ビデオで現場診断
オンラインの現場改善コンサル
結果
(改善前)92分34秒→(改善後)53分2秒(39分32秒削減)
東アジアにあるA社では、輸出向けの製品を製造している。
<A社の課題>
弊社で3カ月のオンラインセミナーを行い、生産性30%UPを達成するため、2020年より1年間のオンラインコンサル指導を受けた。
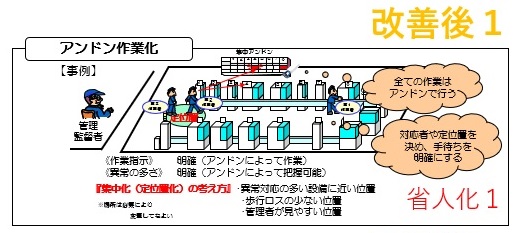
- 業界詳細
- その他の製造
- 国
- 東アジア
- 企業規模
- 従業員 数百名
- 課題
- 生産性UP
- 目的
-
1年間で生産性30 %UPするとともに、自社の改善ノウハウを構築する
収益改善 - 業界
- その他
スケジュール
- 現状把握:経営者、現場責任者とミーティング
- オンラインセミナー:セミナーとワークショップ
- オンライン現場診断:改善スケジュールの作成
- オンラインコンサル:月2回×12ヵ月(作業改善)+集中改善5日間×2回(レイアウト変更、設備の入れ替え)
セミナーとワークショップ
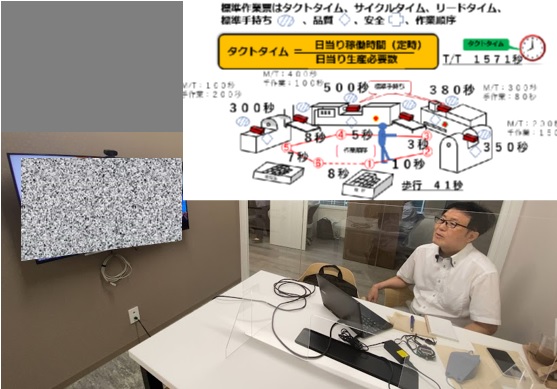
オンライン現場コンサルティングでは、事前に、動画や写真、その他、現場を理解するのに必要な資料を共有させて頂きます。
セミナーやワークショップでは、その時の動画を使い、実践的に改善の考え方を習得します。
<セミナーの目的>
オンライン現場診断
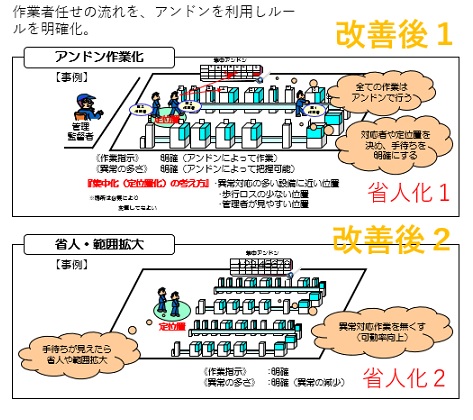
当社の現場改善コンサルの特徴は、実際の現場にコンサルタントが作業や流れを確認して、作業者や責任者とコミュニケーションをとりながら一緒に現状を把握し、改善計画をたて実行することです。
オンラインコンサルでも、改善方法は同じです。
現場診断は、撮影頂いた30分(15分×2本)のビデオをもとに行いました。
