Target is to reduce manufacturing costs by 30% within one year.
We introduced Toyota Production System and thoroughly eliminated waste by visualization.
Result
- Lead time reduction: 40%
- Necessary manpower for assembly: 16 operators → 6 operators
- Space: 200㎡ → 110㎡
We introduce the improvement example of an electrical device manufacturer, Company A, that introduced the Toyota Production System in order to achieve the goal of reducing manufacturing costs by 30% within one year.
Issues before improvement
- Profitability declined and financial situation worsened due to price competition and expansion of personnel and material costs year by year.
- The production volume fluctuated greatly, but the corresponding improvements and labor saving were not be promoted.
- Customers requested production with short delivery time, but they were not able to meet it.
- There were many work-in-process between the processes.
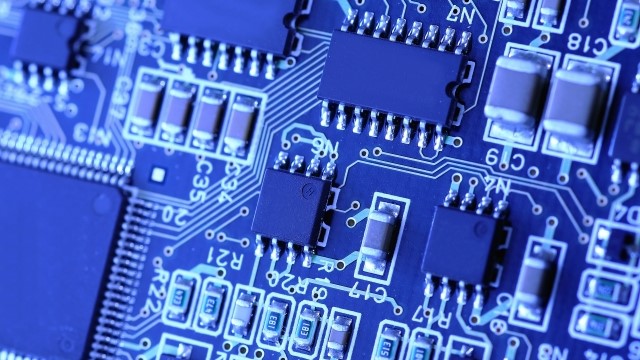
- Industry details
- Electronics
- Country
- Japan
- Company size
- About 380 employees
- Purpose
- Profitability improvement
- Industry
- Electrical and electronic
Streamline “Material and information flow”
This shop floor had a bad layout, for example, each process was a small isolated island, and there were many work-in-process inventories between the processes. So there was no flow in the shop floor and it was a treasure house of waste.
Therefore, in order to eliminate these wastes, they started to streamline the processes, and the challenge of “one-piece flow production” started. There was a lot of refusal reaction from the members of the shop floor that “it was not efficient to make one by one”, but the improvement activities in parallel with the practical training deepened the understanding of all the people involved, and an atmosphere was created that “The one-piece flow production is the form of a line that clarifies waste. Let’s try the one-piece flow production and thoroughly eliminate waste.”
As a result, the lead time was reduced by about 40% with minimal transportation and stagnation, line construction in space, and operation improvement. Furthermore, by shifting from the lot production to the one-piece flow production, 1,000 or more work-in-process boxes became unnecessary.
Clarify waste by the one-piece flow production
Many people think that if they implement the one-piece flow production, the efficiency will increase, but that is wrong. Efficiency will increase by thoroughly eliminating wastes clarified by carrying out the one-piece flow production. This idea of clarifying such waste (making it easy to find waste) is the “visualization” of the Toyota Production System.
Investigate and improve the causes of material stagnation
Examples of the causes |
|
Gemba Kaizen specialist

ITO, Akihiro
Process improvement consultant
He worked for JIT Institute, Tokyo for 20 years.( JIT: Just In Time). During this period, he has learned Just In Time philosophy and method of improvement of productivity in manufacturing plant. Continuously he has been engaged in effective introduction process of Production Management System to small and medium enterprise and even big enterprise.
Consultants from major companies
with experience in over 40 countries will respond.
Please feel free to contact us.
If you are in a hurry, please call us.
(Japan time)
Except for Saturday, Sunday, holidays, Year-End and New-Year holidays
3 reasons why we are chosen REASON
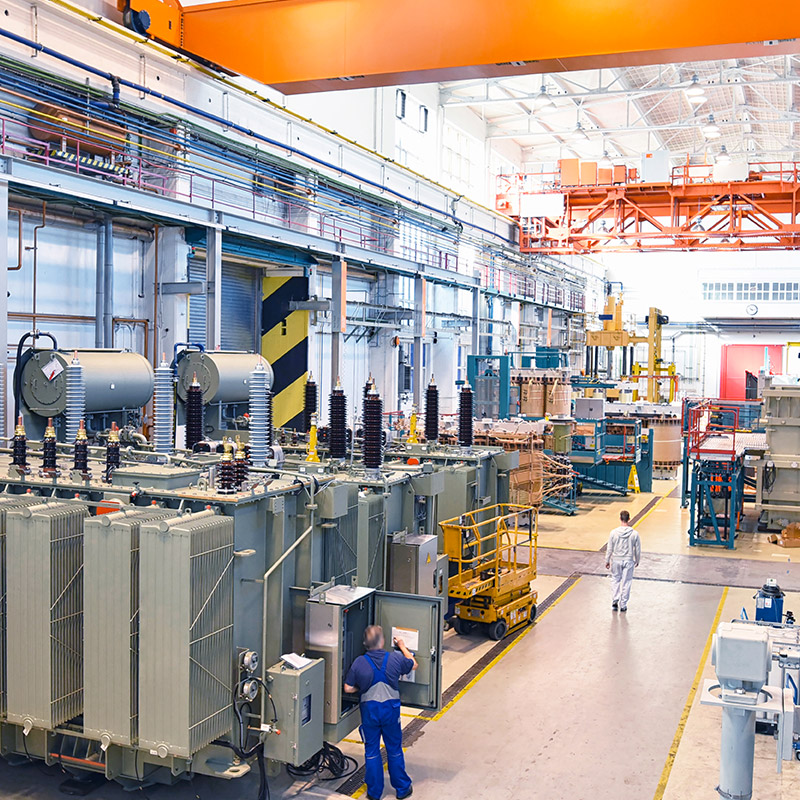
REASON 1
Improvement experience of
more than 1,500 companies in 40 countries
There must be the shop floor issues that cannot be solved by your own company alone. Improvements and reforms for manufacturing industry to survive, regardless of country or industry, need development of your human resources through practical experiences of improvement, and strengthening of your production system base.
