Factory diagnosis by our professional consultant
will show you what and how to improve at a glance
Results
- Issues that customers could not see or notice can be identified
- Improvement plan that combines measures for the shop floor improvement and employees' awareness improvement
We received a request for a half-day factory diagnosis from an automobile parts maker, so we implemented a “simple factory diagnosis” and submitted the following report.
Basically we only raise issues since the time is limited, but if it is decided to conduct consulting in the future, we will create a detailed improvement plan.
1. Diagnosis report
1-1. 5S
1-2. Safety
1-3. Quality
1-4. Cost
1-5. Delivery
1-6. Manufacturing
2.Future issues and countermeasures
2-1. Manpower
2-2. Line・Jig
2-3. Materials・Parts
2-4. Operation method
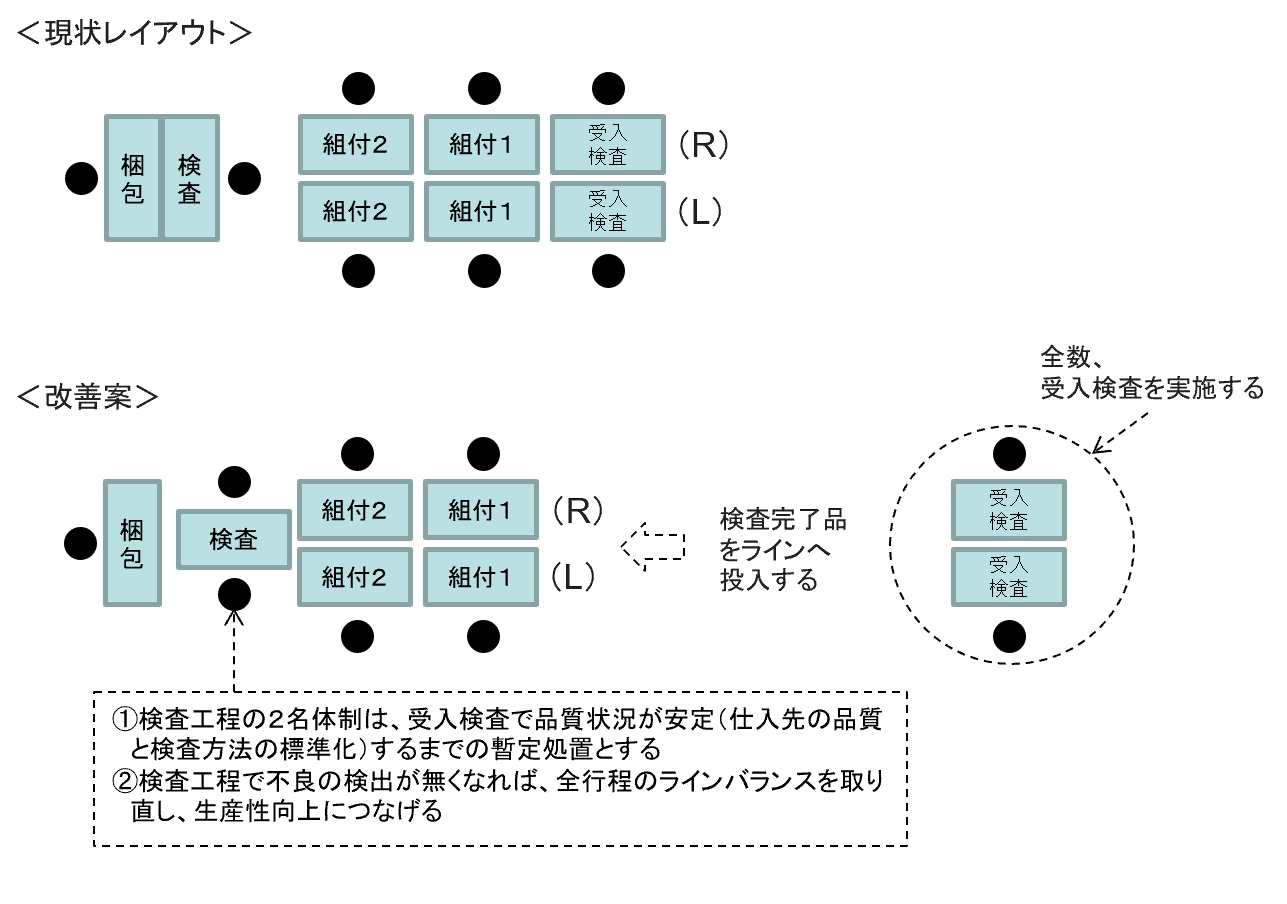
- Industry Details
- Automobile components
- Country
- Japan
- Company Size
- 530 employees
- Issues
-
Productivity improvement
Human resource development - Purpose
- Human resource developmentProfitability improvement
- Industry
- Automobile
1-1. Diagnosis report (5S)
No. | Category | Contents |
1 | Sorting out・Setting in order |
|
2 | Shining・Spic-and Span |
|
3 | Sustaining |
