工場の生産性向上とは、最小限の投資で最大限の付加価値を生み出すことです。
つまり、より少ない原価(人材、材料、設備、時間など)で、より大きな利益を出せることは、生産性が高いといえます。
工場の生産性向上で
こんな課題を解決
ISSUE
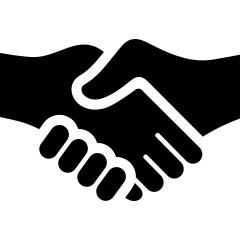
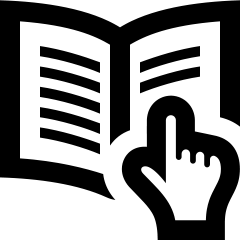
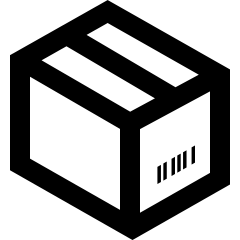
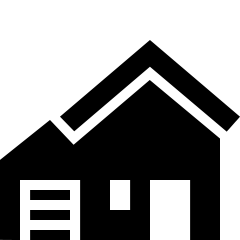
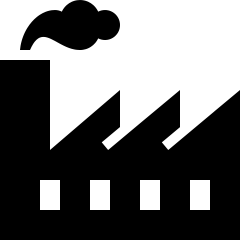
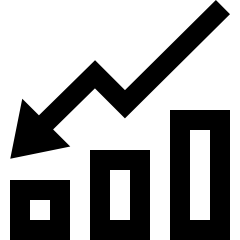
生産性向上のための
3つのポイント
FEATURES
-
1
徹底したムダの排除
-
情報とモノの流れから、ムダ(顧客にとって価値のない行動)を徹底的に排除。
-
2
Iotの活用
-
