高いレベルの改善活動の成功体験が
人材を育成し強い現場をつくる
結果
- 6ヶ月間の改善活動で、生産性 169.6% UP
- 自分たちでは解決できなかった高いレベルの改善ができるようになった!
この工場では自分達で改善活動を進めていたが、自力で出来ることは全てやったという意識があり活動が停滞していた。
そこで日本人の社長が一度、現場改善コンサルティングに外注し、現場を見てもらおうということで平山コンサルに声が掛かった。
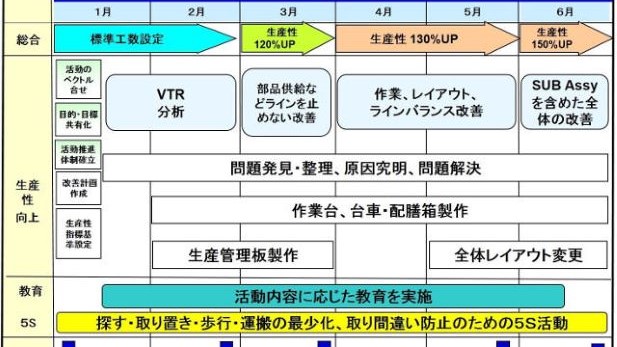
- 業界詳細
- 自動車部品
- 国
- ベトナム
- 企業規模
- 従業員 約300名
- 課題
- 改善活動のマンネリ化
- 目的
- 収益改善人材育成
- 業界
- 自動車
スケジュール
- 工場診断
- 改善プロジェクトの目標を設定
- 改善活動
ステップ1 工場診断
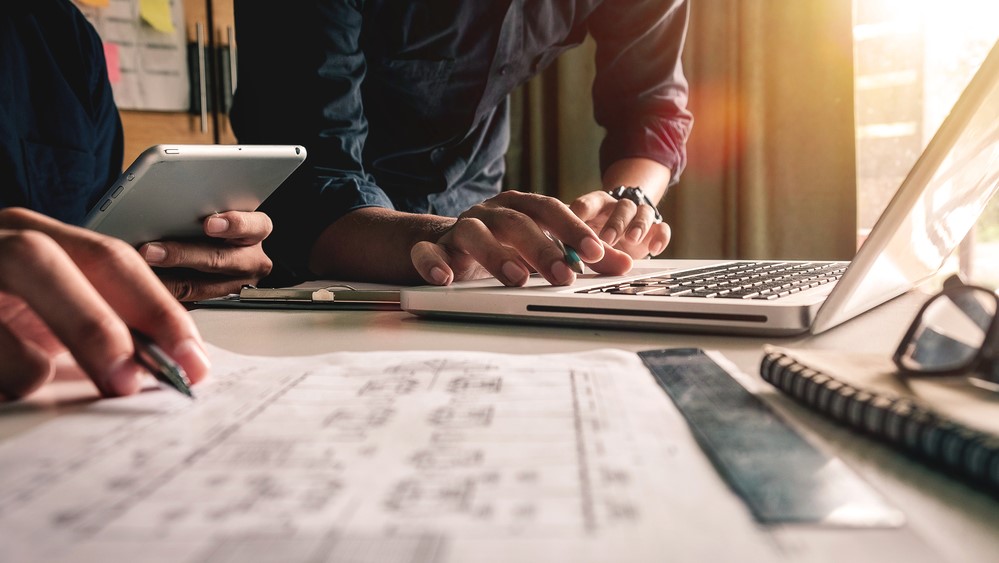
まず現場にどのくらいムダがあるかを調査するため「1日工場診断」を実施。現場に行くと過去に自分たちで一生懸命改善した様子を随所に見ることが出来たが、確かにその後に更に高いレベルで改善を進化させたという状況は見ることが出来なかった。
問題点を分かりやすく伝えるために現場で撮った写真を入れた「工場診断報告書」を35頁で作成し、現場診断の報告会を実施。
診断結果
現場には下記のような問題が残されていた。標準工数の不備 | 要素作業ごとの工数測定がされていないので標準工数がない |
作業のムダの発生 |
・ラインバランスロスが放置されている ・手持ち、取り置き、動作などのムダが放置されている ・構内物流、材料供給のムダが放置されている |
整理整頓の不徹底 | 5Sが不徹底でありムダが発生している |
生産管理不備 |
|