Quality improvement in a factory means improving quality of products to satisfy your customers. Quality does not improve if only strengthening inspection department and quality assurance department.
The inspection and quality assurance departments are just supporters at the manufacturing shop floor. Quality should be made in the process, and operators should guarantee the range of work done by themselves.
Solve these issues
with quality improvement in a factory
ISSUE
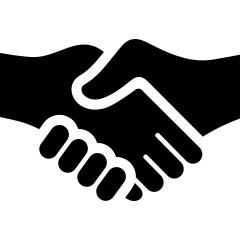
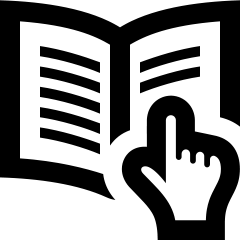
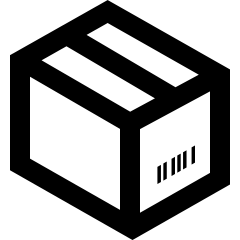
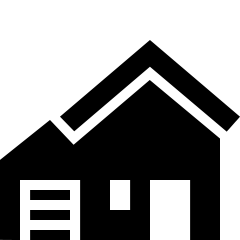
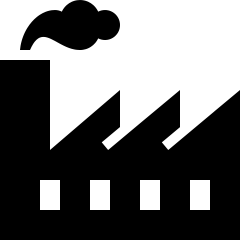
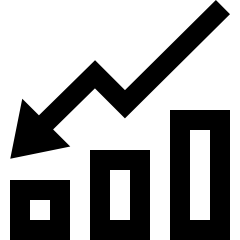
3 points
for quality improvement
FEATURES
-
1
Line stop principle
-
Automatic stop and fixed position stop avoid sending defective products to the next process.
-
2
Thorough prevention of recurrence
-
Identifying the cause of the problem through the “Why-why analysis” thoroughly prevents reoccurrence.
-
3
Countermeasure data accumulation
-
