工場の品質向上とは、お客様にとって満足する商品品質の向上のことです。品質は検査部門や品質保証部門を補強すればよくなるというものではありません。
検査や品証部門は生産現場の補佐役であって、品質は工程で作りこみ、自分で作業する範囲は、作業者が自分で保証するものです。
工場の品質向上で
こんな課題を解決
ISSUE
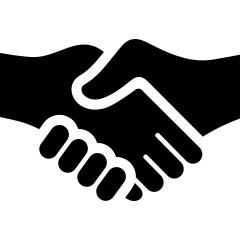
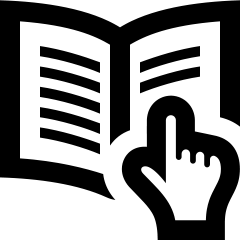
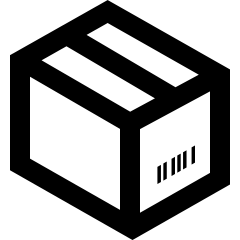
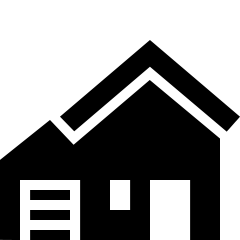
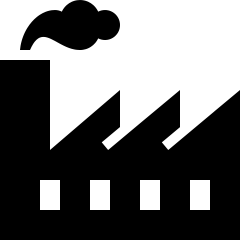
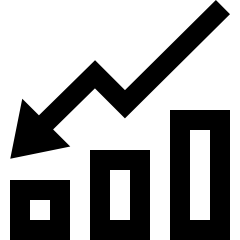
品質向上のための
3つのポイント
FEATURES
-
1
ライン停止の原則
-
自動停止、定位置停止で、後工程に不良品を送らない。
-
2
再発防止の徹底
-
「なぜなぜ分析」による原因突明で、再発防止を徹底。
