Successful experience of high-level improvement activities fosters human resources and creates a strong workplace
result
- Productivity Up to 169.6% by 6 months of improvement activities
- Now the customer can implement high-level improvements that they could not solve by themselves!
At this factory, they were promoting improvement activities by themselves, but they thought they did everything they could do on their own, so the activity was stagnant. Then, the Japanese president decided to outsource a shop floor improvement consulting to have their shop floor checked, and asked us, Hirayama Consulting.
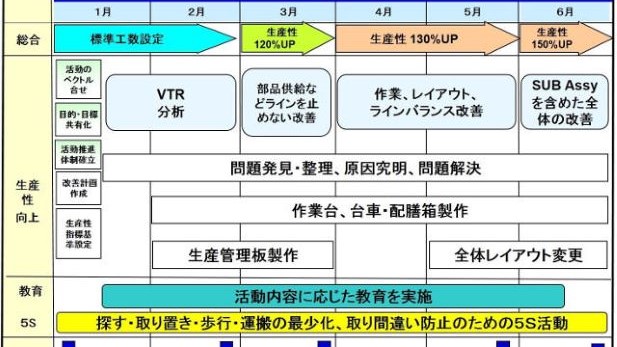
- Industry details
- Auto parts
- Country
- Vietnam
- Company size
- Employee: about 300
- Issues
- Routine improvement activities
- Purpose
- Cost reduction
- Industry
Schedule
- Factory diagnosis
- Setting goals for improvement projects
- Improvement activity
Step 1 – Factory diagnosis
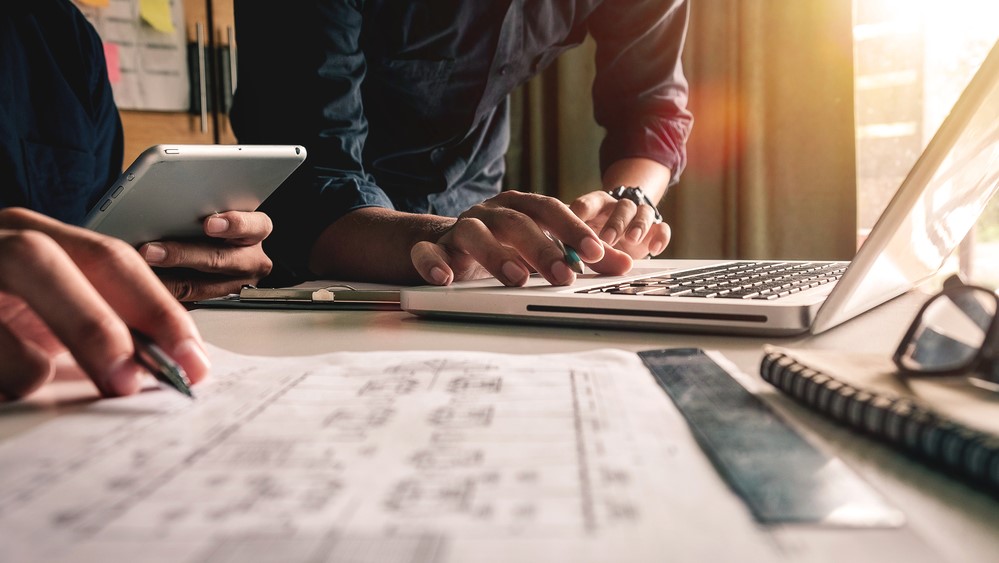
First, we conducted a “one-day factory diagnosis” to investigate how much waste is left at the shop floor.
When we went to the shop floor, we could see everywhere they improved hard by themselves in the past, but we couldn’t find the situation where they improved further at a higher level.
Diagnosis results
The following problems were left at the shop floor.No standard man-hours | Man-hours for each element work were not measured, so there was no standard man-hours. |
Waste of operation |
・A lack of line balance was neglected. ・Wastes of waiting, inventory, and motion were left. ・Wastes of premises logistics and material supply were left. |
Insufficient Sorting and Setting in order | 5S was insufficient and wastes occurred. |
Insufficient Production Control |
|