Data on the details of the countermeasures and the current situation after the measures will be accumulated.
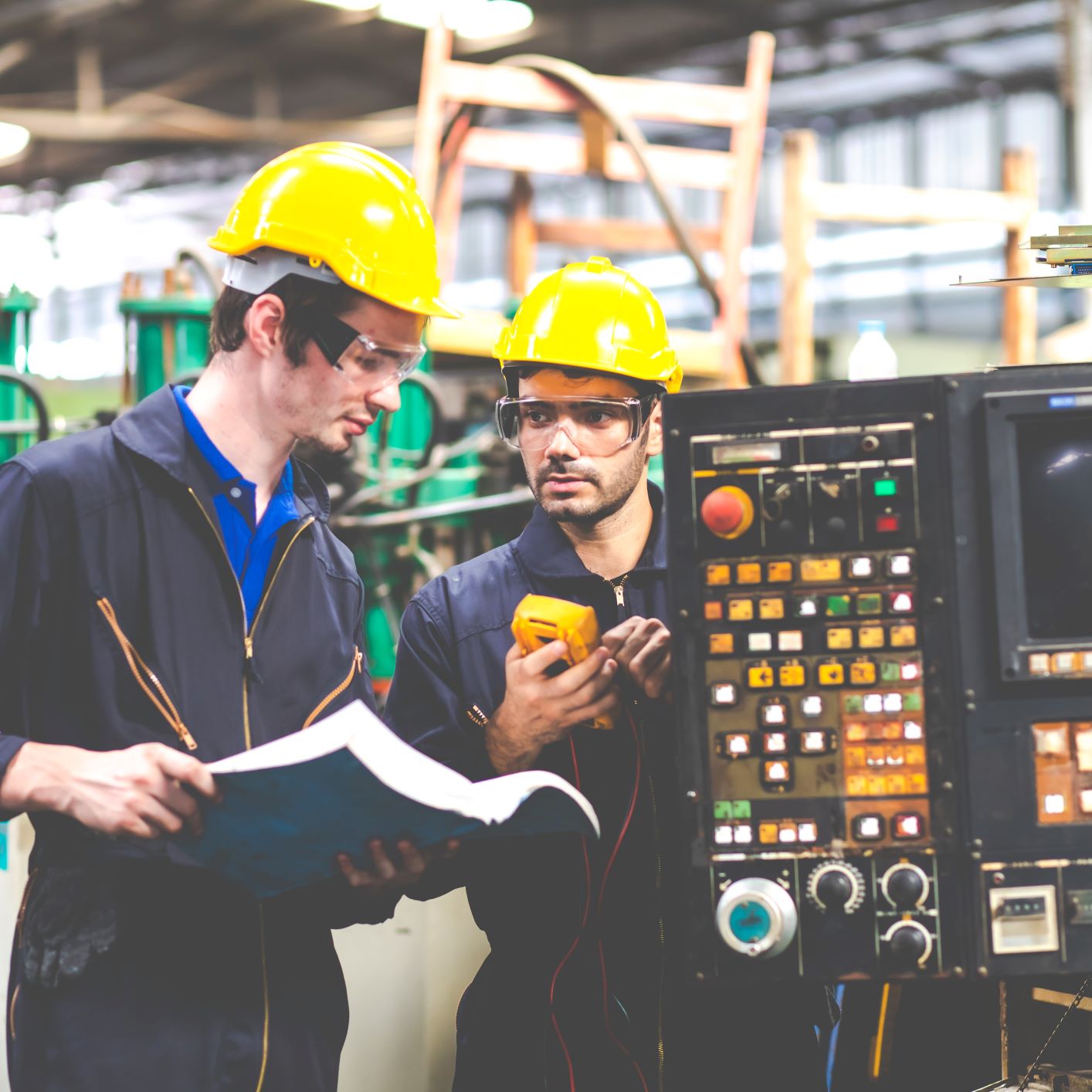
Line stop principle
When an abnormality occurs, the principle is “stop, call, and wait” to prevent the damage expansion and secondary damage. Stop means that an autonomated equipment stops immediately when a quality problem occurs, or if the equipment is a manual work equipment/line, an operator stops it and waits for instructions. By creating such rules and systems, you can immediately solve problems and prevent recurrence when problems occur.
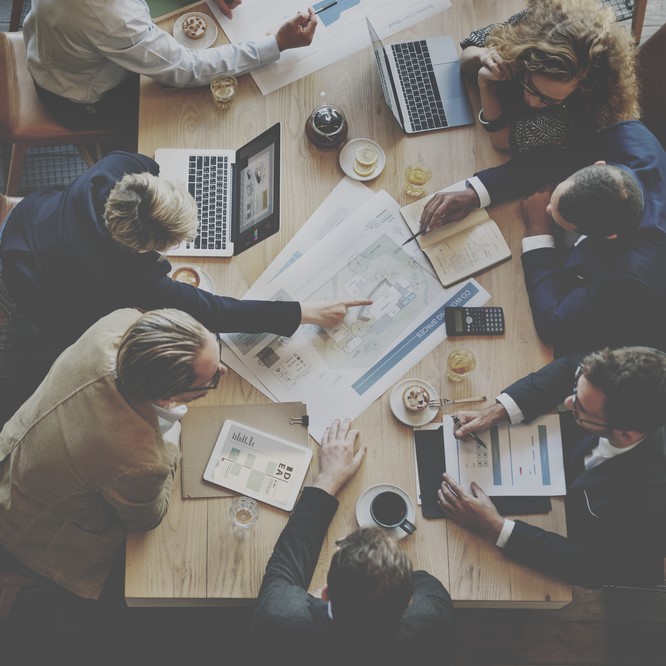
Thorough prevention of recurrence
If you think about only superficial causes when a problem occurs, only the superficial problem can be solved. Therefore, in order to find the root cause of the problem, we conduct “Why-why analysis”. For one problem, we think “why?” to investigate the factor caused the problem, and think further “why?” to investigate the factor caused that factor. If you repeat this several times, you will understand the root cause of the problem and will be able to take fundamental measures.
