Solve factory issues
of all industries
ISSUE
Concerns of factory shop floor vary depending on the each environment. We have our wide range of experience and know-how and solve all issues, from quality, productivity, and delivery time issues to production line and flow reviews, measures to increase employee motivation, system improvements and information utilization, and overseas expansion.
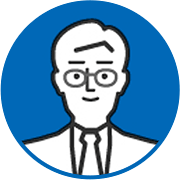
President / Executives
- Poor cooperation between sales department and production department
- Profit does not grow
- Sales does not grow
- Delays in delivery and large material inventory
- Poor organization and no development of human resources
- We would like to start overseas expansion of our factory
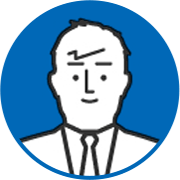
Factory shop floor
- Introduced a new system as per the executive’s instruction, but it does not match the manufacturing system of our shop floor
- We want to reduce the defect rate, but we don’t know the specific method
- Productivity is poor, but we can’t judge what is the problem
- Poor layout, lot production, and bad equipment
What is Hirayama Consulting? ABOUT
Based on TPS (Toyota Production System), we will thoroughly eliminate waste and provide guidance support for creating your own production system in order to realize your management strategy.
When making improvements and reforms, we will build a mechanism that can be effectively developed for continuous improvement according to the actual situation of the shop floor and further leads to human resource development. We will eliminate the distance between consultants and the shop floor, that may occur in conventional consulting styles, and provide consulting that shop floor workers can acknowledge our superiority, trust us, and be pleased.
Recommended for companies
whose direction of improvement is undecided
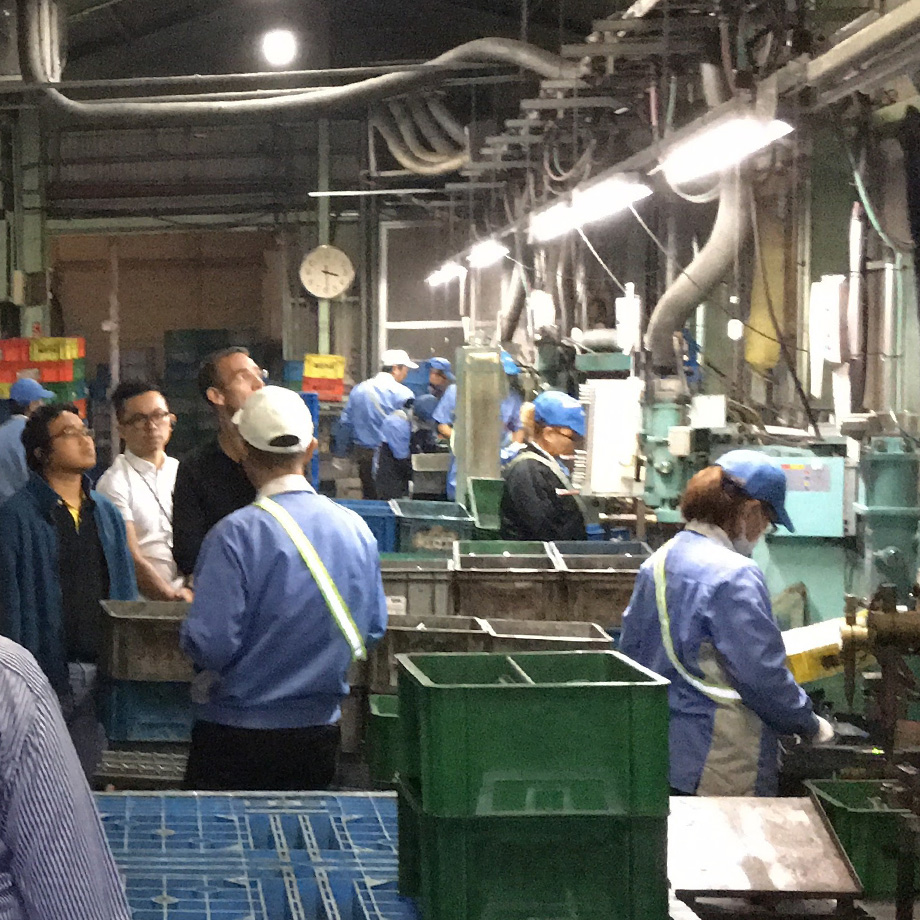
Factory diagnosis
At the shop floor, there are issues that cannot be solved by your own company alone for various reasons.
