Not to Cease Growing even in the COVID-19 Crisis!!
~Operation KAIZEN in a Welding Factory~
Result
⇓
After KAIZEN Total Cycle Time 700” Production Volume 30% increase
Background
At the plank welding factory of our client, entering of people (including the consultant) other than the company with exceptions of special circumstances was prohibited under influence of the COVID-19 crisis. For that reason, KAIZEN promotion had stagnated.Subjects
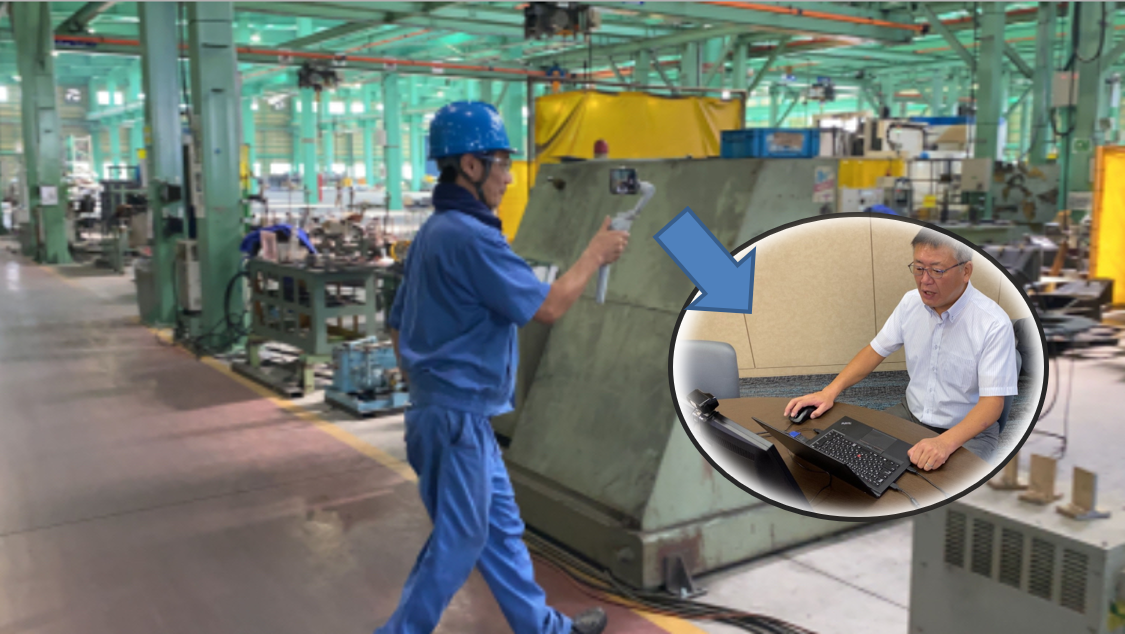
- Details of Industry
- Plank welding factory
- Country
- Japan
- Business Scale
- Employees approx.200
- Purpose
- Profitability improvement
- Industry
- Metal
Remote Gemba (on site) KAIZEN Implementation Procedure

Firstly, the consultant grasped a current situation of the factory by a web meeting. Then, a member of the factory shot videos of “ the distortion elimination process” under the instruction of our consultant in the office.
The camera used for video shooting this time: iPhone
Prepared items by the client
- Factory layout
- Selection of work site, product
- Operation process chart of selected product
- Wireless LAN
- PC, Smartphone, Earphones, Microphone, Tripod, Spare Battery
- Meeting room
The obstacle was the over-time hours for “ distortion elimination process” which proportions to the production volume in the regular working hours
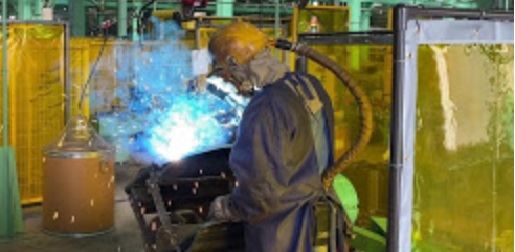
At the on-site, the KAIZEN effects implemented before COVID-19 crisis were appeared, and the production volume for the welding process in the regular working hours was increasing; however, the KAIZEN for the last process, “distortion elimination process”, had not promoted. Therefore, as the production volume of the prior process increased, the over-time hours for the “distortion elimination process” was increased, and the problem became apparent.