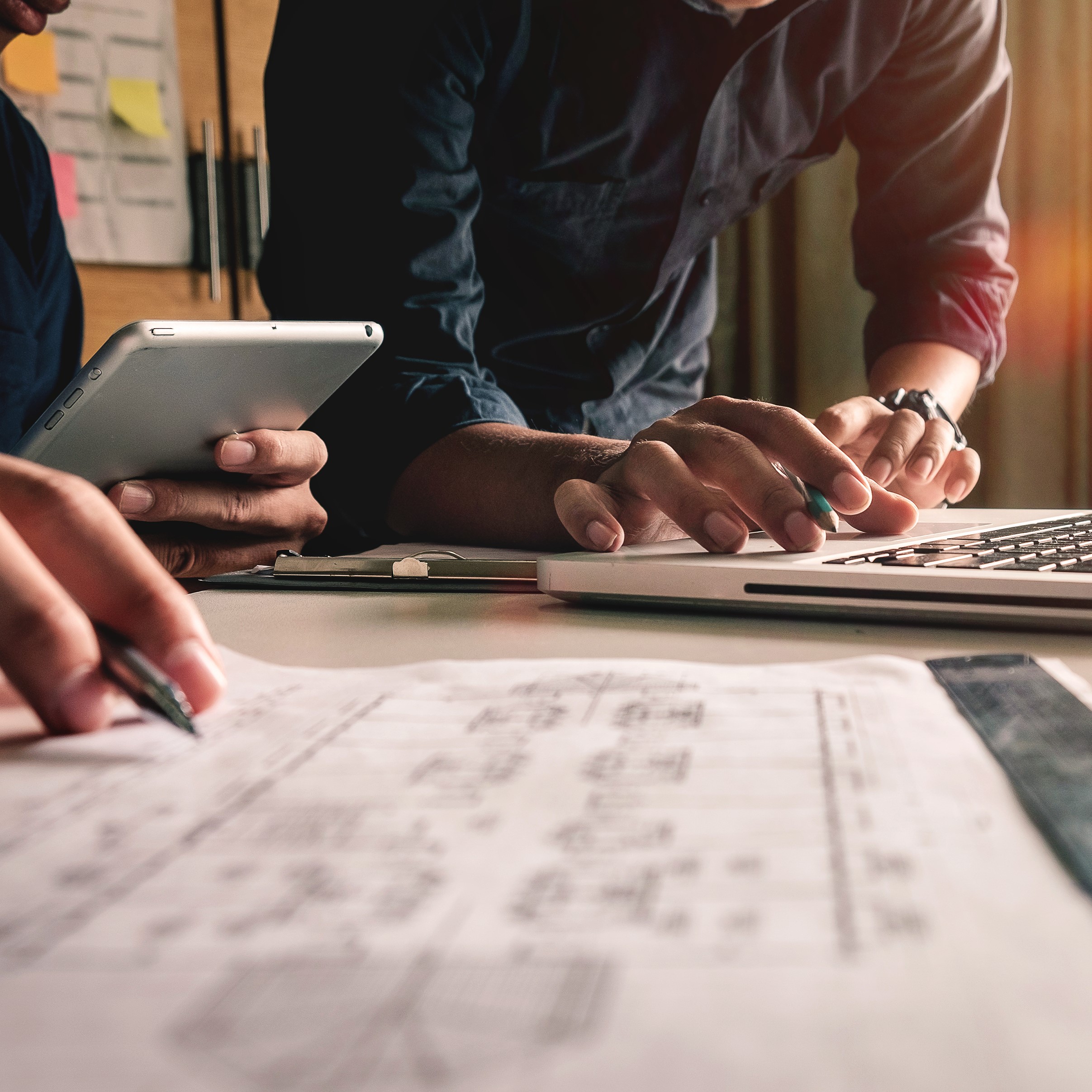
Countermeasure data accumulation
The problems that have occurred, their causes, and the details of countermeasures are treasures and know-how of the company, so it must be accumulated.However, you cannot use it effectively if it is only accumulated, so it should be compiled in a database and accumulated so that you can search by all kinds of keywords. This will speed up problem solving, predict the occurrence of problems, and enable data utilization in various departments.
