Practical Kaizen Implemented in the Genba instead of Class Lectures
Kaizen Activities Rolled out Smoothly from Production Site to Administrative Area
Results
24% Reduction in End-of Month Inventory
44% Reduction in Warehouse Logistics
Lead Time Shortening by 5 Days
<Quality Technology Department/ Quality Control Section>
45% Reduction of Defects Rate in Total of All 10 Supplier Company
Kaizen Case with Company-wide improvement activities under the theme of visualization of 2S and operations led by the CEO.
Full support from the start of improvement activities.
The plan based on the Toyota Production System (TPS / JIT), with the aim of “cultivating human resources” who can continuously promote improvement with the practice of on-site improvement rather than classroom lectures, matched withthe company S policy.
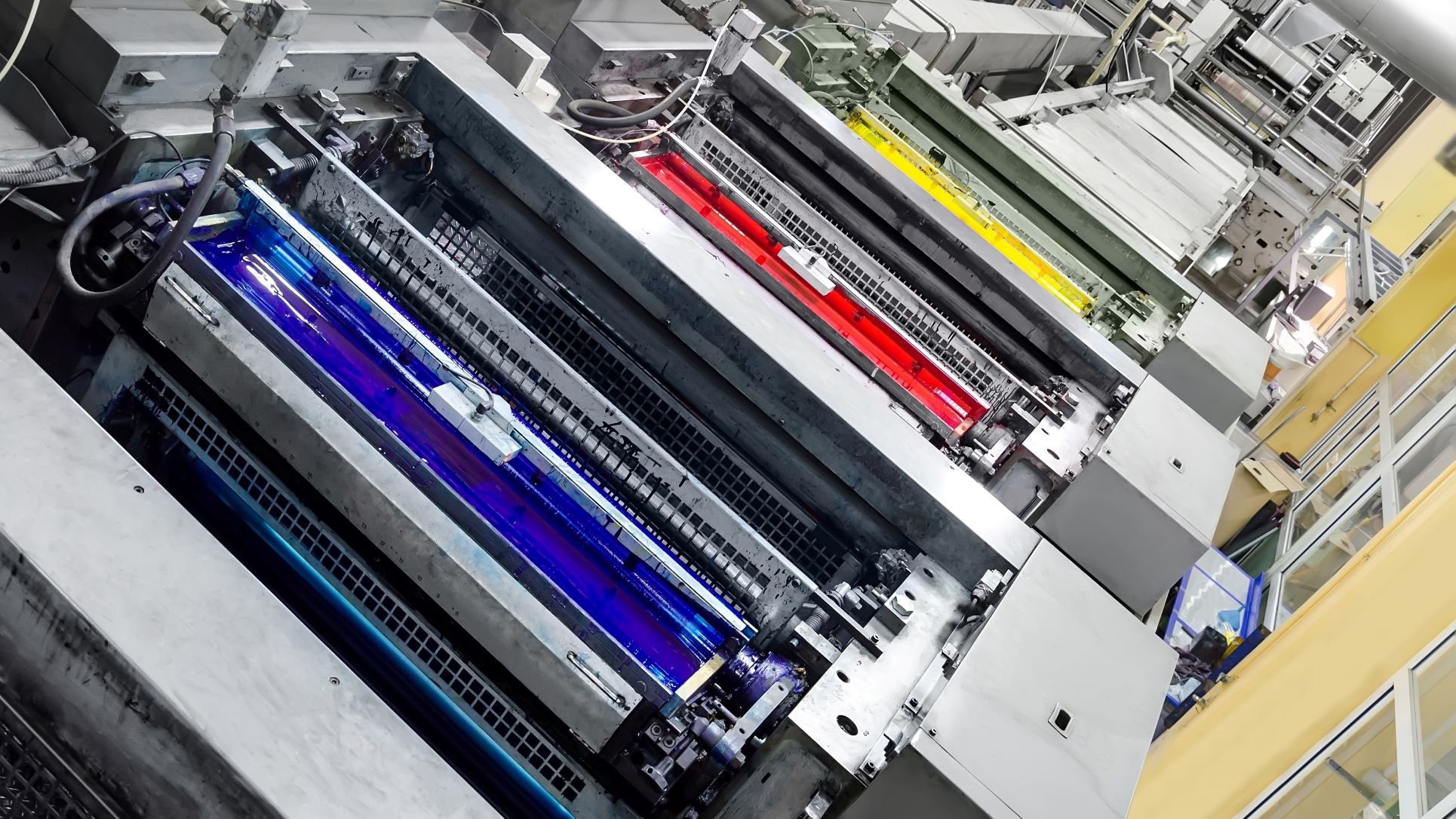
- Company Detail
- OA Equipment Manufacturer
- Country
- Japan
- Employees
- About 380
- Issue
- Profit Improvement
- Purpose
- Human resource development
- Industry
- Electrical and electronic
How it was deployed
For the first two years, we implemented KAIZEN (improvement) activities focused on production-site and from the third year we expanded the activities to company-wide by involving administrative departments.At last, we targeted to develop human resources who can proceed improvements by themselves.
Problems/opportunity
- Operations of members are invisible for managers.
- Progress of operations cannot be controlled.
- Lack of nurturing of Multi-Skilled Workers.
Details of KAIZEN Activities of First Year Involving Administrative Areas
No | Department | Main Improved Items | Contents of Improvement |
1 | Production Control Department |
| |
2 | Manufacturing Department |
|
|
3 | Quality Department |
|
|
4 | Production Engineering Department |
| |
5 | Materials Department |
| |
Key Achievements toward Targets
Target | Achievement |
15% Reduction in end of month inventory 40% Reduction in logistics in warehouse Lead Time Shortening by 5 days (1 week) Halve the occurrence of defects in parts suppliers |
⇒Reduced 24% ⇒Reduced 44% ⇒Shortened 5 days ⇒Reduction of defects in all 10 companies (45% reduction in total)) |