Case Study 1
Optical Instruments Manufacturer Company A
Results
- Semi-annual targets achievement
- Practice of PDCA Cycle properly implemented and
- Formation of personnel with Waste finding and elimination
- High Capacity to adapt to new models orders
Company A, optical instrument manufacturer, were doing contract manufacturing. Since the main lines of its client have been shifted to overseas, production for domestic market declined more than half. Aiming to recover its contract manufacturing business, Company A used Hirayama Consulting Services.
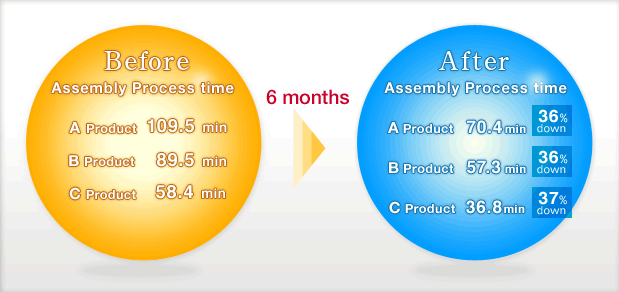
- Industry details
- optical instrument manufacturer
- Country
- Japan
- Purpose
- Quality improvementCost reductionProfitability improvement
- Industry
- Others
issues

Analysis
Implementation
Why did you choose Hirayama Consulting?
The availability of implement the Toyota Production System while nurturing internal personnel capable of keep continuous improvement was the main reason..
- Toyota Production System Basis
- Practical improvement rather than lectures
- Nurturing personnel able to give continuity to Improvement Policies as a primary objective
Case Study 2
Automobile Parts Manufacturer Company B
Effects
Reducing Cost through Operation availability Improvement Project.
- Industry details
- Automobile Parts
- Country
- Japan
- Purpose
- Quality improvementCost reductionProfitability improvement
- Industry
- Others
Analysis

Implementation
Why did you choose Hirayama Consulting?
Have gained a thorough understanding of our worksite and a perfect match of Hirayama with our Improvement activities were the main reason.
- Customer Perspective
- Production based on Standardization
- Pursuit of Plant total optimization
- All process visualization management system structure
- Personnel training through Improvement activities
Genba Kaizen Specialist