-
3
対策処理したデーター蓄積
-
対策内容や対策後現状がどうなったか、データを蓄積。
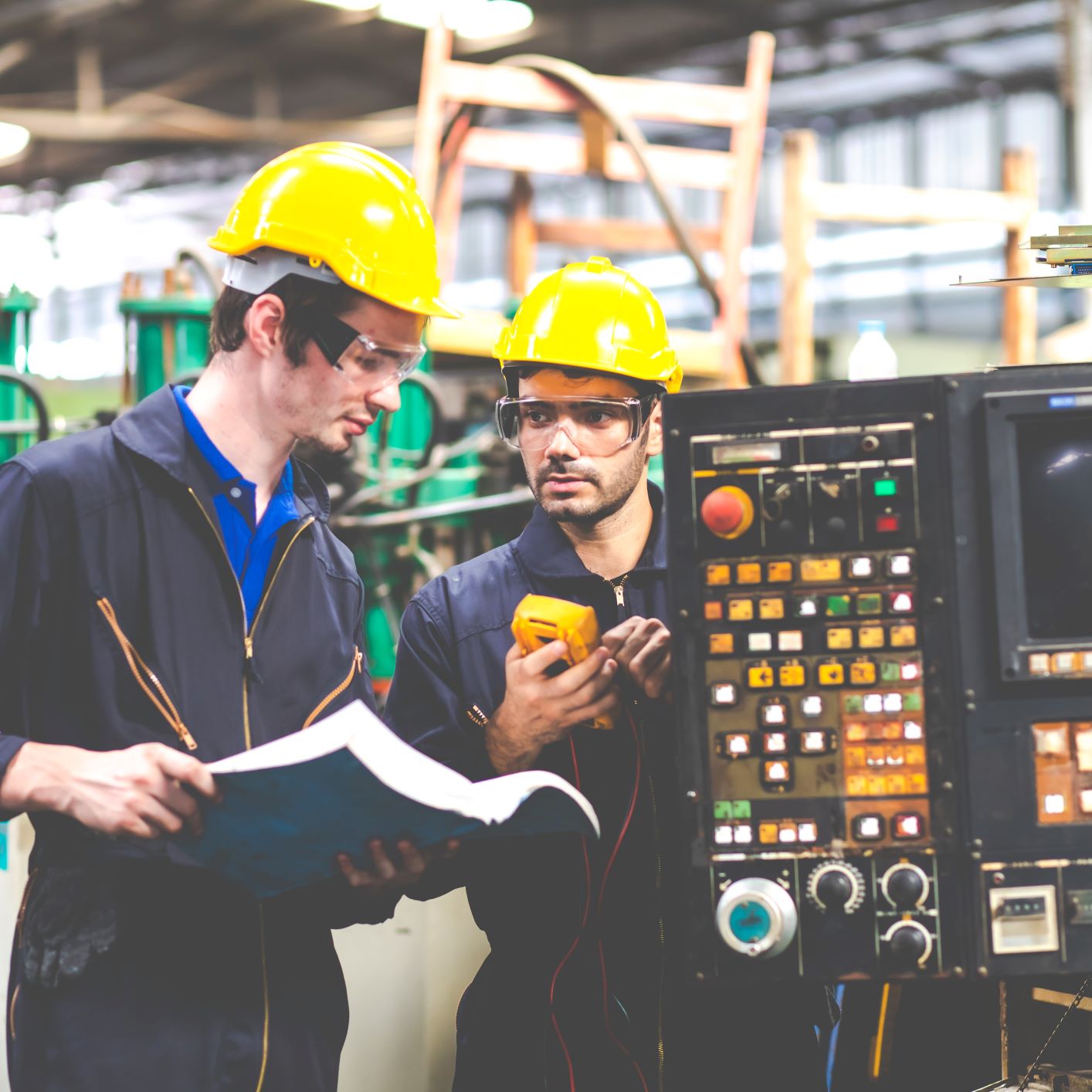
ライン停止の原則
異常発生時には被害の拡大や二次被害防止のために「止める・呼ぶ・待つ」を原則としています。
止めるとは、自働化された設備であれば品質上の問題があれば直ちに止まる。手作業の設備・ラインであれば作業者が止めて責任者を呼び指示を待つ事を言います。このようなルールと体制をつくることで、問題が起きた際に即、問題解決と再発防止を図ることが出来ます。
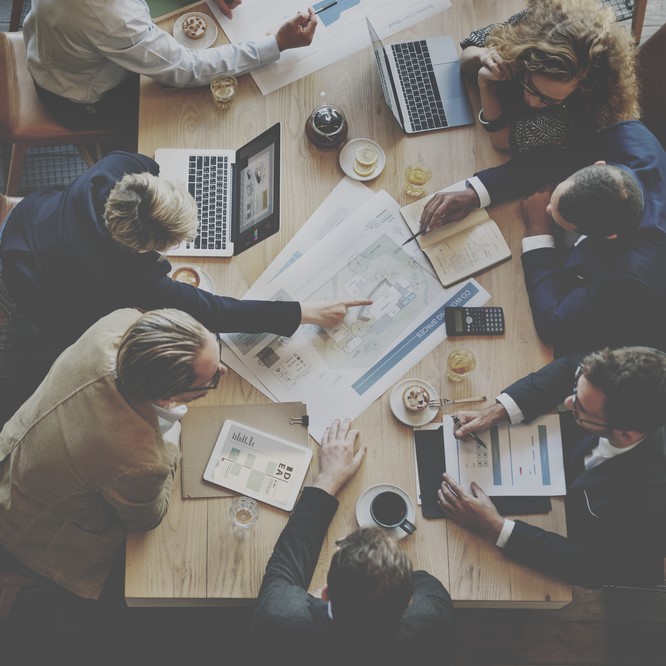
再発防止の徹底
問題発生時に、表面的な原因しか捉えずにいると、表面的な問題の解決しか出来ません。
そこで、発生した問題の真因までたどり着くために「なぜなぜ分析」を行います。1つの問題に対して「なぜ?」とその問題を引き起こした要因を探し、更に「なぜ?」とその要因を引き起こした要因を探していきます。何回かこれを繰り返していくと、問題の真因が分かり、根本的な対策を立てることができます。
