Achieving “Just-in-Time” in Parts-Supply Inventory
Reduction by Shortening Lead-Time from Material Preparation of Delivery to Put in MC
Results
・Achieving Zero Inventory
Company A, which manufactures printed circuit boards, had not made progress in improving production control, and parts inventories had continued to increase for several years which had been giving burden on management.
So, “just-in-time” had been under consideration for putting materials according to MC start time, but times of operations from preparation of material delivery to put in the MC differed greatly depending on the type of parts so that had been remained unsolvable.
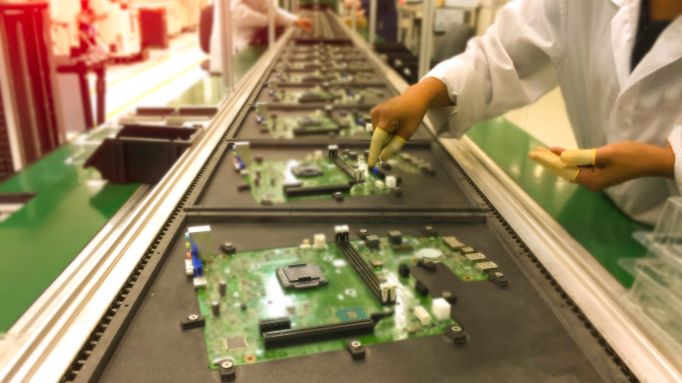
- Business field
- Manufacturing of printed circuit boards
- Country
- Japan
- Company size
- 200 employees
- Issue
- financial Improvement
- Purpose
- Profitability improvement
- Industry
- Electrical and electronic
Schedule
Step1 Operators and supervisors identify problems in the site out of their daily work
Step2 Imagine what it should be and clarify the gap between the current state
Step3 Implement KAIZEN (improvement)
Current Problems and Ideal State
Current State | It takes 50 to 180 minutes in total from delivery preparation of parts to put into the MC. In addition, work-in-process is stagnant at the site. It takes a lot of time to look for parts and each looking time differs depend on types of parts. In addition, work-in-process is stagnant at the site. |
Ideal State | 120 minutes from delivery preparation to put into the MC. No stagnation between processes. |
Process from Delivery to Processing
<Current State>
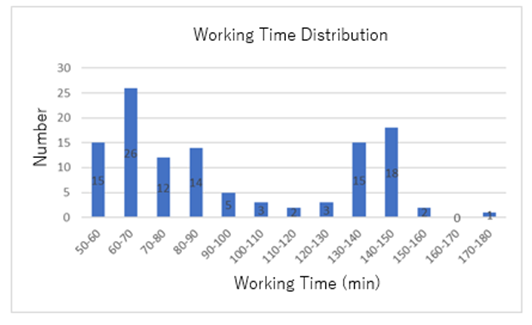
If the work time can be leveled out to 120 minutes for all parts, it enables to achieve zero stagnation to put in parts according to the MC start time.
<After Kaizen>
KAIZEN Items
Summary
the production control department and the manufacturing department to carry out KAIZEN activities, it enables to shorten the lead time and reduce inventory in the overall optimum.
Genbakaizen Specialistト

ITO, Akihiro
Genba Kaizen Consultant
Continuously he has been engaged in effective introduction process of Production Management System to small and medium enterprise and even big enterprise.
Consultants from major companies
with experience in over 40 countries will respond.
Please feel free to contact us.
If you are in a hurry, please call us.
(Japan time)
Except for Saturday, Sunday, holidays, Year-End and New-Year holidays
3 reasons why we are chosen REASON
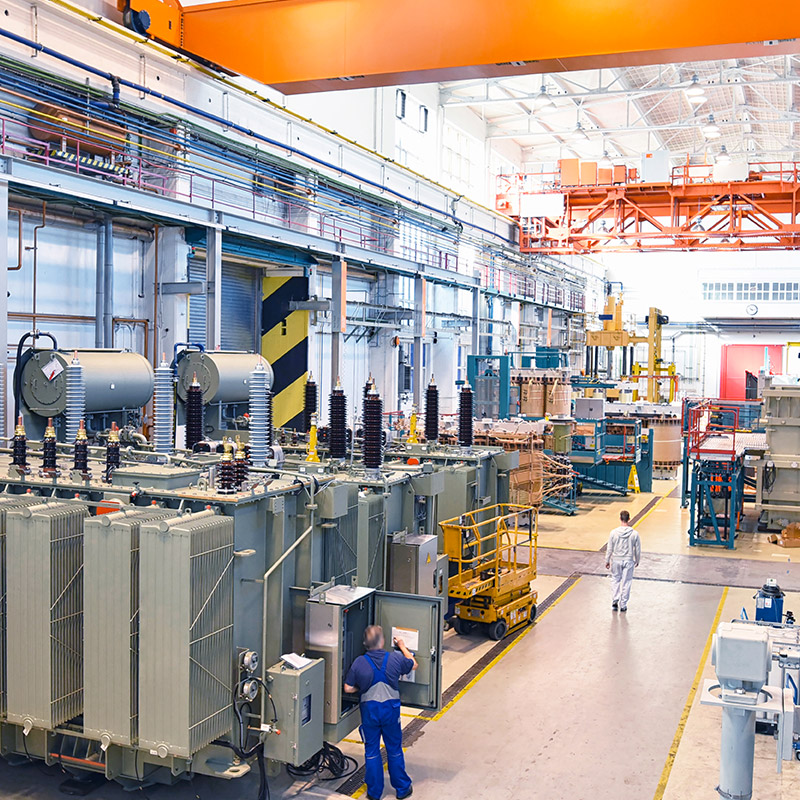
REASON 1
Improvement experience of
more than 1,500 companies in 40 countries
There must be the shop floor issues that cannot be solved by your own company alone. Improvements and reforms for manufacturing industry to survive, regardless of country or industry, need development of your human resources through practical experiences of improvement, and strengthening of your production system base.
