Able to Envision the Ideal State
This is the shortcut to improvement
Results
Productivity Increase by 62%
When visiting the site of Company B in Southeast Asia, I observed numerous inefficiencies. The essence of improvement activities lies in eliminating waste. Any work within the operation that does not add value is considered wasteful.
Improvement cannot occur without everyone recognizing what constitutes waste. At the kickoff for improvement activities, to enable envisioning the ideal state of the workplace, everyone from the plant manager to all management and working staff learned about various forms of waste.
~various wastes~
waste of transportation waste of inventory waste of movement
waste of equipment waste of defects waste of layout
organizational waste waste of waiting waste of management
waste of inspection Waste of work itself・・・・
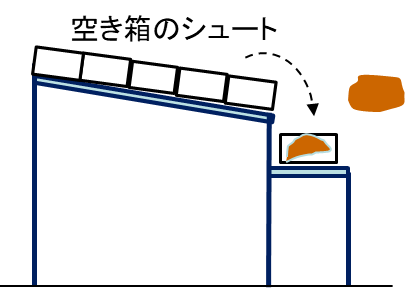
- Industry Details
- Meat processing
- Country
- Japan
- Company size
- 100 employees
- Assignment
- Increase Profit Margin, Reduce Accidents to Zero
- Purpose
- Profitability improvement
- Industry
- food
Schedule
- On-site diagnosis
- Training
- Implementation of improvements
Improvement Case Study
Transporting empty boxes and boxes containing meat |
![]() |
Improvement points
Empty boxes are inserted into the chute. |
![]() |