IoT kaizen improvement!!
Applicable to worksites that use circular meters
Results
・Abnormal condition is reported in real time on smartphone. So, quick action is possible.
●Company A in the food industry raised as a target for this fiscal year that the company will improve its productivity by using IoT as a method to achieve productivity enhancement through cost reduction without degrading the quality in the harsh external environment such as chronic manpower shortage and rising raw material costs.
What the company focused on was the monitoring of pressure gauge meters by man and recording of manual operations.
Post-improvement goals
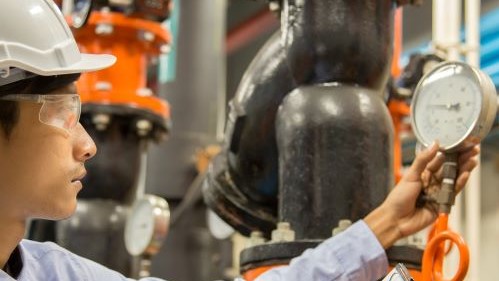
- Industry details
- Precooked foods etc.
- Country
- Japan
- Company size
- No. of employees: Approximately 260
- Issue
- Productivity enhancement
- Objective
- Quality improvementProfitability improvement
- Industry
- food
IIoT improvement schedule
Step 1 Lecture: Easy IoT for factoriesStep 2 Status search (factory diagnosis)
Step 3 Determination of processes targeted for improvement
Step 4 Identification of important facilities and places to install IoT sensors
Step 5 Demonstration experiment (free service available)
Step 6 Introduction
Issue: Willing to discontinue manual operations such as visual meter reading and recording!!
Investigation revealed that 15 hours/month is taken for monitoring and recording of approximately 20 pressure gauge meters and much time is also taken for cause investigation in the event of abnormal conditions.
Pressure gauge meters are so fragile that visual inspection was conducted twice a day.
Improvement measures
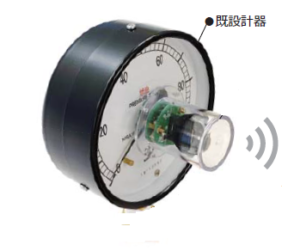
– Increase improvements by adding the help of IT to the conventional manual job improvements.
– Develop a mechanism to surely reduce costs by accumulating the experience and know-how of job improvements little by little that can be conducted by even IoT beginners in the factory.
We investigated several types of reading sensors for various off-the-shelf circular meters as well as those recommended by our consultants and went through the process of validating them among our improvement team members.
The leading camera meter reading method in the market takes much time for various preparations such as the location adjustment of camera setting places and lighting dark worksites. We therefore looked for other methods.
We validated an IoT sensor unit that can be used just by being attached on the surface (outside) of a meter. It can be used not exclusively for a pressure gauge but for every circular meter. Being a magnetic reader, it can solve the demerits of a camera.
Improvement effects
Cost reduction/td> | The IoT sensor avoids the waste of engaging employees in periodical reading. |
Quality assurance | The IoT sensor prevents transcription errors caused by manual operations. Given the increase of foreign workers, we will aim at quality assurance that does not depend on personal skills. |
Response expedition | The real-time monitoring of meter readings can expedite emergency response. |
Statistical analysis | |
Summary: Circular meter reading device
The circular meter reading device has enabled automatic meter monitoring and automatic recording, so that we will take an action only when an abnormality alarm is generated. Thus, we can take an immediate action in the event of an abnormal condition.
This improvement case can be applied to worksites that use not only pressure gauge meters but also any circular analog meters.
The circular meter reading device is so simple that it can be used just by being attached to the outside of an existing meter and easy to be handled by even an IoT beginner, and thus will surely reduce cost reduction.
Intensive Kaizen Specialist

ITO, Akihiro Akihiro Ito
Process improvement consultant
He worked for JIT Institute, Tokyo for 20 years.( JIT: Just In Time). During this period, he has learned Just In Time philosophy and method of improvement of productivity in manufacturing plant.