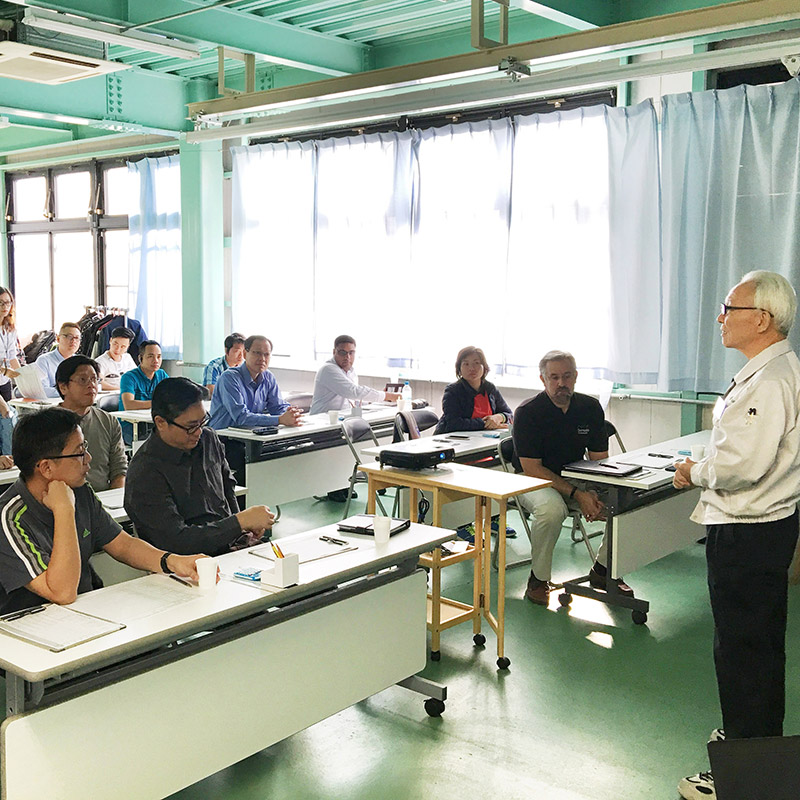
REASON 2
Consulting that shop floor workers
acknowledge our superiority and be pleased
In conventional consulting styles, there was a distance between consultant and the shop floor because it was promoted mainly consultant and management executives. Our consultant can provide a guidance without a distance between consultant and the shop floor through the guidance based on the “seeds of improvement” in a concrete way, instead of “finding fault” like a critic.
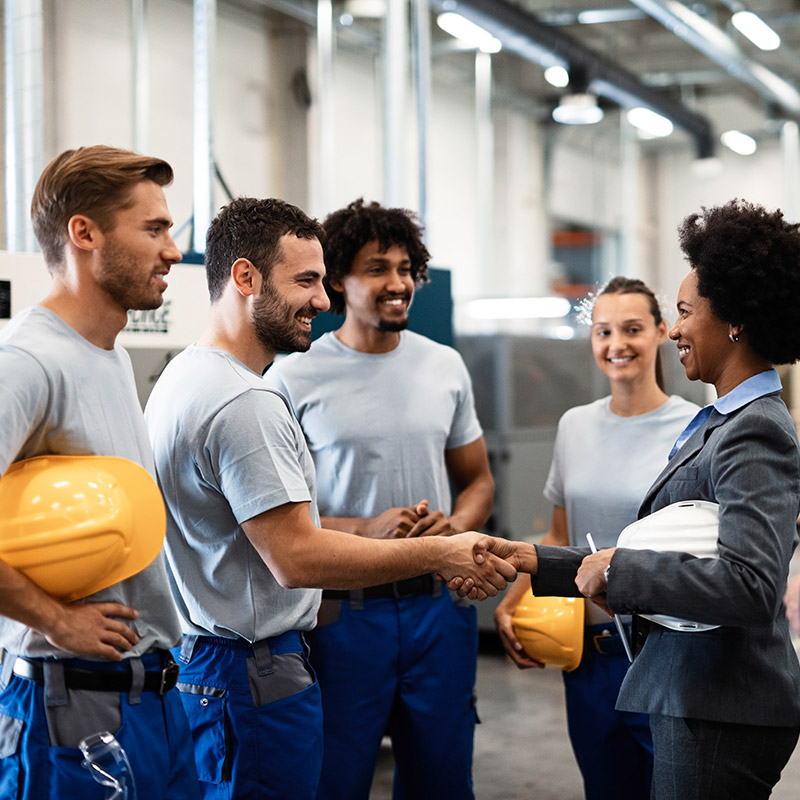
REASON 3
Continuous improvement will continue
even after the end of guidance
While strengthening “human resource development”, we focus on the “overall flow” from design to purchasing, manufacturing, logistics, and production control, and provide guidance that matches the actual situation of your company. Continuous improvement will continue even after the end of guidance through the guidance that is acceptable to the shop floor workers.