Diagnosing the Site through Video
Online On-site Improvement Consulting
Results
(Before Improvement)92 minutes 34 seconds→(After Improvement)53 minutes 2 seconds (reduced by 39 minutes 32 seconds)
Company A, located in East Asia, manufactures products for export.
<Company A’s issues>
The company participated in a three-month online seminar with our firm and received one year of online consulting guidance starting from 2020 to achieve a 30% increase in productivity.
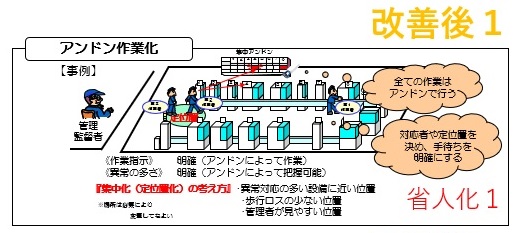
- Industry Details
- Other manufacturing
- Country
- East asia
- Company size
- Hundreds of employees
- Assignment
- Increase productivity
- Purpose
-
Over the course of one year, they not only achieved a 30% increase in productivity but also developed their own improvement know-how.
Profitability improvement - Industry
- Others
schedule
- Current Situation Assessment: Meeting with Managers and Site Supervisors
- Online Seminar: Seminar and Workshop
- Online Site Diagnosis: Creation of an Improvement Schedule
- Online Consulting: Twice a month for 12 months (Work Improvement) + Two intensive improvement sessions of 5 days each (Layout changes, Equipment replacement)
Seminars and workshops
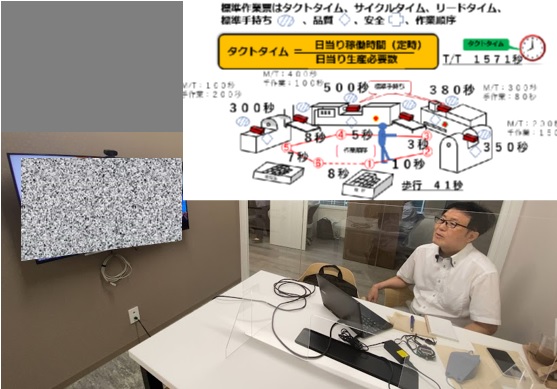
In online on-site consulting, we will share videos, photos, and other materials necessary for understanding the site in advance.
During seminars and workshops, we use current videos to practically learn improvement methodologies.
<Purpose of the seminar>
Online Site Diagnosis
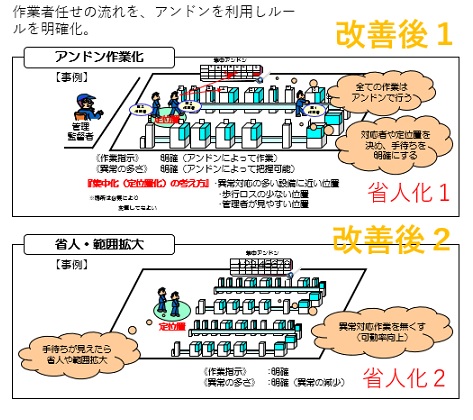
The hallmark of our on-site improvement consulting is that consultants actually visit the site to observe operations and workflows, engaging directly with workers and supervisors to understand the current situation and jointly develop and implement an improvement plan. The approach to improvement remains the same even in online consulting.
The site diagnosis was conducted based on 30 minutes of video footage (two 15-minute clips) provided by you.
The goal of achieving a 30% increase in productivity will be concretely determined through seminars and workshops, where everyone will share and collaboratively develop how and where improvements can be made. (This involves accurately understanding the current state, envisioning the ideal state, and contemplating improvement methods to bridge that gap.)
<Improvement Case Study>
The company was using very old equipment, so the improvement included the introduction of new equipment. Although this represents a significant investment, it is crucial for workers, supervisors, and managers to accurately understand the current issues as a first step in proceeding with the plan systematically.
After creating a standard work combination table and improving the operations, the introduction of new equipment will follow.
Improvement of Setup Change Operations
1)Creation of Standard Work Combination Table
2)Measurement of Setup Change Operation Time: 92 minutes and 34 seconds
3)While reviewing the video, identifying waste in 12 movements, etc… resulted in a reduction of 6 minutes and 37 seconds.
4)Externalizing the preparation of molds and light oil preparation… reduced by 12 minutes and 14 seconds.
5)Of the 18 items for part adjustments, externalizing 7 items… reduced by 20 minutes and 41 seconds.
6)Changing the layout, such as workbenches… improved by 39 minutes and 32 seconds.