Problems and KAIZEN Contents
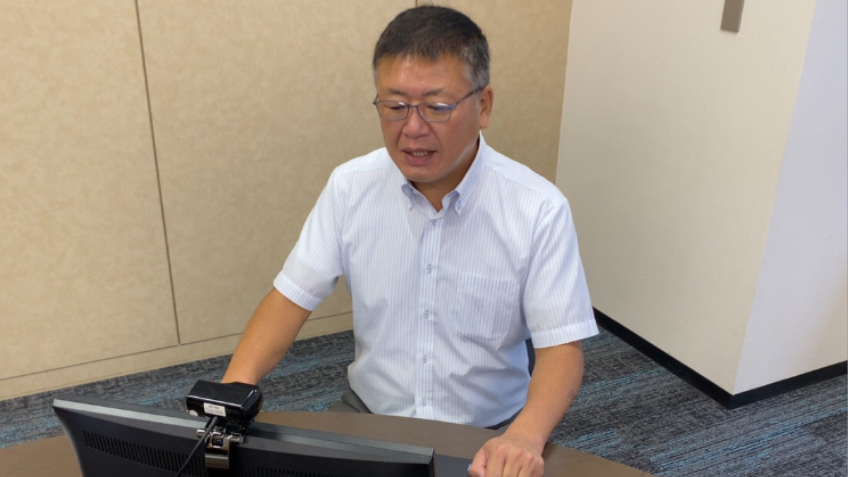
As the consultant checking operations through PC monitor in the office, following wastes of operations were found.
A lot of wastes of walking for operators | Devices for operation to be kept at hand |
Holding operation of the water hose at the water cooling | Making a jig to hold the water hose, and eliminating holding operation (releasing from hand) |
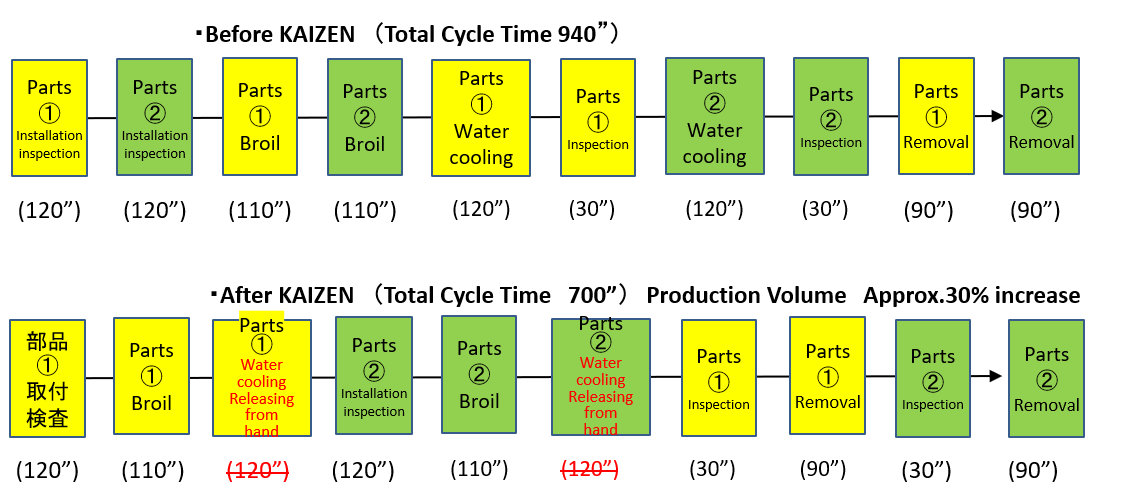
SUMMARY
This time, operation analysis and simple KAIZEN of “ releasing from hand” was implemented. As the next step, improvement for distortion itself to be promoted by reviewing the prior process of welding.