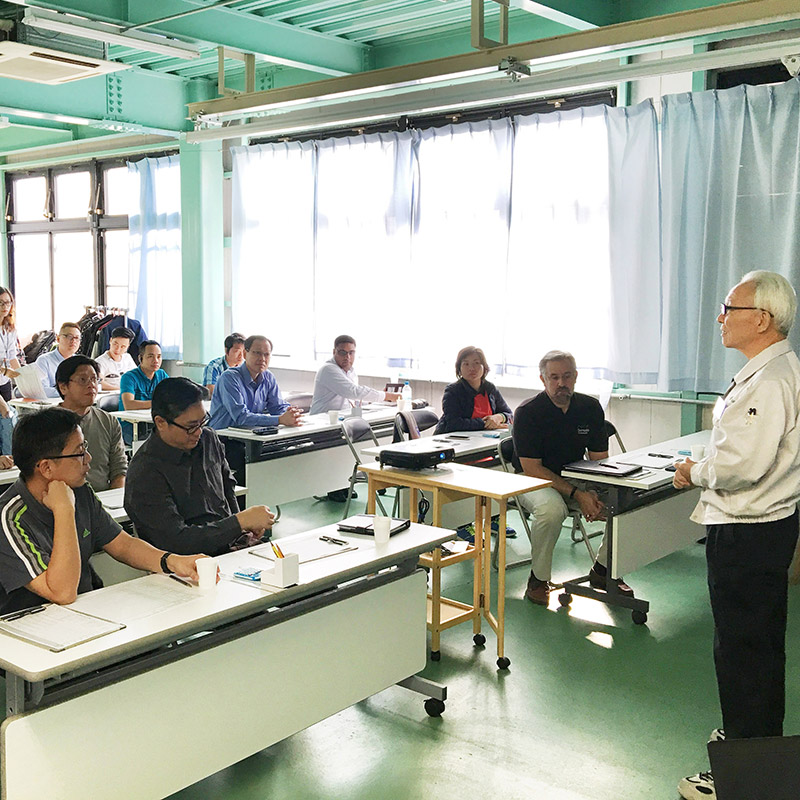
REASON 2
Consulting that shop floor workers
acknowledge our superiority and be pleased
In conventional consulting styles, there was a distance between consultant and the shop floor because it was promoted mainly consultant and management executives. Our consultant can provide a guidance without a distance between consultant and the shop floor through the guidance based on the “seeds of improvement” in a concrete way, instead of “finding fault” like a critic.
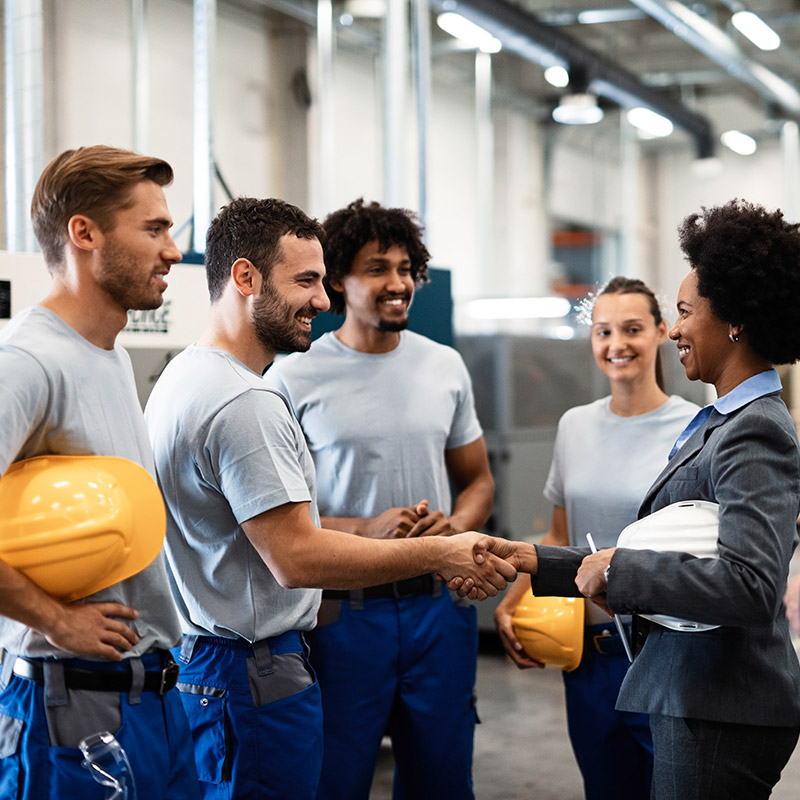
REASON 3
Continuous improvement will continue
even after the end of guidance
While strengthening “human resource development”, we focus on the “overall flow” from design to purchasing, manufacturing, logistics, and production control, and provide guidance that matches the actual situation of your company. Continuous improvement will continue even after the end of guidance through the guidance that is acceptable to the shop floor workers.
Consultants from major companies
with experience in over 40 countries will respond.
Please feel free to contact us.
If you are in a hurry, please call us.
(Japan time)
Except for Saturday, Sunday, holidays, Year-End and New-Year holidays