The Reason Customers Choose Hirayama
Our company had launched online on-site improvement services even before the pandemic. Especially for overseas factories, this allowed us to hold emergency meetings in unforeseen situations, enabling quicker improvements than regular consulting.
Conducting site consulting without being physically present, through videos, photos, and drawings, is extremely challenging. Consultants capable of providing online consulting are rare.
Our clients have chosen us because, even online, we are able to accurately grasp the situation on-site and make improvements. Our consulting skills and track record, along with our approach of not just giving top-down improvement instructions but also engaging in improvement activities that are closely aligned with the site, have been highly valued.
The achievement of a 30% increase in productivity was possible because the people on the ground, the supervisors, and the executives were united in their determination to overcome difficulties, acted without fear of failure. The experience and know-how gained over this year will influence employee motivation, company culture, and training systems, likely leading to productivity gains of over 30%.
Specialist in On-site Improvement
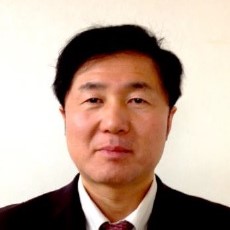
Koichi Kakizawa
Former Ricoh Employee, Quality Assurance Department & Manufacturing Technology Department
At Ricoh, initiated the Ricoh Production System based on the Toyota Production System. Later, provided practical guidance on the Toyota Production System to various other industries, including food, confectionery, and medical sectors. Focused on improving machine productivity, enhancing bottleneck machine capabilities, reducing the cost of conveyor production, constructing cell production systems (individual, patrol, division of labor, and segmentation methods), establishing trolley-pulled production methods, creating a 5S workplace culture, and practicing quality and equipment management.
Consultants from major companies
with experience in over 40 countries will respond.
Please feel free to contact us.
If you are in a hurry, please call us.
(Japan time)
Except for Saturday, Sunday, holidays, Year-End and New-Year holidays
3 reasons why we are chosen REASON
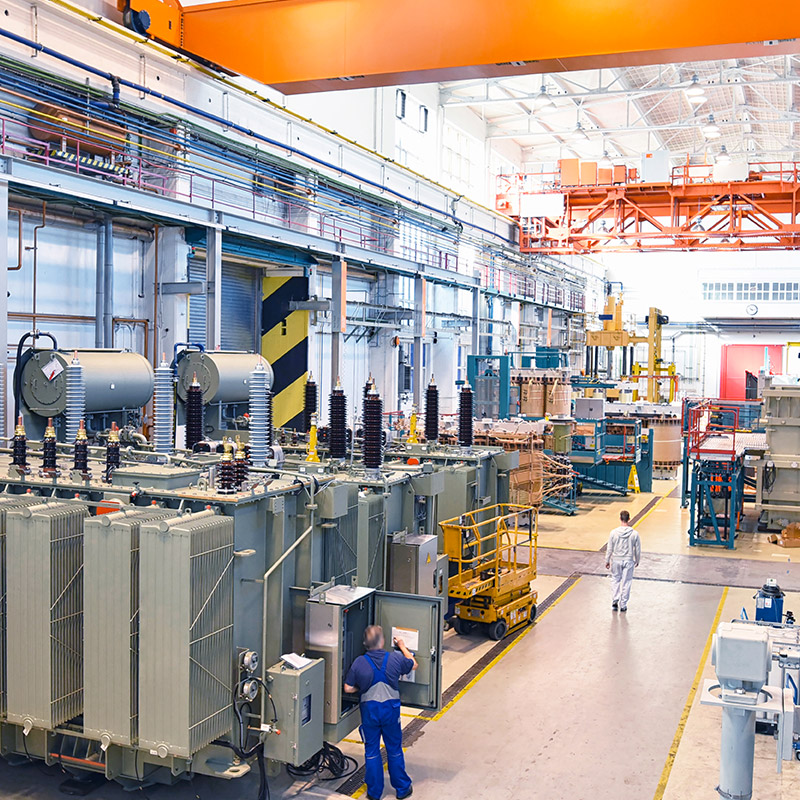
REASON 1
Improvement experience of
more than 1,500 companies in 40 countries
There must be the shop floor issues that cannot be solved by your own company alone. Improvements and reforms for manufacturing industry to survive, regardless of country or industry, need development of your human resources through practical experiences of improvement, and strengthening of your production system base.