モノと情報の流れが正常になった環境で、ITによってQ(品質向上)C(コスト削減)D(納期対応力)を向上させます。
-
3
不良再発防止策の徹底
-
問題が起きたら、リアルタイムで原因を究明し、再発防止策を徹底します。
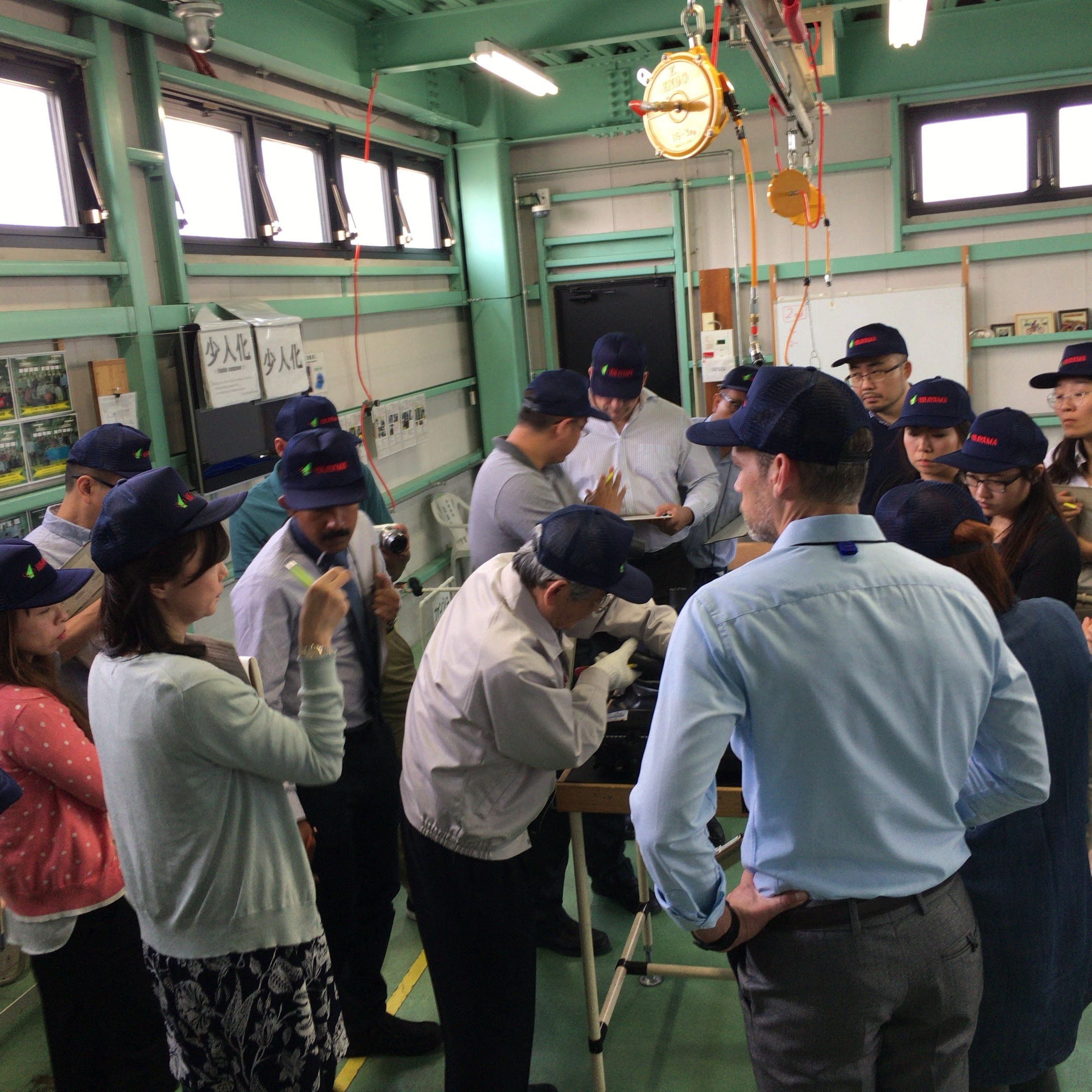
徹底したムダの排除
5Sの推進と共に、作業中のムダ(手待ち、歩行、取り置き、運搬)を排除します。現れ出るのムダを取り除き、タイトな人員配置で作業の再割付を実施し、再配置計画に合わせた多能工化を推進します。
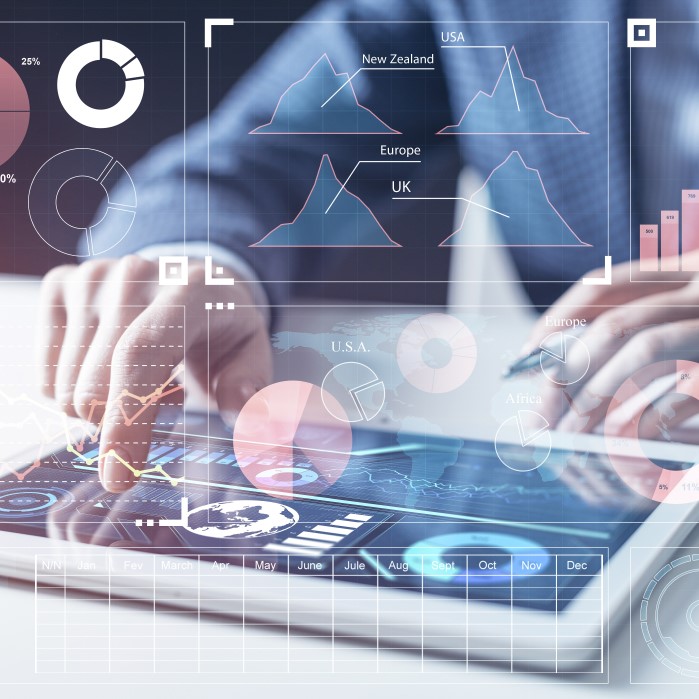
Iotの活用
課題が多く残っている現場にIotを導入すれば、課題が解決されるわけではありません。
モノと情報の流れを整流化、ムダを取り除きモノづくりのあるべき姿に改善してからシステムを導入することで、ITを利用して現場の課題を解決することができます。
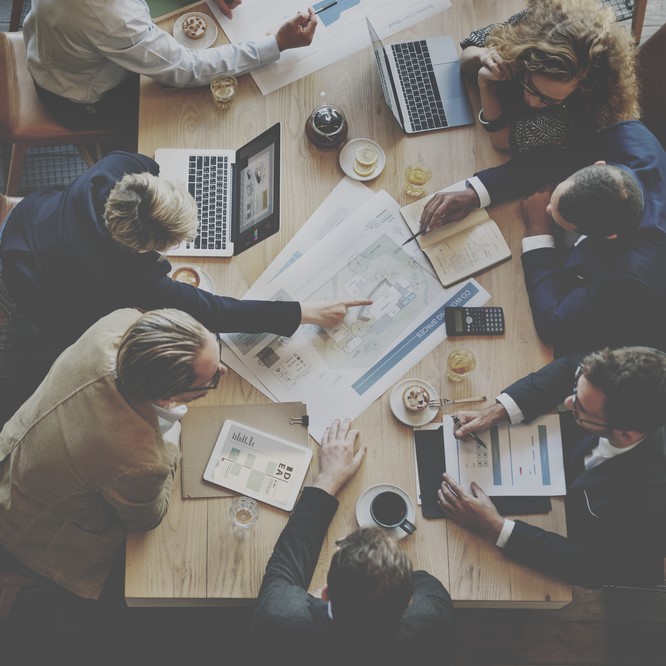