“Factory diagnosis” is conducted by shop floor improvement consultant to actually visit the factory, find “seeds of improvement” in a concrete way, instead of “finding fault” like a critic, and grasp what points are important for improvement activities together with the customer and share it with each other.
Recommended for companies
whose direction of improvement is decided
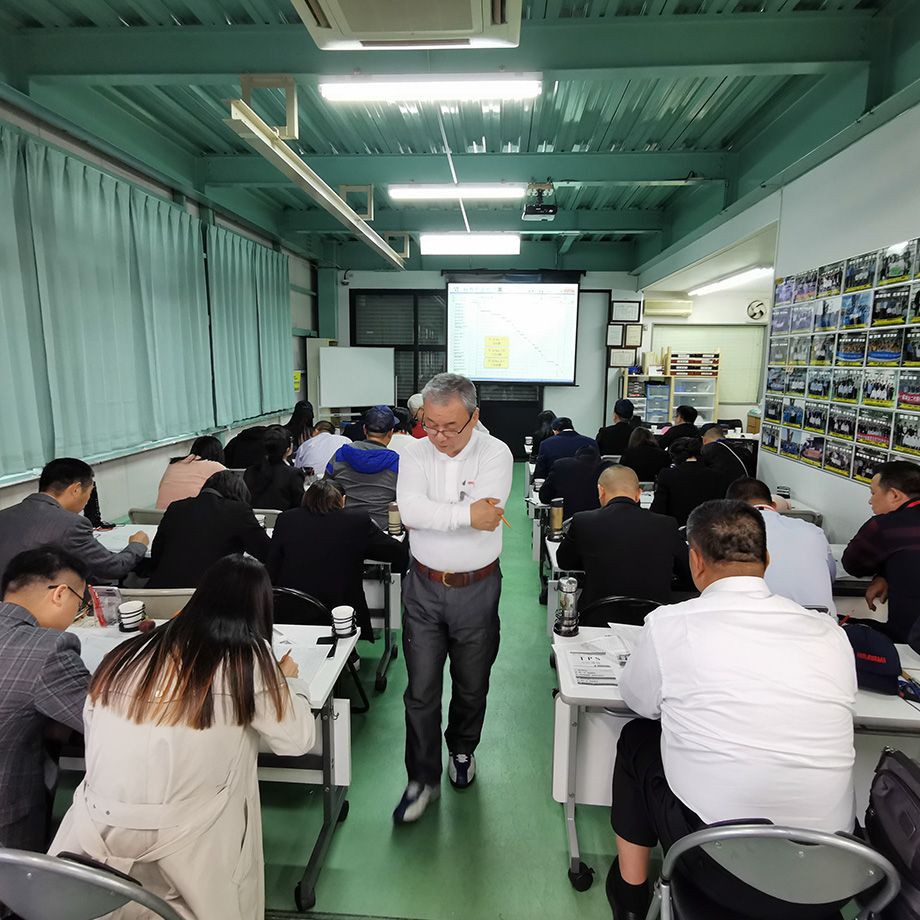
Genba Kaizen Consulting
Experienced consultants will visit factory shop floor around the world to improve problems of the shop floor together with customers, increase technical, quality, and cost competitiveness, and aim to build low-cost manufacturing shop floor.
Consulting by purpose Consulting by measure-
Remote Genba Kaizen Consulting
Remote Genba Kaizen service is a service that an experienced shop floor improvement consultant remotely diagnoses and improves the manufacturing shop floor using the internet communication. -
Seminar training
We have a wide variety of online seminars that combine theory and practice, including the TPS Jissen Dojo by Toyota OB instructors. -
Study tour
Until 2019, approximately 1,000 customers from overseas companies have come to Japan every year to receive our improvement training and return home to improve the efficiency and productivity of their factories. -
Inventory Management Operation Center (IMOC)
We provide solutions such as “inventory management consulting ~ outsourcing service”, inventory reduction / optimization, and inventory management work support / substitute.
