改善で重要なのは、
技術でも経験でもなく、作業を熟知しているかどうか
結果
作業スペース 60% 縮小
生産性 140% UP
シンガポールのA社で実施した、食品工場の「集中改善」の改善事例を紹介します。
改善前の悩み
集中改善の目標
1週間で改善を成功させ、現場リーダーが自信をもって、自分で改善できるようになる
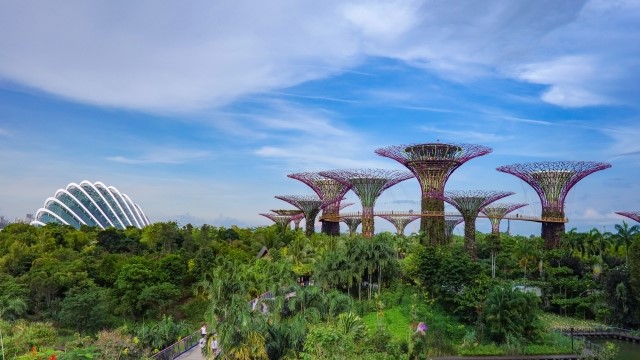
- 業界詳細
- 数店舗展開する食品メーカー
- 国
- シンガポール
- 企業規模
- 従業員 約500名
- 課題
- 生産性向上
- 目的
- 収益改善
- 業界
- 食品
集中改善スケジュール
1日目 AM:講義 PM:講義、現状分析2日目 AM:改善案摘出 PM:改善案検討・決定
3日目 改善実施
4日目 改善実施
5日目 AM:効果確認 PM:まとめ、発表会
改善の苦手意識を取り除け!「動作のムダ取り」からスタート
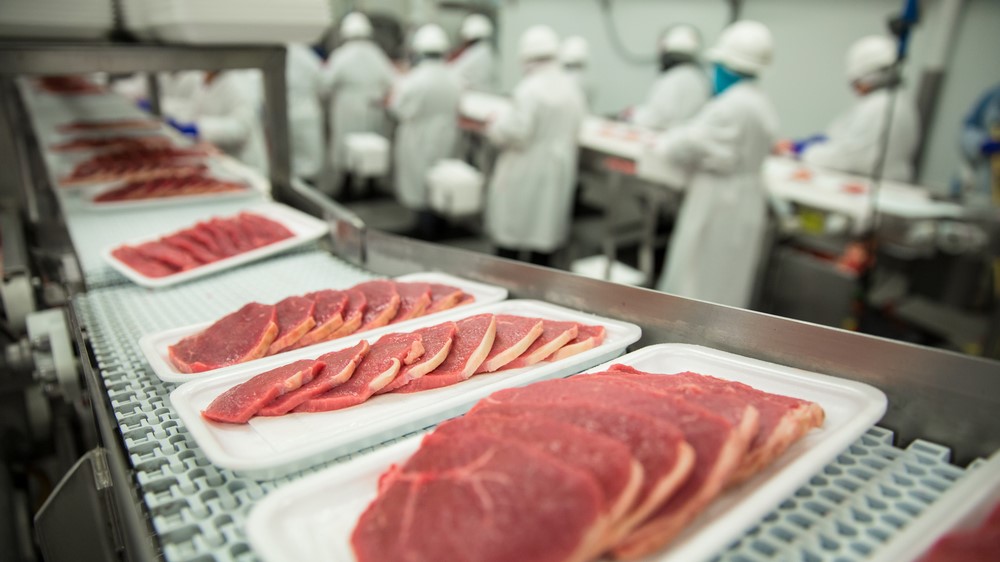
会社から30%の原価低減を命じられた現場リーダー等は、何からすればよいのかわからず、数字を意識しすぎて改善に苦手意識があった。
改善は、「現場に行って実際に目で視て判断する」が基本である。
そして、「目で視て判断する=ムダを発見する」のに必要なのは、技術でも経験でもなく、作業を熟知しているかどうかである。
リーダー等の苦手意識を取り除くために、特別なことをするのではなく、易しいムダ取り技法ですぐに改善結果を出すことにし、動作のムダ取りからスタートする。