不良再発防止策の徹底
問題発生時に、表面的な原因しか捉えずにいると、表面的な問題の解決しか出来ません。そこで、発生した問題の真因までたどり着くために「なぜなぜ分析」を行います。1つの問題に対して「なぜ?」とその問題を引き起こした要因を探し、更に「なぜ?」とその要因を引き起こした要因を探していきます。何回かこれを繰り返していくと、問題の真因が分かり、根本的な対策を立てることができます。
生産性向上のスペシャリスト

伊藤 彰洋(いとう あきひろ)
現場改善コンサルタント
業種を問わず、現場改善の文化を企業へ根付かせ、現場の人間と共に改善活動をおこない、品質向上・生産性向上・リードタイム短縮を実現する。
また、生産管理システムを手掛けた経験により、「営業~資材~生産管理~製造~外注」と工場内のあらゆるプロセスにおいて改善活動を実践する。
生産性向上の事例 RESULTS
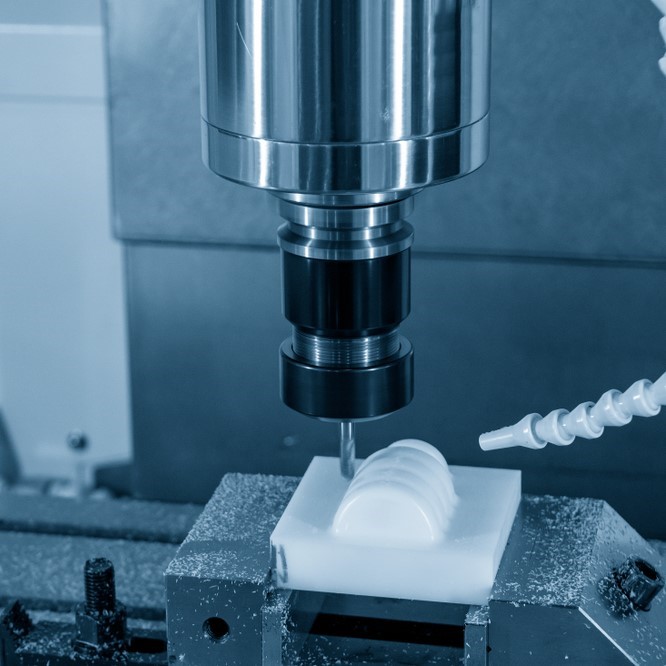
海外赤字工場を黒字化へ
品質向上で新規取引先2件獲得!