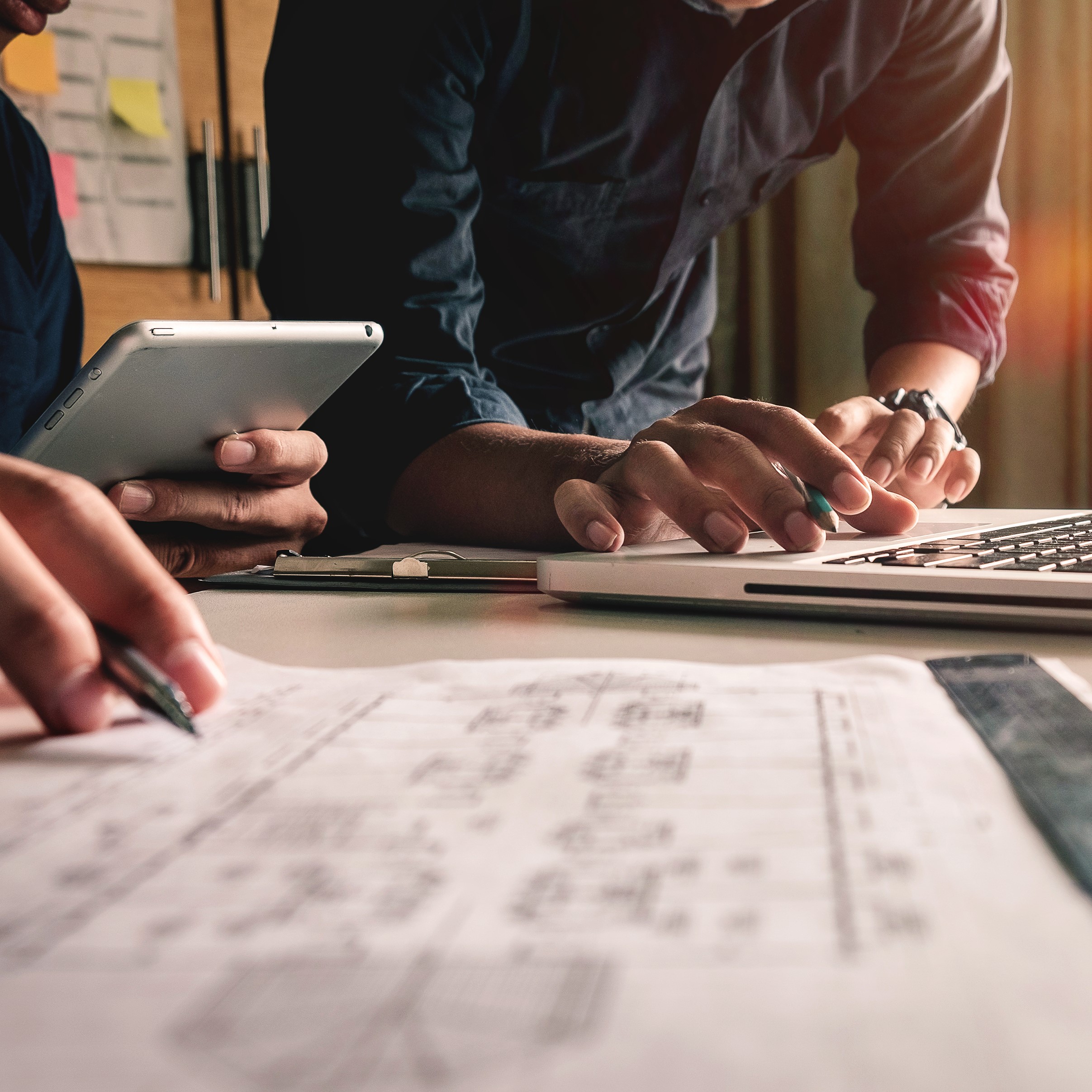
対策処理したデーター蓄積
発生した問題とその原因、そして対策内容は、企業の宝でありノウハウとなるので蓄積していかなければなりません。
しかし、ただ蓄積しただけでは必要時に有効に使うことが出来ませんので、データーベース化して蓄積しておくことであらゆるキーワードで検索できるようになります。
このことにより、問題解決のスピードアップ、問題発生の予測、更に様々な部門でもデーターの活用が出来るようになります。
品質向上のスペシャリスト
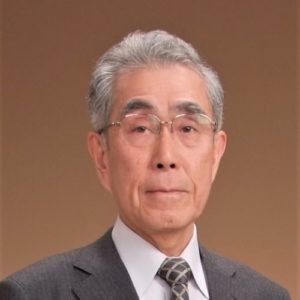
林田 博光(はやしだ ひろみつ)
トヨタ自動車OB 田原工場副工場長
トヨタ生産方式を実践指導。溶接・組立技術が専門。
調達・生産管理などを包括した工場全体の改善活動を進める。各種工場の指導経験が豊富。
品質向上の事例 RESULTS
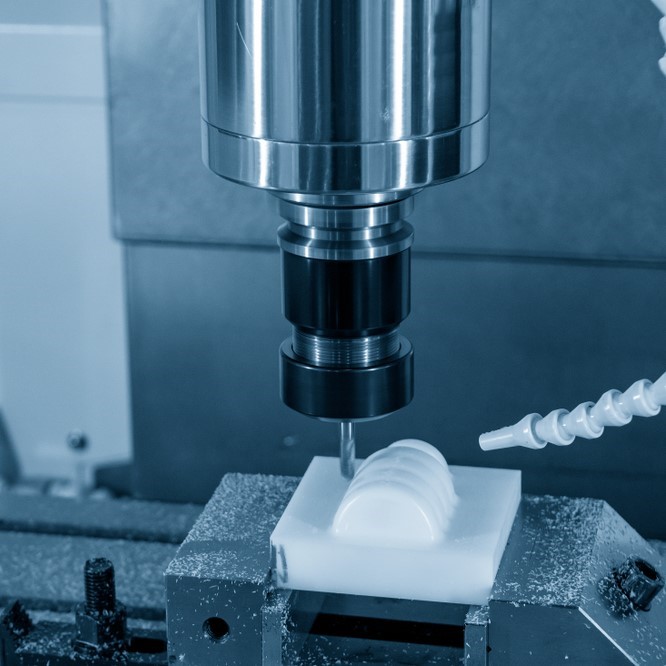
海外赤字工場を黒字化
品質向上で新規取引先2件獲得!