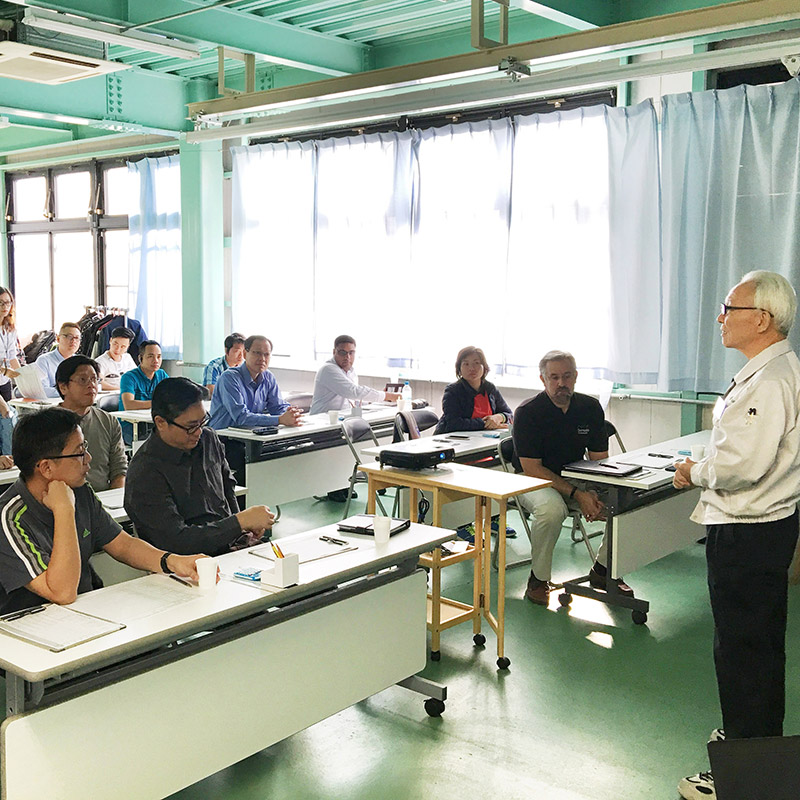
REASON 2
Consulting that shop floor workers
acknowledge our superiority and be pleased
In conventional consulting styles, there was a distance between consultant and the shop floor because it was promoted mainly consultant and management executives. Our consultant can provide a guidance without a distance between consultant and the shop floor through the guidance based on the “seeds of improvement” in a concrete way, instead of “finding fault” like a critic.
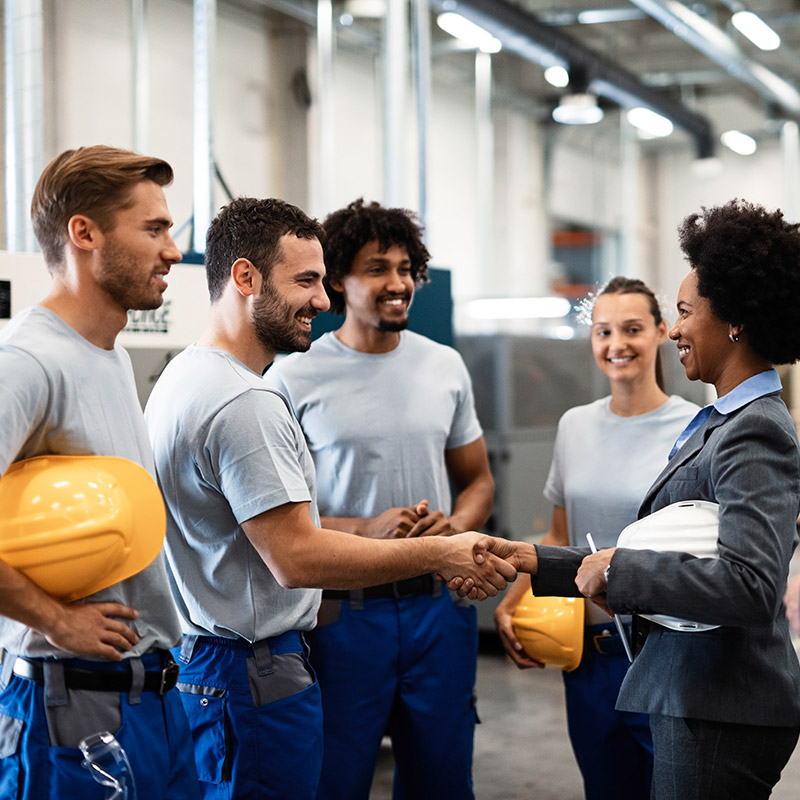
REASON 3
Continuous improvement will continue
even after the end of guidance
While strengthening “human resource development”, we focus on the “overall flow” from design to purchasing, manufacturing, logistics, and production control, and provide guidance that matches the actual situation of your company. Continuous improvement will continue even after the end of guidance through the guidance that is acceptable to the shop floor workers.