|
1-2. Diagnosis report (Safety)
No. | Category | Contents |
1 | Safe work |
|
1-3. Diagnosis report (Quality)
No. | Category | Contents |
1 | Awareness of defects |
|
2 | Actual status of countermeasures for defects is unclear |
|
3 | Not working hard to prevent outflow of defects to customers |
|
4 | Making countermeasures for early mastery and variation of operator’s skill is manager and supervisor’s work |
|
5 | If managers and supervisors are not in the manufacturing shop floor, it’s impossible to know the reality of workplace |
|
6 | Confusing inspection and sorting |
|
7 | No cooperation between inspection, quality assurance section, and manufacturing shop floor |
|
1-4. Diagnosis report (Cost)
No. | Category | Contents |
1 | Cost awareness |
|
2 | Neglect of waste |
|
1-5. Diagnosis report (Delivery)
No. | Category | Contents |
1 | Keep delivery time |
|
1-6. Diagnosis report (Manufacturing)
No. | Category | Contents |
1 | One set flow |
|
2 | IE technology |
|
1-7.Future issues and countermeasures (Manpower)
No. | Category | Issues | Countermeasures |
1 | Segregation of duties | Employee roles are unclear |
|
2 | Shop floor supervisor (Group leader・Process manager) | There is no supervisor who always stay at the manufacturing shop floor |
