What is the “Skill” to Implement the Principles of “TPS”…..
Hello everyone. I’m TR from the TPS Practice Dojo.
At the TPS Dojo, we learn about TPS through both lectures and practical application, mastering methods for cost reduction.
But, is learning about TPS and implementing cost reduction really all it takes to make improvements?
The answer is NO.
Without “skills,” simply being well-versed in the principles and knowledge of “TPS” will not allow you to make effective “improvements.”
The “skills” necessary for implementing TPS are as follows:
1.「TJI-How to Teach Work」
2.「TCS- How to Handle People」
3.「TPS-How to Improve」
At Toyota Motor Corporation, training on these three aspects, known as “TWI” (Training Within Industry), is almost universally provided to supervisors and their potential candidates.
This training continues today as the foundation for supervisor skill training and personnel development.
In essence, this is also the foundation of the Toyota Production System (TPS).
Scene from the TPS Practice Dojo
It’s “people” who make things.
The supervisors on the shop floor work there every day and stand in the most suitable positions for making improvements.
Improvements led by them, who possess leadership and communication skills to handle people, can produce effective results.
**TPS Dojo Toyota-style Work Teaching Program Example**
- The role of the person teaching (definition of a trainer)
- Five necessary conditions for the trainer
- The need for training
- Imperfect teaching methods
- Correct teaching methods
- How to teach (demonstration)
- Preparations before teaching
- Training
- Task breakdown
- Practice (demonstration & training)
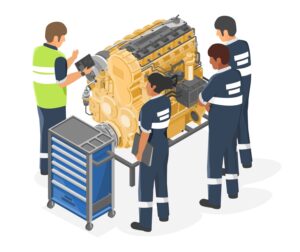