プロによる工場診断で
どこをどう改善すればよいか一目瞭然
結果
- 自分たちでは見えなかった、気づかなかった課題が明確に。
- 現場改善の対策と社員の意識向上を融合した改善案
某自動車部品メーカーから工場を診断して欲しいと依頼があり「簡易工場診断」を実施し下記のようなレポートを差し上げました。
時間が少ないので基本的に問題提起のみですが今後コンサルティングに入る事が決まれば具体的な改善プランを作成していきます。
1. 診断報告
1-1. 5S
1-2. 安全作業 (Safety)
1-3. 品質確保 (Quality)
1-4. コスト低減 (Cost)
1-5. 納期遵守 (Delivery)
1-6. モノづくり
2.今後の課題と対策
2-1. 人
2-2. ライン・治具
2-3. 材料・部品
2-4. 作業方法
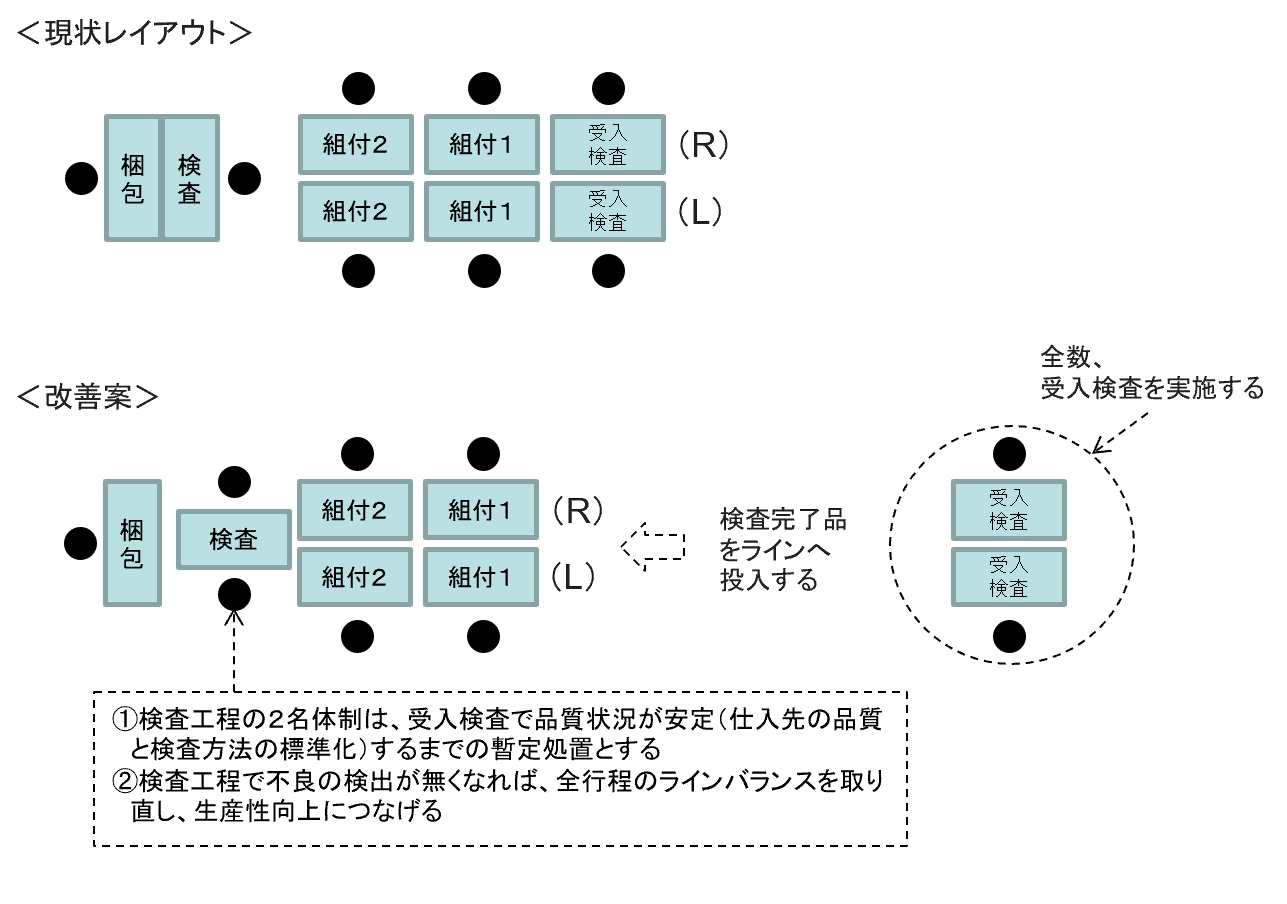
- 業界詳細
- 自動車部品
- 国
