It needs 10 times in speed compares to the others for KAIZEN activities in food manufacturing factories!!!
Results
Before KAIZEN 10 min. → After KAIZEN 5min.
Features of food manufacturing are such as follows;
・the sell-by date is short
・there are variations in the materials
・production fluctuation is large
As I mentioned as above, the food manufacturing changes status frequently in many factors, so that it is necessary to carry out KAIZEN activities as quickly to make them profitable steadily.
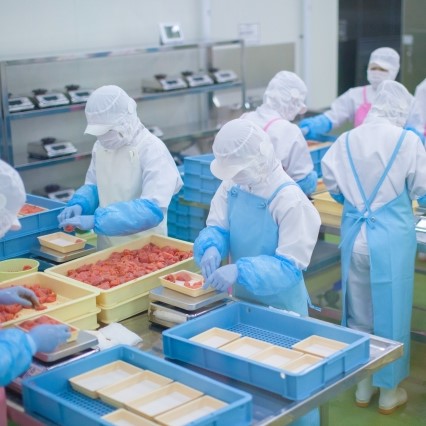
- Details of industry
- Manufacturing ready-to eat food
- Country
- Japan
- Company size
- 200 employees
- Subjects
- Profitability improvement
- Purpose
- Profitability improvement
- Industry
- food
Schedule
Step 1 Analysis of current situations(No Kaizen without analysis of the current situation)Step 2 Safety:Identifying potential dangers for injury (hand operating/machine operation)
Step 3 Measuring times such as operation time, pre-setup time, and setup time
Step 4 Operation KAIZEN
Reduction of walking at the switching
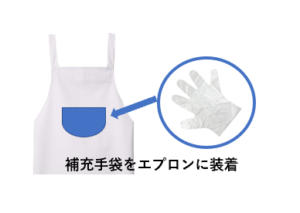
In food manufacturing, the products may be spoiled in seconds.
Therefore, 0 second pre-setup/setup to be challenged.
For example, the gloves are changed every time when the products are altered. Round walking to pick up new gloves to the storage place is waste. The gloves are replenished in the apron, which achieves 0 walking.
Kaizen for the food containers
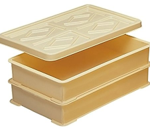
The food containers are designed to be piled up. Therefore, many of food factories use them piling up.
However, most of the times, it causes 12 wastes in the motion of operators and 2 big wastes related to the containers.
<2 Big Wastes>
1)Waste of searching
2)Waste of putting aside
This time, I made the pipe-framed cart that enables to take out the container directly without searching/ putting aside.
<Setup Time Reduction>
Before KAIZEN 10min. → After KAIZEN 5 min.
Tips for “KAIZEN in 10 times of speed”!
0. “Analysis of Operation”
1. Setting the “registration form for problems” at the work site.
2. Having “brainstorming” sessions against indicated problems
3. Extraction of “KAIZEN potentials”
4. Making the “registration form for KAIZEN themes”
5. Implementation of KAIZEN/ Evaluation(Making case study reports of Before/After KAIZEN)
As other thing, the setup KAIZEN cannot be resolved only at the work site.
Kaizen of the system is also necessary. Levelled production and visualization of production plan, 5S and SANTEI (3 fixes) at the work site; all of the above should be put in practice as a whole. Please feel free to contact us for the details.
Food factory improvement specialist
Ricoh Co. – Quality Control Divison
Introduced Toyota Production System in Ricoh after training for five years in Motomachi Plant of Toyota Motor Co.After that, he instructed other industries, such as food and confectionery industry and medical industry etc., on the Toyota Production System. He works on machine productivity improvement, capacity improvement of bottleneck machines, cost reduction of conveyor production system, construction of cell production system (single person system, rotation system, work sharing system, work divide system), construction of production line using carts, establishment of 5S workplace culture, and quality and equipment management.
Consultants from major companies
with experience in over 40 countries will respond.
Please feel free to contact us.
If you are in a hurry, please call us.
(Japan time)
Except for Saturday, Sunday, holidays, Year-End and New-Year holidays
3 reasons why we are chosen REASON
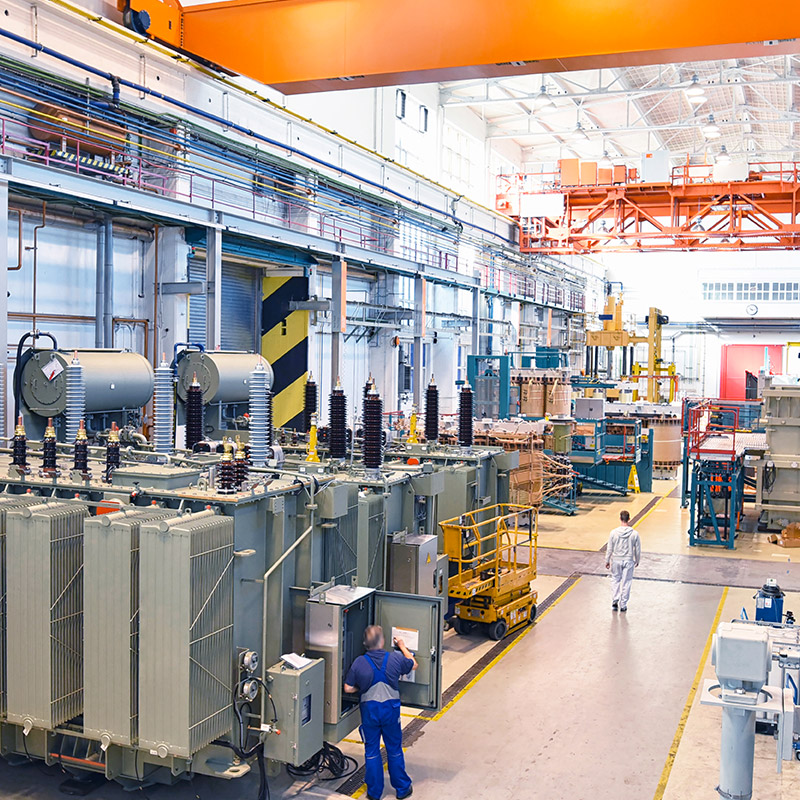
REASON 1
Improvement experience of
more than 1,500 companies in 40 countries
There must be the shop floor issues that cannot be solved by your own company alone. Improvements and reforms for manufacturing industry to survive, regardless of country or industry, need development of your human resources through practical experiences of improvement, and strengthening of your production system base.
