During my active career, I had the opportunity to experience three projects: two new constructions and one renovation of an existing facility. I would like to share this valuable experience with you.
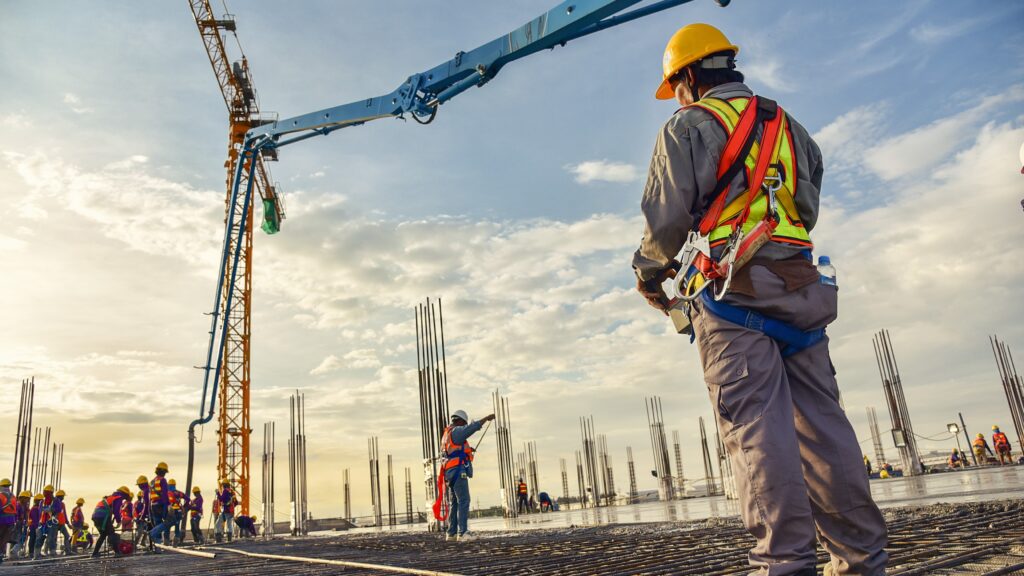
1. Factory Construction and Production Engineers
In addition to experience as production engineers, factory construction requires a comprehensive understanding and know-how of building construction, equipment installation, and more. This is not something that can be quickly learned or acquired through short-term training; it often involves on-the-job training (OJT) with experienced seniors and learning from failures, which are valuable assets in themselves.
The process from factory building and maintenance to the installation, adjustment, and operation of equipment after completion is fraught with continuous troubles. Coordinating daily with construction companies, equipment manufacturers, installation teams, and transportation companies to solve problems on-site is crucial for managing the construction schedule as planned. Safety management becomes especially important as fires or injuries can significantly impact the startup phase.
Furthermore, the costs related to production preparation can be very high, making it important for production engineers to manage these expenses within the budget. Therefore, having a measure for construction duration and costs is also necessary.
2. Factory Startup: New Construction in Japan
The construction company resolved issues that arose during the construction according to the architectural blueprints. During the finishing stages of construction, there were many adjustments related to the preliminary installation of production equipment and foundational work (related to the building).
Due to its proximity to the sea, the entire site was raised, and special construction methods were employed, such as driving piles down to the bedrock on reclaimed land. At the time, this resulted in the construction of Japan’s largest single building exceeding 120,000 sqm. Furthermore, the factory was designed to optimize information and logistics flow from the entrance to the exit.
3. Factory Startup: Europe
Due to various problems arising daily, we held regular meetings every day. We organized the issues that occurred each day, assigned responsibilities, set deadlines, and followed up daily. Amidst the new challenges (country, ethnicity, language, European customers, collaborating companies, etc.), we established a European hub.”
4. Renovation of an Existing Factory
After relocating the piping equipment, we cleared out the remaining discarded equipment, as well as air conditioning ducts, air pipes, steam pipes, electrical ducts, and wires that were hanging from the factory’s beams.
Once the factory was cleared, we conducted inspections and maintenance on various systems including the substation, industrial water supply devices (inspection and disinfection), the septic system, repairs for leaks, air conditioning systems, and replacement of shutters including the installation of quick shutters. We also worked on the factory’s oil recovery facilities, supported notifications to river management organizations, and provided assistance with notifications for specific facilities.
We implemented a systematic commercial packaging line that includes milk run for part pickups and multiple deliveries, and introduced a cardboard box manufacturing machine capable of producing boxes in the smallest unit of one box.
Currently, there is a trend of recovery from the COVID-19 pandemic, and it is anticipated that securing construction companies and workers will become more difficult. In response to the labor shortage, it is considered necessary to elevate the level of construction management through the generation of flexible ideas and improvements in construction work.
The Consultant Who Wrote This Column
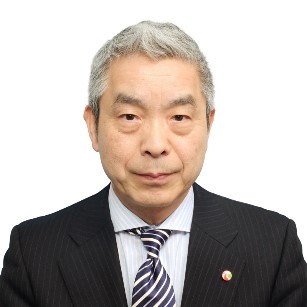
Takeshi Kawabata
A former member of the Production Engineering Department at DENSO Corporation.
He acquired and implemented the Toyota Production System through direct experience with Toyota Motor Corporation. Additionally, he has been involved in the construction of two new factories and the renovation of one existing factory, managing construction schedules and budgets as planned, and achieving optimization of information and logistics from the factory entrance to exit. He was responsible for overseeing the construction of Japan’s largest single factory building at the time, covering 120,000 square meters.