工場の至るところにあった仕掛品・不良品在庫はほとんどなくなり、人員を省人化したが、毎月あった顧客クレームはほとんどなくなりました。(自動車業界/工場長)
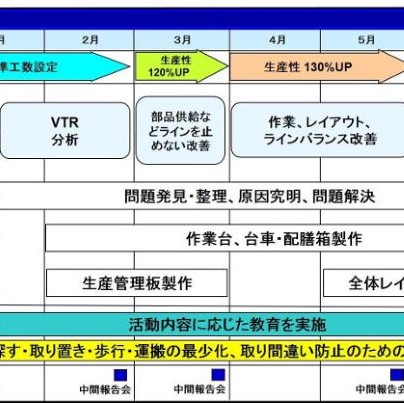
生産性 169.6% UP
スタッフの士気も向上
自力での改善活動に限界を感じコンサルティングを依頼。人材が育ち、今まで自分たちでは解決できなかった高いレベルの改善ができるようになりました。(自動車業界/工場長)
選ばれる3つの理由 REASON
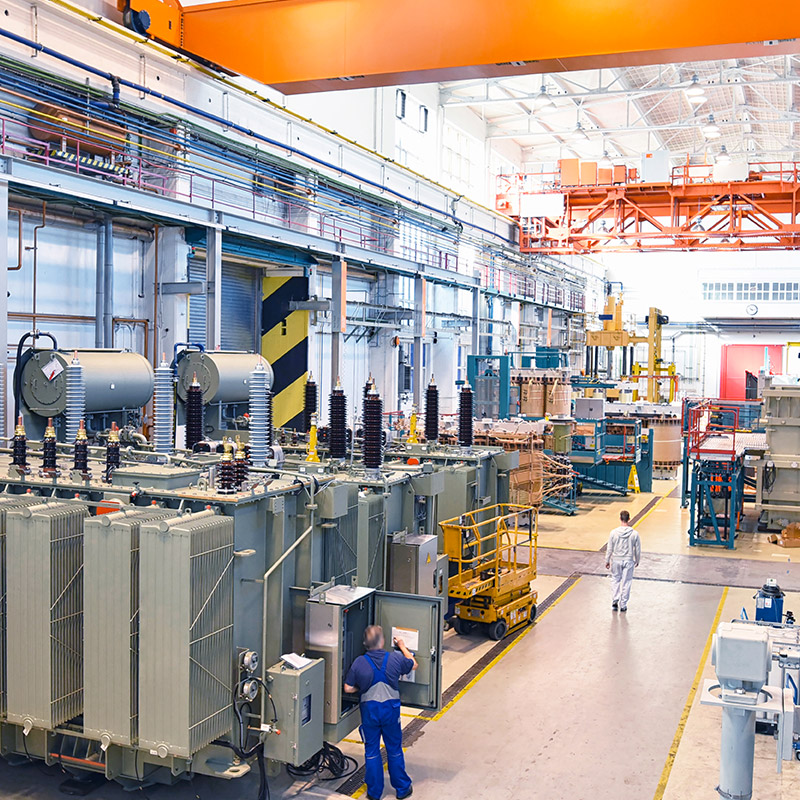
REASON 1
40ヶ国、
1,500社以上の改善実績
自社だけでは解決できない現場の問題は必ずあります。製造業が勝ち残るための改善・改革は、国や業界を問わず、改善の実践体験を通じて、人材を育成し、生産体制基盤を強化することが必要です。
