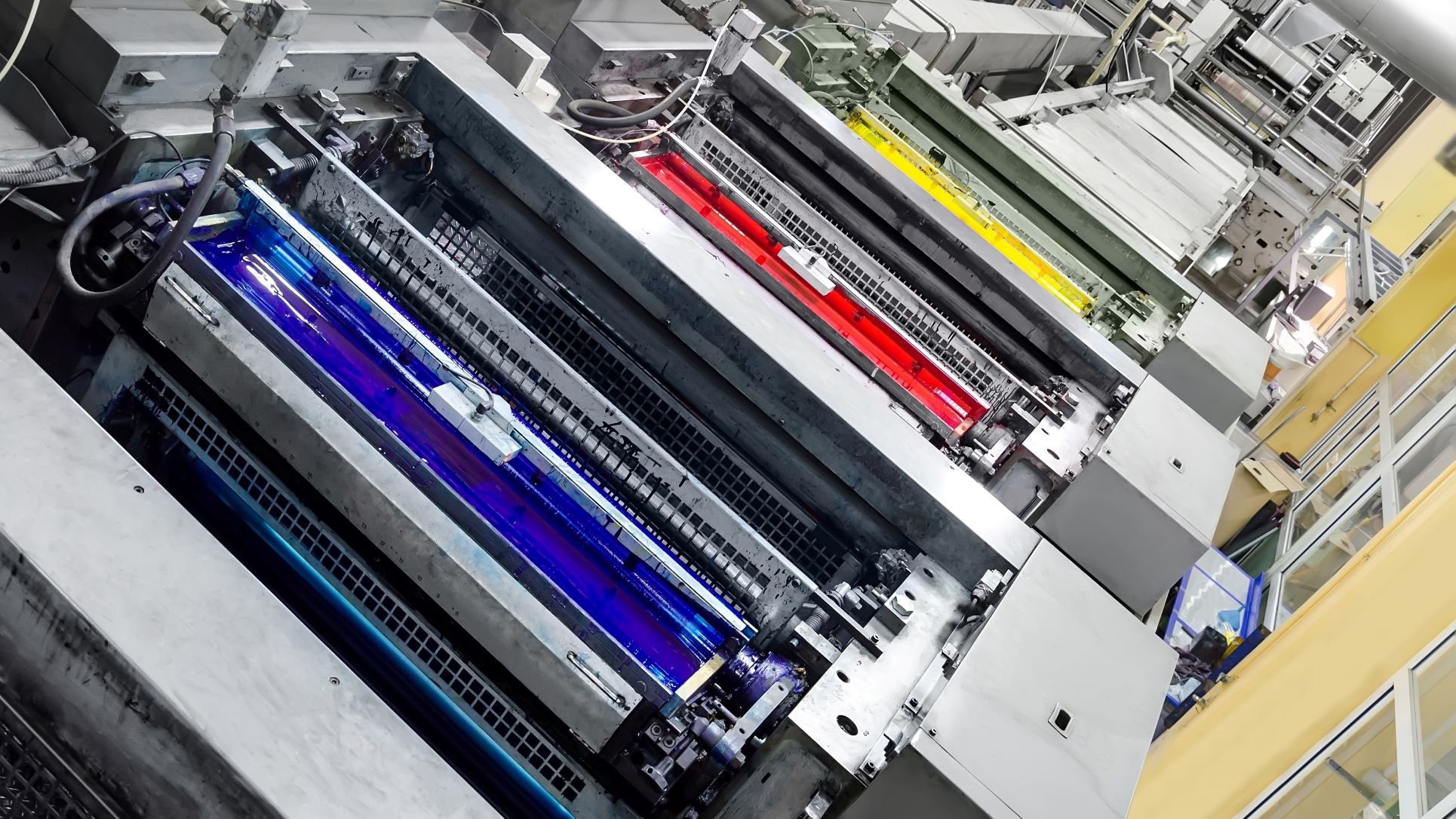
- 業界詳細
- OA機器メーカー
- 国
- 日本
- 企業規模
- 従業員 380名
- 課題
- 収支改善
- 目的
- 人材育成
- 業界
- 電機・電子
進め方
最初の2年間は現場改善指導に重点を置いて改善活動を始動し、3年目から間接部門を巻き込んだ全社を挙げての改善活動へと展開。最終的に、自主改善が展開できる人材育成を目指す。
問題点
- 管理者自身が部員の業務内容が見えていない。
- 業務の進捗管理ができていない。
- 業務の多能工化が進んでいない。
間接部門を巻き込んだ改善活動初年度の取り組み内容
No | 部門 | 主な改善項目 | 改善内容 |
1 | 生産管理部門 |
| |
2 | 製造部門 |
|
|
3 | 品質部門 |
|
|
4 | 生産技術部門 |
| |
5 | 資材部門 |
| |
目標に対する主な実績
目標 | 実績 |
<生産管理部門> 月末在庫金額の15%低減 倉庫内物流の40%低減 リードタイム5日(1週間)短縮 <品質技術部・品質管理課> 部品サプライヤの不良発生を半減化 |
⇒24%低減 ⇒44%低減 ⇒5日短縮 ⇒10社全てで不良が減少(合計45%の減少) |