Initially met with strong resistance,
but transformed into a passionate improvement advocate!
Result
・Work Improvement: Reduction of 48 to 120 minutes per day
Background to the improvement
When we received a consultation from Company A about on-site improvements, their first concern was, “Can improvements be made even if our staff doesn’t have special educational backgrounds or experience?”
Educational background or experience is completely irrelevant when it comes to improvement. What matters most are the “Four Key Attitudes,” I explained.
First, we draw out the initial curiosity and interest in improvement, known as “Sono-Ki” (willingness). Then, we nurture “Yaru-Ki” (motivation), followed by “Hon-Ki” (seriousness), and finally, “Gen-Ki” (enthusiasm).
These “Four Key Attitudes” are integrated into the workplace through workshop seminars and collaboration with management, such as implementing incentive systems.
“Gen-Ki” refers to making the improvement process enjoyable.
In our workshop seminars, we focus on familiar items found in the workplace, like toolboxes and parts shelves, to create an engaging and enjoyable experience.
At Company A, approximately 10 months after starting their improvement initiatives, the results have been remarkable. Some teams are now proposing as many as 50 improvement ideas in a single month, and there are even individuals creating workbenches at home to enhance their processes.
As with any job, the most important factor is the mindset.
Just like at Company A, even if there are initial concerns and dissatisfaction, creating an environment where employees can actively and enjoyably propose improvements on their own is the responsibility of both consultants and management.
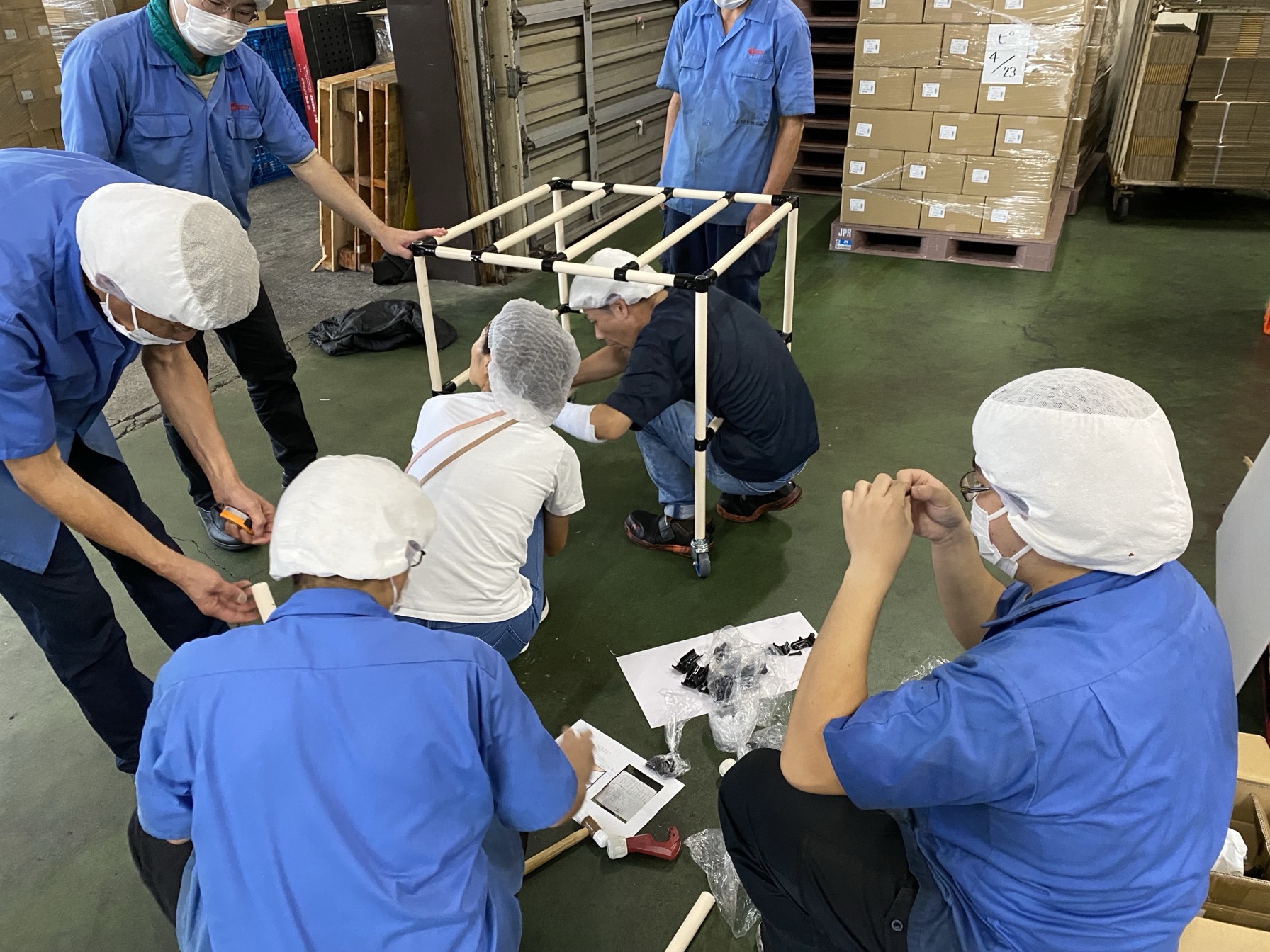
- Industry details
- Mainly processing and manufacturing bean sweets
- Country
- Japan
- Company size
- 100 employees or less
- Assignment
- Change your company! !