- 日本
- 企業規模
- 従業員 約530名
- 課題
-
生産性向上
人材育成 - 目的
- 人材育成収益改善
- 業界
- 自動車
1-1. 診断報告(5S)
No. | 分類 | 内容 |
1 | 整理整頓 |
|
2 | 清掃清潔 |
|
3 | しつけ |
|
1-2. 診断報告(安全作業)
No. | 分類 | 内容 |
1 | 安全作業 |
|
1-3. 診断報告(品質確保)
No. | 分類 | 内容 |
1 | 不良に対する意識 |
|
2 | 不良対策の実態が見えない |
|
3 | 顧客への流出防止を総力で取り組んでいるとは言えない |
|
4 | 作業者の早期の習熟や出来栄えのバラツキの対策は管理・監督者の仕事 |
|
5 | 生産現場に管理・監督者の不在は、職場の現実を知ることはできない |
|
6 | 検査と選別を混同 |
|
7 | 検査、品証部門と生産現場の連携がない |
|
1-4. 診断報告(コスト低減)
No. | 分類 | 内容 |
1 | コスト意識 |
|
2 | ムダの放置 |
|
1-5. 診断報告(納期遵守)
No. | 分類 | 内容 |
1 | 納期遵守 |
|
1-6. 診断報告(モノづくり)
No. | 分類 | 内容 |
1 | 1セット流し |
|
2 | IEの技術 |
|
2-1. 今後の課題と対策(人)
No. | 分類 | 課題 | 対策 |
1 | 職務分掌 | 従業員の役割分担が不明確 |
|
2 | 現場の監督者(組長・工程管理) | 生産現場に常駐する監督者が不在である |
|
3 | ライン長 | 生産現場に常駐するライン長が不在である |
|
4 | 現場作業者 | 作業に対する適正テストが未実施 |
|
2-2. 今後の課題と対策(ライン・治具)
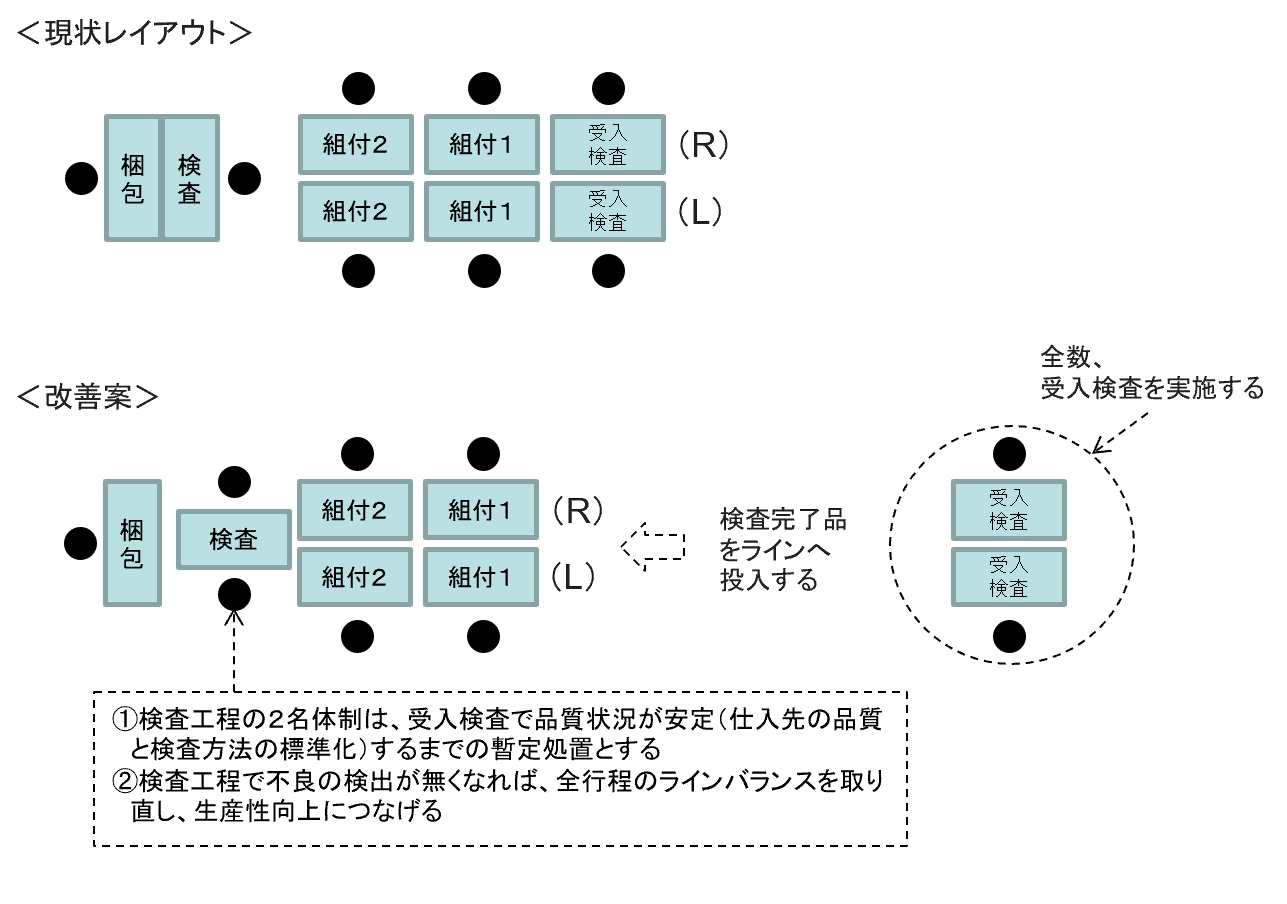
2-3. 今後の課題と対策(材料・部品)