また、ムダを発見しやすくするために1個流し生産へ切り替える。
講義:動作は「付加価値動作」「付随動作」「ムダな動作」の3分類
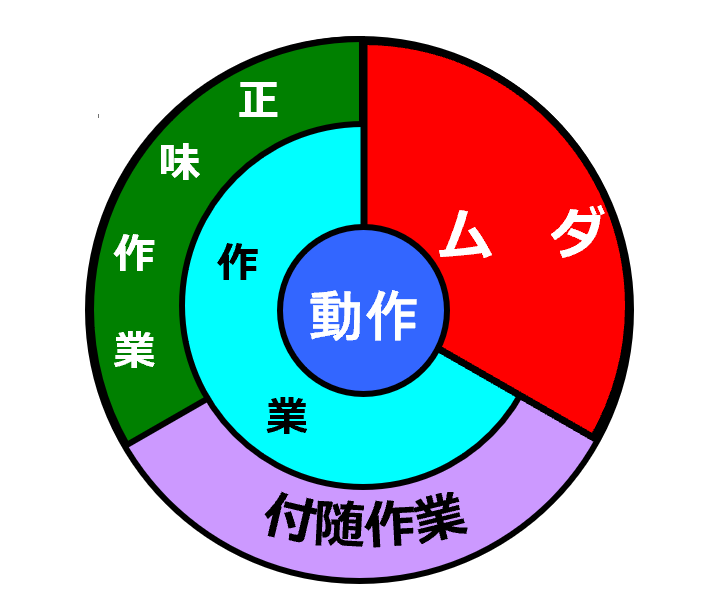
手作業で商品を詰め合わせし、包装機でパッキングする工程を今回の集中改善の最初のターゲットとした。
現場で作業動作を計測し、付加価値動作、付随動作、ムダな動作の3分類にわける。ムダな動作は削除し、付加価値動作・付随動作は、作業域の見直しと、動作経済の原則に沿った動きに改善する。
付加価値動作(正味作業) | 付加価値をつけてくれる動作 |
付随動作 | 付加価値動作を成立させるための必要最低限の動作 |
ムダな動作(非正味作業) | 付加価値のない、作業の目的に関係ない動作 |
・手待ち
・空手歩行
・不良品の手直し
講義:1個流し生産の真の目的 問題を顕在化し改善する
1個流し生産を行うと、今まで気付かなかった問題がわかるようになる。
問題を顕在化させるために行っているのだが、1個流し生産にすることで、手待ちが目立つようになり、真面目な従業員ほど不安を覚える。
よって、顕在化した問題を改善することで生産性が向上することを、みなが理解することと、物理的に1個しか置けないしくみをつくることが重要である。
講義:段取り替え作業の時間短縮