- Purpose
- コスト削減人材育成
- Industry
- 食品
Karakuri Cardboard Cart
Workbench with dispenser
Site improvement specialist
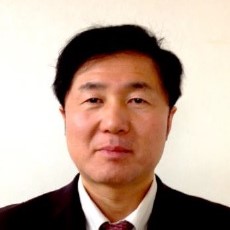
Koichi Kakizawa
Former Ricoh Employee – Quality Assurance & Manufacturing Technology Departments
During his tenure at Ricoh, he established the Ricoh Production System based on the Toyota Production System (TPS). Afterward, he extended his expertise to various industries, including food, confectionery, and medical sectors, where he guided the implementation of TPS principles.
Consultants from major companies
with experience in over 40 countries will respond.
Please feel free to contact us.
If you are in a hurry, please call us.
(Japan time)
Except for Saturday, Sunday, holidays, Year-End and New-Year holidays
3 reasons why we are chosen REASON
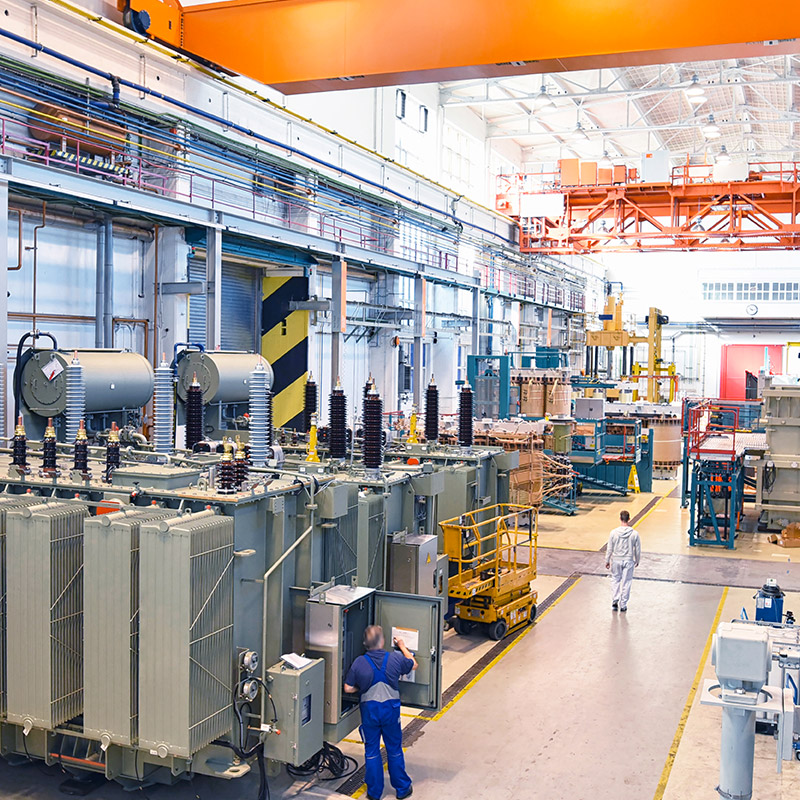
REASON 1
Improvement experience of
more than 1,500 companies in 40 countries
There must be the shop floor issues that cannot be solved by your own company alone. Improvements and reforms for manufacturing industry to survive, regardless of country or industry, need development of your human resources through practical experiences of improvement, and strengthening of your production system base.
