For over 20 years, I have been working as a coordinator for on-site improvements at Japanese sites overseas.
Today, I would like to talk about TPS or improvement education abroad.
A distinctive feature of Hirayama Consulting is that our consultants actually visit the site and provide direct guidance to workers, managers, or even business owners while observing the operations on-site.
While overseas clients demand systematic improvements, the Japanese approach to improvement might excel more on the mindset aspect. Manager of Consulting Division1. Example of On-site Improvement Guidance in China
The same approach applies overseas. This photo was taken during a TPS improvement education session in China. We conduct a lecture on TPS implementation in the morning and then visit the actual site in the afternoon.
Many factories in China cover large areas, which often results in a significant amount of waste, such as inventory and work-in-progress items, between warehouses and workers.
Lines producing older products tend to have lower productivity, while lines for newer products often have more staff assigned. Therefore, we review the process layout as part of overall improvement efforts.
For this particular company, we provided homework and conducted the improvement over three months.
2. Differences in Improvement Implementation between Overseas and Japan
Overseas, improvements that are visible and tangible, such as machinery and systems, are more easily appreciated, whereas in Japan, the fundamental aspect of improvement is developing people.
This represents a significant difference in sustaining improvement efforts.
Therefore, Hirayama Consulting places great importance on going to the site, observing the actual work with the operators, and engaging workers and managers in thinking processes to facilitate improvement and develop personnel.
(This photo is from a safety management system briefing conducted for South America.)
このコラムを書いた現場改善コーディネーター
Miyuky Honda
In Hirayama Co. he has been coordinating Toyota Production System consulting and training for the last 8 years. Mr. Honda has helped hundreds of foreign Specialists, Executives and Technicians in grasping the essence of TPS. He is also in charge of leading Benchmark Programs for Consulting partners from overseas.
3 reasons why we are chosen REASON
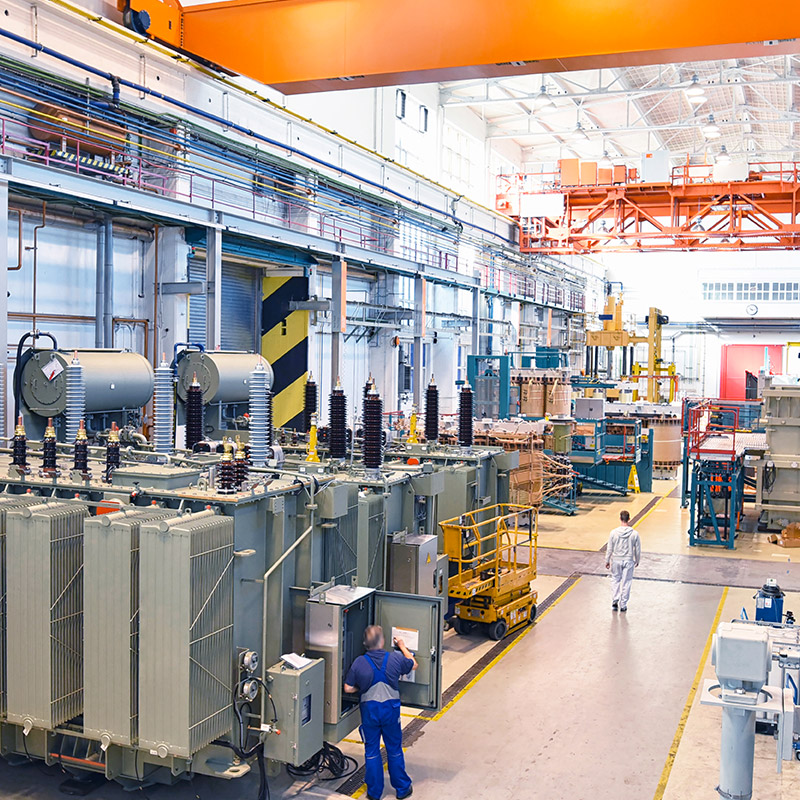
REASON 1
Improvement experience of
more than 1,500 companies in 40 countries
There must be the shop floor issues that cannot be solved by your own company alone. Improvements and reforms for manufacturing industry to survive, regardless of country or industry, need development of your human resources through practical experiences of improvement, and strengthening of your production system base.