|
3 | Line leader | There is no line leader who always stay at the manufacturing shop floor |
|
4 | Shop floor operator | Appropriate test for operation has not been performed |
|
2-2. Future issues and countermeasures (Line・Jig)
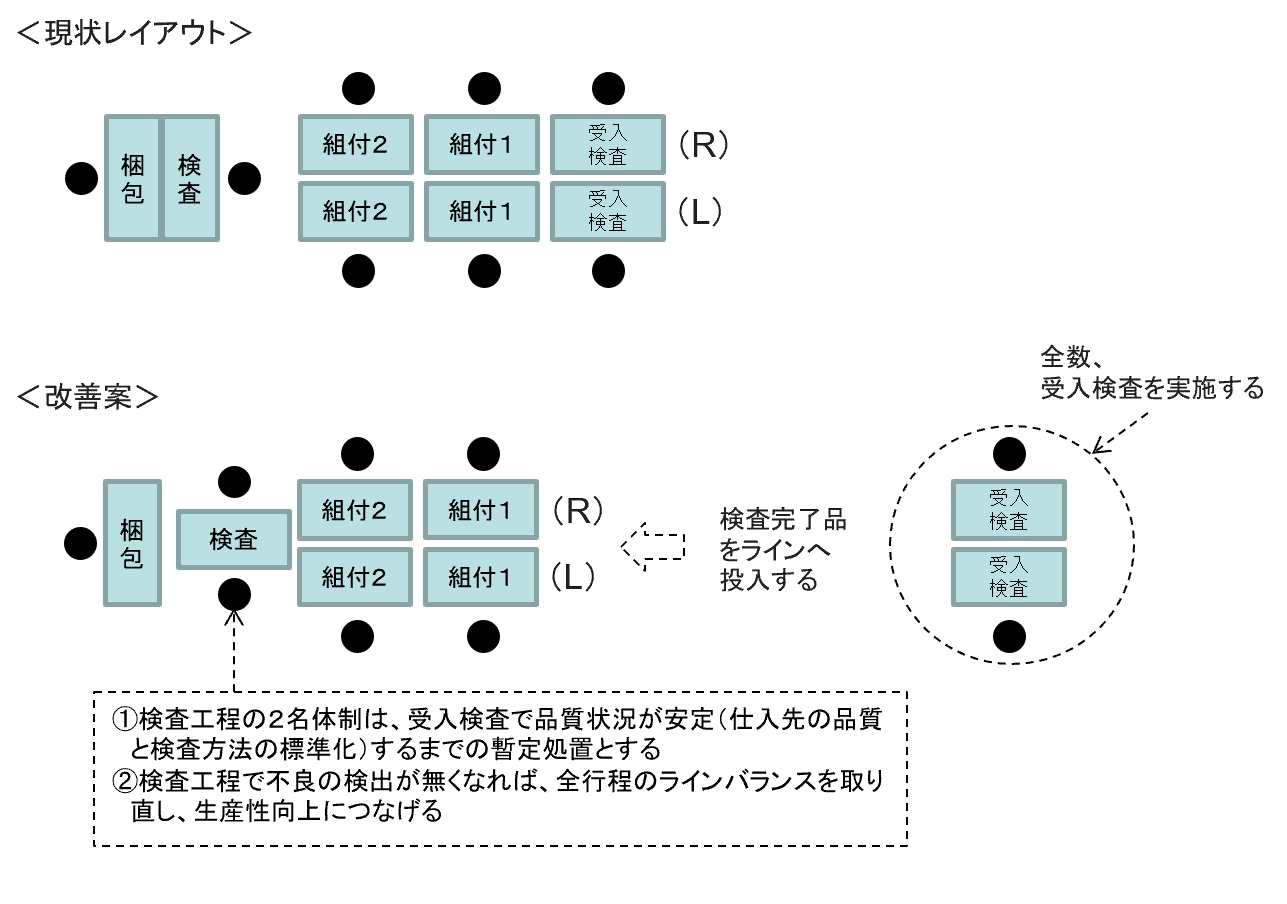
2-3. Future issues and countermeasures (Materials・Parts)
No. | Category | Issues | Countermeasures |
1 | A lot of quality defects | Defective products are delivered from supplier at receiving inspection | |
2 | Air blow of painting | Air blow is operated next to the degreasing process and trash flies |
|
3 | Control of material amount | Depending on the production plan and quality situation of the supplier, the delivery amount of the four materials from supplier, front (left and right) and rear (left and right), is not unified, so sometimes the inventory amount of the four materials is insufficient. |
|
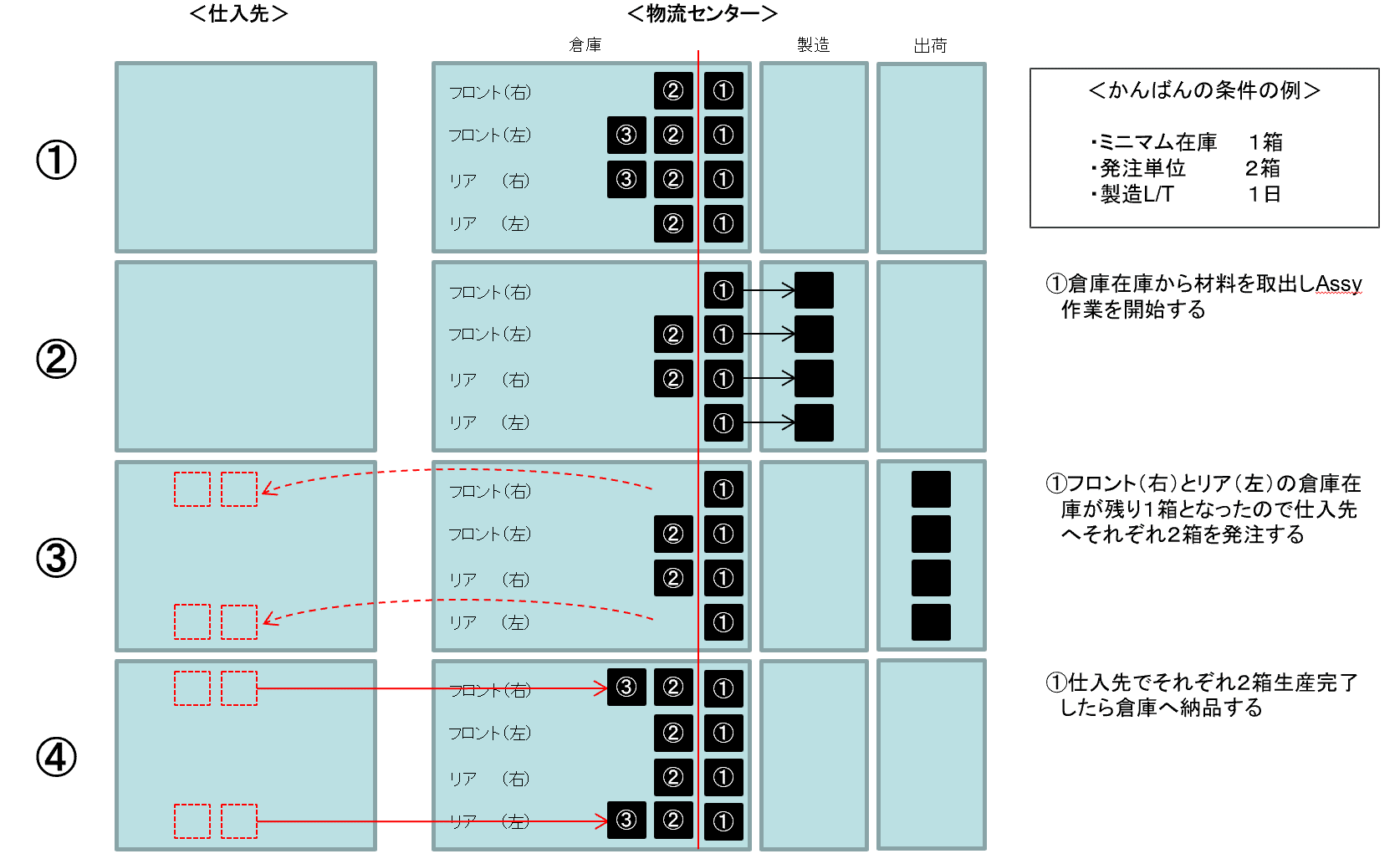
2-4. Future issues and countermeasures (Operation method)
No. | Category | Issues | Countermeasures |
1 | Illuminance management | Light illuminance and direction vary depending on the process | Unify the light environment
|
2 | Waiting | If there is a defective material, cycle time fluctuates and operators cannot work with the rhythm. This leads to a decreased concentration of workers, and make it difficult to ensure quality. |
|
3 | When a defect is found | When a defect is found, everything is left to operators since there are no unified rules. |
|
4 | Finger pointing and calling | Self-check is not performed at the end of work |
|
5 | Through standardized work | Work procedures are different by each operator |
|
Factory diagnostic specialist

Genba Kaizen Consultant
Akihiro Ito is active on the front line as a shop floor improvement consultant. He has improved a wide variety of large and medium-sized shop floors of over 300 companies in more than 12 countries in Japan and overseas, and has solved the problems of each shop floor every time. Based on his experience working on the production control system, he implements improvement activities in all processes of a factory such as sales, materials, production control, manufacturing, and outsourcing. In addition, he implements the improvement activities together with the people at the shop floor, make the culture of shop floor improvement rooted in the company, and realize quality improvement, productivity improvement and lead time reduction.