Upcoming
Seminar / Training
SEMINAR / TRAINING
日時が決定している開催予定は現在ありません。
5 features why we are chosen FEATURES
-
01
Direct effect on management
Our guidance and improvements, with an emphasis on the “overall flow” from design to purchasing, manufacturing, logistics, and production control, will realize direct effect on management. -
02
Foster human resources
Improving the understanding of waste and practical experience of improvement according to the actual situation fosters human resources and strengthens the foundation of the production system. -
03
Production technology and tools
Experts in all fields are able to implement theoretically-constructed guidance, using consulting tools that have been continuously improved. -
04
Process oriented
With many years of experience, we also focus processes in improvement activities, and we can implement efficient improvement without waste. -
05
On-site principle
Through our “Genchi Genbutsu principle”, which is on-site actual-item principle, we are able to provide guidance that matches the actual situation of the shop floor and is acceptable to the shop floor workers.
3 reasons why we are chosen REASON
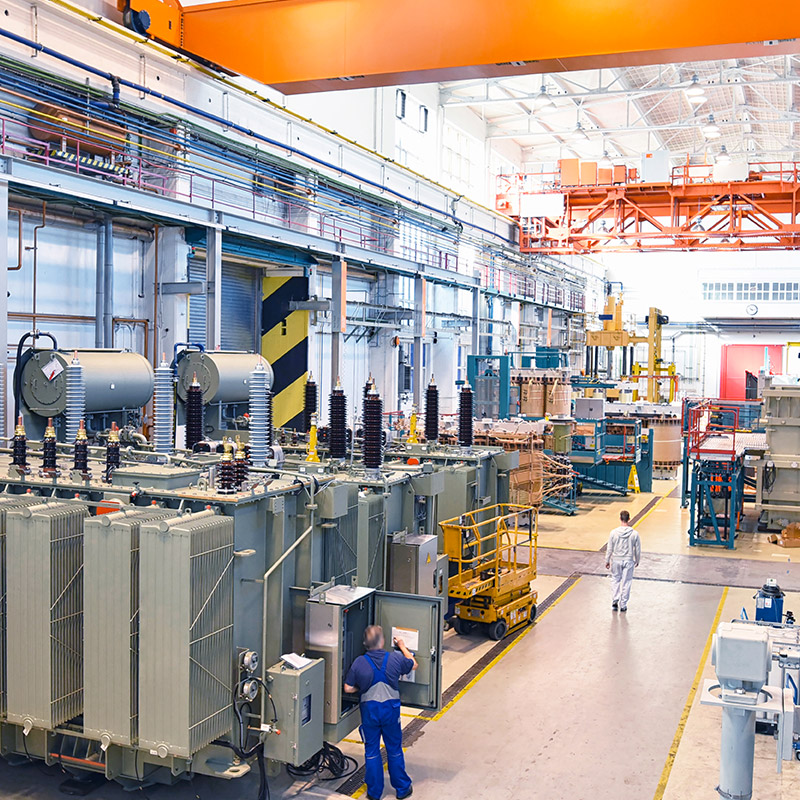
REASON 1
Improvement experience of
more than 1,500 companies in 40 countries
There must be the shop floor issues that cannot be solved by your own company alone. Improvements and reforms for manufacturing industry to survive, regardless of country or industry, need development of your human resources through practical experiences of improvement, and strengthening of your production system base.