Consultants from major companies
with experience in over 40 countries will respond.
Please feel free to contact us.
If you are in a hurry, please call us.
(Japan time)
Except for Saturday, Sunday, holidays, Year-End and New-Year holidays
Quality improvement Specialist
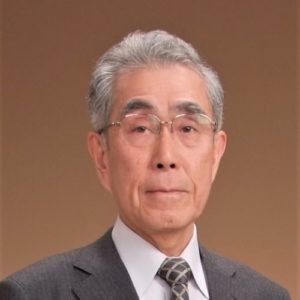
HAYASHIDA, Hiromitsu
Toyota Motor Corporation, Horie Metal Co., Ltd.
A TPS specialist. His expertise lies with welding and assembly technology. He promotes Kaizen (continuous improvement) that comprehensively encompasses entire factory operations including procurement and production control. He is well-versed in giving advice to different types of factories and plants.
Case example of Genba Kaizen Consulting RESULTS
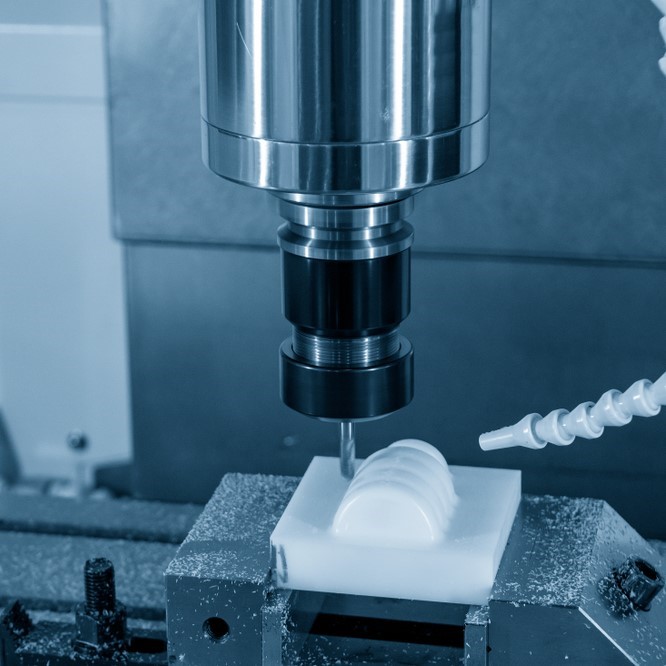
Acquired orders from two new customers
by improving quality.