Consultants from major companies
with experience in over 40 countries will respond.
Please feel free to contact us.
If you are in a hurry, please call us.
(Japan time)
Except for Saturday, Sunday, holidays, Year-End and New-Year holidays
3 reasons why we are chosen REASON
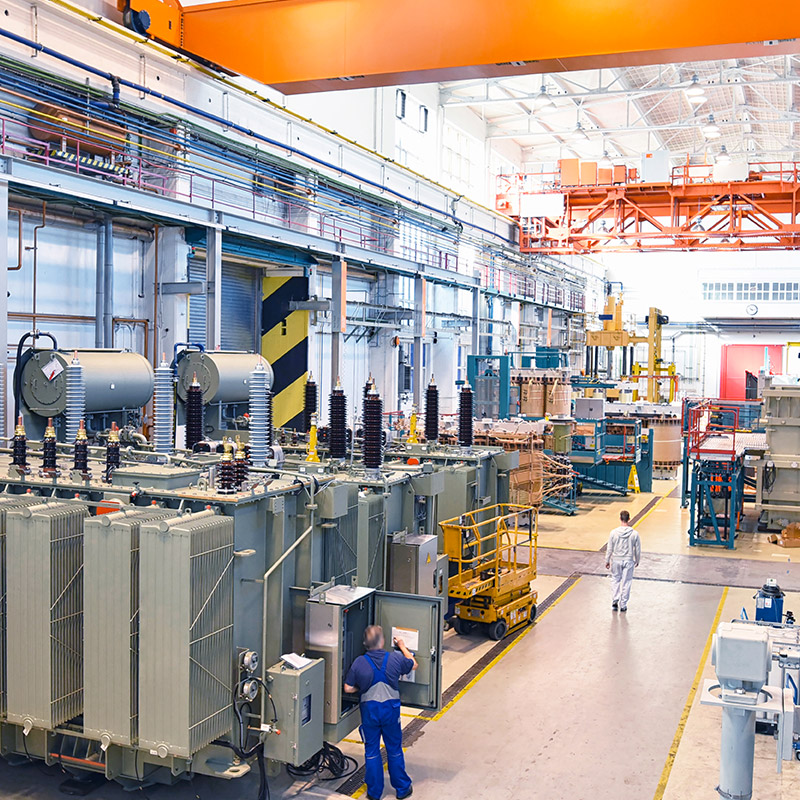
REASON 1
Improvement experience of
more than 1,500 companies in 40 countries
There must be the shop floor issues that cannot be solved by your own company alone. Improvements and reforms for manufacturing industry to survive, regardless of country or industry, need development of your human resources through practical experiences of improvement, and strengthening of your production system base.
