How to Improve Care Facilities?
Challenges Faced in the Tenth Year of Operation
Result
・Reorganization of layout
・New service ideas (boosting staff motivation)
When Care Facility A first opened 10 years ago, both its appearance and the content of its services were novel and successful. However, in recent years, the number of months with deficits has gradually become more noticeable.
**Facility’s Capacity to Accommodate**
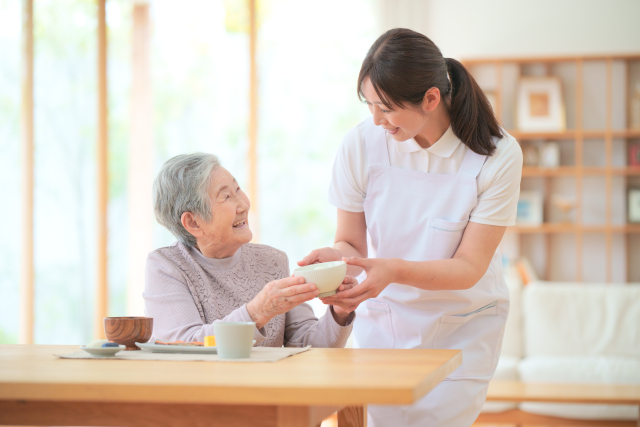
- Industry Details
- Care Services Business
- Country
- Japan
- Company Size
- Fewer than 50 employees
- Challenge
- Achieving profitability
- Objective
- 収益改善生産性 向上コスト削減
- Industry
- その他
Summary
At the time of opening, the facility had a novel appearance and content. However, now, ten years later, there is nothing new, and the building and equipment have deteriorated, with unused items left unattended.
Moreover, the operations have become stagnant, with a lack of awareness in considering new methods or identifying and solving problems
1.Assessment Items
No | Item | Improvement Points |
1 | Target Number of Admissions | The breakeven point is 20 people, but if the admission target is also set at 20 people, the facility will always be operating at the breakeven point. Therefore, it is advisable to set the admission target at 22 people. |
2 | Staff |
<Direct Tasks> 1)Entrance reception 2)Health checks 3)Bathing assistance 4)Toilet assistance 5)Rehabilitation 6)Meal assistance 7)Nap assistance 8)Conversation 9)Handling of health issues <Indirect Tasks> 1)Driving the transport vehicle 2)Tablet data entry 3)Meal distribution 4)Preparation for activities such as coloring 5)Writing in communication notebooks 6)Laundry |
3 | Bathing | Bathing, which needs to be completed in the morning, becomes a bottleneck. All users are bathed in the morning (16 minutes per person), resulting in a significant physical burden on the caregivers. |
4 | Day Room Capacity |
|
5 | Sleeping Capacity |
|
6 | Recreation Capacity |
|
7 | Rehabilitation Capacity |
|
8 | Office |
|
2. Schedule
First, improve the visual impression and enhance the efficiency of caregiving staff’s tasks to lead to better services for the users.
Step 1 Remove unnecessary items from inside and outside (to make layout changes easier)
▼
Step 2 Consider overall layout (reconfigure to include new nap rooms, recreation rooms, and additional services)
▼
Step 3 Improve office and staff operations (rearrange equipment to optimize workflow, reduce unnecessary walking by using carts)
▼
Step 4 Enhance services for users and review marketing methods
3.Conduct interviews with staff
It would be beneficial for staff to share their opinions and propose improvements for each item.**Improvement Sheet Example**
Physically Demanding Tasks for Staff | Improvement Plan |
When transferring users to the bathing wheelchair, it is necessary to support their body, which places a significant burden on the back, waist, and knees. | |
When assisting with dressing and undressing, bending over or staying in a semi-crouched position places a significant burden on the back, waist, and knees. | |
The high temperature and humidity, especially during the summer, are particularly difficult. |
4.Removal of Unnecessary Items, Reorganization of Layout
Based on the premise of having 23 day service users, which is the breakeven point, the capacity of each room is insufficient. (Currently: day service seats are sufficient but cramped, and the recreation room is insufficient.)
Additionally, it appears that the training room was previously open to the community, and now unused items such as treadmills, fitness bikes, and other training equipment are taking up space unnecessarily.