工場の至るところにあった仕掛品・不良品在庫はほとんどなくなり、人員を省人化したが、毎月あった顧客クレームはほとんどなくなりました。(自動車業界/工場長)
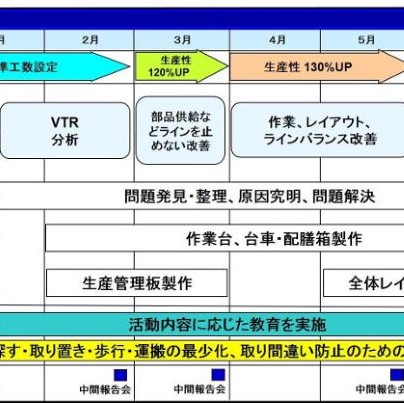
生産性 169.6% UP
ベトナム日系工場における改善
自力での改善活動に限界を感じコンサルティングを依頼。人材が育ち、今まで自分たちでは解決できなかった高いレベルの改善ができるようになりました。(自動車業界/工場長)
選ばれる3つの理由 REASON
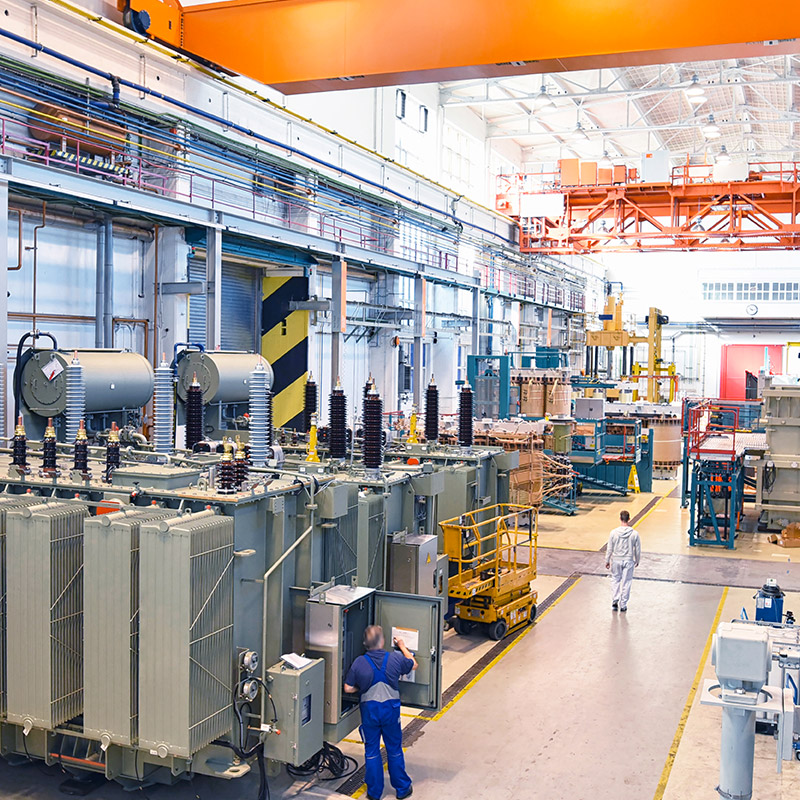
REASON 1
40ヶ国、
1,500社以上の改善実績
自社だけでは解決できない現場の問題は必ずあります。製造業が勝ち残るための改善・改革は、国や業界を問わず、改善の実践体験を通じて、人材を育成し、生産体制基盤を強化することが必要です。