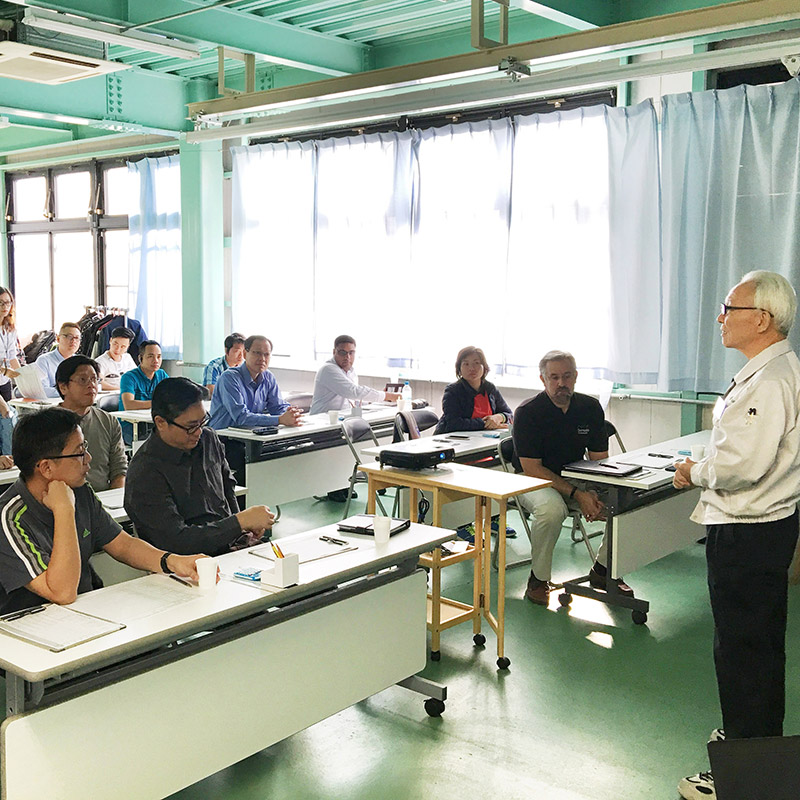
REASON 2
Consulting that shop floor workers
acknowledge our superiority and be pleased
In conventional consulting styles, there was a distance between consultant and the shop floor because it was promoted mainly consultant and management executives. Our consultant can provide a guidance without a distance between consultant and the shop floor through the guidance based on the “seeds of improvement” in a concrete way, instead of “finding fault” like a critic.
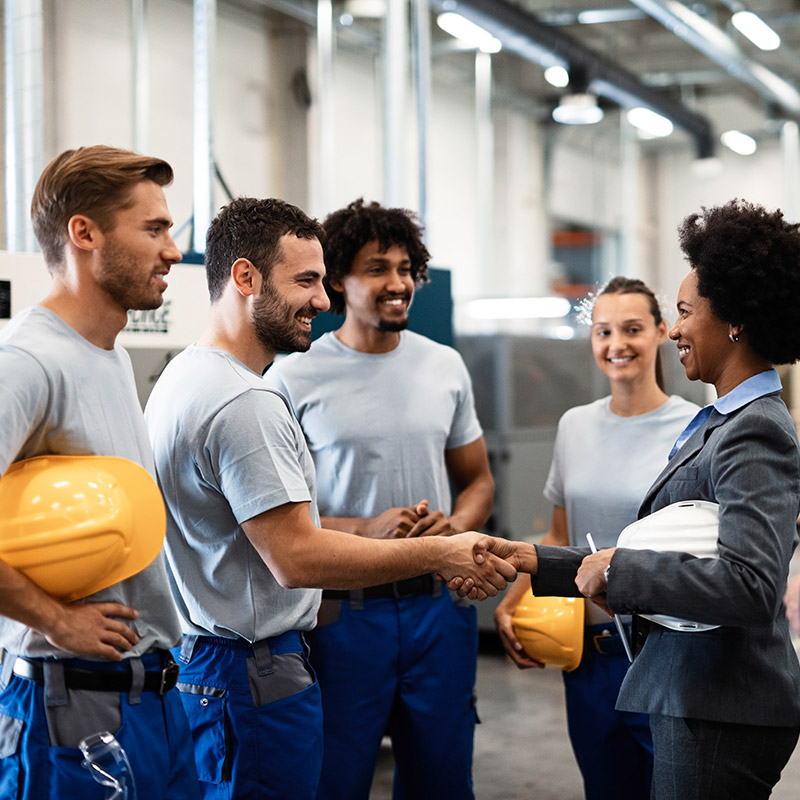
REASON 3
Continuous improvement will continue
even after the end of guidance
While strengthening “human resource development”, we focus on the “overall flow” from design to purchasing, manufacturing, logistics, and production control, and provide guidance that matches the actual situation of your company. Continuous improvement will continue even after the end of guidance through the guidance that is acceptable to the shop floor workers.