段取り替えをいかに短縮するかという点は、生産効率に直結する。A社は500種類以上の製品を扱い多品種少量生産であるため、段取り替え作業の時間は、研究を重ねるべき課題である。
<段取り替え作業の基本的な改善手法>
1. 内段取り、外段取り、ムダの3つに分類
2. 「ムダの削減」と「内段取りの外段取り化」
3. 内段取り、外段取りにおけるムダな動作の削除
改善実施:レイアウトを再形成
1個流し生産への切り替え、ムダな動作を徹底的に排除することを意識しラインレイアウトを再形成すると、工程人数は10人から6人に、作業スペースは60%縮小した。
<改善内容>
・1個流し生産へ
・仕掛品置き場を1個しか置けないようにする
・工程間の運搬作業をシュートに変更することでなくす
・ラインバランシング
「動作のムダ取り」改善は、改善範囲が狭いので比較的簡単に改善を行うことができるが、作業者の負担は軽減し、改善効果も出しやすく現場の改善ムードは高まるため、改善入門として良い手法の一つである。
「集中改善」とは
「集中改善」では、コンサルタントが貴社の改善メンバーと、1週間集中して改善に従事することで、短期間で改善効果を絞り出し、改善活動を引っ張っていく人材育成を目的としています。
集中改善詳細
集中改善のスペシャリスト

伊藤 彰洋(いとう あきひろ)
現場改善コンサルタント
現場改善コンサルタントとして第一線で活躍中。国内外12か国以上、大中多種多様な現場の改善を実施し、都度、現場の問題を解決してきた。
