ジャストインタイムで部品供給を実現
部材払出し準備~MC投入までのリードタイムを短縮し在庫削減
結果
・在庫はゼロへ
プリント基板製造のA社は、生産管理業務の改善が進んでおらず、部材在庫は数年間増え続け経営を圧迫していた。
そこで、MCの作業開始時間に合わせジャストインタイムでの部材投入を検討したが、部材払出し準備からMC投入の作業時間が、部品によって大きく異なっていたため、解決できないままであった。
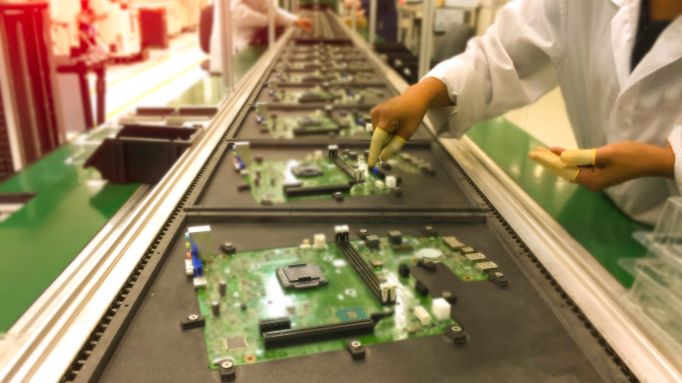
- 業界詳細
- プリント基板の製造
- 国
- 日本
- 企業規模
- 従業員 200名
- 課題
- 収支改善
- 目的
- 収益改善
- 業界
- 電機・電子
スケジュール
ステップ1 作業者、監督者が日常業務の中から職場の問題点を洗い出すステップ2 あるべき姿を描き、現状とのギャップを明確にする
ステップ3 改善を実施する
現状の問題点とあるべき姿
現状の姿 | 部材払出し準備からMC投入までの作業時間合計が50分~180分掛かっている。 部材探しに手間取り作業時間のバラつきが大きい。 また、仕掛品が現場で停滞している。 |