Continuously he has been engaged in effective introduction process of Production Management System to small and medium enterprise and even big enterprise.
Consultants from major companies
with experience in over 40 countries will respond.
Please feel free to contact us.
If you are in a hurry, please call us.
(Japan time)
Except for Saturday, Sunday, holidays, Year-End and New-Year holidays
3 reasons why we are chosen REASON
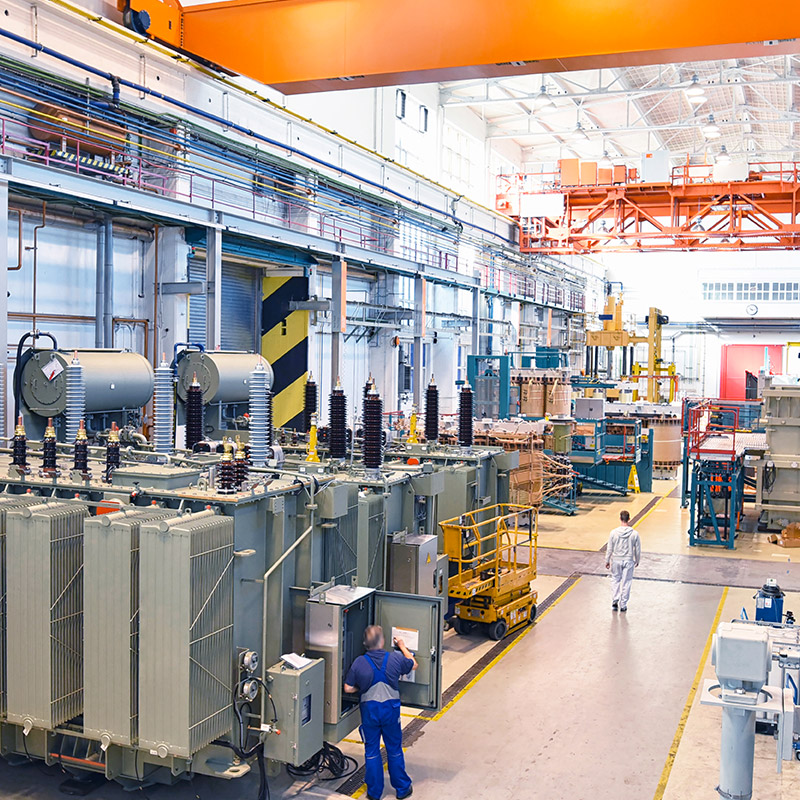
REASON 1
Improvement experience of
more than 1,500 companies in 40 countries
There must be the shop floor issues that cannot be solved by your own company alone. Improvements and reforms for manufacturing industry to survive, regardless of country or industry, need development of your human resources through practical experiences of improvement, and strengthening of your production system base.