No. | 分類 | 課題 | 対策 |
1 | 品質不良が多い | 受入検査時に仕入先より不良品が納入される |
|
2 | 塗装のエア吹き | エア吹きの隣で脱脂しているのでゴミが飛んでいく |
|
3 | 材料仕入れ量のコントロール | 仕入先での生産計画や品質状況により、フロント(左、右)、リア(左、右)の4材料の納入量が均一化されていないので、4材料の在庫量が揃わない場合がある |
|
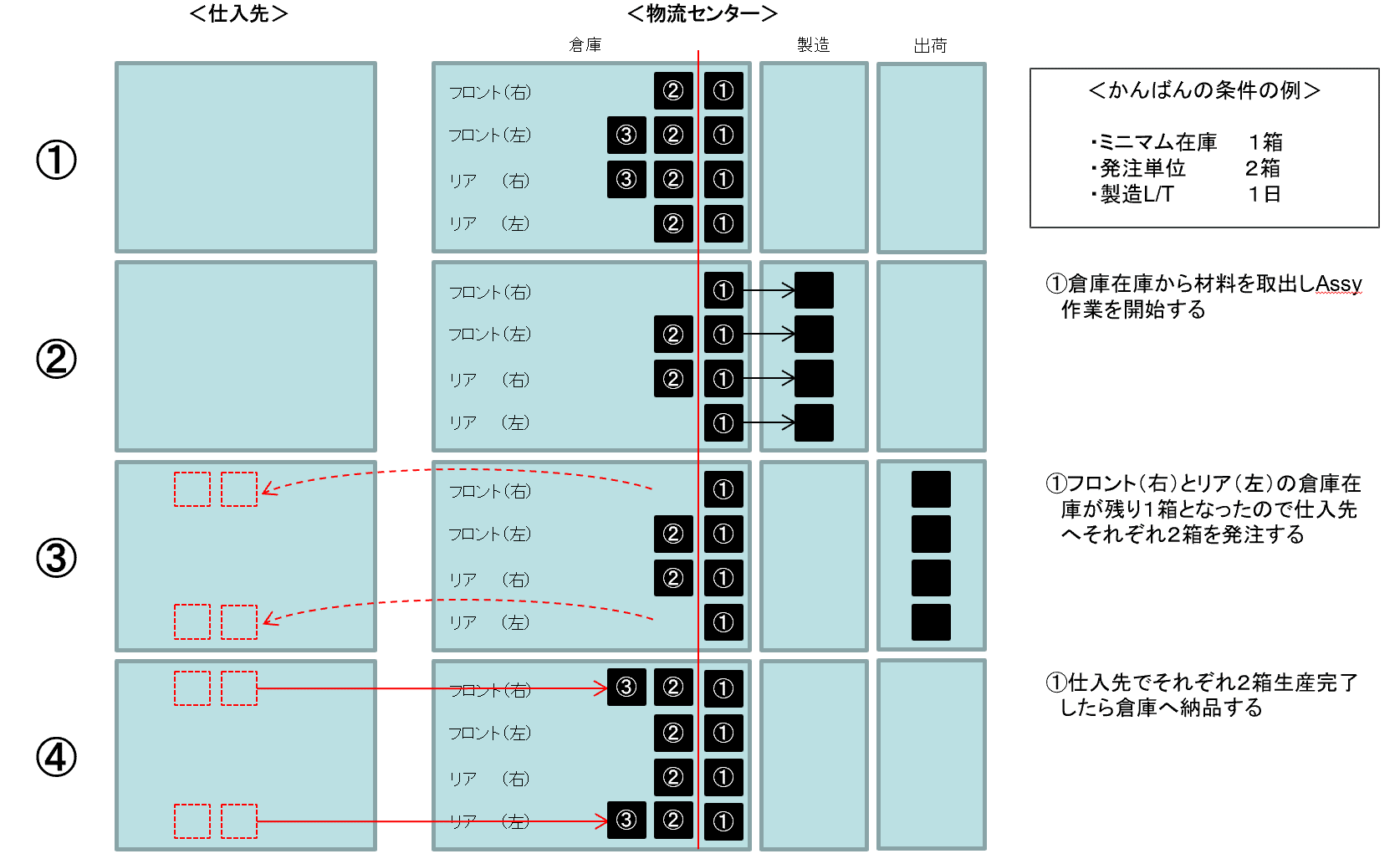
2-4. 今後の課題と対策(作業方法)
No. | 分類 | 課題 | 対策 |
1 | 照度管理 | 工程により、光の照度と方向にバラツキがある | 光の環境を統一する
|
2 | 手待ち | 作業者は、材料不良があるとサイクルタイムがぶれるので、リズムに乗った作業が出来なくなる。 このことは、作業者の集中力低下にもつながり、品質の確保がしにくくなる。 |
|