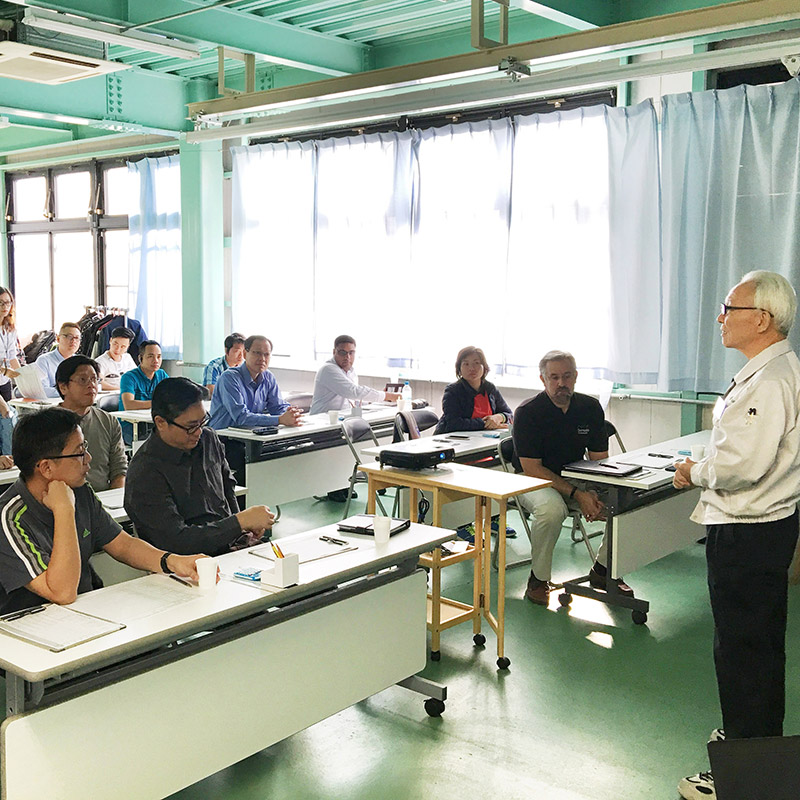
REASON 2
Consulting that shop floor workers
acknowledge our superiority and be pleased
In conventional consulting styles, there was a distance between consultant and the shop floor because it was promoted mainly consultant and management executives. Our consultant can provide a guidance without a distance between consultant and the shop floor through the guidance based on the “seeds of improvement” in a concrete way, instead of “finding fault” like a critic.
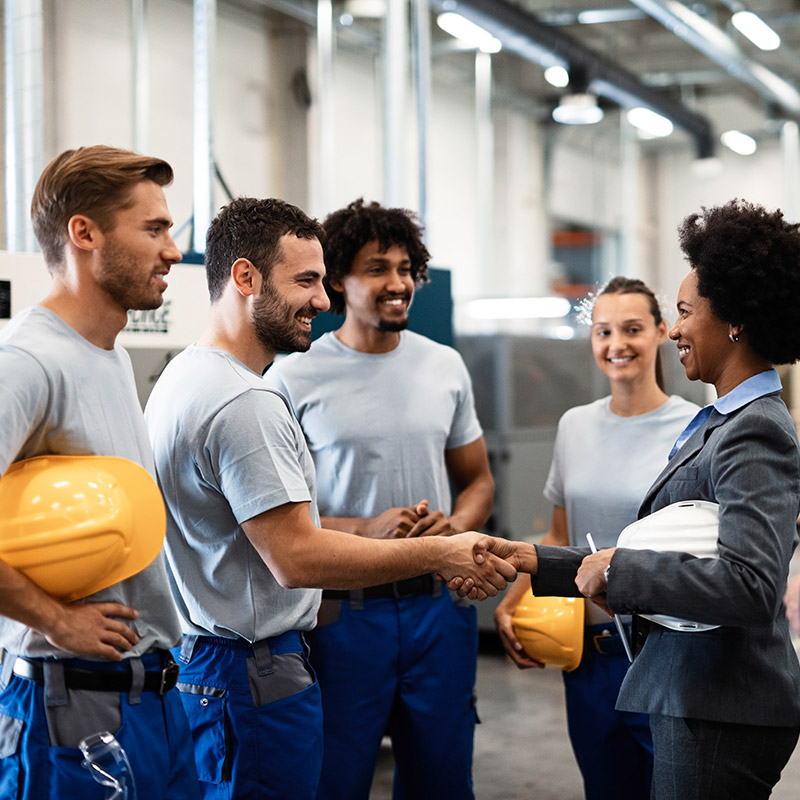
REASON 3
Continuous improvement will continue
even after the end of guidance
While strengthening “human resource development”, we focus on the “overall flow” from design to purchasing, manufacturing, logistics, and production control, and provide guidance that matches the actual situation of your company. Continuous improvement will continue even after the end of guidance through the guidance that is acceptable to the shop floor workers.
Consultants from major companies
with experience in over 40 countries will respond.
Please feel free to contact us.
If you are in a hurry, please call us.
(Japan time)
Except for Saturday, Sunday, holidays, Year-End and New-Year holidays