How to Improve Care Facilities?
Challenges Faced in the Tenth Year of Operation
Result
・Improvement of staff working conditions
・Reduction of task time to approximately one-third
This is the second part of the improvement case study for the preliminary on-site assessment of Care Facility A, now in its tenth year of operation.
In the second part, we will introduce some improvement examples of “enhancing the visual impression” and“improving the efficiency of caregiving staff’s tasks.”
Click here for the first part
**Facility’s Capacity to Accommodate**
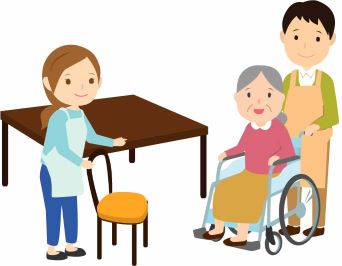
- Industry Details
- Care Services Business
- Country
- Japan
- Company Size
- Fewer than 50 employees
- Challenge
- Achieving profitability
- Objective
- 収益改善生産性 向上コスト削減リードタイム短縮その他
- Industry
Day Service Area: Streamlining Workflow
|
![]() |
<Improvement Points>
・Implement 5S by categorizing items on the counter into “necessary/unnecessary” and “immediate use/not immediate use.”
・Reevaluate the placement of shelves for each task, or use carts instead of shelves so that when the cart is brought over, everything needed for the task is available.
Example: tea cart, coloring cart, snack cart, word game cart, etc.
Improve workflow to increase turnover rate
<Improvement Points>
・The main issue in increasing the number of users is how to improve the turnover rate for bathing.
・To bathe 22 people in two bathrooms from 9:00 to 12:00 (180 minutes), it requires 16 minutes per person.
・Increase the utilization rate of the bathtubs by external setup.
Vending Machine & Bulletin Board
<Improvement Points>
・Consider replacing the vending machine with a newer, slimmer model, or reevaluate its placement.
・Do not post items all over the place; use the bulletin board.
・Clearly label the bulletin board with titles such as “Information Bulletin Board” and decide what should be posted there.
5S for the Office」
|
![]() |
<Improvement Points>
・Implement 5S by categorizing items into “necessary/unnecessary” and “immediate use/not immediate use.”
・Reevaluate the placement of supplies according to the workflow (streamlining the workflow).
For inquiries about on-site assessments, please contact here