あるべき姿 | 払出し準備からMC投入まで120分。工程間の停滞はゼロ。 |
払出から加工までの工程
<現状の姿>
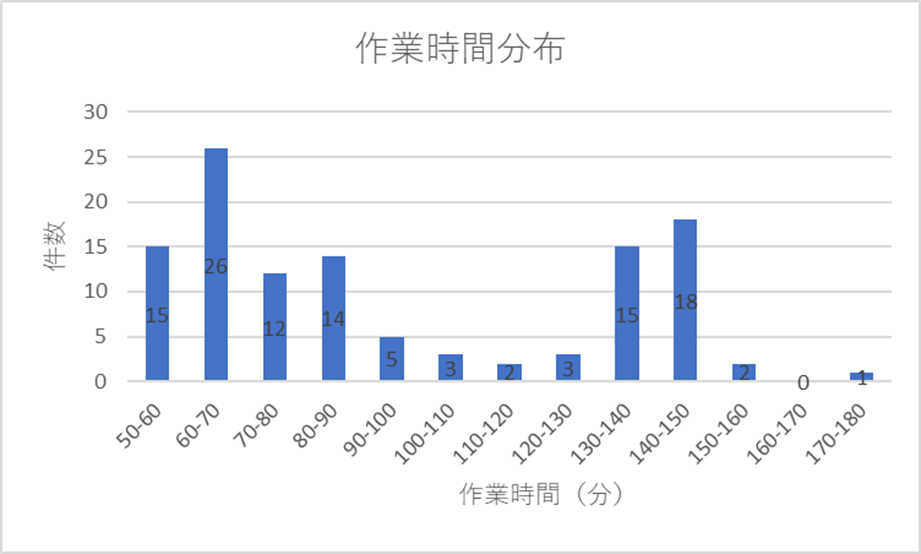
作業時間を全ての部品において120分に平準化が出来れば、MC作業開始時間に合わせ、停滞ゼロで部材投入ができるようになる
<改善後の姿>
改善項目
まとめ
生産管理部門と製造部門が連携して改善活動をすることで全体最適でのリードタイム短縮と在庫削減が実現されます
現場改善のスペシャリスト

伊藤 彰洋(いとう あきひろ)
現場改善コンサルタント
業種を問わず、現場改善の文化を企業へ根付かせ、現場の人間と共に改善活動をおこない、品質向上・生産性向上・リードタイム短縮を実現する。 また、生産管理システムを手掛けた経験により、「営業~資材~生産管理~製造~外注」と工場内のあらゆるプロセスにおいて改善活動を実践する。
選ばれる3つの理由 REASON
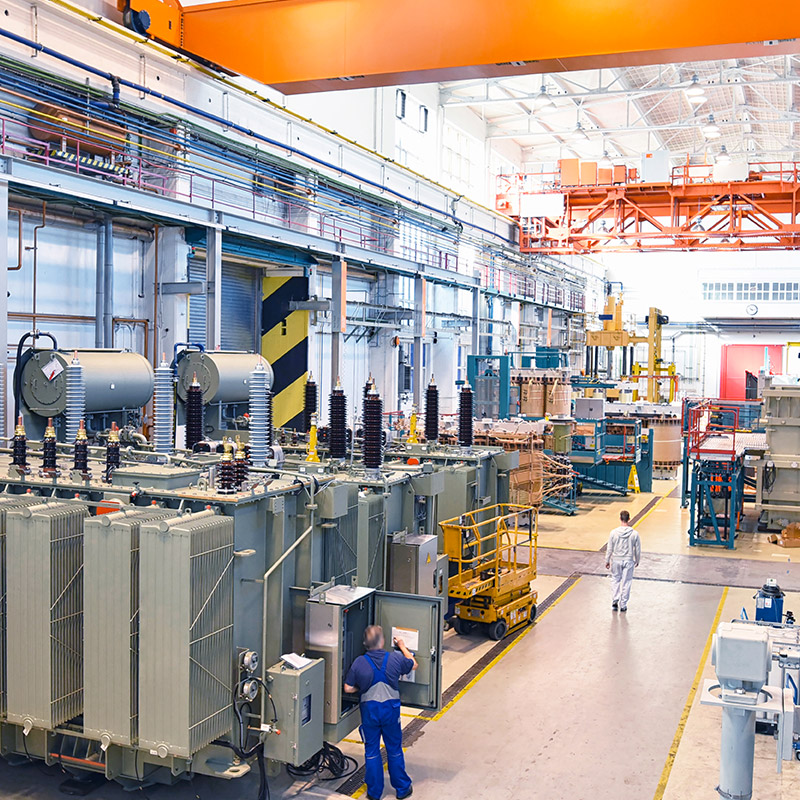
REASON 1