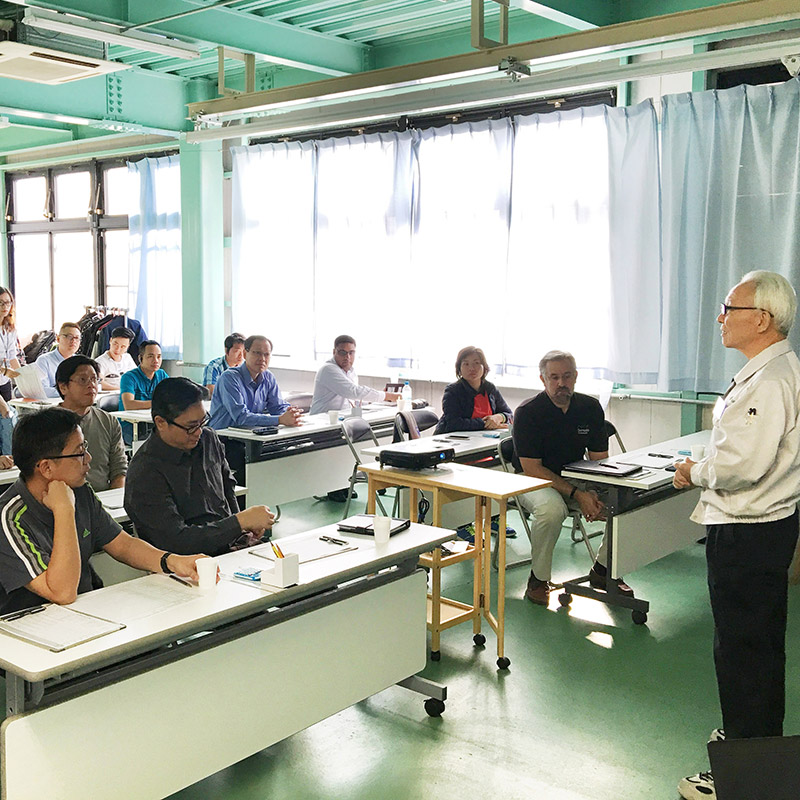
REASON 2
現場が一目置き、
喜ぶコンサルティング
従来のコンサルティングでは、経営層とコンサルタントが中心になってすすめるため、現場とコンサルタントの間に距離がありました。弊社コンサルタントは、評論家的な「あら探し」ではなく「改善の種」を具体的に見出す指導により、現場の人間との隔たりのない指導をすることができます。
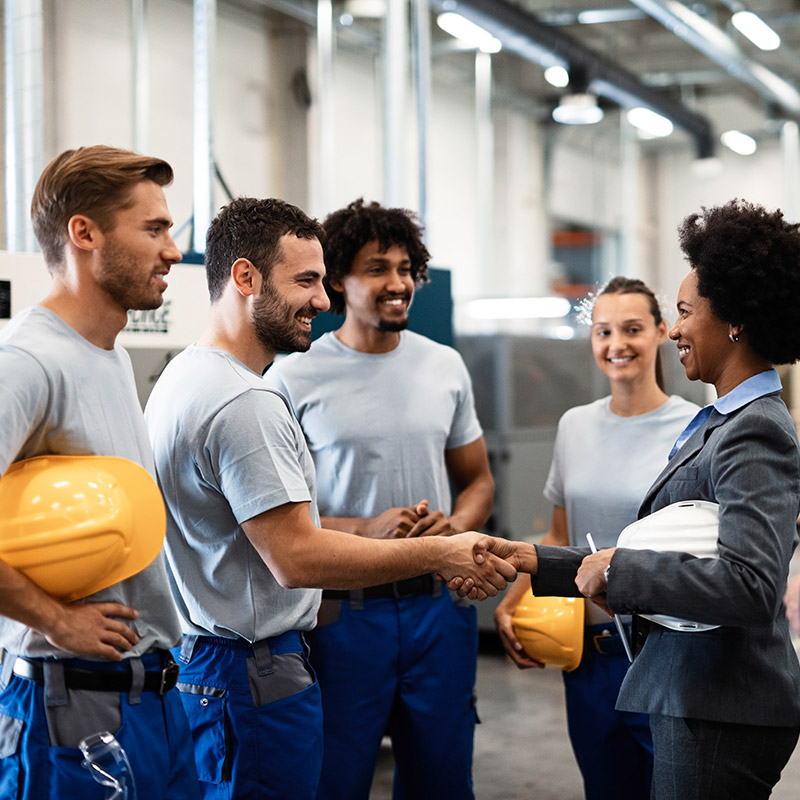
REASON 3
指導終了後も
継続的改善がされる
「人づくり」を強化しながら、設計から調達・製造・物流、そして生産管理と「全体の流れ」を重視し、貴社の現場の実態に合った指導を実施。現場が納得できるコンサルティング指導を行うことで、指導終了後も改善文化が継続されます。