Gemba Kaizen specialist

ITO, Akihiro
Process improvement consultant
He worked for JIT Institute, Tokyo for 20 years.( JIT: Just In Time). During this period, he has learned Just In Time philosophy and method of improvement of productivity in manufacturing plant. Continuously he has been engaged in effective introduction process of Production Management System to small and medium enterprise and even big enterprise.
Consultants from major companies
with experience in over 40 countries will respond.
Please feel free to contact us.
If you are in a hurry, please call us.
(Japan time)
Except for Saturday, Sunday, holidays, Year-End and New-Year holidays
3 reasons why we are chosen REASON
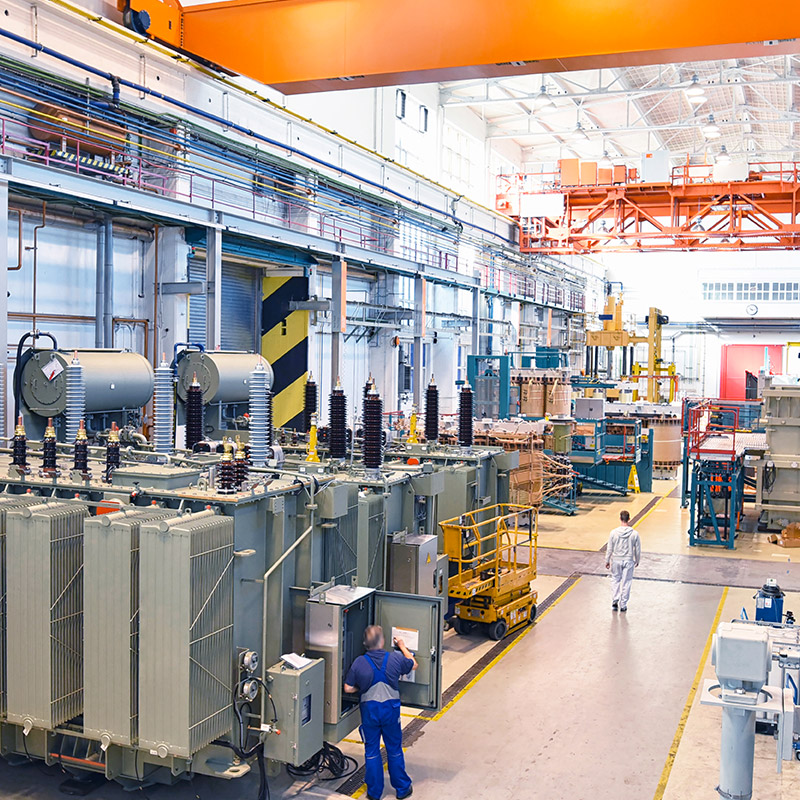
REASON 1
Improvement experience of
more than 1,500 companies in 40 countries
There must be the shop floor issues that cannot be solved by your own company alone. Improvements and reforms for manufacturing industry to survive, regardless of country or industry, need development of your human resources through practical experiences of improvement, and strengthening of your production system base.