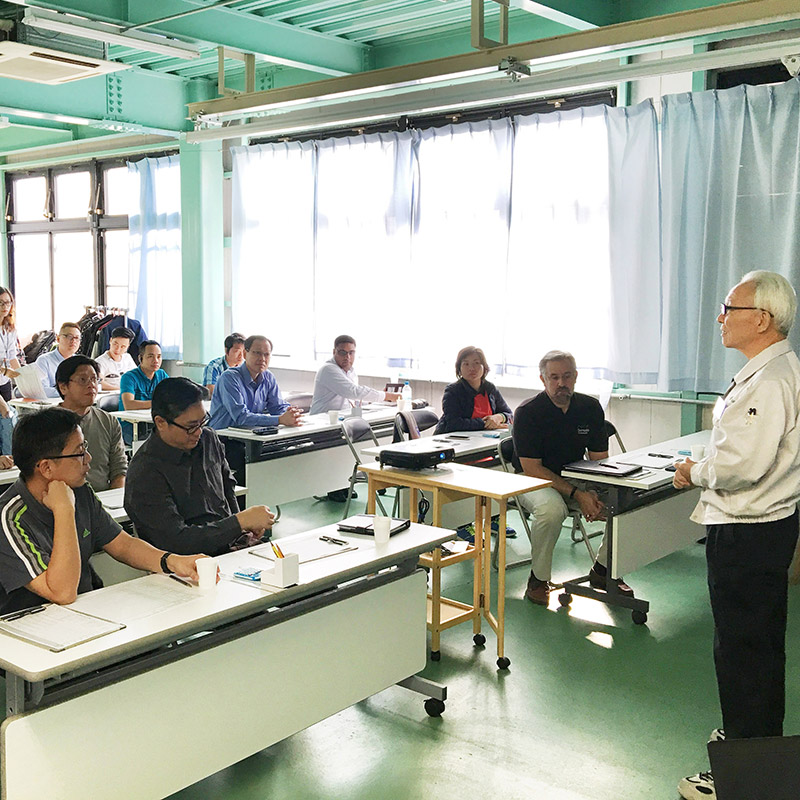
REASON 2
現場が一目置き、
喜ぶコンサルティング
従来のコンサルティングでは、経営層とコンサルタントが中心になってすすめるため、現場とコンサルタントの間に距離がありました。弊社コンサルタントは、評論家的な「あら探し」ではなく「改善の種」を具体的に見出す指導により、現場の人間との隔たりのない指導をすることができます。
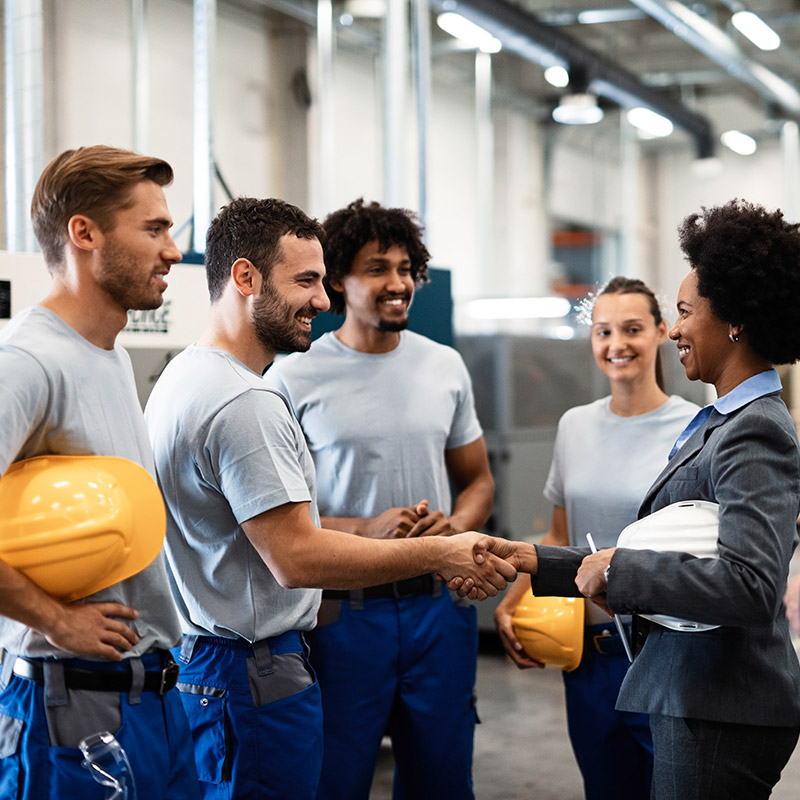
REASON 3
指導終了後も
継続的改善がされる
「人づくり」を強化しながら、設計から調達・製造・物流、そして生産管理と「全体の流れ」を重視し、貴社の現場の実態に合った指導を実施。現場が納得できるコンサルティング指導を行うことで、指導終了後も改善文化が継続されます。