40ヶ国、
1,500社以上の改善実績
自社だけでは解決できない現場の問題は必ずあります。製造業が勝ち残るための改善・改革は、国や業界を問わず、改善の実践体験を通じて、人材を育成し、生産体制基盤を強化することが必要です。
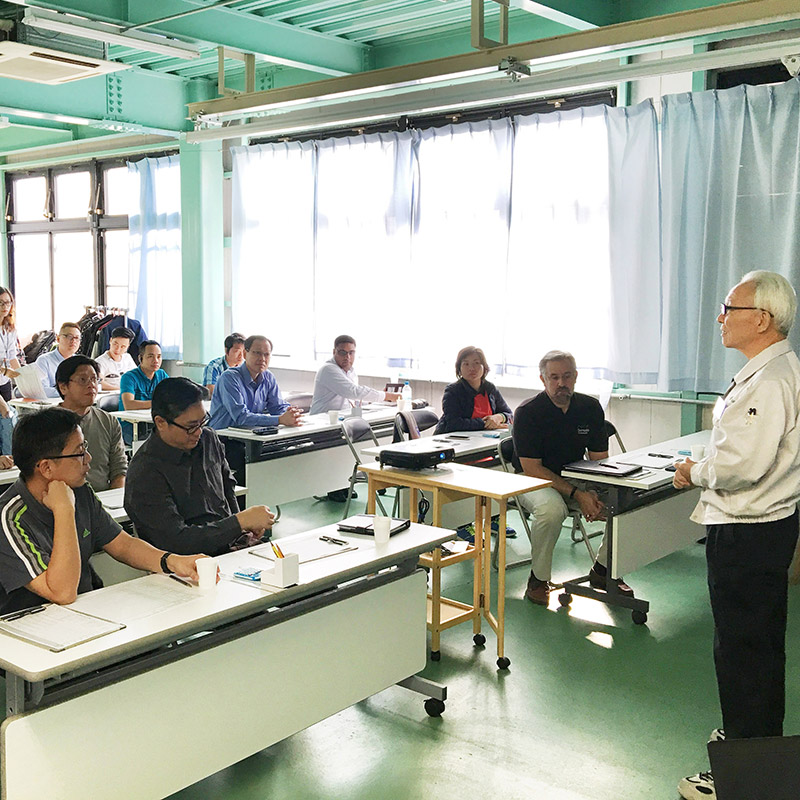
REASON 2
現場が一目置き、
喜ぶコンサルティング
従来のコンサルティングでは、経営層とコンサルタントが中心になってすすめるため、現場とコンサルタントの間に距離がありました。弊社コンサルタントは、評論家的な「あら探し」ではなく「改善の種」を具体的に見出す指導により、現場の人間との隔たりのない指導をすることができます。
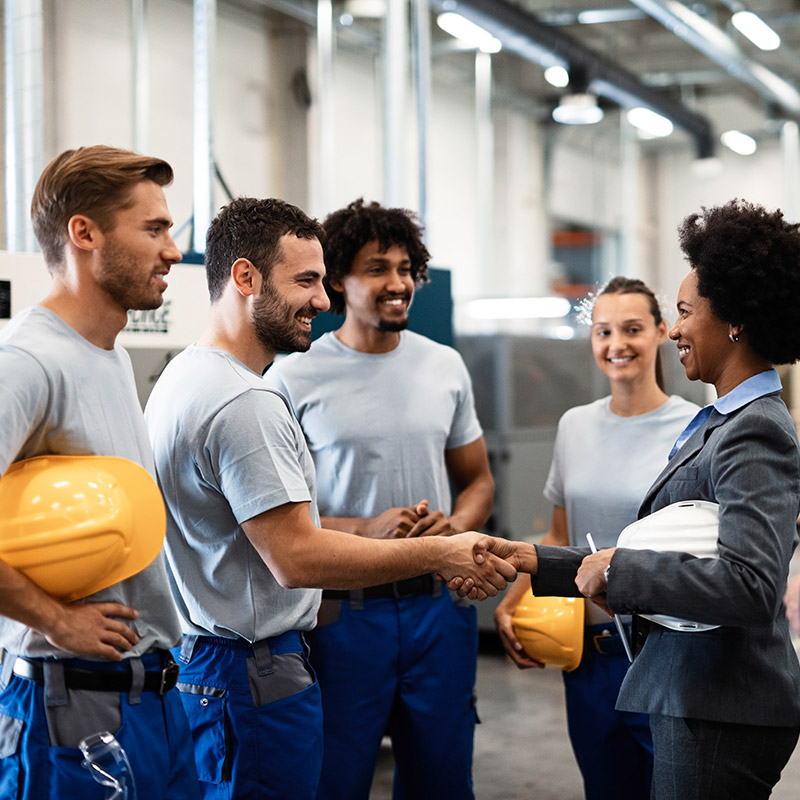
REASON 3
指導終了後も
継続的改善がされる
「人づくり」を強化しながら、設計から調達・製造・物流、そして生産管理と「全体の流れ」を重視し、貴社の現場の実態に合った指導を実施。現場が納得できるコンサルティング指導を行うことで、指導終了後も改善文化が継続されます。