3 | 不良発見時 | 不良発見時に、ルールが統一されておらず作業者任せになっている部分がある |
|
4 | 指差し呼称 | 作業終了時に自己チェックが実施されていない |
|
5 | 標準作業の徹底 | 作業者によって作業手順が異なっている |
|
現場改善のスペシャリスト

伊藤 彰洋(いとう あきひろ)
現場改善コンサルタント
業種を問わず、現場改善の文化を企業へ根付かせ、現場の人間と共に改善活動をおこない、品質向上・生産性向上・リードタイム短縮を実現する。 また、生産管理システムを手掛けた経験により、「営業~資材~生産管理~製造~外注」と工場内のあらゆるプロセスにおいて改善活動を実践する。
選ばれる3つの理由 REASON
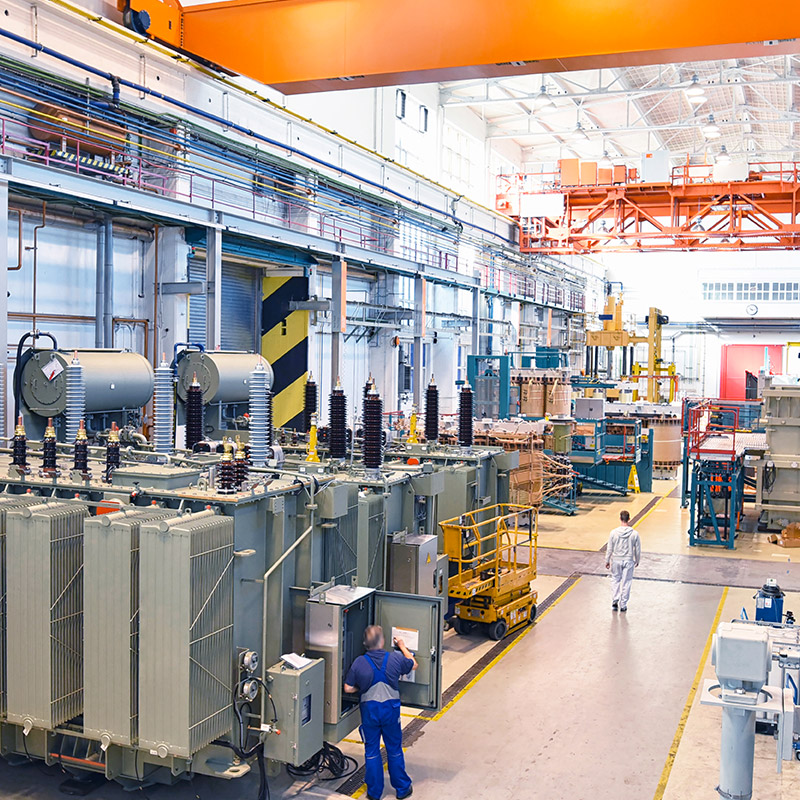
REASON 1
40ヶ国、
1,500社以上の改善実績