ITO, Akihiro
Process improvement consultant
He worked for JIT Institute, Tokyo for 20 years.( JIT: Just In Time). During this period, he has learned Just In Time philosophy and method of improvement of productivity in manufacturing plant. Continuously he has been engaged in effective introduction process of Production Management System to small and medium enterprise and even big enterprise.
Consultants from major companies
with experience in over 40 countries will respond.
Please feel free to contact us.
If you are in a hurry, please call us.
(Japan time)
Except for Saturday, Sunday, holidays, Year-End and New-Year holidays
3 reasons why we are chosen REASON
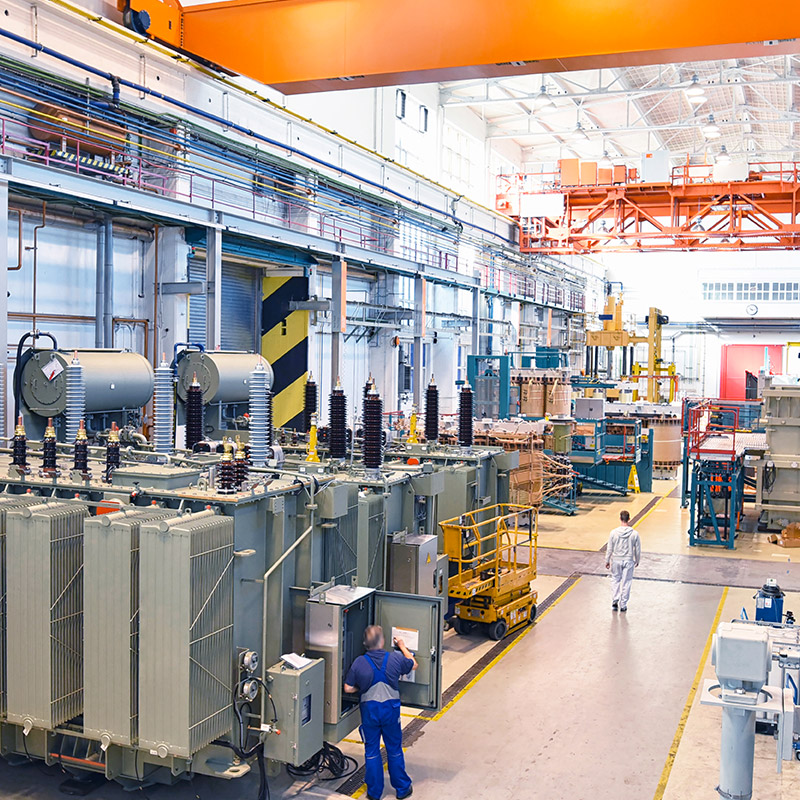
REASON 1
Improvement experience of
more than 1,500 companies in 40 countries
There must be the shop floor issues that cannot be solved by your own company alone. Improvements and reforms for manufacturing industry to survive, regardless of country or industry, need development of your human resources through practical experiences of improvement, and strengthening of your production system base.
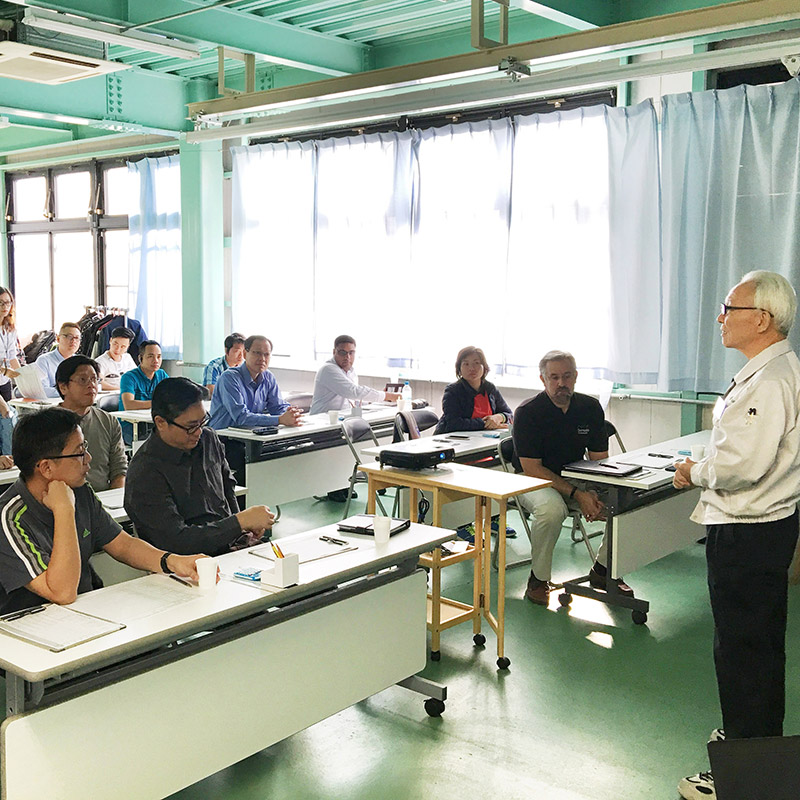
REASON 2
Consulting that shop floor workers
acknowledge our superiority and be pleased
In conventional consulting styles, there was a distance between consultant and the shop floor because it was promoted mainly consultant and management executives. Our consultant can provide a guidance without a distance between consultant and the shop floor through the guidance based on the “seeds of improvement” in a concrete way, instead of “finding fault” like a critic.
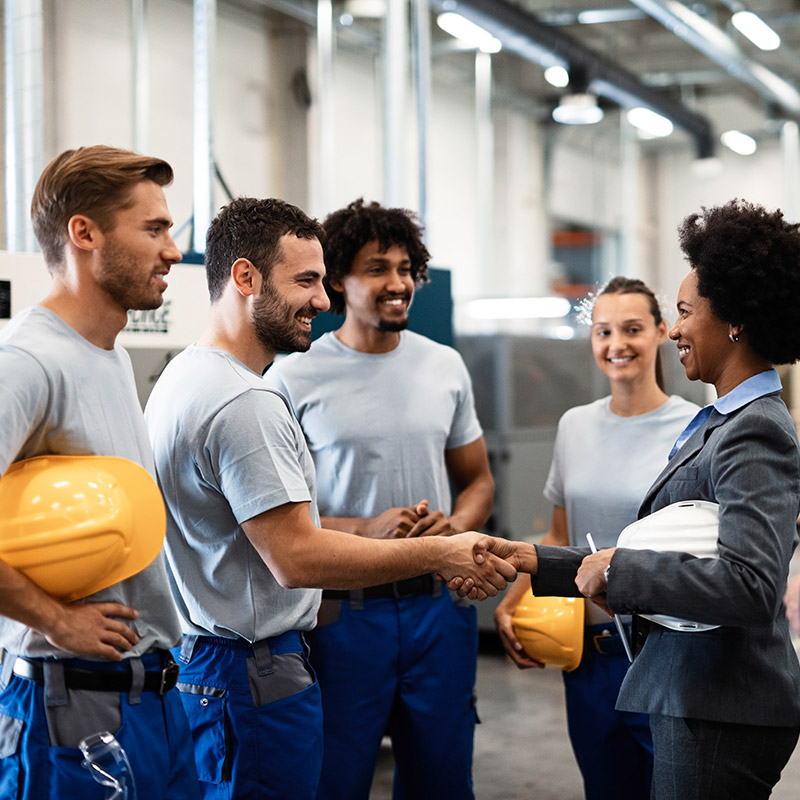
REASON 3
Continuous improvement will continue
even after the end of guidance
While strengthening “human resource development”, we focus on the “overall flow” from design to purchasing, manufacturing, logistics, and production control, and provide guidance that matches the actual situation of your company. Continuous improvement will continue even after the end of guidance through the guidance that is acceptable to the shop floor workers.
Consultants from major companies
with experience in over 40 countries will respond.
Please feel free to contact us.
If you are in a hurry, please call us.
(Japan time)
Except for Saturday, Sunday, holidays, Year-End and New-Year holidays