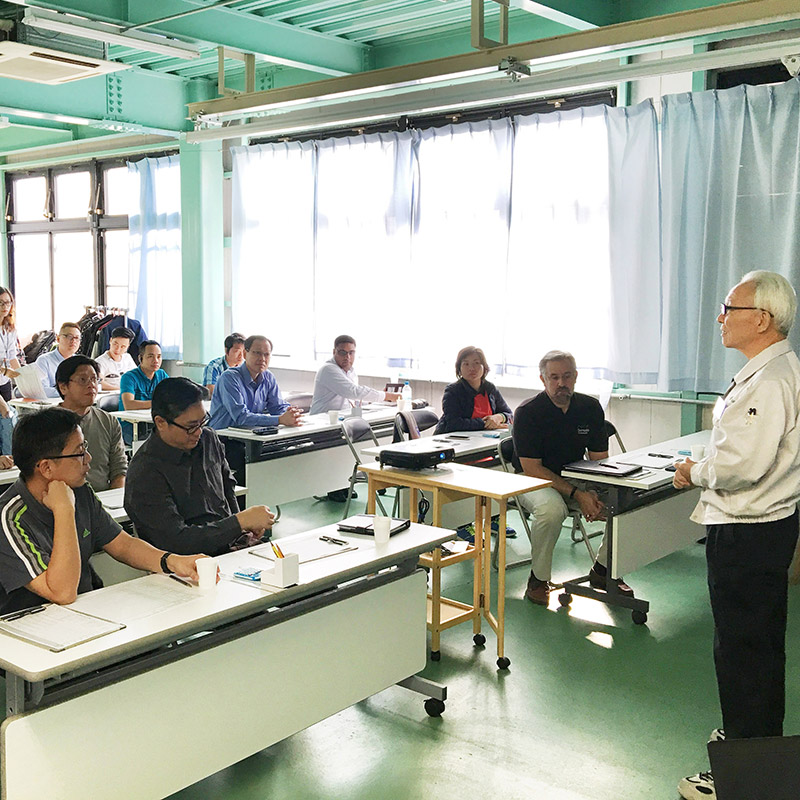
REASON 2
Consulting that shop floor workers
acknowledge our superiority and be pleased
In conventional consulting styles, there was a distance between consultant and the shop floor because it was promoted mainly consultant and management executives. Our consultant can provide a guidance without a distance between consultant and the shop floor through the guidance based on the “seeds of improvement” in a concrete way, instead of “finding fault” like a critic.
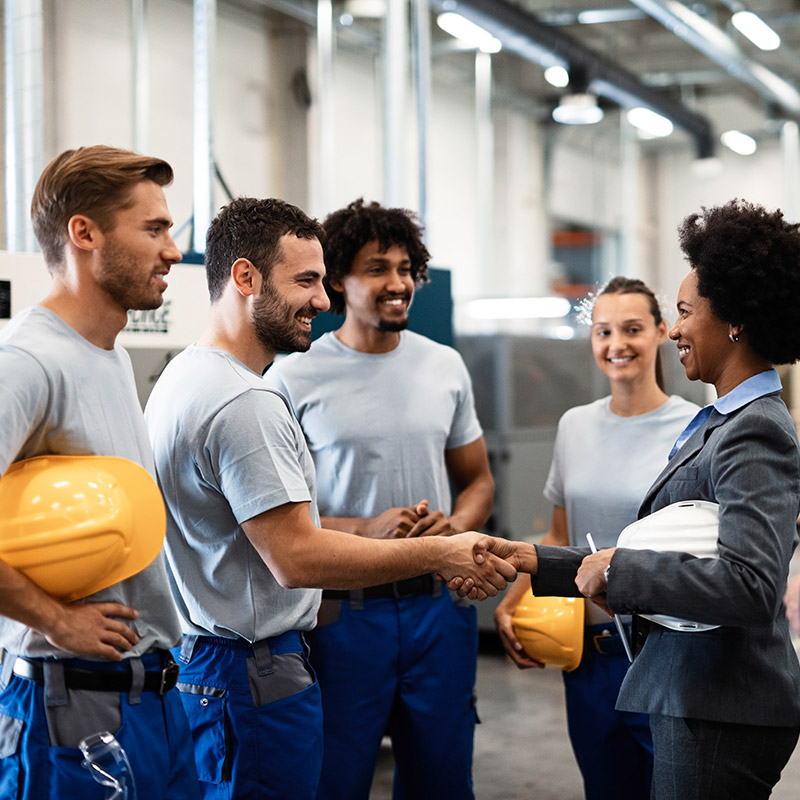
REASON 3
Continuous improvement will continue
even after the end of guidance
While strengthening “human resource development”, we focus on the “overall flow” from design to purchasing, manufacturing, logistics, and production control, and provide guidance that matches the actual situation of your company. Continuous improvement will continue even after the end of guidance through the guidance that is acceptable to the shop floor workers.