A reform on which the company’s fate depends
A four-year project
Result
Defect rate: Less than 0.1%
Lead time 16-hour reduction
On-time delivery rate of 98%
To survive against foreign products, it was necessary to reduce costs and shift towards a system capable of handling a wide variety of products in small quantities.
The field resists change, but over the course of about a year, worker education (awareness reform) was conducted, and the reform was implemented. The number of improvements per person ranged from 5 to 15 items per month.
During the four-year project, more than 40,000 improvements were made, achieving targets in productivity, defect rate, on-time delivery rate, and lead time for each item.
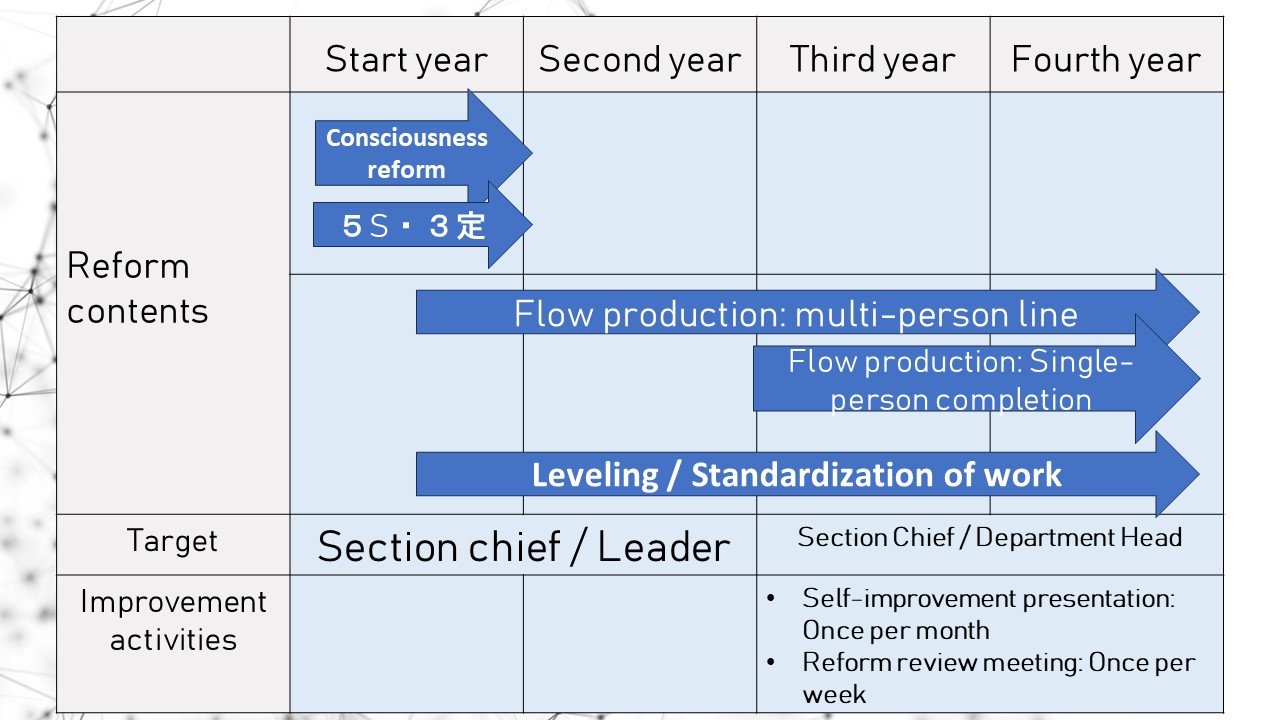
- Industry Details
- Precision Machinery
- Country
- Japan
- Company Size
- Employees: 100 to 200
- Challenge
- High-mix, low-volume production
- Objective
- Profitability improvement
- Industry
- Electrical and electronic
The background of the reform
Industry trends |
|
Current situation |
|
Issues |
|