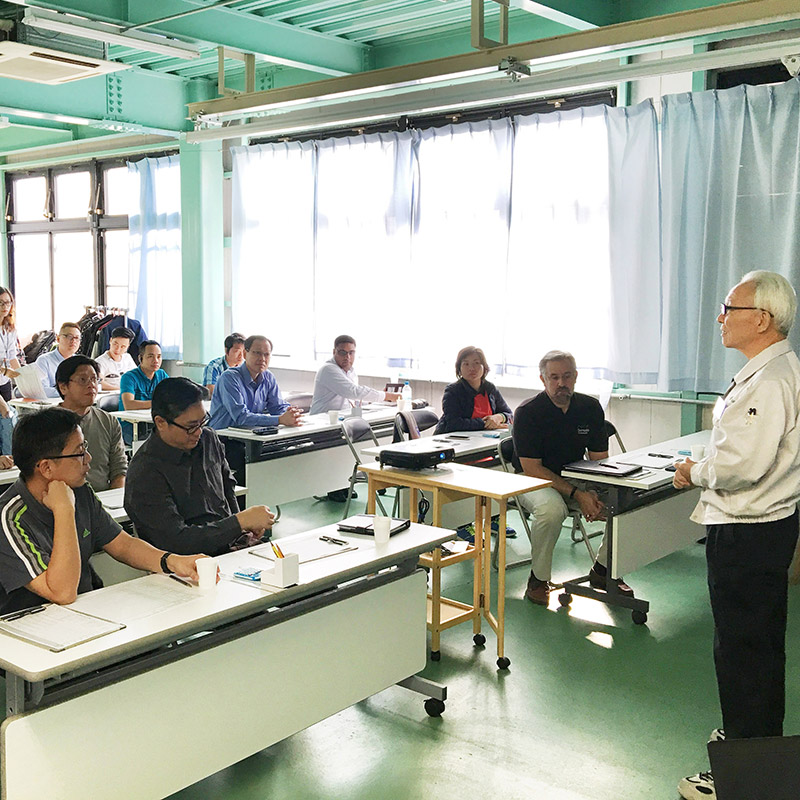
REASON 2
Consulting that shop floor workers
acknowledge our superiority and be pleased
In conventional consulting styles, there was a distance between consultant and the shop floor because it was promoted mainly consultant and management executives. Our consultant can provide a guidance without a distance between consultant and the shop floor through the guidance based on the “seeds of improvement” in a concrete way, instead of “finding fault” like a critic.
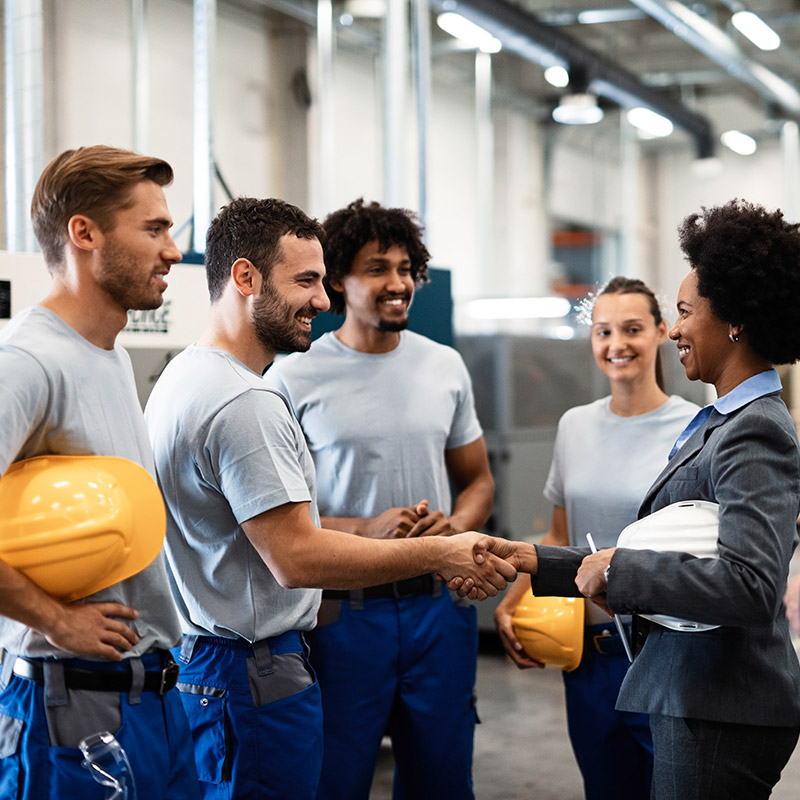
REASON 3
Continuous improvement will continue
even after the end of guidance
While strengthening “human resource development”, we focus on the “overall flow” from design to purchasing, manufacturing, logistics, and production control, and provide guidance that matches the actual situation of your company. Continuous improvement will continue even after the end of guidance through the guidance that is acceptable to the shop floor workers.
Consultants from major companies
with experience in over 40 countries will respond.
Please feel free to contact us.
If you are in a hurry, please call us.
(Japan time)
Except for Saturday, Sunday, holidays, Year-End and New-Year holidays