Unnecessary items are scattered both inside and outside the facility, creating an unappealing appearance. The first step is to remove unused items and unnecessary materials to make it easier to reorganize the layout.
To be continued in the next section.
For inquiries about on-site assessments, please contact here
On-site Improvement Specialist

Ito Akihiro
Genba Kaizen Consultant
Akihiro Ito is active on the front line as a shop floor improvement consultant. He has improved a wide variety of large and medium-sized shop floors of over 300 companies in more than 12 countries in Japan and overseas, and has solved the problems of each shop floor every time. Based on his experience working on the production control system, he implements improvement activities in all processes of a factory such as sales, materials, production control, manufacturing, and outsourcing. In addition, he implements the improvement activities together with the people at the shop floor, make the culture of shop floor improvement rooted in the company, and realize quality improvement, productivity improvement and lead time reduction.
Consultants from major companies
with experience in over 40 countries will respond.
Please feel free to contact us.
If you are in a hurry, please call us.
(Japan time)
Except for Saturday, Sunday, holidays, Year-End and New-Year holidays
3 reasons why we are chosen REASON
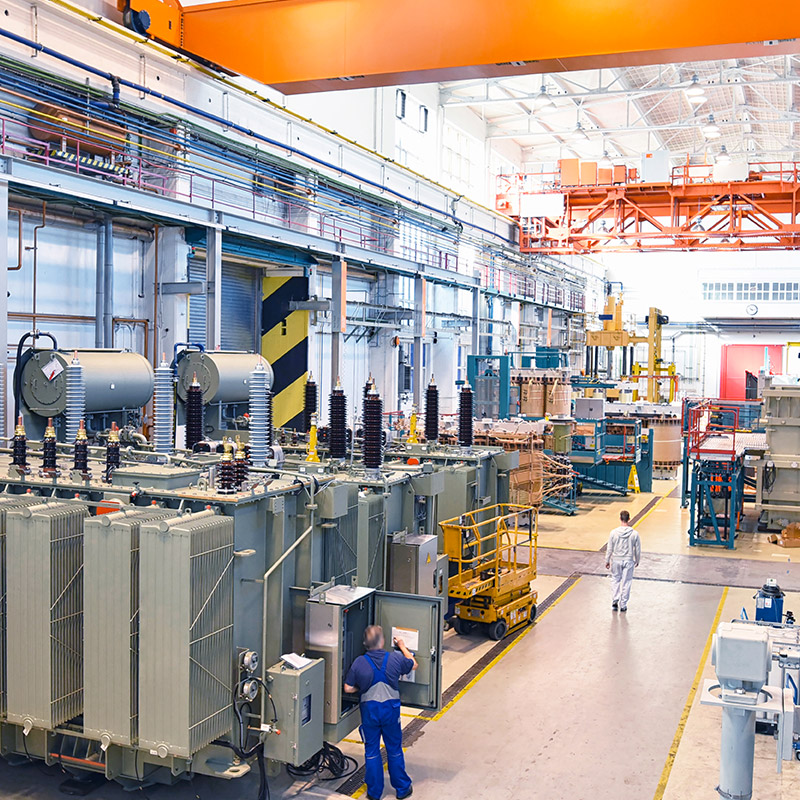
REASON 1
Improvement experience of
more than 1,500 companies in 40 countries
There must be the shop floor issues that cannot be solved by your own company alone. Improvements and reforms for manufacturing industry to survive, regardless of country or industry, need development of your human resources through practical experiences of improvement, and strengthening of your production system base.