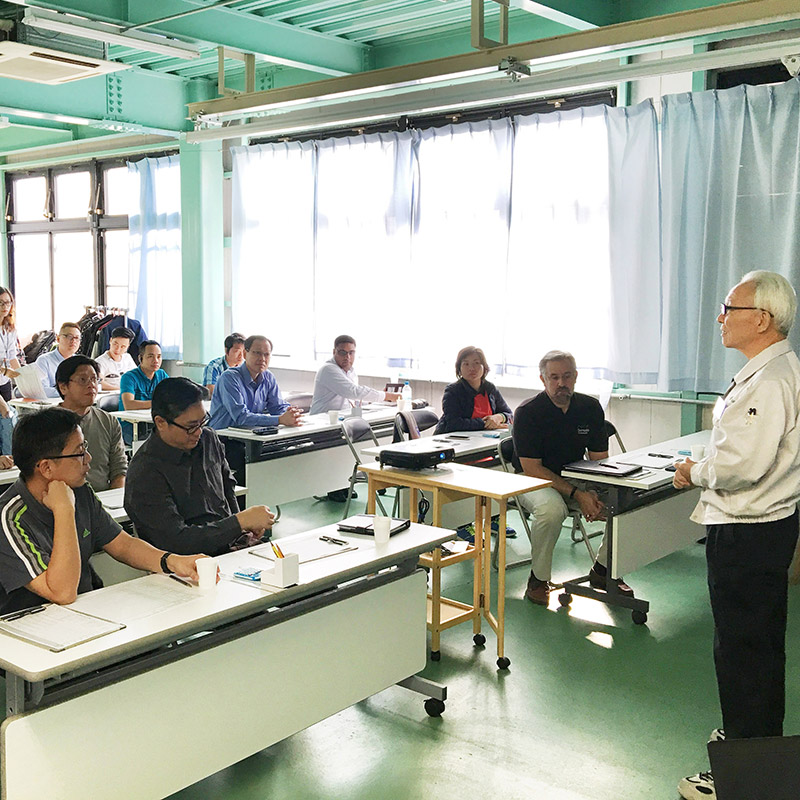
REASON 2
Consulting that shop floor workers
acknowledge our superiority and be pleased
In conventional consulting styles, there was a distance between consultant and the shop floor because it was promoted mainly consultant and management executives. Our consultant can provide a guidance without a distance between consultant and the shop floor through the guidance based on the "seeds of improvement" in a concrete way, instead of "finding fault" like a critic.
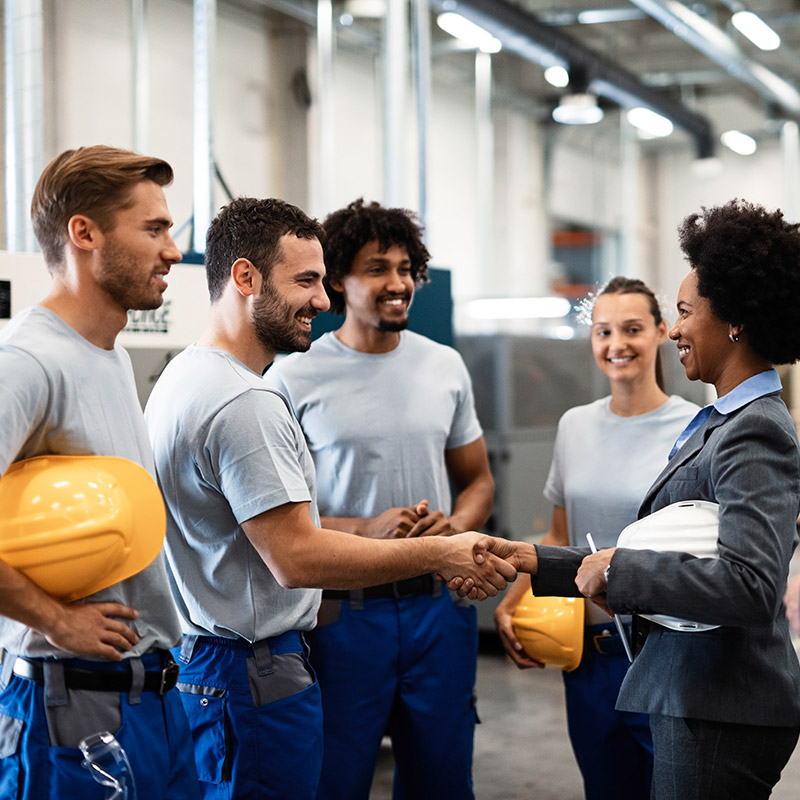
REASON 3
Continuous improvement will continue
even after the end of guidance
While strengthening "human resource development", we focus on the "overall flow" from design to purchasing, manufacturing, logistics, and production control, and provide guidance that matches the actual situation of your company. Continuous improvement will continue even after the end of guidance through the guidance that is acceptable to the shop floor workers.
Genba Kaizen Movie MOVIE
The consultants are all experienced personnel who have accumulated many achievements at the shop floor of major manufacturing companies. There are many consultants who have TPS trainer qualifications, and our practical and accurate consulting is highly evaluated both in Japan and overseas.