TPS Dojo June 2023 – In Italy
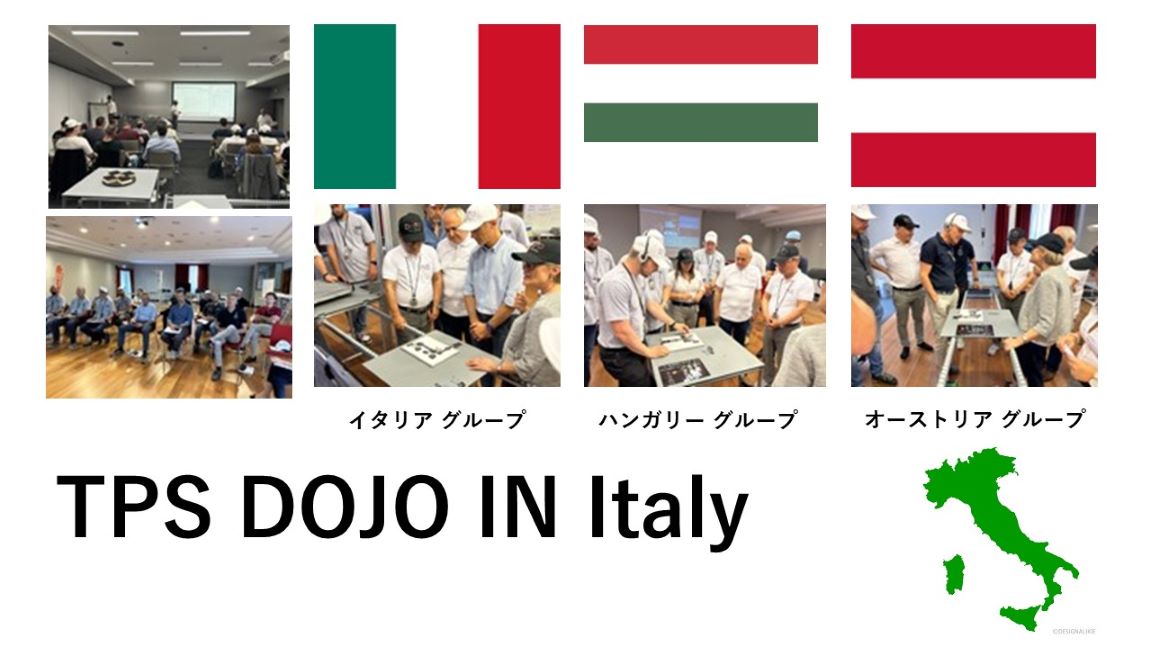
In June 2023, with the cooperation of a local partner company, we held a TPS Implementation Dojo in Italy.
Date: June 2023, held in three locations
Content: TPS Implementation Dojo 1DAY (practical training using equipment and lectures)
Location: The first and second sessions were held in rented venues, and the third session was conducted at a steel plate company
Number of Participants: 62 in total (over three sessions)
At the TPS Implementation Dojo, participants learn about the general philosophy of manufacturing as practiced by Toyota, through both lectures and hands-on training.
In the improvement proposals, layouts and unique ideas were presented that one might not typically consider in Japan, highlighting the differences in manufacturing cultures in a positive way.
It’s possible that participants might imagine their own manufacturing processes and realize there might be more efficient methods available. However, by demonstrating various examples of improvements on-site, it is believed that a deeper understanding of TPS was achieved.
~Improvement Mindset at an Italian Steel Plate Company~
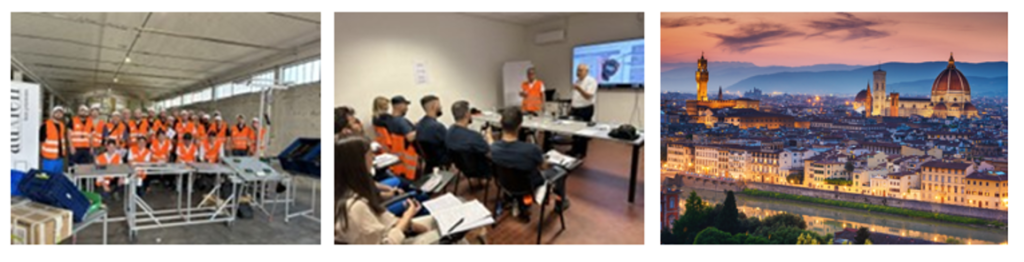
During the session held at the steel plate company, it began with the company’s top executive expressing a strong desire to “seriously pursue improvement” to the employees, ensuring that the intent was understood before starting.
~ Tri-lingual Simultaneous Interpretation~
At the second venue, participants from Italy, Austria, and Hungary were in attendance, and the TPS Dojo was conducted with tri-lingual simultaneous interpretation.
Regarding the translation of materials, there were instances where the translation seemed to indicate a misunderstanding of TPS, prompting requests for corrections.
For example, in the documentation explaining “work sequences,” the translated version altered the diagram in such a way that it appeared as if steps in the process were skipped.
It was emphasized that in standard operations, it is crucial to perform tasks in a waste-free and efficient order. After explaining this, understanding was reached, and the materials were replaced with corrected versions.