We reduced most work-in-progress inventories and defective inventories, which were found throughout the factory, and reduced manpower, and now we almost no longer receive customer complaints that we had every month before. (Automobile industry / Plant manager)
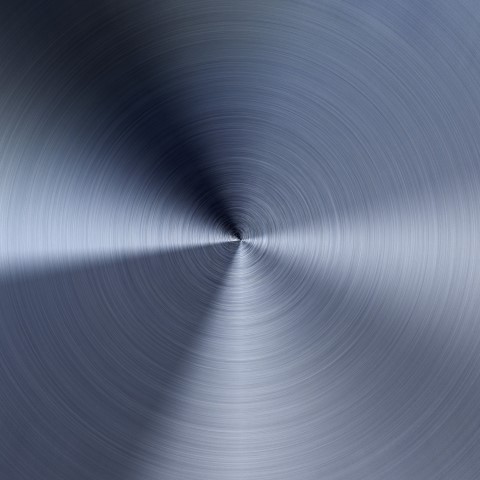
Turn the factory into a showroom
in order to improve profitability
We improved 250 cases out of 300 cases pointed out by the 5S patrol conducted for one year. The factory was realized to be the showroom and also achieved cost reduction of 30 million yen per year. (Metal processing / Director)
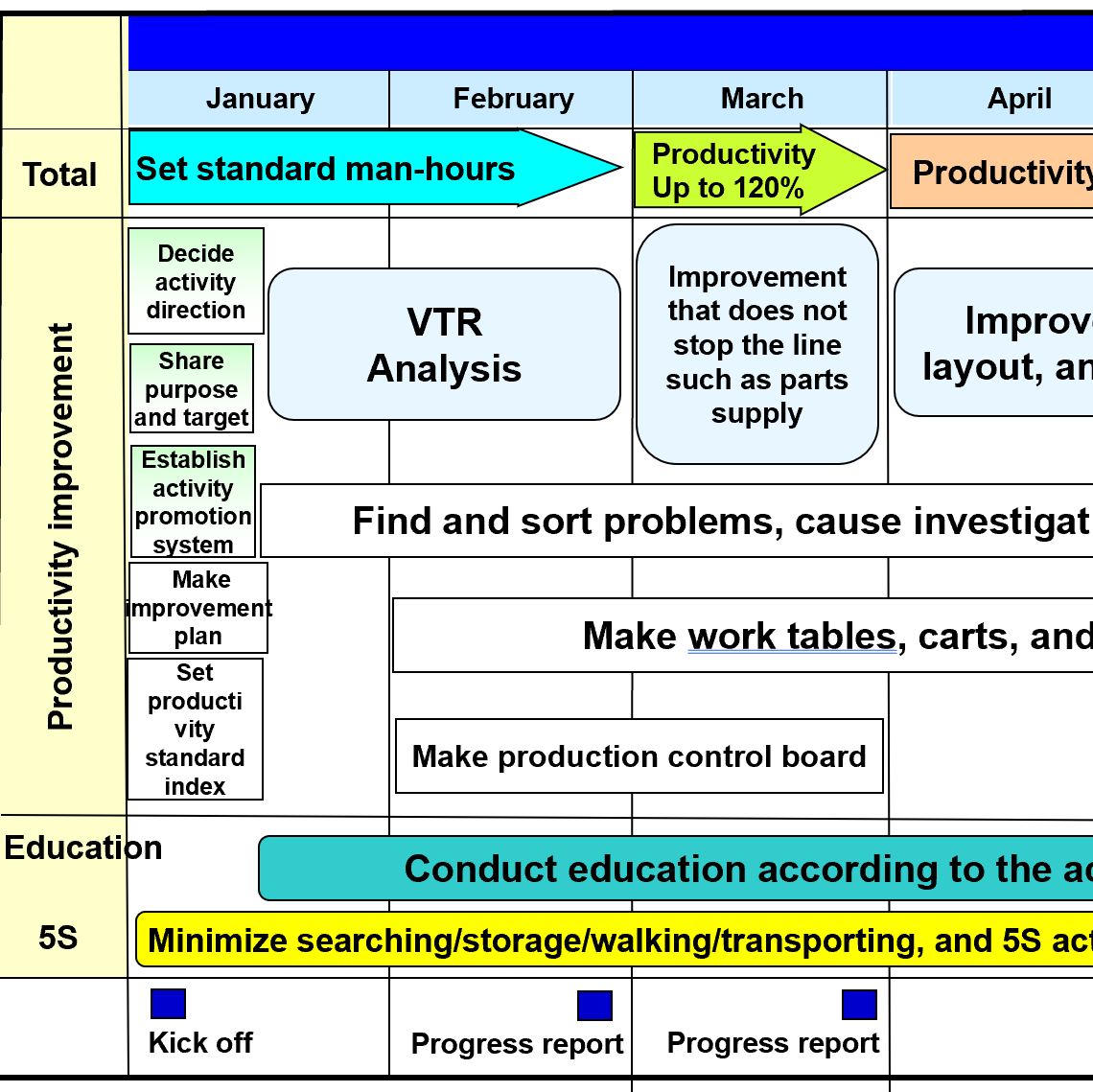
Productivity Up to 169.6%
by 6 months of improvement activities
