TPS also prohibits “Three Cs”
*Three Cs: Closed spaces with insufficient ventilation, Crowded conditions with people, Conversations in short distance
“Material and Information flowchart” is an important means to realize change from the three Cs situation to the “Just-in-time” that you make and transport what you need, when you need it, as much as required.
COVID-19 seemed to be almost under control in late May, but the number of infected people began to increase again in mid-June. And now (early August), the number of infected people nationwide per day has doubled from the peak in April, and the record is updated every few days. This kind of recurrence was expected to some extent, but again I feel this virus is stubborn and horrible.
Even though we do not have enough medical knowledge, we can expect that it will take a long time to fight off the virus, so we must create a new lifestyle in order to prevent the spread of infection and achieve economic activities at the same time. The key point for that is to avoid “Three Cs”. It is necessary to take concrete measures to avoid “Three Cs” not only in daily life, but also in workplaces, medical sites, educational/academic places, leisure places, and other places where people interact. Humans are basically supposed to live in a group, and the quality of our life is improved by the three Cs, so that we can enjoy a spiritual fulfillment. It is quite terrible because we have to stop that important “Three Cs”. However, this is the only way to prevent the spread of infection at the moment, so there is no choice but to implement it.
Why are the “Three Cs” prohibited in TPS?
By the way, the word “Three Cs” is not used in TPS, but the word “dense” is sometimes used in the phrase “dense situation”. In the general society before the COVID-19 occurs, the “dense situation” was not always a bad image, but it has a bad image in TPS. If the parts and finished products are in a “dense situation”, that means there is an extra inventory that you do not need to have, and you should doubt that there is a problem (waste) that should be improved.
For example, the situation that parts and finished products are piled up in a dim warehouse, and old ones are full of dust. Or the situation that some parts are always put between the manufacturing processes and stagnant. If you have such a situation, you need to consider why you have to keep inventory there. Then, some kind of problems or items to be solved (wastes) should be apparent.
In TPS, the situation that materials (parts, half-finished products, finished products) are constantly flowing is ideal. The common “one piece flow production” is the best example of this. It is easy to understand if you think of a river. If the water of the river is constantly flowing, the water will rarely get dirty. However, if there is a stagnant place, the water there easily gets dirty. This means that “waste” is likely to occur where materials are stagnant.
Break away from “dense situation” using the “Material and Information flowchart”
TPS positions this “material flow” and the “information flow” that directs the manufacturing and transportation of products as very important. Therefore, there is a system to create the “Material and Information flowchart” that represents these two and check whether materials are flowing like a clear stream. This is an important means to realize what is called “Just-in-time” that you make and transport what you need, when you need it, as much as required. However, I would like to add, just in case there is a misunderstanding, that there are some cases that you may need to be aware of the temporary waste and have an inventory depending on the surrounding circumstances. For example, you must have a minimum amount of inventory necessary to handle with frequent traffic jams and special events with a rapid increase of demand.
In response to the COVID-19, it is safer to reduce the number of times you shop at a supermarket, so buying products for the necessary number of days at one time may be another concrete measure to prevent the “Three Cs”. In any case, I hope that the “new lifestyle” will bring back a society that can be “Three Cs” as soon as possible.
TPS Improvement Consultant who wrote this column
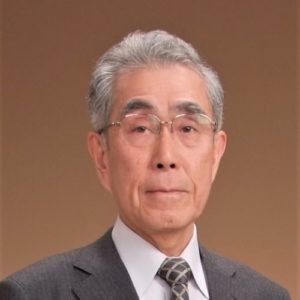
Hiromitsu Hayashida
Former deputy plant manager of Tahara plant, Toyota Motor Corporation
He provides practical guidance of Toyota Production System. He specializes in welding and assembly techniques. He promotes improvement activities for entire plant including Purchasing and Production Control. He has a wealth of experience in guiding for various plants.