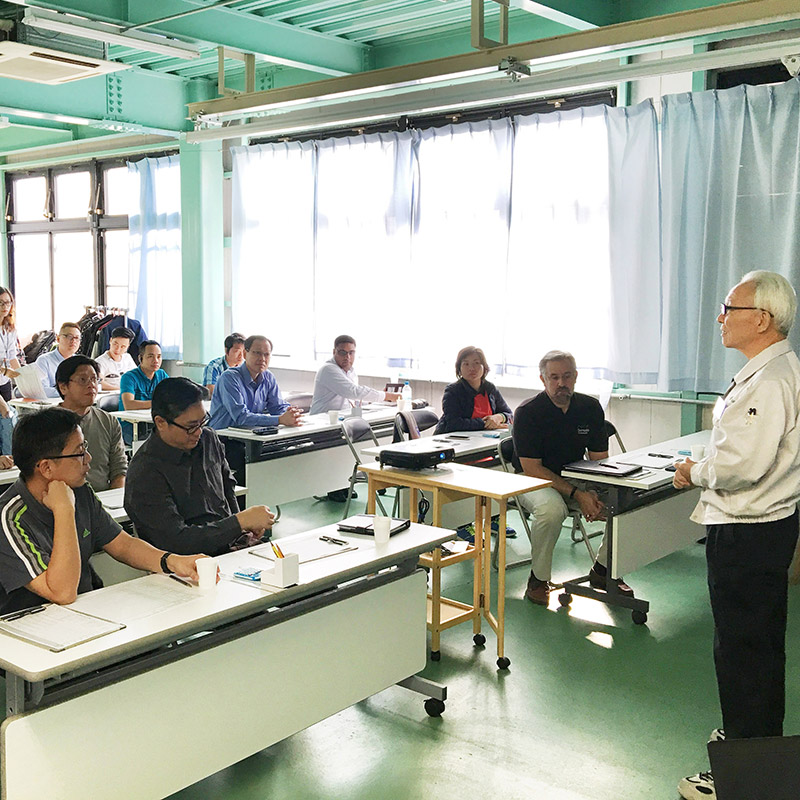
REASON 2
Consulting that shop floor workers
acknowledge our superiority and be pleased
In conventional consulting styles, there was a distance between consultant and the shop floor because it was promoted mainly consultant and management executives. Our consultant can provide a guidance without a distance between consultant and the shop floor through the guidance based on the “seeds of improvement” in a concrete way, instead of “finding fault” like a critic.
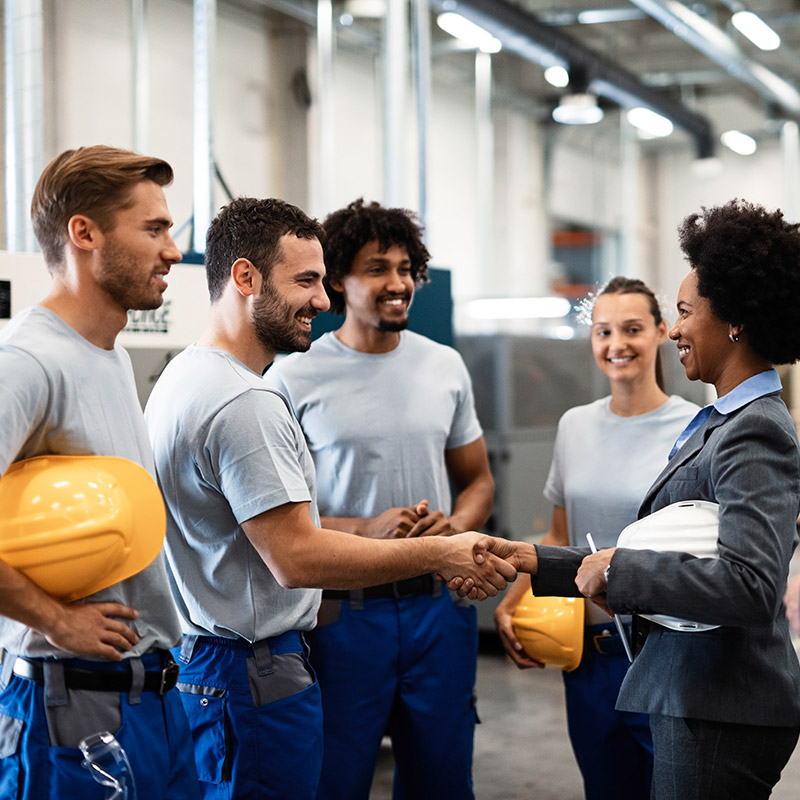
REASON 3
Continuous improvement will continue
even after the end of guidance
While strengthening “human resource development”, we focus on the “overall flow” from design to purchasing, manufacturing, logistics, and production control, and provide guidance that matches the actual situation of your company. Continuous improvement will continue even after the end of guidance through the guidance that is acceptable to the shop floor workers.
Consultants from major companies
with experience in over 40 countries will respond.
Please feel free to contact us.
If you are in a hurry, please call us.
(Japan time)
Except for Saturday, Sunday, holidays, Year-End and New-Year holidays