生産管理システムを手掛けた経験により、営業~資材~生産管理~製造~外注と工場内のあらゆるプロセスにおいて改善活動を実践する。また、現場の人間と共に改善活動を行い、現場改善の文化を企業に根付かせ、品質向上・生産性向上・リードタイム短縮を実現する。
選ばれる3つの理由 REASON
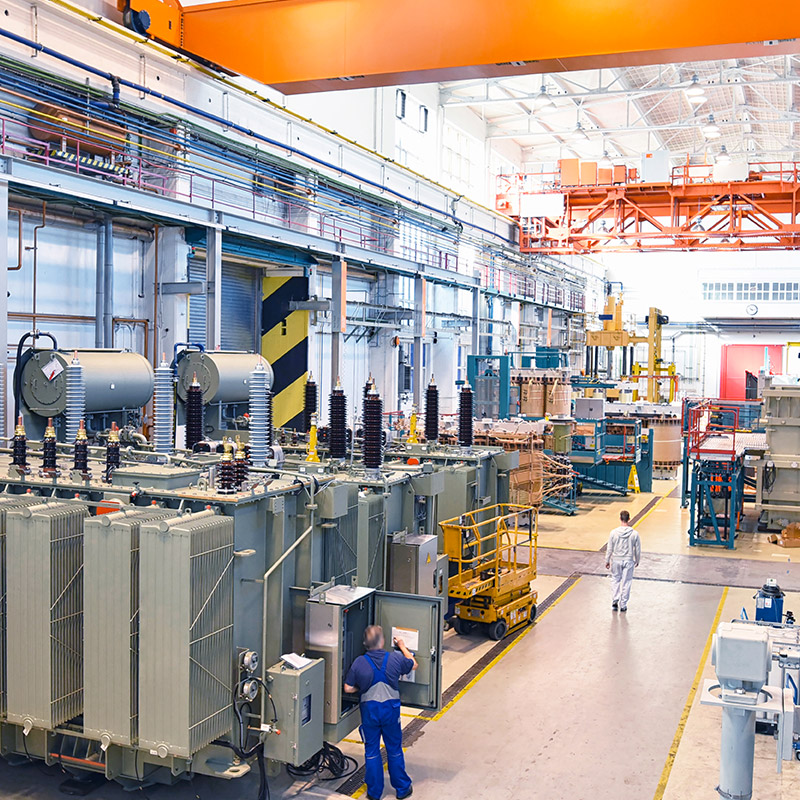
REASON 1
40ヶ国、
1,500社以上の改善実績
自社だけでは解決できない現場の問題は必ずあります。製造業が勝ち残るための改善・改革は、国や業界を問わず、改善の実践体験を通じて、人材を育成し、生産体制基盤を強化することが必要です。
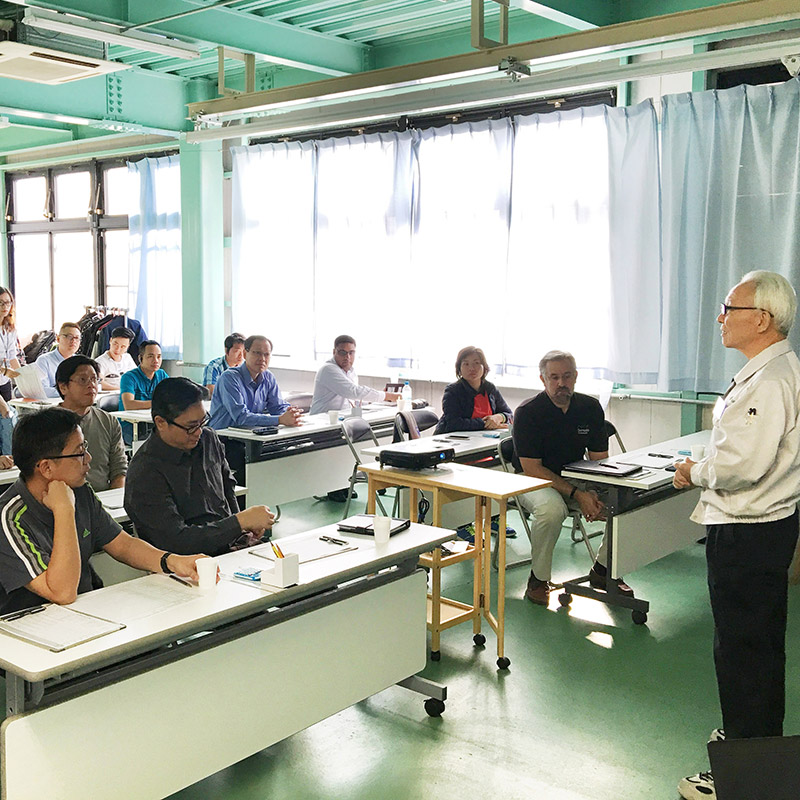
REASON 2
現場が一目置き、
喜ぶコンサルティング
従来のコンサルティングでは、経営層とコンサルタントが中心になってすすめるため、現場とコンサルタントの間に距離がありました。弊社コンサルタントは、評論家的な「あら探し」ではなく「改善の種」を具体的に見出す指導により、現場の人間との隔たりのない指導をすることができます。
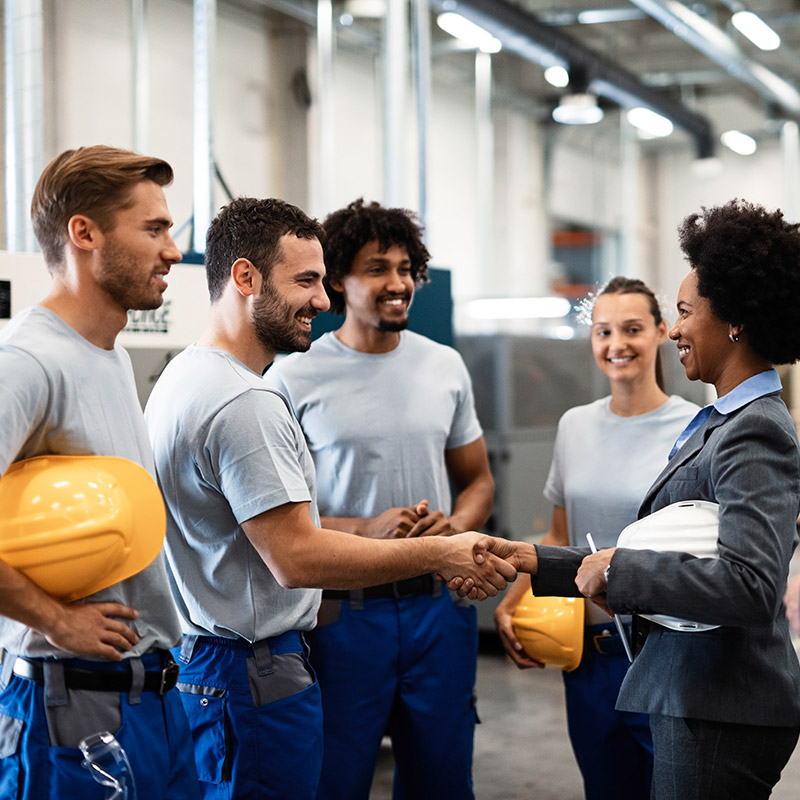
REASON 3
指導終了後も
継続的改善がされる
「人づくり」を強化しながら、設計から調達・製造・物流、そして生産管理と「全体の流れ」を重視し、貴社の現場の実態に合った指導を実施。現場が納得できるコンサルティング指導を行うことで、指導終了後も改善文化が継続されます。