the Japanese president decided to outsource a shop floor improvement consulting to have their shop floor checked, and asked us, Hirayama Consulting.(Auto parts manufacturer/Managing director)
3 reasons why we are chosen REASON
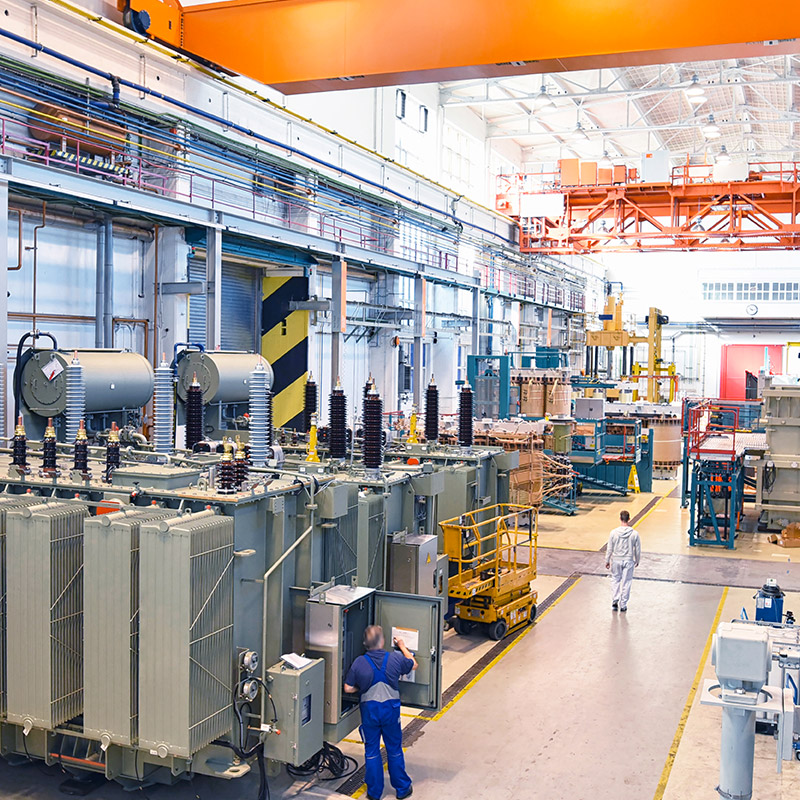
REASON 1
Improvement experience of
more than 1,500 companies in 40 countries
There must be the shop floor issues that cannot be solved by your own company alone. Improvements and reforms for manufacturing industry to survive, regardless of country or industry, need development of your human resources through practical experiences of improvement, and strengthening of your production system base.