生産性30%UPを目標を、具体的にどこをどう改善すれば達成できるかは、セミナーやワークショップをとおして全員で共有しながら、いっしょに作成します。(現状を正しく把握し、本来あるべき姿を想像し、そのギャップをうめるための改善方法を考察する)
<改善例>
大変古い設備を利用しており、新規設備の導入も含めた改善となりました。
大きな投資となりますが、計画的にすすめるために、まず作業者・責任者・経営者が現状の問題点を正しく理解することが重要です。
標準作業組み合わせ表を作成し、作業改善をおこなったうえで、新設備の導入となります。
段取り変えの作業改善
1)標準作業組み合わせ表の作成
2)段取り変え作業時間の測定・・・92分34秒
3)ビデオを見ながら、動作12のムダ出しなど・・・6分37秒削減
4)金型準備、軽油準備は外段取り化・・・12分14秒削減
5)18項目あった部品調整のうち、7つを外段取り化・・・20分41秒削減
6)作業台などレイアウト変更(39分32秒改善)
お客様が平山を選んだ理由
弊社では、コロナ禍以前より、オンライン現場改善サービスをスタートさせておりました。特に海外工場においては、予期せぬ事態においても、緊急で打ち合わせを開くことができ、通常のコンサルよりスピーディーな改善が実施できるようになりました。
現場に行かずしても、映像や写真、図面を見て、現場コンサルティングを行うことは大変難しいです。オンラインコンサルタントができるコンサルタントは稀な存在です。
お客様からは、オンラインであっても確かな現場把握を行い、改善ができるコンサル能力と実績および、上から目線の改善指示だけではなく、現場によりそった改善活動が評価されご用命を頂きました。
今回、生産性30%UPを達成できましたのは、現場の方々、責任者の方々、経営者の方々が、困難に打ち勝つことを決意され心が1つとなり、失敗をおそれず行動してくださったからです。この1年間の経験・ノウハウは、社員のモチベーション、社風や育成制度などにも影響し、生産性30%以上の効果をもたらすでしょう。