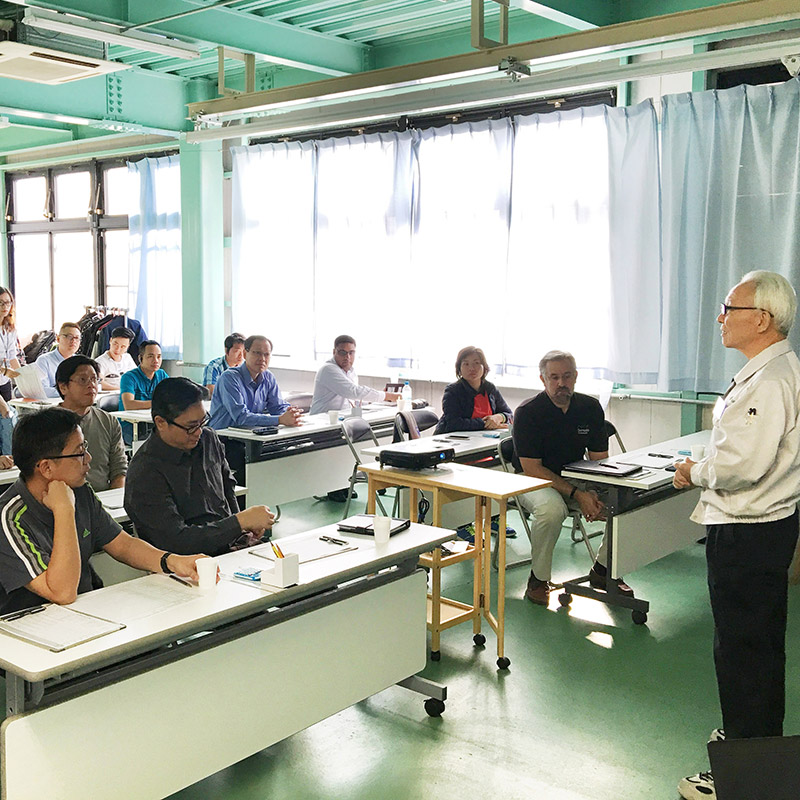
REASON 2
Consulting that shop floor workers
acknowledge our superiority and be pleased
In conventional consulting styles, there was a distance between consultant and the shop floor because it was promoted mainly consultant and management executives. Our consultant can provide a guidance without a distance between consultant and the shop floor through the guidance based on the “seeds of improvement” in a concrete way, instead of “finding fault” like a critic.
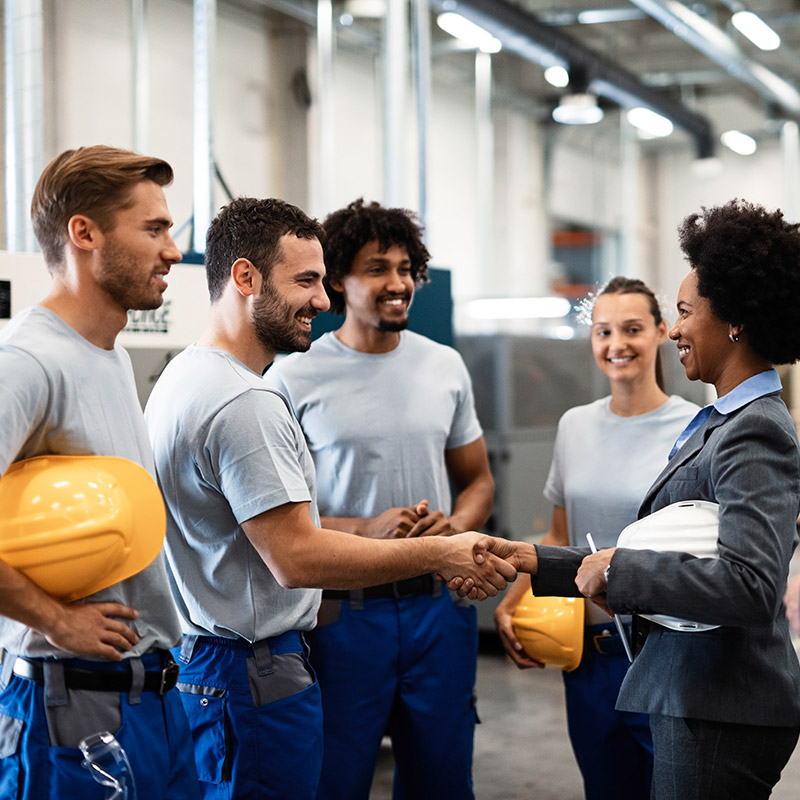
REASON 3
Continuous improvement will continue
even after the end of guidance
While strengthening “human resource development”, we focus on the “overall flow” from design to purchasing, manufacturing, logistics, and production control, and provide guidance that matches the actual situation of your company. Continuous improvement will continue even after the end of guidance through the guidance that is acceptable to the shop floor workers.