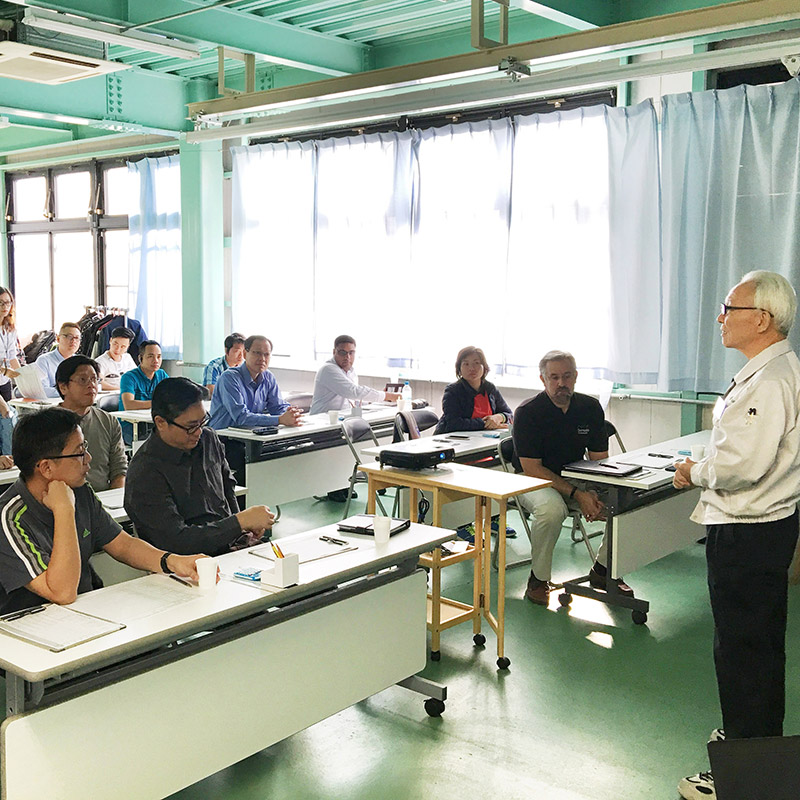
REASON 2
Consulting that shop floor workers
acknowledge our superiority and be pleased
In conventional consulting styles, there was a distance between consultant and the shop floor because it was promoted mainly consultant and management executives. Our consultant can provide a guidance without a distance between consultant and the shop floor through the guidance based on the "seeds of improvement" in a concrete way, instead of "finding fault" like a critic.
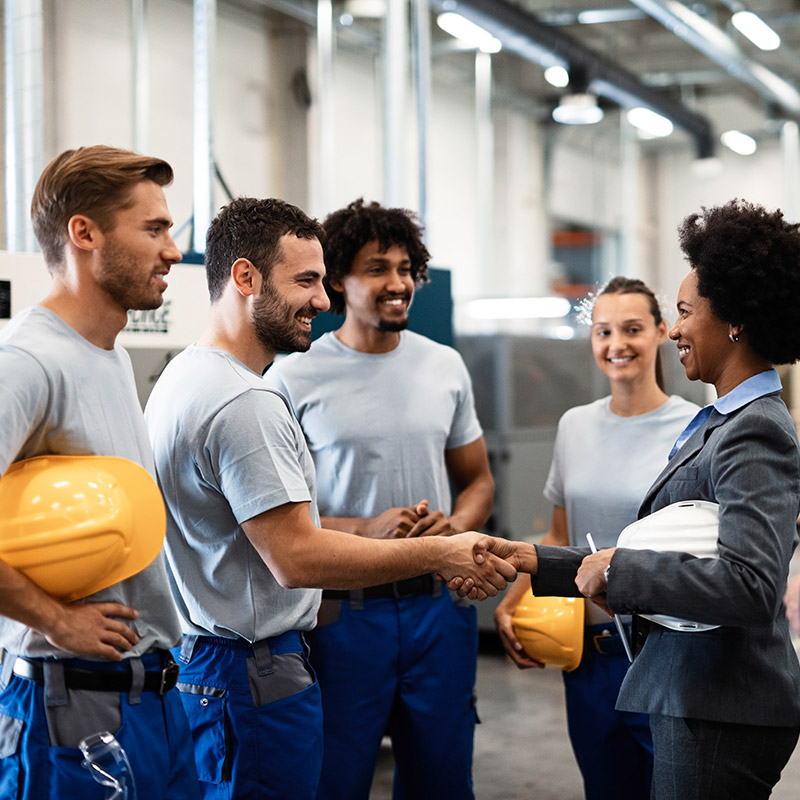
REASON 3
Continuous improvement will continue
even after the end of guidance
While strengthening "human resource development", we focus on the "overall flow" from design to purchasing, manufacturing, logistics, and production control, and provide guidance that matches the actual situation of your company. Continuous improvement will continue even after the end of guidance through the guidance that is acceptable to the shop floor workers.