This training is a two-day program consisting of lectures and practical exercises aimed at leveling up the production site.
・The theories and knowledge necessary to address challenges faced in the field
・Skill JI for implementing improvements and achieving concrete results
Improvements led by manufacturing supervisors and leaders who possess both theoretical knowledge and practical skills, as well as the ability to manage people, are likely to produce effective and tangible results.
This is a TPS practical training session conducted by an officially certified trainer who has supported Toyota’s production sites for over 40 years.
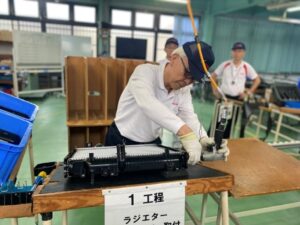
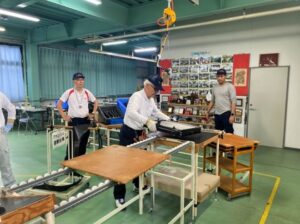
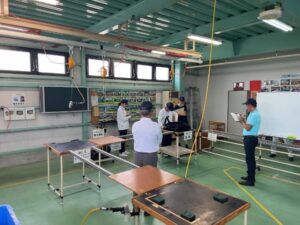
Seminar Overview
title | TPS Dojo (2-Day Edition) |
Category | TPS Doujo |
schedule | Decided after consultation *Please let us know your desired date. |
Capacity | 20 participants (please consult us if more than 20) |
Place |
Our training center (1-84-1 Miyama-cho, Toyota City, Aichi Prefecture) TEL:(0565)71-5288 Click here for the map |
Teacher | Tadamasa Ishigaki、 Mitsu Suzuki、 Matsuki-aoyama |
Diploma | It will be given to you after attending the seminar.![]() |
Fee | 99,000 yen/person (tax included) *Transportation, accommodation, and lunch costs are not included. |
Training content
program
In the “TPS Dojo (2-Day Course)”, participants will comprehensively master the TPS mindset and perspective through both lectures and practical exercises.
This training is designed for managers and supervisors responsible for manufacturing site operations. It provides clear and accessible lessons, incorporating exercises and group discussions to ensure effective learning tailored to this essential leadership level.
Lecture : Basics of TPS | |
---|---|
1. Importance of cost reduction 2. Basic concept of Toyota Production System |
3. Idea of improvement 4. Standard Work |
Practice | |
1.Understanding and considering current issues 2. Consideration and implementation of improvement plans |
3.Save people and strengthen workplace capabilities |
Lecture : How to teach work | |
(1)Role of the teacher (definition of instructor) (2)Five conditions necessary for a person who teaches (3)About the Need for Training (4)About Incomplete Teaching Methods (5)Correct Teaching Methods (6)How to teach (demonstration) (7)Preparation before teaching (8)Training (9)Work breakdown (10)Practical training (demonstration & training) |
TPS practice dojo with video
Consultants from major companies
with experience in over 40 countries will respond.
Please feel free to contact us.
If you are in a hurry, please call us.
(Japan time)
Except for Saturday, Sunday, holidays, Year-End and New-Year holidays