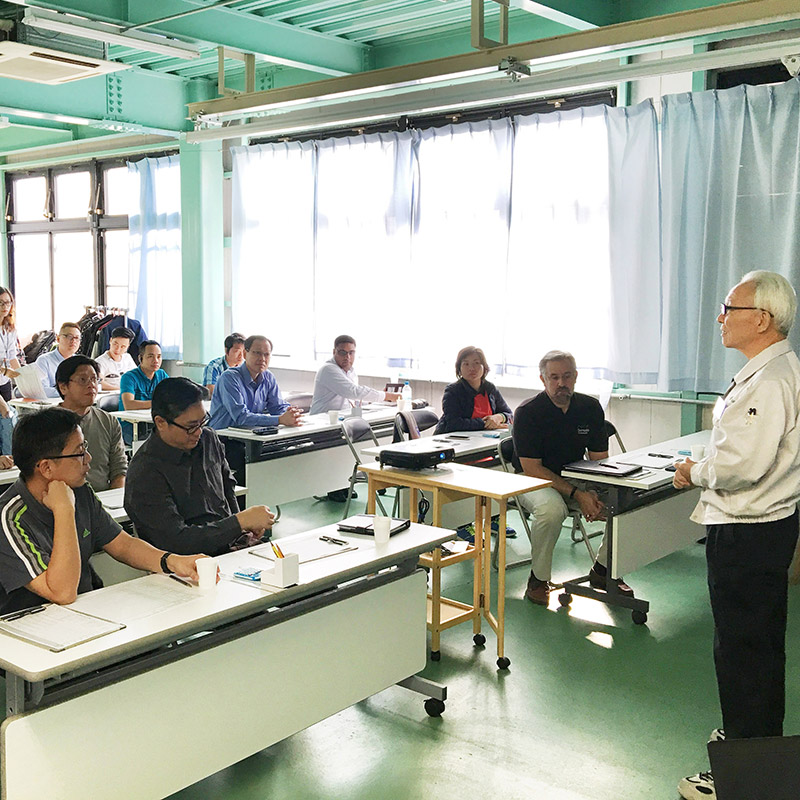
REASON 2
Consulting that shop floor workers
acknowledge our superiority and be pleased
In conventional consulting styles, there was a distance between consultant and the shop floor because it was promoted mainly consultant and management executives. Our consultant can provide a guidance without a distance between consultant and the shop floor through the guidance based on the “seeds of improvement” in a concrete way, instead of “finding fault” like a critic.
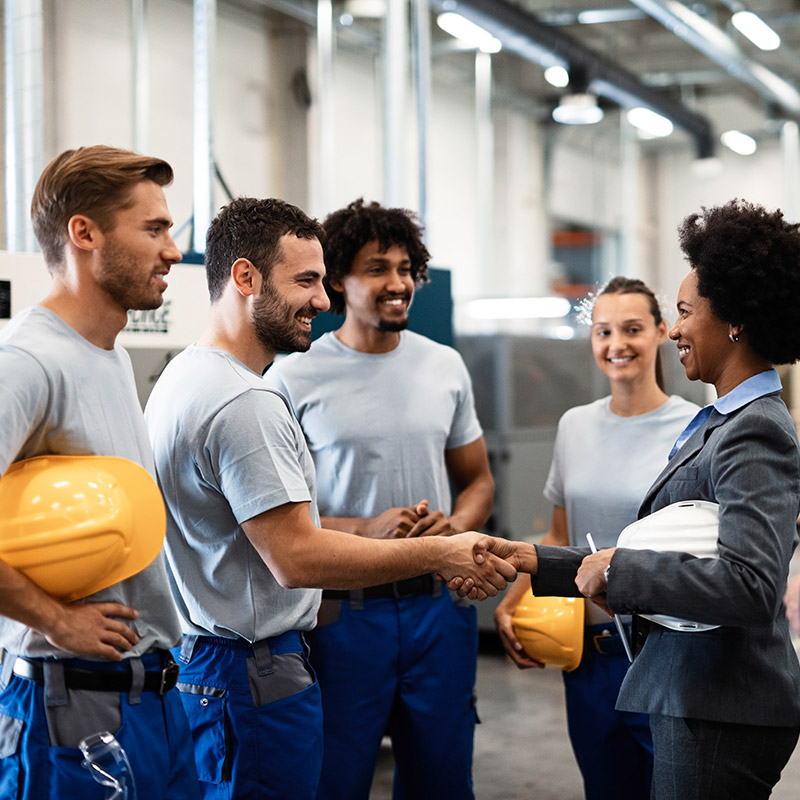
REASON 3
Continuous improvement will continue
even after the end of guidance
While strengthening “human resource development”, we focus on the “overall flow” from design to purchasing, manufacturing, logistics, and production control, and provide guidance that matches the actual situation of your company. Continuous improvement will continue even after the end of guidance through the guidance that is acceptable to the shop floor workers.