オンライン現場改善のスペシャリスト
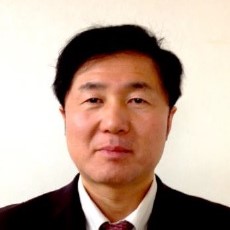
柿沢 高一(かきざわ こういち)
リコーOB 品質保証部・製造技術部
リコーにてトヨタ生産方式をベースにリコー生産方式を立ち上げ。その後、食品・菓子、医療業界など他業種にトヨタ生産方式を実践指導。 マシンの生産性向上、ネックマシンの能力向上、コンベア生産の原価低減、セル生産(1人方式・巡回方式・分業方式・分割方式)の構築、台車引き生産方式の構築、5S職場風土づくり、品質・設備管理を実践する。
選ばれる3つの理由 REASON
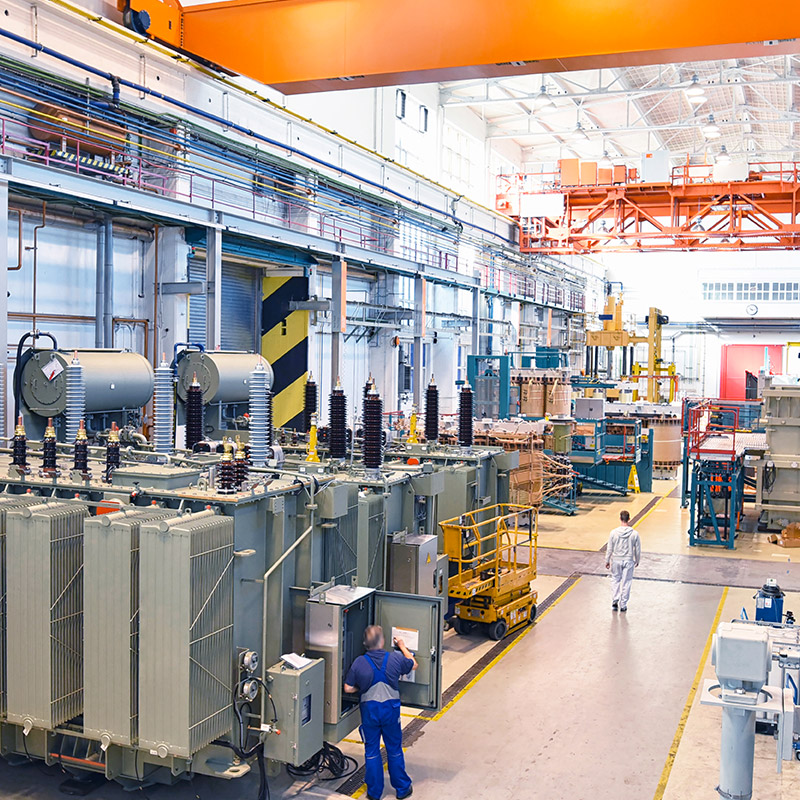
REASON 1
40ヶ国、
1,500社以上の改善実績
自社だけでは解決できない現場の問題は必ずあります。製造業が勝ち残るための改善・改革は、国や業界を問わず、改善の実践体験を通じて、人材を育成し、生産体制基盤を強化することが必要です。
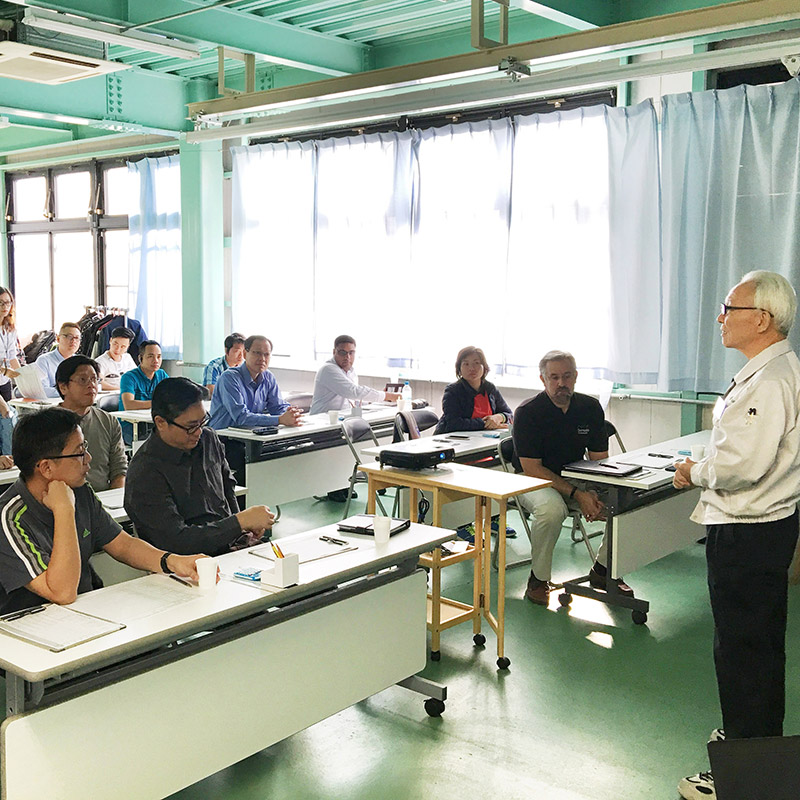
REASON 2
現場が一目置き、
喜ぶコンサルティング
従来のコンサルティングでは、経営層とコンサルタントが中心になってすすめるため、現場とコンサルタントの間に距離がありました。弊社コンサルタントは、評論家的な「あら探し」ではなく「改善の種」を具体的に見出す指導により、現場の人間との隔たりのない指導をすることができます。
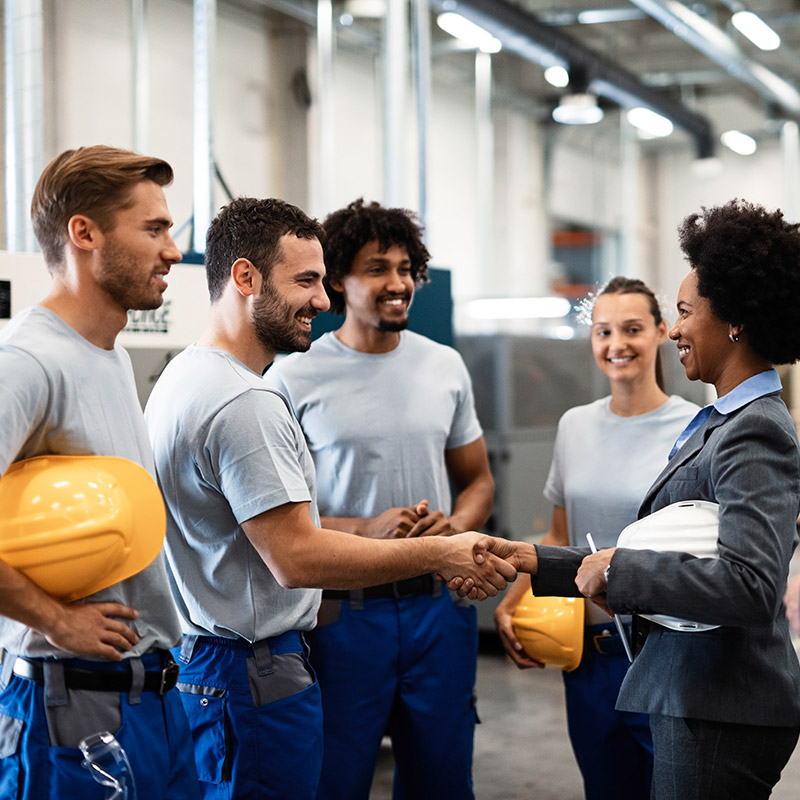
REASON 3
指導終了後も
継続的改善がされる
「人づくり」を強化しながら、設計から調達・製造・物流、そして生産管理と「全体の流れ」を重視し、貴社の現場の実態に合った指導を実施。現場が納得できるコンサルティング指導を行うことで、指導終了後も改善文化が継続されます。