Engineers who have experience in the major project of constructing new manufacturing facilities are truly rare.
Furthermore, the construction of new facilities is not something that happens frequently, so the experience is often not passed down, leading to the current situation.
In such circumstances, when faced with the task of building a new factory, it’s common to not know where to start. Often, the project proceeds under the direction of design and construction firms, resulting in escalating costs and the creation of facilities that are not user-friendly. It’s a common story to hear about people having to make do with what they have, despite the challenges.
At HIRAYAMA Consulting’s ‘Factory Startup Support’, we offer comprehensive assistance throughout the entire process of establishing a new manufacturing facility:
✔ From the construction of new factories to layout design
✔ Production preparation (production lines/equipment)
✔ Building production management systems
✔ From staffing to the initiation of production
✔ Continuous production activities
Our team of experienced professionals and operational units are dedicated to providing full support in all aspects.”
Four Types of Support
for Factory Startups
FEATURES
-
1
Efficient Advancement of New Factory Construction Projects
-
2
High-Productivity Layout Design Based on TPS Principles
-
3
Building a Production Management System for Real-Time Visibility of the Shop Floor
-
4
Securing Personnel and Implementing Rapid Production Startup
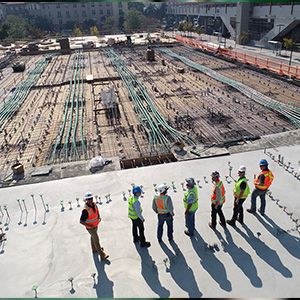
New Factory Construction (New Builds/Expansions/Renovations)
Key Points
- Site Selection
- Factory Orientation
- Space for Future Expansion
- Cost-Effectiveness of Layout Levels
- Major Factory Specifications
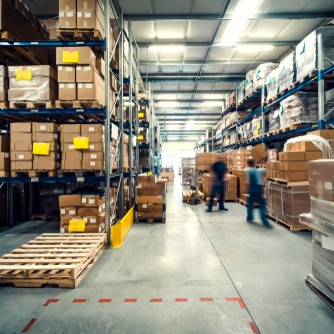
Production Preparation
Key Points
- Process/Equipment Planning (Machining/Assembly Evaluation)
- Line/Process Layout (Design based on TPS principles)
- Production Technology Development (Methodology/Jigs/Molds/Automation/Poka-Yoke)
- Workload Planning (Work Time/Personnel)
- Quality Assurance Planning (QC Process Charts/FMEA)
- Work Standards/Standard Work Setup
- In-Plant Logistics (Design based on TPS principles)”
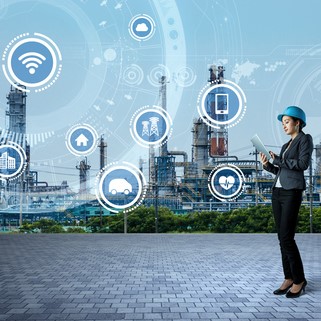
Production Management System (ERP/MES/DX/IoT)
Key Points
- Collecting management decision information in real-time
- Accurate data capture
- Improving operational efficiency
- Smart operations that do not overburden the shop floor
- Integration of MRP systems and Kanban systems
- Visualization
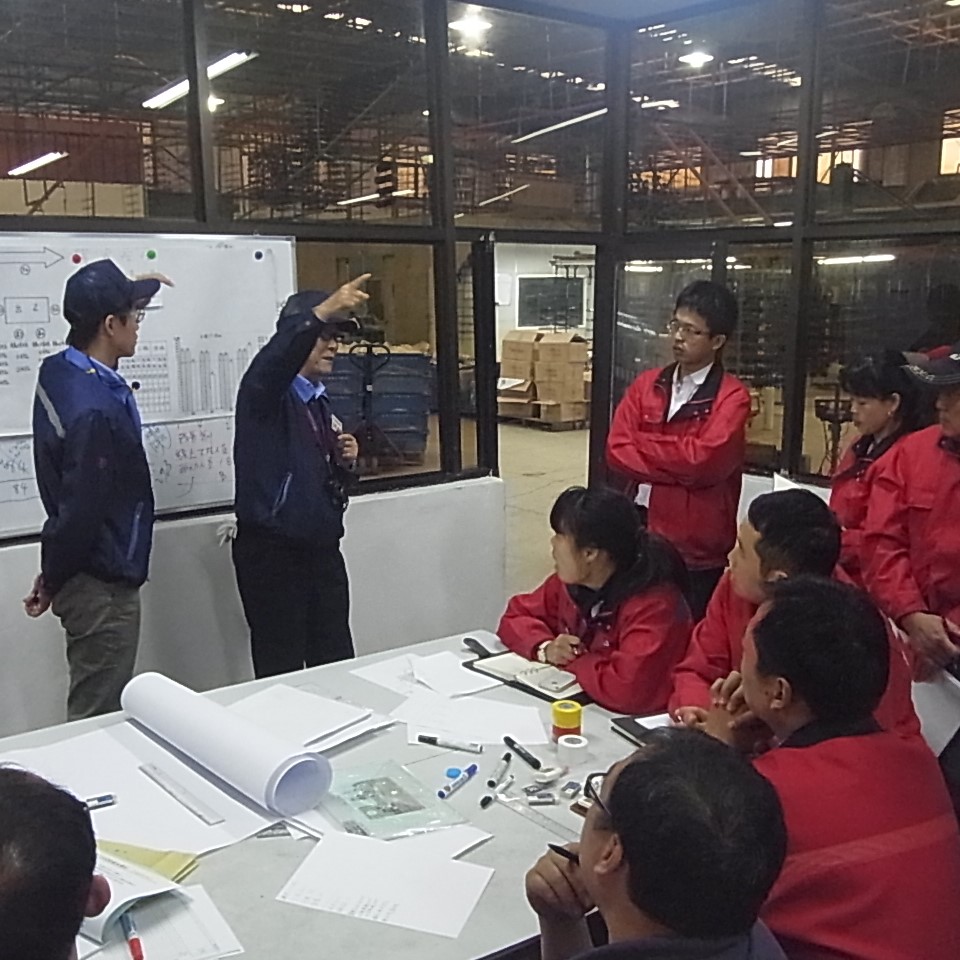
Securing Personnel and Production Activities
Key Points
- Manufacturing Outsourcing
- Staffing Services
- Foreign Talent
- Field Engineering
- Continuous Improvement Activities”