自社だけでは解決できない現場の問題は必ずあります。製造業が勝ち残るための改善・改革は、国や業界を問わず、改善の実践体験を通じて、人材を育成し、生産体制基盤を強化することが必要です。
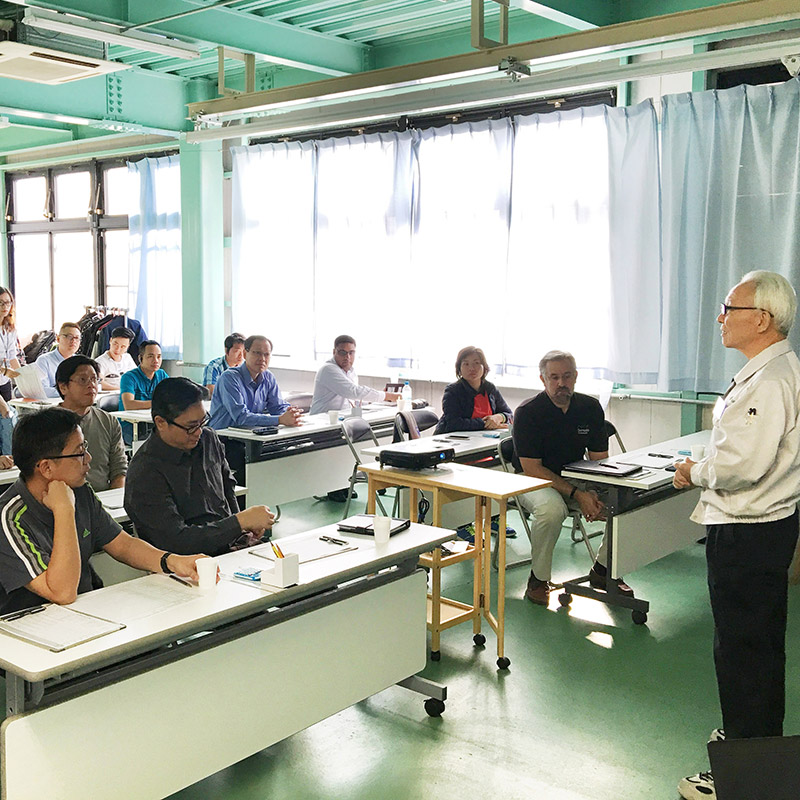
REASON 2
現場が一目置き、
喜ぶコンサルティング
従来のコンサルティングでは、経営層とコンサルタントが中心になってすすめるため、現場とコンサルタントの間に距離がありました。弊社コンサルタントは、評論家的な「あら探し」ではなく「改善の種」を具体的に見出す指導により、現場の人間との隔たりのない指導をすることができます。
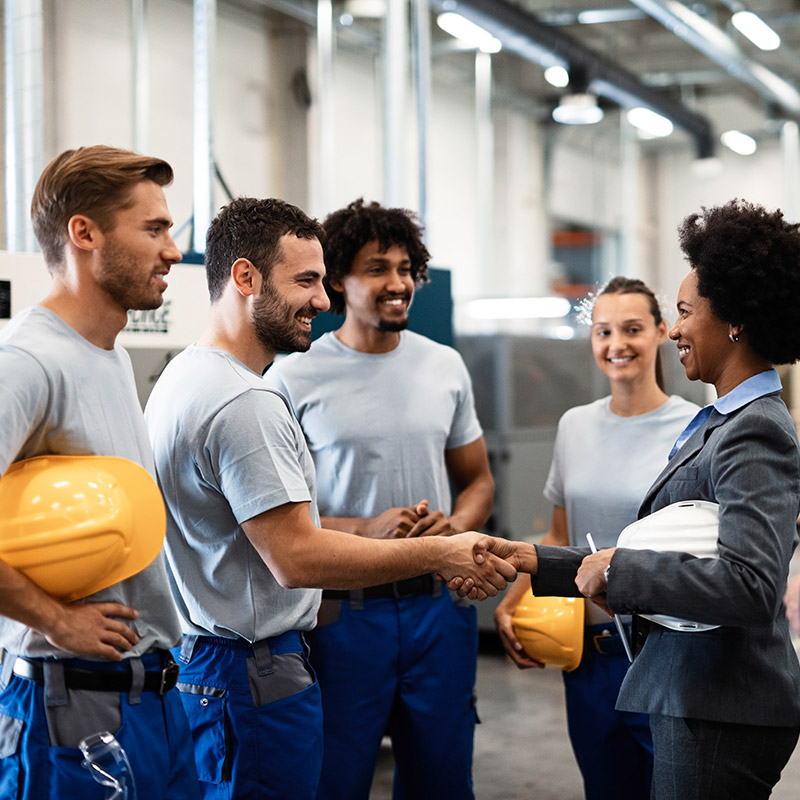
REASON 3
指導終了後も
継続的改善がされる
「人づくり」を強化しながら、設計から調達・製造・物流、そして生産管理と「全体の流れ」を重視し、貴社の現場の実態に合った指導を実施。現場が納得できるコンサルティング指導を行うことで、指導終了後も改善文化が継続されます。